Optimizing reliability of rotating machinery in the Australian mining industry
Mining is a challenging industry at the best of times and keeping all of the equipment properly maintained to a high standard is essential for continued reliability. Working with a maintenance partner with the experience and expertise to deliver a wide range of services can save time and money.
Glenn Heyes, Newcastle Service Center Manager for Sulzer in Australia looks at the skills and services that help mine operators reduce their costs and keep their equipment efficient as well as reliable.
The scale of mining operations and the equipment that is used can present considerable challenges in terms of minimizing the cost of maintenance. At the same time, the more remote locations that are typical in this industry can add delays in getting support when it is needed. Achieving high levels of productivity requires an effective maintenance regime that minimizes downtime by increasing proactive intervention.
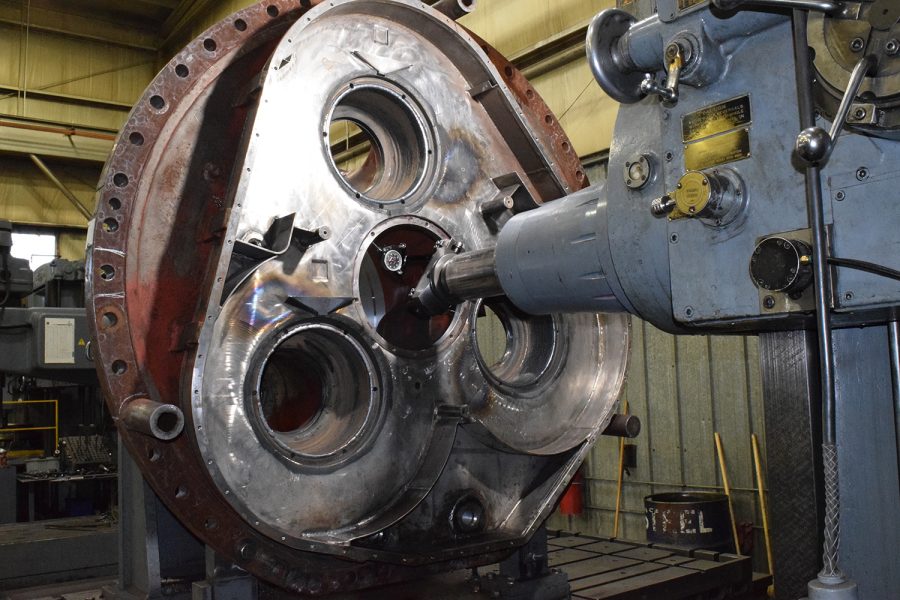
Machining mechanical assemblies as part of a parts upgrade
Maintenance budgets are regularly estimated at between 20% and 35% of total mine costs, making them ideal from streamlining. Optimizing scheduled maintenance procedures, reducing unplanned downtime and using contract maintenance support are all methods of reducing the costs associated with running a mining operation.
Working with a maintenance partner brings a number of advantages, most notably specialist equipment and expertise that can be deployed when it is required. As specialists in repairing mining equipment, these partners can offer fast turnarounds for unplanned events as well as in-depth planning and logistics for scheduled maintenance.
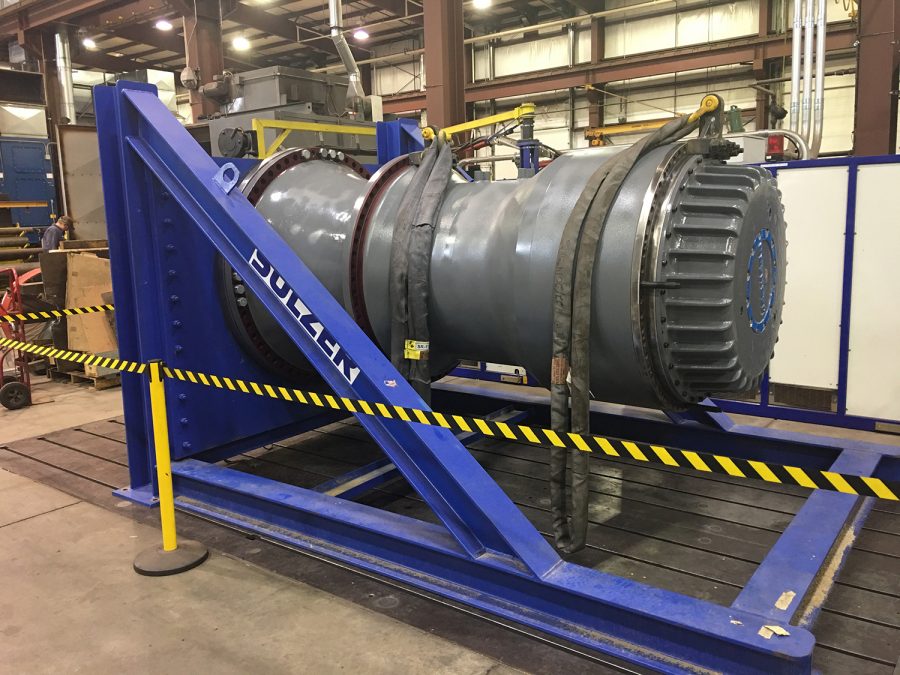
A refurbished wheel set on a specially designed test bed
For some of the largest equipment, such as draglines and loading shovels, as well as fixed equipment such as conveyors, it is essential that any maintenance partner can deliver a full range of support on site. Mobile servicing is a field that requires specialist equipment as well as experience in the machinery itself.
Overhauling large mobile and fixed assets on the surface of the mine requires expertise in many areas. Complex electromechanical assemblies such as generators, gearboxes and wheel sets, need specialist support that is preferably delivered with knowledge of the original equipment manufacturer’s (OEM’s) standards and specifications.
Maintenance providers that work with OEMs have to demonstrate that they are capable of delivering repairs to the high standards required. In return, OEM’s offer engineering assistance as well as direct access to genuine parts to ensure robust and durable repairs.
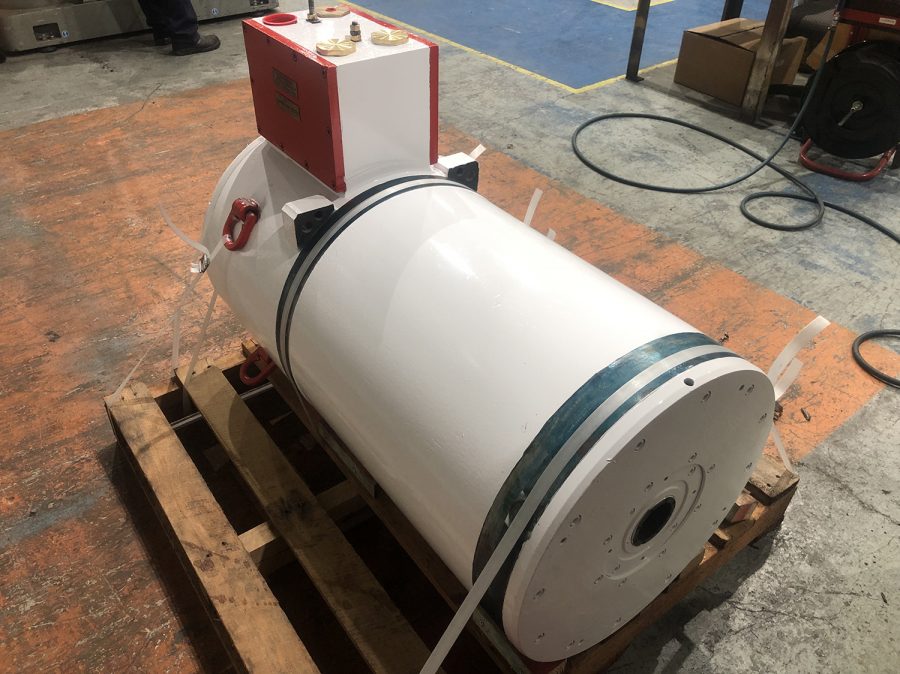
A refurbished generator ready to be shipped back to the customer
Any electrical equipment that is destined to operate in a potentially explosive atmosphere must be suitably designed and installed to comply with industry standards. Motors that operate underground, for example, must be Ex or IECEx rated and maintenance operators need to be certified to carry out these repairs and capable of supplying original components to ensure the project is completed quickly.
In addition to unplanned maintenance there is a requirement for all electrical equipment to undergo a four-year certification to prove it is safe to continue operating below ground. With careful planning, precision management and the necessary qualifications, an experienced maintenance provider can handle the whole process, ensuring that all records are kept up to date.
Furthermore, the variety of electric motors, whether they are in conveyors, shuttle cars, shearers or loaders, means that any full-service provider needs to have extensive knowledge and technical expertise.
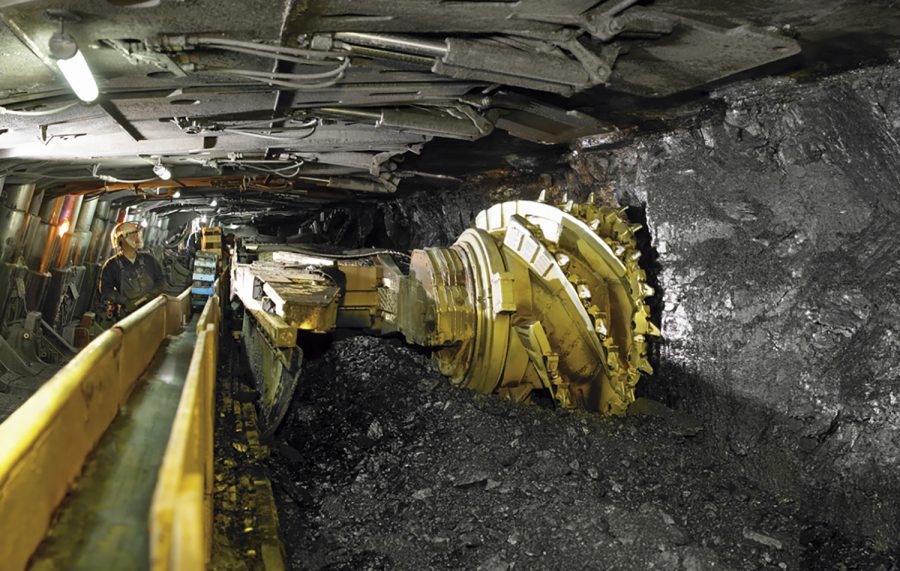
Keeping water away from the coalface is essential for efficient operations
(Image Source – Peabody Energy)
Above ground, haul trucks provide the link between the mine excavations and the processing equipment. Many need to operate 24/7, and above all they need to be reliable to keep the mine productive. At their heart, a generator provides the electrical energy required to drive the wheel sets, which consist of a motor and a gearbox.
Refurbishment of these complex electromechanical assemblies should be completed by the OEM, or one of their selected partners that has access to the necessary engineering support. In many cases, the latter option will enable the service to be delivered more quickly.
This speed of service is even more important when unexpected issues arise, such as oil leaks from the duo-cone set on the gearset, which can be a common problem on some models. Designed to keep the lubricating oil in the gearbox separate from the electric motor, these seals can be replaced overnight by specialists, such as Sulzer.
Case study: Fleet overhaul scheduling
For operators with larger fleets of haul trucks, scheduled maintenance, overhauls and repairs need to be carefully scheduled to minimize downtime and optimize productivity of mines. Sulzer has equipped a group of service centers with all the necessary tooling and test facilities to deliver fast turnarounds.
For one customer operating a fleet of MT400 trucks, Sulzer setup a schedule to manage the complete mechanical strip down, inspection and electrical testing of the GEB25 wheel set. Using designated workshop areas equipped with custom tooling and jigs, experienced engineers operated two shifts to optimize the turnaround of each wheel set.
Working in partnership with OEMs and extensive in-house manufacturing capabilities, means Sulzer’s service centers are fully equipped with a flexible workforce that can overhaul wheel sets that will continue to deliver reliable service.
The ideal maintenance partner
To deliver a comprehensive service, maintenance providers need to have the skills and resources to repair and remanufacture generators, electric motors, both DC and AC, gearboxes and control equipment. Aside from repairing specific components, more general skills, such as rebuilding shafts and bearing seats, are very important as this wear and tear can often be discovered during a routine maintenance project.
Sulzer has a worldwide reputation for delivering high-quality repairs to a large number of heavy industries including mining. In Australia, there is a network of service centers covering the main mining areas that offers class-leading delivery of repair and maintenance projects. By working with the major OEMs, Sulzer uses lean engineering principles to minimize downtime and improve the reliability of mining assets.
Using its extensive experience and expertise, Sulzer delivers fast and accurate repairs for a wide range of mine equipment, where attention to detail is essential. Using properly trained staff that attend regular updates is essential for those working in an industry where observance of manufacturing standards is so vital. Regular internal training ensures that any changes in repair procedures or assembly processes can be implemented at the earliest opportunity, assuring customers of best practice in every project.
About Sulzer:
Sulzer is a global leader in fluid engineering. We specialize in pumping, agitation, mixing, separation and application technologies for fluids of all types. Our customers benefit from our commitment to innovation, performance and quality and from our responsive network of 180 world-class production facilities and service centers across the globe. Sulzer has been headquartered in Winterthur, Switzerland, since 1834. In 2019, our 16’500 employees delivered revenues of CHF 3.7 billion. Our shares are traded on the SIX Swiss Exchange (SIX: SUN).