Authors: Maurizio Rovaglio, Vice President, Oil & Gas Technology and Alliances, Schneider Electric, and Jack Creamer, Market Segment Manager, Pumping Equipment–Industry Business, Schneider Electric
The Oil & Gas industry spent $6 Billion in 2015 on data management with a projected annual compound spending growth rate of 28% to $21 Billion by 2020 (footnote #1). With more and more data storage moving to the cloud, this represents the IIoT layer where enterprise systems (e.g., ERP, PLM, CRM) and next-generation functions, including asset, operations and energy management converge.
The cloud layer is where Big Data, gathered from intelligent devices across the value chain of operations, is stored. This layer helps to accelerate the monetization of IIoT deployment. For example, by implementing cloud-based well management solutions, operational savings can reach 50% during the first year while achieving 30% in the subsequent years. O&G companies today can implement such solutions, or they can engage OEM suppliers for applications such as pumping, which can benefit greatly from such solutions.
Cloud-based predictive maintenance represents another opportunity for streamlined operations. In the area of pump maintenance, for instance, a typical planned maintenance schedule would change pump seals every 2 years, whether or not these changes were needed. By implementing cloud base predictive solution, the predictive model and algorithm help forecast future failures and seals are only changed once they begin to exhibit warning signs of potential future failure. Thus, unnecessary maintenance interventions are reduced.
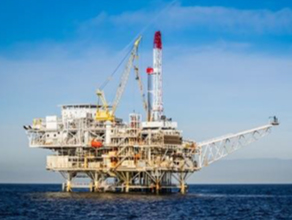
The cloud enables shared information within the fuel supply chain to keep operations running smoothly and efficiently.
The cloud enables shared information within the whole supply chain to keep operations running smoothly and efficiently. Direct back office integration of critical data provides all parties the information they need, eliminates time consuming manual entry, and reduces potential keystroke errors.
Using cloud technologies to connect existing automation in the oil field aids in the distribution of the data sources, data aggregation levels, and defines processes where the results of the analysis can be applied back to the field. Actionable information derived from cloud-based analysis helps to close the loop with automation systems, service providers, operators or other entities that are capable of performing actions in the field.
This allows the implementation of a system that integrates well management, for instance, with the functionalities of pump control, production monitoring, alarm analysis, failure tracking and work order management. This system can provide guidance on data models standardization across the field devices and software platforms. The result is a highly scalable solution that allows remote/fast deployment and minimal software configuration for optimized well automation.
Cloud Wells Management is a web-enabled monitoring application generating information and KPIs from real-time process data historians, production databases, field devices and simulation well models. From a desktop computer or a tablet, operators can visualize key performance data, access different hierarchical views of the field and manage all assets. A simulated view of oil and gas well performance and diagnostic displays allows timely response to emerging well issues for faster recovery of optimal operation. Such identification of underperforming oil wells helps operators avoid deferred production, reduce maintenance costs, increase production and maximize field efficiency and oil recovery. Designed to highlight the benefits of “as a service” solution, Cloud Wells Management is easy to deploy and can demonstrate immediate returns on investment within two to six months.
Footnotes:
- Markets & Markets, “Oil and Gas Data Management Market by Type”, May, 2015
This article is part of an eight-part series looking at how the Industrial Internet of Things (IIoT) concepts are transforming the Oil & Gas industry business model. For more information, please visit: goo.gl/4ohXN7.
READ PART 1 | READ PART 2 | READ PART 3
About the Authors
Maurizio Rovaglio is Vice President of Oil & Gas Technology and Alliances at Schneider Electric in Italy. Mr. Rovagilo holds multiple patents and has authored over 100 technical articles published in international scientific journals, and has delivered presentations at multiple international conferences. Mr. Rovaglio has over 15 years’ experience in software sales, marketing, resource planning and project execution in the O&G domain across the world.
Jack Creamer is Schneider Electric Segment Marketing Manager – Pumping Equipment, based in the United States. Mr. Creamer has more that 30 years in the Electrical Industry, and has been involved for 10 years in the Pumping Industry. He is involved in key industry organizations such as the Hydraulic Institute and Submersible Wastewater Pump Association, where he holds both Committee Chair and Board level positions. In his time in the Pump industry, he has help Schneider create numerous solutions that both enhance pumping efficiency and address issues such as maintenance and downtime.