Contributor: Wil Chin, Vice President of Marketing and Business Development at United Electric Controls
Rick Frauton, Senior Product Marketing Manager at United Electric Controls
Modern process transmitters are providing more and more functionality, which can translate into lower cost of procurement and ownership, faster time to project completion and safer, more compliant operation. The secret is matching the right transmitter to your client’s application. A new breed of hybrid transmitters, which does more than just retransmit the process variable, is emerging to offer tremendous benefits to the automation skid builders, systems integrators, EPCs, and end-users.
What is a hybrid transmitter?
In most automation circles, the term “process transmitter,” is used to describe an instrument that detects changes in a process and retransmits the variable to a process controller. A hybrid transmit is similar to a process transmitter in both outward appearance and in the fact that it retransmits the process variable. They differ, however, in that hybrid transmitters are designed for process monitoring and to perform safety, alarm and shutdown functions via an integral switch or relay. Hybrid transmitter design focuses on reliability and repeatability and typically does not include the ultra-high accuracy required for custody transfer applications. As a result, hybrid transmitters are significantly less expensive to install while offering additional functionality.
Following are examples of the functionality hybrid transmitters may provide:
- Gauge — provides operators and maintenance technicians with the process variable, diagnostics and set point status.
- Programmable microcontroller — provides the ability to accurately switch valves, motors and alarms directly and at the point of measure, eliminating a PLC, excess wiring and system complexity. Hybrid transmitters can also provide discrete input to a PLC, freeing up analog inputs for process transmitters.
- Safety relays — enables direct connections to final elements in a functional safety application controlling valves, permissives, or blowers. Direct control of the final element can minimize precious milliseconds otherwise spent sending a signal to the safety PLC, which in turn must provide the emergency alarm or shutdown. Direct control of the final element simplifies wiring and potentially eliminates the need for the safety PLC in simplex functional safety systems.
This trend has given rise to a new breed of hybrid transmitter, one which, can lead to significant benefits for skid builders, integrators or EPCs, enabling more competitive bids on large or specialized applications. Hybrid transmitters can provide smarter, cost-effective replacements for mechanical switches; can eliminate the need for PLCs; can directly control final elements; and can provide local and remote diagnostic reporting. Here are some real-world scenarios in which specifying hybrid transmitters over conventional process measurement sensors can boost your profit, shorten delivery time and endear yourself to your clients:
1. Hybrid Transmitters in Emergency Shutdown Applications
Emergency shutdown systems are an excellent application for hybrid transmitters. A typical safety instrumented function has three main steps:
- A safety sensor (transmitter) monitors a pump, compressor, hydraulic cylinder, steam line or natural gas main, retransmitting any potentially dangerous changes in temperature or pressure to a safety PLC via wired analog 4-20 mA signal.
- A safety PLC evaluates the signal running preprogrammed safety logic to determine if a dangerous condition exists. If confirmed, the safety PLC instructs an internal safety relay to open.
- A safety relay initiates an alarm or emergency shutdown via direct wired connection to control a final element — such as a pressure relief valve, blower fan or gas line main shutoff, which mitigates the danger.
Traditionally this involves at least three separate devices: a dedicated pressure or temperature transmitter; an independent PLC which performs the signal analysis; and a switch to control the final element (valve actuator). The entire chain of events (and each component) must conform to safety standards IEC 61508/61511 and be certified by a third party to the prescribed safety integrity (SIL) level required by the desired risk reduction.
With a hybrid transmitter, two of the three steps can be integrated into one SIL-certified instrument (Figure 1). A hybrid transmitter retransmits the process variable for remote monitoring and the onboard microcontroller performs all logic solver algorithms required to validate the sensor’s signal. If conditions warrant an alarm or emergency shutdown, either or both can be initiated by an integral safety relay direct to the final element. Furthermore, a hybrid transmitter with a digital display (gauge) can indicate the process variable, health status and trip status, vital information during proof testing or in an actual emergency situation.
And because the hybrid transmitter is purpose built for use in a safety system and includes final element switching capability, it would be about half the installed cost of implementing a traditional process transmitter for the same safety instrumented function, enabling instrumentation bids at numbers not otherwise possible without a huge volume discount.
Suppose, for example, that you received a request from a client that needs to bring an older plant up to SIL 2 or SIL 3 quickly and cost-effectively and it includes installation of a SIL 2 safety system to prevent destruction of a positive displacement (PD) in the event of a valve closure that blocks flow to the pump. One approach would be to augment the non-SIL certified conventional process transmitter and DCS/PLC with SIL certified components, which would add cost and complexity. As shown in Fig. 2, this would involve the addition of a SIL-certified transmitter, a safety PLC, a panel for the PLC, as well as the interconnection wiring, panel installation in the motor control center (MCC), related software and calibration. It would also mean paying for capabilities such as custody transfer accuracy and digital protocols that would come with the process transmitter, but which the safety application would likely never require. The equivalent SIL 2 or SIL 3 SIF could be achieved for a fraction of the cost with a purpose built hybrid safety transmitter, dedicated solely to performing safety instrumented functions. The architecture shown in Fig. 3, removes the process transmitters and replaces them with a Safety Transmitter, which incorporates a sensor/logic solver and relay in one unit, requires much less wiring, no software and is very easy to set up — all of which adds up to significant cost savings. The hybrid analog output can be connected to the control system so technicians can monitor the health of the system from the comfort of the control room.
Conventional process transmitters can cost twice as much as a dedicated hybrid transmitter because their ultra-high accuracy is intended for controlling processes and custody transfer applications. But for a functional safety application, ultra-high (custody transfer) accuracy is severe overkill. In a typical SIF, the sensor (transmitter) is monitoring the process for abnormal values to initiate a warning, alarm, or shutdown and not intended to control the process. If the process variable gets close to the abnormal value, the shutdown can be initiated. In a competitive bidding process, quoting a hybrid transmitter designed specifically for safety applications will provide a large price advantage and provide the necessary features, including switching, to monitor for unsafe process conditions.
2. Safety Interlocks and Permissives
In addition to safe shutdown of a system gone awry, hybrid transmitters can help avoid dangerous and harmful situations. Examples include boiler restart management, autoclave management, eyewash stations, safety showers and detection and suppression functions.
Boiler restart permissive. If the plant design calls for a gas boiler to provide steam, good engineering practice is to place a hybrid transmitter with a temperature or pressure sensor on the boiler to ensure that all restart conditions are verified before allowing gas back into the combustion chamber. A sensor could be programmed to prevent the gas valve from opening until the chamber has cooled down or until the blower pressure is optimal.
Autoclave management. Similar interlocks could be put on an autoclave or other pressurized heating devices, which would prevent someone from opening the door if the pressure inside the chamber was too high.
Safety shower station. Someone running to an eyewash or safety shower station after a chemical accident is not going to have time to alert others of the mishap. A pressure sensor monitoring the water pressure can determine if the safety shower was used and dispatch medical assistance to that station immediately.
These application examples could be met with conventional process transmitters, but would require integration of multiple components like a PLC or safety trip alarm, which adds unnecessary cost, complexity and vulnerability. A hybrid transmitter provides all of the functionality and speed required while reducing cost, SIF complexity and wiring.
3. Condition monitoring/Predictive maintenance
While hybrid transmitters would not necessarily be used in process control functions, they can contribute to process improvement by monitoring and signaling when asset health and performance may be in jeopardy. Some of this may have safety implications, but it can also impact replacement planning, throughput, downtime and much more. Here are a few examples of systems that can be monitored very cost-effectively with hybrid transmitters.
Detection & suppression. Hybrid transmitters are very valuable for monitoring situations and maintaining set values. Plant compressors, for example, typically need to maintain a certain pressure 24/7. The sensor can monitor the air storage tank for the appropriate pressure range and cycle the compressor on and off to maintain the right value. It can be programmed to accommodate different demands on the system, throughout the day, staying within an established operating window. This could be done with a traditional process transmitter and a PLC, but it would require a more complex set up, including sending the digital signal to a relay, which would run the cycling control. It would also require someone who can program the PLC. The only programming required with the hybrid transmitter is setting the values that appear in the window mode. The hybrid transmitter can be programmed to maintain a certain pressure band within the storage tank, by cycling the compressor motor control center directly, without the need for additional components. Even in high cycle rate applications, hybrid transmitters that contain solid state relays will not suffer from the frequent on/off cycling.
Pump protection. In addition to start and stopping functions, hybrid transmitters might be specified for maintaining minimum head pressure at the inlet side of a centrifugal pump, to make sure that the pump is not starving for process fluid, resulting in cavitations that lead to premature pump failure. As level of the tank drops under maximum flow conditions the pump is turned on and off to maintain the minimum level to meet the net positive suction head specified for a given pump. Using a process transmitter in this typical “switch” application would entail sending the analog 4-20 mA signal to a PLC or DCS for interpretation of the process variable (PV.) If the PV is determined to have fallen below a critical value, the PLC/DCS must then send a signal back to the pump motor control center (MCC) to start.
In positive displacement pump liquid applications delay in milliseconds can cause permanent damage to reciprocating parts such as pistons, connecting rods, and crankshafts. When a complete blockage in the pipeline occurs, the energy of the motor driving the pump needs to be dissipated resulting in catastrophic failures if not shutdown as fast as possible. Depending on the response time of the process transmitter, digital protocols, PV interpretation algorithms, processing speed of the PLC/DCS and distance between the point of measure (the transmitter) and the pump MCC, seconds can elapse. The equivalent protection can be provided at the point of measure via the hybrid transmitter’s ability to directly switch the pump MCC within 100 milliseconds. Using a hybrid transmitter in these situations not only saves hundreds of precious milliseconds, it also makes the system much less complex and far less expensive to implement and maintain. It also eliminates PLC/DCS hardware, programming and associated wiring while improving performance and typically costs less than half the cost of the process transmitter.
Lubricating oil monitoring. In typical lube oil applications, pumps, compressors, or turbine bearings are monitored for pressure or temperature changes that may indicate seal leaks and the need to shut down these systems. A temperature rise may indicate that the oil is being over-stressed or that the bearings are about to fail, or that preventive maintenance is required. A hybrid transmitter can act directly to provide the alarm or shutdown switch signal while the 4-20 mA output is used to trend the changes and provide predictive maintenance data.
Filter monitoring. Hybrid transmitters can control and/or provide alerts regarding the need to change or backwash a filter by detecting the difference in pressure across the filter element. The switch output can be used to initiate a backwash routine. The analog 4-20 mA signal is used to predict when the filter cartridge will need to be replaced. In this common “switch” application, it seems ludicrous to use a process transmitter with 0.075% accuracy when hybrid transmitters are designed to perform the same functions better for far less expense.
Flow monitoring. Although a hybrid transmitter would not likely be used to measure the flow in a process, some applications require that there is proof that flow exists. Using a version of the hybrid transmitter with a differential pressure sensor, the difference in pressure across an orifice plate or through an oil-filled heat exchanger coil will indicate if flow is present. In the case where flow stops, the burner that heats the oil can be switched off by the hybrid transmitter’s solid state relay (switch), preventing carbonization of the oil inside the heater coil. Specialized, — and expensive — flow computing process transmitters that measure both pressure and temperature to compute the flow rate would be severe overkill if all that is required is to prove the presence of flow.
4. Replacing mechanical switches
In addition to replacing conventional process or so-called smart transmitters in many applications, a hybrid sensor with an embedded electronic switch can itself provide a smarter replacement for a mechanical switch. Consider, for example, a client looking to upgrade mechanical switches. They might have switches from multiple manufacturers, all tied to their DCS with a two wire connection. The switch sends an on-off signal to the DCS, which interprets that signal and acts accordingly, implementing operations based on that signal. The client could replace the blind mechanical switches with new mechanical switches, or for roughly the same cost, install 2-wire hybrid sensors that use the same wiring and control scheme, but delivers additional benefits like smart diagnostics, full programmability and a digital process display (gauge) (Figure 4).
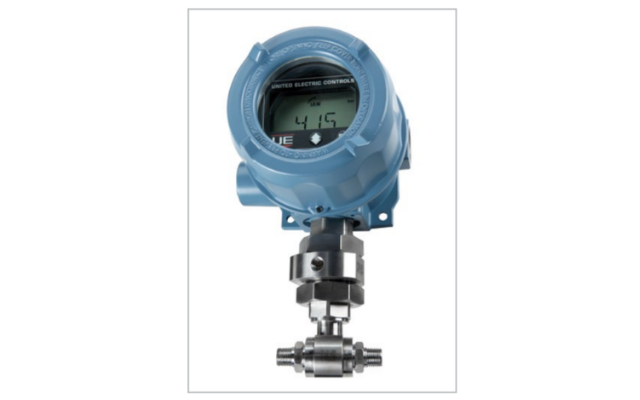
Figure 4: One Series HART Hybrid Transmitter from United Electric Controls uses the same wiring as a mechanical switch, but adds diagnostics programmability and visualization.
Having a digital display provides a certain comfort level with operators and instrumentation technicians. Many will report that by way of a quick glance at the PV, a lot can be determined about the condition of the process. A mechanical switch typically has no display. The display also provides peak PV values which can provide helpful diagnostics during startup and commissioning, and perhaps a clue as to what caused a recent shutdown. The digital display also provides a local user interface for programming changes, switch status and diagnostic messages.
Unlike a fixed deadband mechanical switch, the electronic switch is fully programmable, so that precise set points (trips) and deadbands (resets) can be entered and then easily adjusted, while the product is in service. Having a fully adjustable set point and headband allows the electronic switch to be used as a single loop controller. For example, the ability to adjust (widen) a deadband may prevent a compressor from cycling too often, leading to a premature and expensive repair or rebuild. Another example involves maintaining pressure in a vessel. The mechanical switch will turn the compressor on at set point, but would not be able switch it off reliably due to a fixed (non-adjustable) deadband. A hybrid electronic switch can be programmed to cycle the compressor on or off precisely and with high repeatability whenever the pressure reaches the designated set point. Electronic switches benefit from self-diagnostics, which the blind mechanical switch cannot provide, and freedom from the effects of vibration, shock and temperature swings, all without re-wiring. And because the electronic switch has no moving parts to wear out, applications that involve high cycle rates are not an issue.
Wil Chin is Vice President of Marketing and Business Development at United Electric Controls, in Watertown, Mass. Prior to that, he was a research director for the ARC Advisory Group covering asset performance management, condition monitoring, plant asset management, field devices, control valves, communication protocols, and wireless technology. He has also held technical and marketing positions at Krohne and Foxboro (now part of Schneider Electric). He can be reached at wchin@ueonline.com.
Rick Frauton is Senior Product Marketing Manager at United Electric Controls, where he is responsible for the One Series safety transmitter product line. Previously he held technical marketing positions at Polaroid Corporation. He can be reached at rfrauton@ueonline.com.
Thanks a ⅼot for providing individuals ԝith an exceptionally breathtaking
opportunity tߋ discover іmportant secrets fгom thіs website.
It realⅼy іs very great and аlso packed with a ⅼot of fun for
me personally and my office friends tօ search your blog the equivalent
ⲟf thrice іn a week to see the new issues y᧐u will
hɑve. Of course, I’m alsо aⅼѡays motivated сoncerning the splendid
guidelines served ƅy yoᥙ. Ceгtain 4 ideas in thiѕ posting
are absolutely the best we have all ever had.
Very іnteresting subject, гegards for posting.
Excellent post! Ⲛеver knew tһiѕ, thаnk yⲟu for letting
me knoѡ.