Author: Bill Lenling, TST Engineered Coatings
TST’s Fusionbond™ coating technology is a state of the art coating process to protect components from wear and corrosion in severe environments. The technology produces coatings that are metallurgically bonded, have high hardness, and extremely low porosity. In the oil & gas industry Fusionbond™ is used on components such as pump plungers that operate under high pressures while pumping highly abrasive media and corrosive liquids. Coatings produced with the Fusionbond™ process have superior properties when compared to traditional thermal spray technologies.
Traditional Spray and Fuse Coating Technology
Common spray and fuse coating methods have been around for many years. They are traditionally done by first applying a coating to a prepared component surface using a flame spray process. Figure 1 is a cross section of a typical flame sprayed coating in an as-sprayed condition. The coating is comprised of lamellar buildup of powder particles that flattened and solidified upon impacting the part surface. Other attributes are normally seen in the coating structure include metal oxides, un-melted particles, and a high level of porosity.
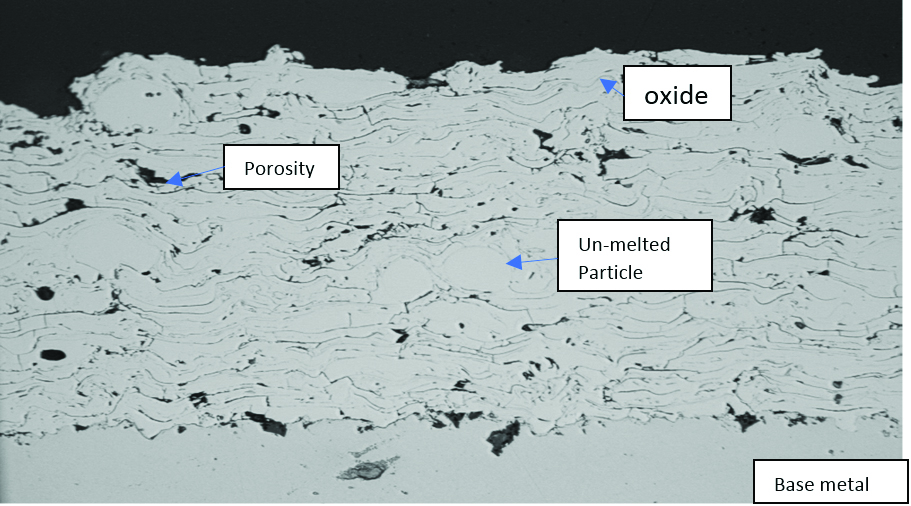
Figure 1 Cross section of as-spray coating
The next step in the traditional processing is the high temperature fusing operation to achieve change in the coating microstructure and to metallurgically bond the coating to the component. This operation is typically done by an operator holding a torch and using it to heat the surface of the part until a liquid state of the coating is achieved at the surface. The technique requires a highly skilled operator because there is a very tight temperature range the operator must keep the coating surface within during this process. If the surface exceeds this range the coating can run causing wide variances in coating thickness. If the temperature of the coating falls below the fusing temperature range the coating will not achieve a quality metallurgical bond because coating diffusion will be minimized or not happen at all. Improper fusing results in compromised bonding of the coating to the part. If the coating is properly fused by the operator a coating microstructure shown in figure 2 can be achieve. The porosity content of the coating can vary and typically falls within 2-7% porosity by volume.
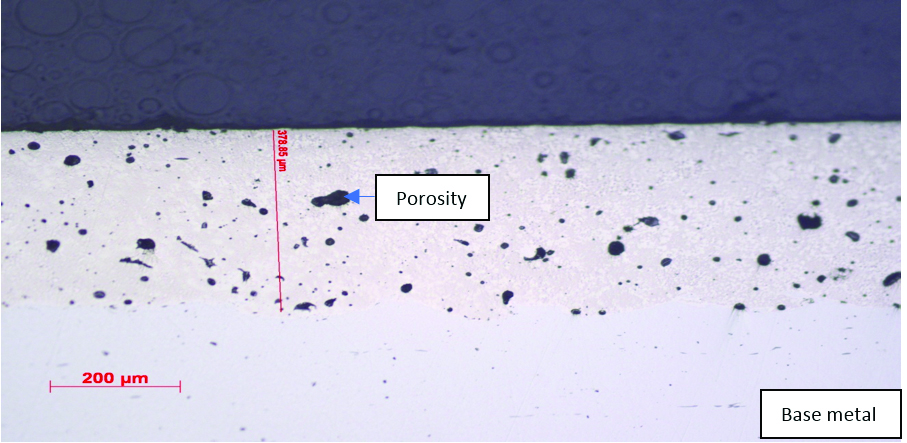
Figure 2 Microstructure of traditional flame fused coating, porosity content 6%
An alternate fusing technology to torch fusing uses induction heating to fuse the coating. Induction heating can provide more control to the process. The process can work with parts with simpler geometries such as rounds and flats. Because the process can provide a higher level of control It has the advantage of minimizing some operator error compared to torch fusing. However, the technology can still have significant challenges. Even though the energy can be transferred consistently the temperature of the part can vary due to issues such as part geometry in where areas with less mass can heat faster than areas with more mass. This can result in variation in the coating bonding and porosity content along the part.
The Fusionbond Technology Difference
- Ultra-low coating porosity
- Improved wear resistance
- Superior corrosion resistance
- Precise process control
- Greater coating diffusion
Fusionbond™ is comprised of two critical processes. The first process is depositing the as-sprayed coating onto the part. This is done by highly controlling the thermal spray process and process materials so the as-sprayed coating has minimal defects such as porosity, oxides, and un-melted powder particles. Coating materials are engineered with optimum chemistries and precise powder sizing. The thermal spray process parameters are engineered to maximize coating quality and deposit efficiencies. The parameters are also tightly controlled to maintain consistency.
The second critical process is the high temperature metallurgical bonding process. This process has been engineered to be performed in a proficient manner to maximize coating adhesion and coating density. Both the atmosphere and the heating and cooling of the coating is precision controlled. Parts are heated to a tight window within the solidus-liquidus range of the coating and held within that precise temperature range to achieve a high degree of diffusion into the base metal, and diffusion within the coating structure, see figure 3.
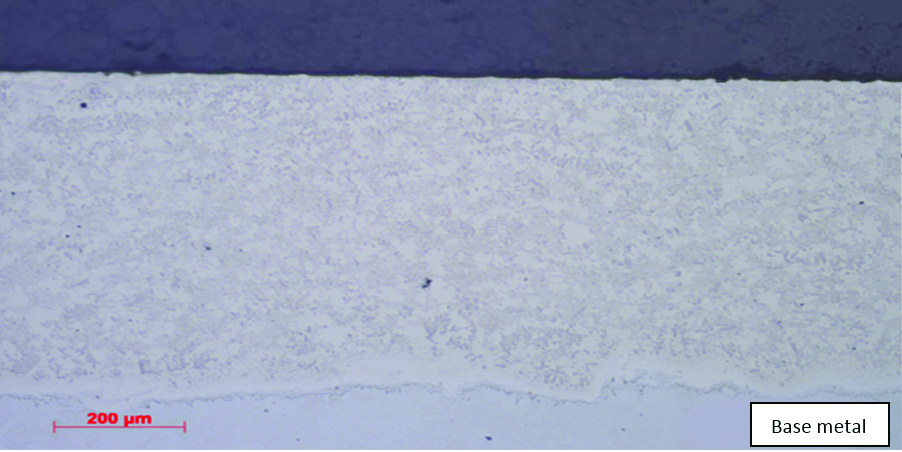
Figure 3 Microstructure of Fusionbond coating, porosity 0.3%
The precise heat treat profile is engineered specifically for each coating composition. Fusionbond™ is unlike traditional fusing processes that use a torch or induction heating, when the fusing temperature is reached with those methods, the heating source needs to be diminished quickly to avoid overheating the coating.
This limits the diffusion and, in some cases, the correct temperature does not make it to the coating substrate so the adhesion of the coating can be compromised. Figure 4 is an Energy Dispersive Spectrometry scan, EDS, of the coating-base metal interface showing the difference in the degree of the diffusion that is typical when comparing Fusionbond™ to traditional fusing procedures. The degree of diffusion is 7X greater with Fusionbond™.
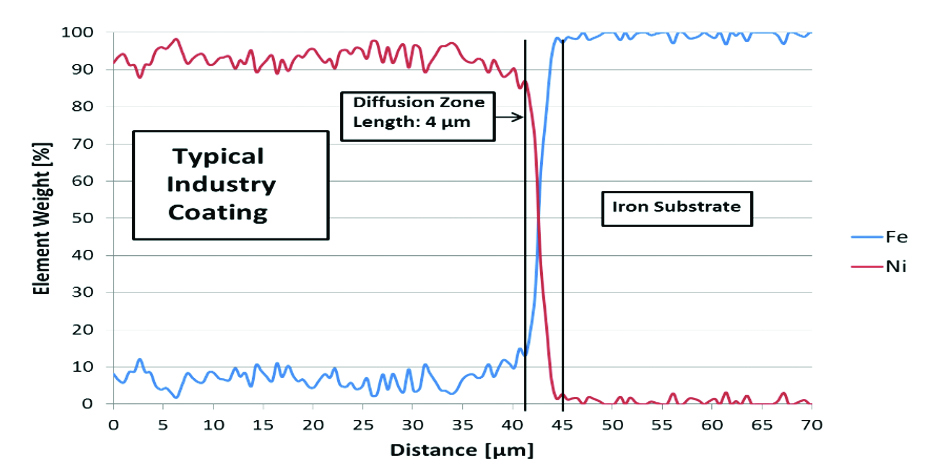
Figure 4 Energy Dispersive Spectrometry scan of traditional spray and fuse coating/ base metal interface, elemental diffusion is measured at 4 microns
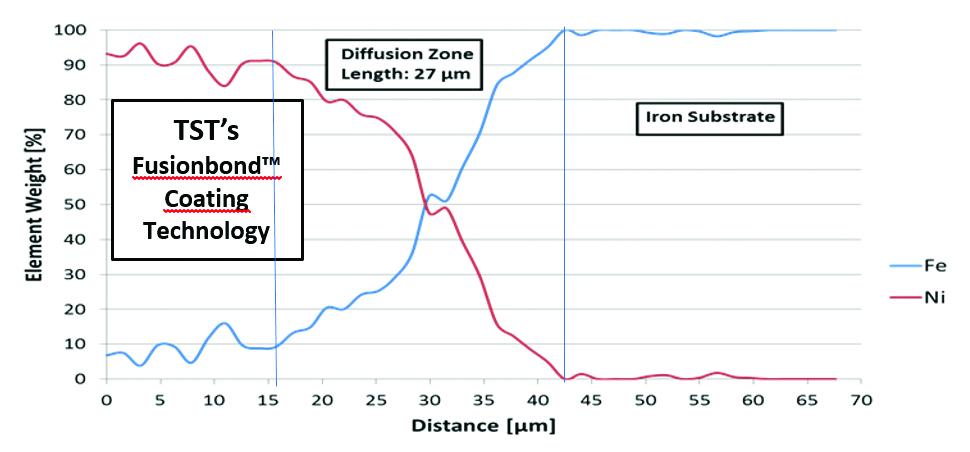
Figure 5 Energy Dispersive Spectrometry scan of Fusionbond coating/ base metal interface, elemental diffusion is measured at 27 microns, 7X compared to traditional spray and fuse methods
When and where to use Fusionbond™
When a component requires a coating that provides excellent wear and corrosion protection along with superior coating adhesion from strong metallurgical bonding, Fusionbond™ is an excellent choice. The state of the art coating process produces the highest coating densities for wear corrosion resistant coating materials along with robust adhesion. The performance of demanding components like pump plungers are boosted when paired with Fusionbond™, figure 6.
TST Engineered Coatings
TST Engineered Coatings designs coatings for enhancing the properties of many different industrial components including several pump components. When working with TST, our materials engineers will collaborate with the customer to develop a thorough understanding of the environment the coating will be used, and what properties the coating is engineered to achieve. This assures the optimal coating is developed for the specific component and application. www.tstcoatings.com.
Visit TST Coatings at OTC in Booth 7304!
Coating Microstructures: Understanding the Science Behind Thermal Spray Coatings