Contributor: Jennifer Cardillo, Marketing and Communications Manager Americas, Rotating Equipment Services, Sulzer
Southern California benefits from Sulzer’s global expertise and 24-7 response
Expert maintenance support is essential to minimizing downtime and ensuring ongoing performance, especially in the power generation sector. At the forefront of this industry is Sulzer, an independent maintenance provider that has recently expanded its support network to include the Colton Service Center in Southern California, where experts in rewinding motors and generators keep wind turbines operational.
Repairs and upgrades are usually preferred to replacement when it comes to larger pieces of rotating equipment because they offer a cost-effective solution that improves reliability and efficiency. Sulzer has been delivering independent maintenance services to operators of rotating equipment for decades and has built a global network of service centers that offers round-the-clock support.
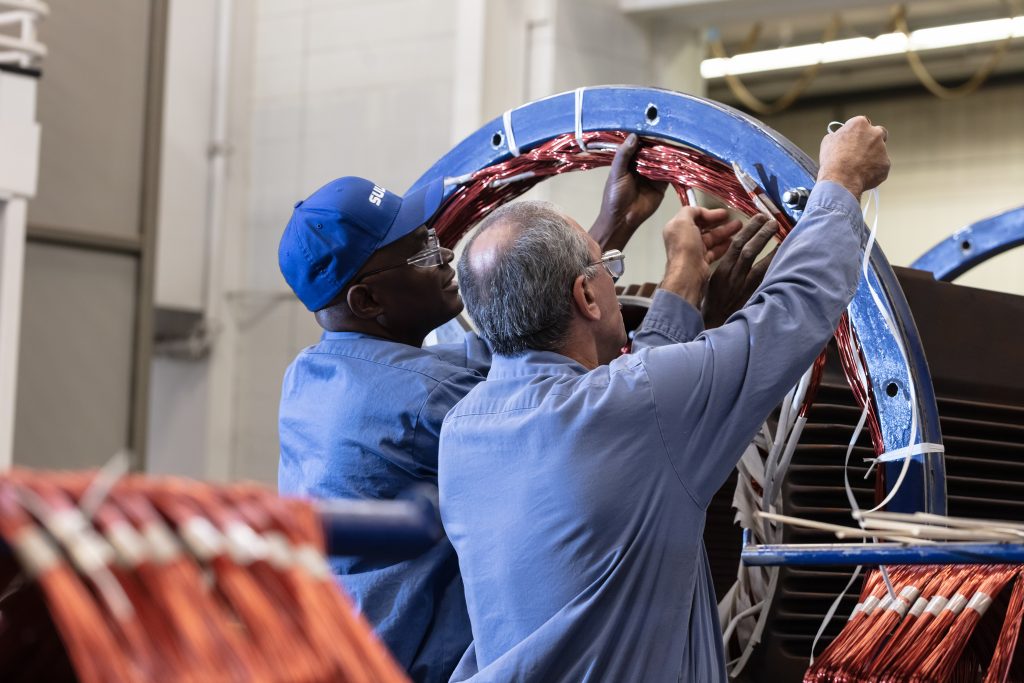
Engineers at Colton Service Center have expertise in rewinds for motors and generators. Photography By: Clint Brewer
Engineering improvement
Gary Patton, Colton Service Center Manager, explains: “We offer expertise in rewinds for motors and generators as well as having a full-service machine shop and specialist design and manufacturing facilities for motor control panels. The service center works with original equipment manufacturers (OEMs) to carry out inspections and warranty repairs as an approved supplier.”
This is exemplified by a recent intervention, where a 2’500 hp motor was manufactured with an inherent engineering flaw in the sealing mechanism that prevented oil ingress from the bearing cavity into the motor casing. On initial start-up, the customer found that most of the oil was immediately drained from the bearing cavity and deposited inside the motor casing. Engineers at Colton Service Center worked with the OEM to redesign, manufacture and install new seals, which have performed perfectly since.
Sulzer has a reputation for high quality workmanship and a fast turnaround for repairs. These qualities are essential when dealing with important infrastructure assets in the industrial and municipal sectors. Sulzer delivers the best possible solution for each situation by building relationships with customers and understanding their requirements.
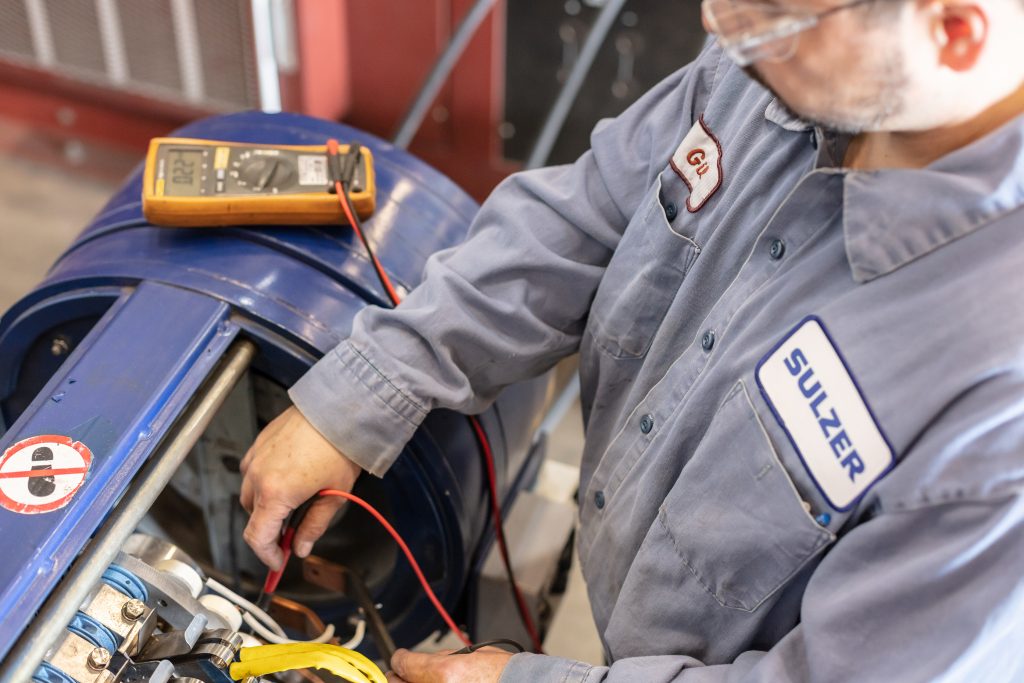
Tests are carried out to discover the condition of the wind turbine generator. Photography By: Clint Brewer
Case study: Fast delivery using exchange parts
In a case where a motor-gearbox combination from a vinegar manufacturer had been badly damaged by the operating atmosphere, an urgent repair was required. Instead of a complete rewind, Sulzer needed to deliver a faster solution. It replaced the complete stator, refitted the end covers with new seals and bearings and returned the motor to the customer within 12 hours, instead of the two days for a stator rewind.
The Colton Service Center has also accumulated considerable expertise in the maintenance and repair of wind turbines, especially the generators. Capable of rewinding anything between 50 kW and 3 MW, Sulzer ensures that turbine equipment will continue to deliver reliable service for many years to come.
Gary continues: “Operators whose turbines are no longer covered by the OEM warranty need to be able to count on a maintenance partner that is capable of delivering high-quality repairs, quickly. We have the necessary expertise and facilities to repair and test both mechanical and the electrical equipment.”
Minimizing downtime
Furthermore, this expertise extends to motor control panels, which can be designed, manufactured, and installed by experienced engineers. Site engineers can also diagnose faults and repair them, keeping downtime to a minimum.
Gary concludes: “We offer a wide range of services that focus on the power generation, water and other major industrial sectors. Our aim is to find innovative solutions using the highest quality materials and to deliver the best possible service for our customers.”
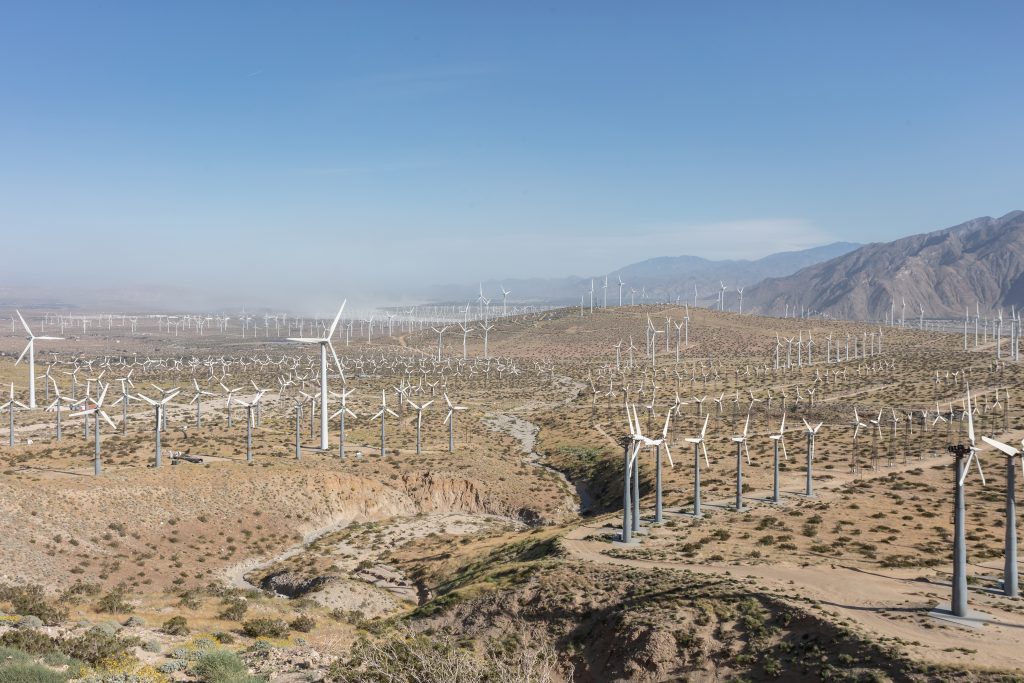
The Colton Service Center has also accumulated considerable expertise in the maintenance and repair of wind turbines. Photography By: Clint Brewer
About Sulzer:
Sulzer is the leading worldwide, independent service provider for the repair and maintenance of rotating machines including turbomachinery, pumps and electro-mechanical equipment. With a global network of over 180 technically advanced manufacturing and test facilities, Sulzer offers a collaborative advantage that delivers high-quality, cost-effective, customized and turnkey solutions, providing its customers with the peace of mind to focus on their core operations.
Sulzer Rotating Equipment Services, a division of Sulzer, can accommodate all brands of rotating equipment including turbines, compressors, generators, motors and pumps. With an enviable track record, dedicated teams of on-site engineers provide best-in-class solutions to ensure that the most effective service is delivered.
Sulzer is dedicated to providing superior service solutions to a range of industries including power generation, oil and gas, hydrocarbon and chemical processing, water and air separation. Every solution is customized to suit the business needs of each application – whenever or wherever that may be.
With a long history of providing engineering service support, Sulzer is headquartered in Winterthur, Switzerland where it began in 1834. Today, with sales over US$ 3 billion and with approximately 15,500 employees, the Sulzer footprint spans across the globe. The core aim is to deliver a flexible and cost-effective service that optimizes customer operational efficiency and minimizes downtime.
For more information on Sulzer, visit www.sulzer.com