Upgrading designs and materials: Using retrofit projects to improve efficiency and reliability
Fertilizer and other chemical manufacturing processes rely on several key pieces of rotating equipment to maintain efficient production rates. Using a preventative maintenance approach to uphold the reliability and efficiency of equipment is an important strategy. In addition to this, retrofit projects enable new materials and component designs to be integrated with legacy equipment, extending their service life and reducing operating costs.
Even the most urban of us rely on well fertilized soil. From the food we eat to the celebratory bouquet – plants need good soil. Everything that we farm is only as good as the soil that it is grown in. Fertilizers help farmers create nutrient-rich soils, which in turn will promote the growth of healthy plants.
Paul Richardson, Service Center Manager at Sulzer’s Middlesbrough Service Center, looks at how revitalizing existing rotating equipment can offer a cost-effective improvement in efficiency and reliability.
The equipment used in the chemical industry to manufacture fertilizer operates in a challenging environment, which can cause accelerated wear, reducing efficiency. The need to minimize capital expenditure means that replacement of machinery is not always a viable strategy. Rather than purchase new machinery, it can be more cost-effective to repair or modify existing plant equipment to extend its service life and make it more effective.
Proactive maintenance
Generally, turbines, compressors and pumps are all subject to a variety of process-driven conditions that contribute to corrosion, erosion, fouling and various other process-related issues and can be managed through effective maintenance intervention. Rotating equipment that is in direct contact with the process media and under constant attack, presents a major challenge. It is possible, however, to reduce degradation to a minimum by selecting the correct protective coating.
In the harshest of operating conditions, solid and/or liquid particles can pass through the equipment causing erosion. This can result in moderate to severe material loss and change aerodynamic efficiencies significantly. If left unattended, it can even affect the strength of the critical components and lead to premature blade/vane wear and failure in service.
In situations where these circumstances exist, and their effect needs to be minimized, specialized coatings can provide improved protection against fouling and erosion. These can be applied to both stationary and rotating blades as well as diaphragms, guide vanes, rotors and impellers. The exact composition of these coatings can be tailored to specific applications and will include an aluminum base coat for corrosion protection as well as an inorganic sealer and a specialist non-stick final layer.
Preventative maintenance: Improving reliability
The most effective way of avoiding downtime caused by machinery breakdown is to employ preventative maintenance techniques, such as vibration monitoring, partial discharge analysis and thermal imaging. These procedures can be very useful in monitoring the overall condition of equipment as well as its remaining lifetime.
Analyzing trends can reveal issues that would otherwise not be seen without disassembling the machine. Early indications of issues with bearings, coils, vane clearances or just general performance, allow remedial actions to be planned in during regular maintenance windows.
The advance warning also ensures that all the necessary personnel and parts can be assembled to ensure the most efficient use of time and any external resources that may be required.
Reducing downtime
Shutdown periods provide an extended opportunity to carry out maintenance as well as refurbishment and upgrade work. As such, they allow companies to improve the performance and reliability of their equipment without affecting productivity.
However, with many legacy pieces of equipment used in the chemical manufacturing sector, some may no longer have support from the OEMs, which means that alternative solutions need to be found when repairs and upgrades are required. In other cases, the lead-times offered by OEMs may not meet the needs of the business and an independent maintenance provider could be the best solution.
In situations where speed of response is essential to minimize downtime, taking advantage of the services and expertise offered by an experienced maintenance provider could be the best solution.
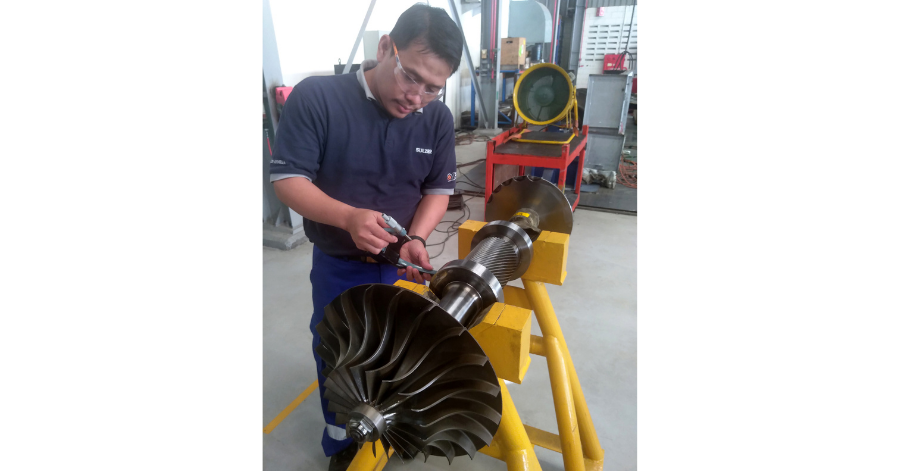
Compressor repairs included precision remanufacturing
Case study: Rapid rewind
For example, a CO2 compressor powered by an aging 1’300 kW high voltage motor had been identified for a complete rewind during a planned shutdown period. Sulzer identified the rewind option as the most cost-effective solution to extend the reliable service life of the motor without impacting productivity.
The project called for a complete rewind to be delivered within a 30-day window, which would require a fast turnaround. Since the OEM drawings were not available, the dimensions of the coils could not be established until the motor arrived in the service center to be dismantled.
As part of the repair, the coil designers were able to create the necessary drawings that would also deliver improved efficiency and performance for the refurbished motor. In cases such as this, where a motor has been in service for a few decades, the coil insulation will be of a lower specification than the materials used today.
Using class F insulation, which is thinner than the original materials, as well as improved processes, it is possible to increase the copper content of the coils to fill the gap that would otherwise be present. This additional copper also provides an incremental increase in efficiency as well as helping to reduce the operating temperature of the coils. By improving efficiency, the design modification also helps to reduce annual running costs.
In all, 60 coils were designed, manufactured and installed within the 30-day period. This was a complex operation and the engineers worked through the night to complete the brazing, taping, varnishing and testing, before the motor was returned to the customer.
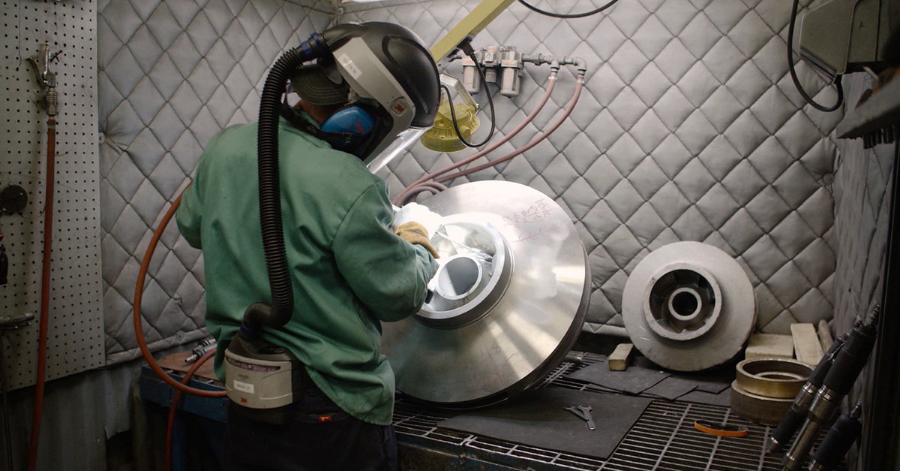
Replacement impellers can now be manufactured quickly to minimize downtime
Case study: Compressor savings
Modern centrifugal compressors deliver air or other gases at high volumes and high pressures into storage, transportation pipework or to downstream machinery. The machines themselves can be very large indeed, consuming hundreds of kW of power, but the critical component at their heart is a precision-engineered high-speed impeller, which can be just a few centimeters in diameter.
In one example, a compressor had been operating out of balance for some time and the resulting vibrations had caused extensive damage to the impeller, which was beyond repair. Since the compressor OEM was unable to offer a timely or cost-effective replacement, the company approached Sulzer.
A specialist engineering team was dispatched to collect all the data needed to recreate the part. Using a combination of laser scanning technology and conventional measurements, the team collected digital and dimensional inspection data to build a complete 3D representation of the impeller.
By applying engineering analysis to the geometry of the broken part they were able to “undo” the damage digitally and determine the precise geometry of the original component. The replacement part was machined from a single block using five-axis milling techniques.
After surface finishing, the new impeller was spin tested at high speed to check for any imbalance before being reassembled in the compressor. The entire process was completed within the timescale required by the operator and at a 40% cost saving over the replacement part from the OEM.
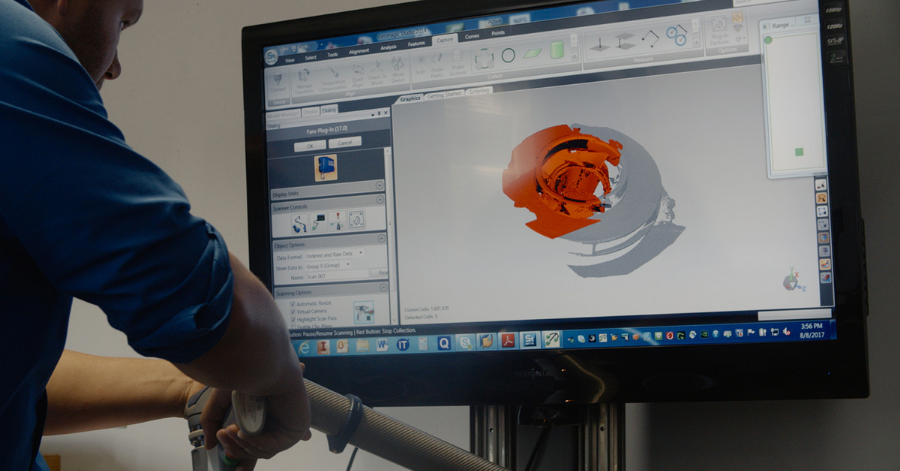
Precision mapping of complex components reduces lead-times on new parts
Fast repairs for pumps
Innovative solutions can also be applied to the huge number of pumps installed within the facility. Remanufacturing of impellers, balancing and bearing overhauls can all be accomplished within scheduled maintenance intervals, while the application of surface treatments can also be used to extend the operational life of these assets.
At the center of a pump’s design is the impeller, which provides an increase in the fluid head. As a result, impellers are subjected to the most damage, which can have a huge impact on efficiency, productivity and running costs. Therefore, it is important to be able to source new impellers when they are required and, if necessary, take advantage of the latest improvements in design and materials technology to increase reliability.
Creating replacement parts has become a much quicker process, with reverse engineering being used to design and manufacture enhanced components. Improvements to the flow geometry combined with the latest manufacturing techniques, such as using 5-axis milling or rapid prototyping techniques to print casting molds, can reduce the lead time required to procure the replacement parts and deliver significant improvements in performance and reliability.
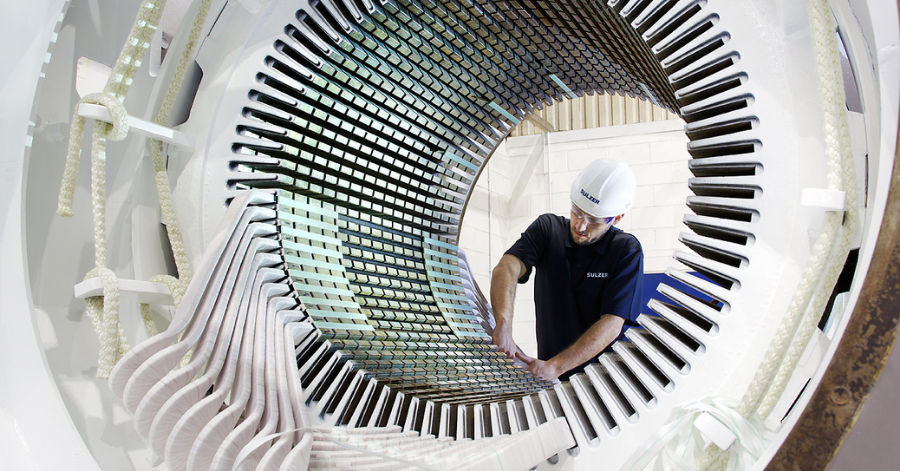
Stator rewinds extend the service lives of generators and large motors
Extending and optimizing legacy equipment
Modern design and manufacturing techniques, as well as advanced alloys and specialized coatings, can all have a beneficial effect on the expected lifetime of legacy equipment. In situations where either the lead time or the scale of the expenditure for new equipment do not fit the business’ expectations, alternatives, such as retrofit projects, can deliver cost-effective solutions within reduced timeframes.
The key to implementing the most effective solution is the experience and expertise of the solution provider. Turnkey projects are best delivered by those with all of the necessary skills and resources in house. For the end-user, a single point of contact that provides a full range of project options and continuous updates on progress, ensures the management of any upgrade is efficient as well as cost-effective.
About Sulzer
Sulzer is a global leader in fluid engineering. We specialize in pumping, agitation, mixing, separation and application technologies for fluids of all types. Our customers benefit from our commitment to innovation, performance and quality and from our responsive network of 180 world-class production facilities and service centers across the globe. Sulzer has been headquartered in Winterthur, Switzerland, since 1834. In 2019, our 16’500 employees delivered revenues of CHF 3.7 billion. Our shares are traded on the SIX Swiss Exchange (SIX: SUN).
Comments