Air seals are an essential component in various industrial applications, including pumps, mixers, and other rotating equipment. Here are five crucial things users should know about air seals:
Operating Principle:
- Air seals utilize a barrier of air or inert gas to prevent leakage of process fluids. Users need to understand that these seals work by creating a positive pressure barrier, which is greater than the process pressure, effectively preventing product leakage.
Installation Requirements:
- Proper installation is key to the functionality of air seals. Users must follow the manufacturer’s guidelines for installation, which often require precision and attention to detail. Incorrect installation can lead to premature failure or reduced efficiency of the seal.
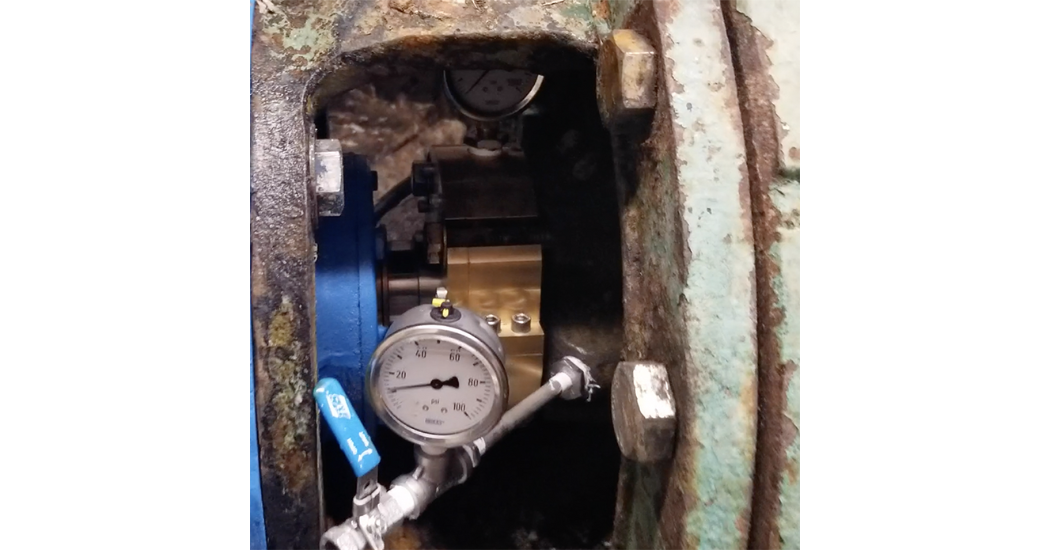
SEPCO SAS-P Installed
Maintenance Needs:
- While air seals are generally low maintenance, it’s important for users to periodically check the air supply system for pressure stability, flow rate, and cleanliness. Any contaminant in the air supply can affect the seal’s performance.
Application Suitability:
- Users should be aware that air seals are best suited for applications where contact with the process fluid must be avoided, such as with abrasive, corrosive, or toxic fluids. It’s essential to select an air seal that is appropriate for the specific service conditions and fluid properties.
Economic and Environmental Impact:
- Air seals can offer economic benefits by reducing product loss and extending the maintenance intervals for the equipment. They also have environmental benefits, as they help to reduce emissions and contamination. Users should consider the life cycle cost and environmental impact when selecting an air seal for their application.
By understanding these key aspects, users can make informed decisions about the selection, use, and maintenance of air seals, ensuring their systems operate efficiently and reliably.