Author: Heinz Bloch
Viscosity is by far the most important property of the lubricants applied to process pump bearings and recent, highly practical texts deal with the issue in great detail (Ref. 1). In general, thicker oil films will give better pump bearing protection than thinner oil films. For process pumps with rolling element bearings, ISO Grade 68 lube oils will allow higher operating loads. They are generally preferred over ISO Grade 32 lubricants.
But not all application methods are possible with ISO viscosity grades higher than VG 32. How to capture the benefits of thicker lubricants without actually using them or how to best apply ISO VG 68 and thicker oils will be one of our subjects.
Figs. 1 and 2 allow quick determination if a particular lubricant selection is in the right range. Suppose we were dealing with an 1,800 rpm pump and its bearings had bore diameters of 65 mm (dimension d) with bearing outer diameters (D) of 120 mm.
Since dm = 0.5 (d+D), in this case dm = 92 mm. Enter the horizontal x-axis of Fig. 1 at this calculated mean dimension and plot upward to intersect an imaginary 1,800 rpm diagonal line–just above the 2,000 rpm diagonal. From there, move to the left and read off ~11 mm^2/s (a measure of viscosity that is more commonly called 11 centistokes, generally abbreviated as cSt.
We have now established that, in this example, the minimum kinematic viscosity required to give adequate protection at operating temperature is 11 cSt. Since oils become thinner when heated up and if our operating temperature is very high, we realize we should have selected a thicker oil. As this thicker oil then reaches a higher operating temperature it will, hopefully, not “thin out” to a viscosity below 11 cSt.
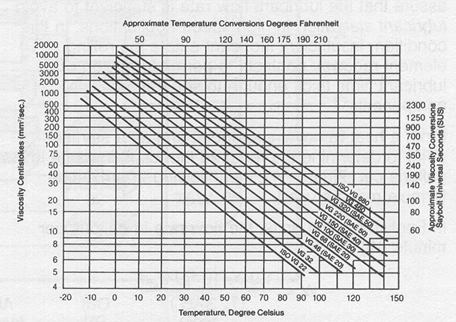
Fig. 2: For a required viscosity (vertical scale), the permissible bearing operating temperatures (horizontal scale) increases as thicker oils are chosen (diagonal lines)
Continuing on Fig. 2, we must now either assume a certain bearing operating temperature, say, 70 degrees C or 158 degrees F. Entering the horizontal x-axis scale at 70 C and moving upwards to ISO VG 68 would allow us to read off 20 cSt on the vertical scale—close to twice what we need. (Important: We should always ascertain that our oil delivery system works with this thicker-than-needed oil.) We might pick ISO
VG 32 and, as long as our actual bearing operating temperature does not exceed our assumed temperature of 70 degrees C, we would now read off (from the vertical y-scale) an operating viscosity of 11 cSt—just right.
We could also use Fig. 2 by entering the vertical y-scale at the required 11 cSt and, after intersecting a particular viscosity grade oil, plot down to read off the maximum allowable bearing operating temperature on the horizontal x-scale. Thus intersecting at, say, VG 68, would tell us that this oil could be allowed to reach 92 degrees C and still satisfy our viscosity requirement of 11 cSt (Ref. 1).
Thicker film oils are easily and reliably applied with oil mist methods (Ref. 3), but thick oils get us into trouble with careless pump manufacturers who sometimes forget to put a drain hole at locations where bearings butt up against a shoulder (Fig. 3, Ref. 4). Sooner or later the stagnant puddle of oil will overheat and turn into tar, which is not good for bearings. (As we then get short bearing life, the pump manufacturer will deny culpability and avoid class action suits). Also, thick oils can be quite difficult to apply with only the standard oil rings found in many pumps.
Running a pump one might ultimately achieve an operating temperature that allows a certain thick oil to flow nicely. But what if, at startup, the initial operating temperature is quite low and the oil will not flow? That’s what often happens when someone buys a standard “multipurpose oil” without really thinking things through.
In slow and medium speed pumps lubricant is usually applied with the oil level reaching to the center of bearing elements at the 6-o’clock position. In these instances, ISO Viscosity Grade 68 allows operation in a relatively wide range of ambient temperatures.
However, in applications using oil rings and with oil levels reduced below the periphery of the lowermost bearing component, premium-grade synthetic ISO Grade 32 lubricants may have to be used simply because not all oil rings will work with thicker than ISO VG32 oils. Synthetic ISO VG 32 with a high VI (viscosity index) serve us best.
Here are a few general guidelines worth considering:
- Using a mineral oil would generally require oil to be changed every 6 to 12 months. With a clean, premium grade synthetic lubricant one would typically extend oil change intervals to about 24 months. Much debris can be kept away from the oil by simply using a set of advanced bearing housing protector seals. You will recognize these protector seals by their axially-moving O-rings.
- ISO Grade 32 mineral oils are often considered too thin for pump bearings. They rarely qualify for long-term, risk-free use in pumps equipped with rolling element bearings in typical North American and European ambient conditions. But simply switching to ISO Grade 68 mineral oils will be risky for bearings that are fed by oil rings.
- Appropriately formulated with the right base stock and with proprietary additives, ISO VG 32 synthetics are quite acceptable from film strength and film thickness points of view ( 1 and 3). In fact, the performance of some ISO VG 32 synthetics duplicates that of ISO VG 68 mineral oils. These superior ISO VG 32 synthetics excel by simultaneously satisfying the requirements of sleeve bearings and rolling element bearings (Ref. 1).
Superior synthetics achieve high film strength through proprietary additives. So, there can be significant differences in the performance of two lubricants of the same viscosity and using the same base stocks. Only one might be suitable for highest reliability services and an honest lube application engineer/specialist from a reputable provider or lube manufacturer can give you sound guidance. Try to link up with sales and marketing people with staying power. In 1976 or thereabouts I worked with such a person. She is still working for the same prosperous company today.
Finally, the notion that one oil type or viscosity suits all applications is never correct and is easy to disprove. Similarly, no fixed or particular oil ring geometry is ideally suited for all oil types and viscosities. Custom-designed oil rings may be required to work with the thicker oils at certain high shaft DN values.
Read: When and why high film strength synthetic lubricants are used
References
- Bloch, Heinz P.; “Pump Wisdom: Problem Solving for Operators and Specialists,” (2011), Wiley & Sons, Hoboken, NJ, (ISBN 978-1-118-04123-9)
- SKF USA, Kulpsville, Pennsylvania; General Catalog, 2008, (Engineering Section of catalog)
- Bloch, Heinz P. and Kenneth Bannister; (2017) “Practical Lubrication for Industrial Facilities”, 3rd Edition, Fairmont Press, Lilburn, GA 30047, ISBN 978-1-138-62679-973-579-5
- Bradshaw, Simon, Presentation at 17 Texas A&M International Pump User’s Symposium, Houston, TX, September 2000