Contributor: Johann Fourrat-Besson, Mouvex®, PSG®
There may be no more globally famous consumer brand than Coca-Cola. As one of the most recognizable brands in the world, there is no one that either hasn’t tasted a Coke, or one of its 130 associated beverage brands, or doesn’t recognize the Coca-Cola logo or its iconic contour bottle. Many of its ad slogans have even entered the everyday vernacular, reinforcing its marketing impact, including “It’s the Real Thing” (1969), “Have a Coke and a Smile” (1979) and “Open Happiness” (2009).
Always looking to introduce innovative processes and products while maintaining the traditions and product quality that are demanded of such a well-known company can be a daunting task. To that end, The Coca-Cola Co., which has its global headquarters in Atlanta, GA, USA, works hard to ensure that its bottling partners around the globe march to the beat of the same drummer. This means that all of them are charged with meeting the expectations of consumers while simultaneously producing their products at the highest levels of corporate responsibility and environmental sustainability.
In parts of Europe and Africa, this task falls to the Coca-Cola Hellenic Bottling Company (HBC), Zug, Switzerland, which was formed in 2000 when the Hellenic Bottling Company SA acquired Coca-Cola Beverages Ltd. Today, Coca-Cola HBC operates in 28 countries ranging from Ireland in the west to the Pacific Coast of Russia in the east and the Arctic Circle in the north to Nigeria in the south. In 2015, Coca-Cola HBC produced more than two billion unit cases, or the equivalent of approximately 50 billion servings, of sparkling (carbonated) soft drinks and still drinks like water, juices, teas and energy drinks, with reported net sales revenue in the region of €6.3 billion (US$7.04 billion).
Just as important as ensuring product quality, Coca-Cola HBC prides itself on the fact that its 59 production plants, 289 filling lines and 292 warehouse and distribution centers operate in the most environmentally sensitive and cost-efficient way possible. This commitment was acknowledged in 2014 and 2015 when the company topped the Dow Jones Sustainability Indexes (DJSI) both globally and in Europe. The DJSI honors those companies that have shown an ability to continuously improve their sustainability performance.
Sustaining A Passion For Excellence
Sustainability is integrated across every aspect of Coca-Cola HBC’s business as the company looks to be a leader in the industry in terms of customer service and cost efficiency. In Hungary, where this year’s Coca-Cola ad slogan is “Kóstold meg az érzést” (“Taste the Feeling”), Coca-Cola HBC operates nine facilities, two of which are manufacturing plants while the rest are warehouses. The largest Coca-Cola bottling plant in Hungary is in the city of Dunaharaszti, located about 15 kilometers (10 miles) south of the Hungarian capital of Budapest. The man responsible for meeting Coca-Cola HBC’s meticulous standards regarding production and sustainability is Zoltán Marincsák, who is the Maintenance Manager for the Coca-Cola HBC Dunaharaszti facility.
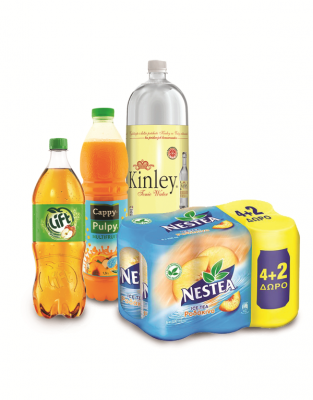
As one of the most recognizable brands in the world, there is no one that either hasn’t tasted a Coke, or one
of its 130 associated beverage brands.
“Sustainability at Coca-Cola is very important,” Marincsák explained. “Coca-Cola is the most famous brand in the world, so people expect a certain quality, and we also try to reduce day by day our carbon footprint or effect on the environment.”
The beverage-production process in Dunaharaszti involves the facility receiving constant shipments of different consignments of raw materials and components such as sugar, concentrates, bases and syrups. These components are then transformed into the most popular drinks like Coke, Sprite, Cappy Juices, Nestea Iced Tea, Kinley, Lift and Powerade sports drinks.
A key link in the production chain is the unloading of the tanker trucks that deliver the base components to the syrup room. Focusing on production efficiency, Coca-Cola HBC decided to employ a “just in time” approach for its supply of concentrates. Because of this, it is imperative that unloading times are optimized and that no delays are experienced, lest the strict production schedule be compromised. Knowing that the fabrication of beverages has to adhere to rigorous regulations and guidelines, these concentrates, bases and syrups must be handled in the most sanitary manner possible in order to avoid the risk of bacteriological contamination.
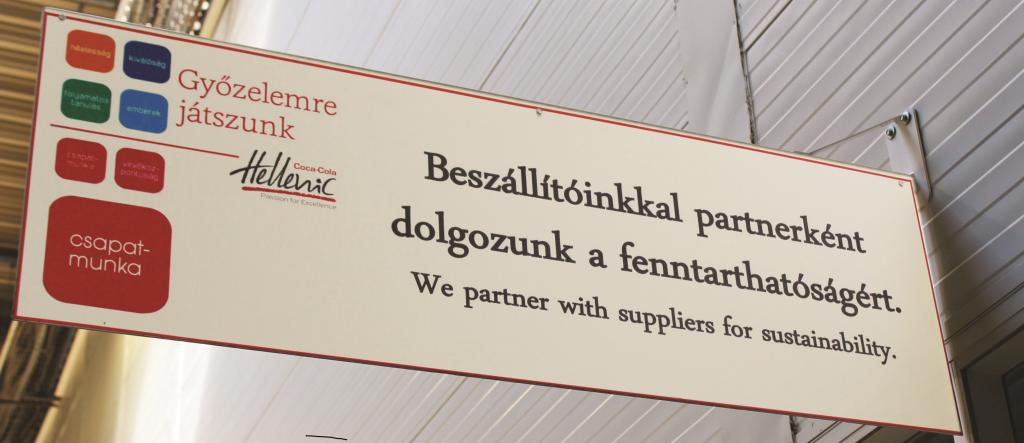
Sustainability is integrated across every aspect of Coca Cola HBC’s business as the company looks to be a
leader in the industry in terms of customer service and cost efficiency. Coca-Cola HBC prides itself on the
fact that its 59 production plants, 289 filling lines and 292 warehouse and distribution centers operate in the
most environmentally sensitive and cost-efficient way possible.
This puts tremendous pressure on the pumps that are used to unload the tankers and transfer the beverage components to their specific storage and holding tanks. The unloading of these trucks was a job that the existing twin screw pumps were finding increasingly difficult to perform safely and satisfactorily at the Dunaharaszti plant.
“It would also take about four to six hours to empty one tank, and due to the low temperature and highly viscous nature of the concentrates we were transferring, the pumps would sometimes freeze,” said Marincsák. “It’s important that the pumps work every time because the trucks are always coming in and all of our production is scheduled just-in-time. We cannot have any stoppages, and if there are, I have to schedule maintenance, therefore, I need to know every time that the system will operate as I require. The twin screw pumps were not able to empty out the total system, so from every tanker we had a lot of wasted product.”
Seeing Is Believing
With frustration mounting, Marincsák began a search for a solution and turned to PROBC Kft., a Miskolc, Hungary-based distributor of pumps and industrial equipment for use in industrial liquid-transfer applications. During a visit to the Coca-Cola HBC Dunaharaszti facility to assess the situation, it became immediately clear to Richard Lackner and David Pétervári, Co-Owners of PROBC, that the existing pump technology was at the root of the facility’s bottleneck.
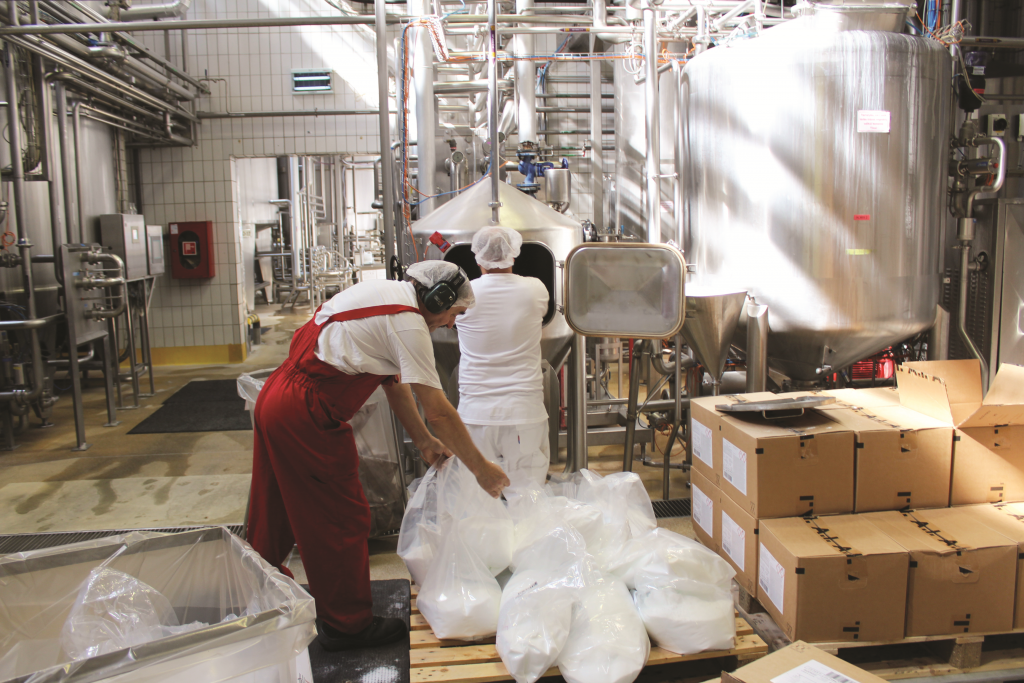
The beverage-production process in Dunaharaszti involves the facility receiving constant shipments of
different consignments of raw materials and components such as sugar, concentrates, bases and syrups.
“We realized that the main challenge was with the pump, but there was also an improvement to be done in the piping at the connection to the system,” recalled Pétervári. “By changing the pump and adapting the piping, we knew they could solve the problems that the twin screw pump was causing, including low unloading speeds from trucks, cavitation that caused noise, large energy consumption and very high maintenance costs.”
PROBC’s solution was to introduce the SLS Series Eccentric Disc Pump from Mouvex®, Auxerre, France, a product brand of PSG®, a Dover company, Oakbrook Terrace, IL, USA. SLS Series pumps have been designed for use in the food, beverage, cosmetic and pharmaceutical industries, all of which require extremely hygienic operations. What sets the SLS Series pumps apart is an innovative seal-less design that incorporates a hermetic pump head with a self-adjustable eccentric shaft protected by a double-wall stainless-steel bellows that ensure long life and product safety. Eliminating mechanical seals, packing and magnetic drives, the way Mouvex pumps are constructed reduces the risk of product contamination and costly leakages while avoiding messy spills, waste and product spoilage. This design has helped the SLS pumps earn certification from EC 1935/2004, EHEDG, 3A and FDA for use in food-processing applications.
Along with these advancements, the eccentric disc technology offers a range of innovative benefits, including strong vacuum and compression effect for enhanced line stripping and optimized product recovery; low shear rate; self-priming and dry-run capabilities; exceptional volumetric consistency; no slip; and almost completely pulsation-free operation. Due to the fact that the pump has only two wear parts, maintenance is easy and can be performed while the pump is inline.
“The Mouvex eccentric disc technology has a lot of benefits for Coca-Cola HBC,” said Pétervári. “In this case, the elimination of cavitation and vibration, the improvement of unloading times to around two hours, a reduced energy consumption, and CIP and water savings – no flushing water is necessary since the pump is seal-less. But the best benefit for Coca-Cola HBC is that the SLS pump guarantees a higher rate of product recovery because the Mouvex pump can suck much more concentrate from the container and push more of it through the pipeline to the tank.”
Pétervári provided an SLS test pump to Coca-Cola HBC and for Marincsák seeing was definitely believing. In fact, he was so impressed he didn’t want the test pump to be taken away after he had seen it in action.
“After the trial period, they were going to return the trial pump and we said, ‘No! We would like to keep the Mouvex!’” Marincsák chuckled.
After his own SLS Series pump had been installed, Marincsák has also had no reason to question his decision to deploy a different pump technology.
“Food safety is critical because it’s a hygienic industry and it’s very important that there are no seals where foreign material can enter the system, so the hygienic design of the Mouvex pump is very important,” he said. “Although there was a strong argument to justify integrating the Mouvex pump into the system, the key selling point was the recovery of pure concentrate and the contribution to the facility’s sustainability goals. There used to be more than 300 kilograms (660 pounds) left in the truck and pipe system with the old pump. With the Mouvex, less than 100 kilograms (220 pounds) remain in the pump and the piping system. So, if we reduce waste by 200 kilograms per load and recover more than one ton, that saves thousands of euros.”
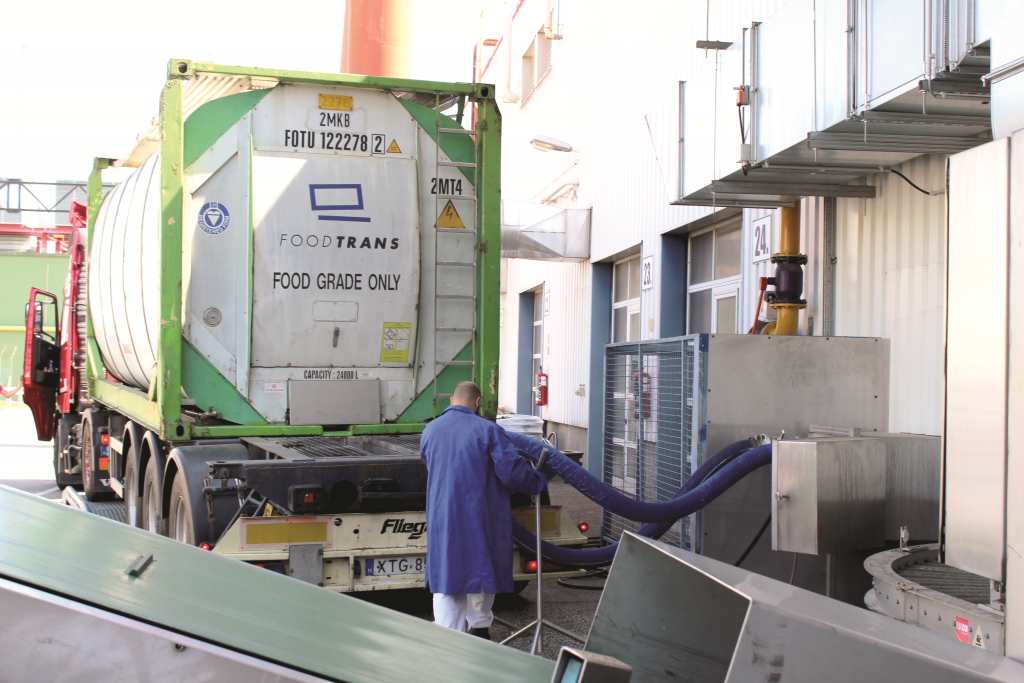
A key link in the production chain is the unloading of the tanker trucks that deliver the base components to the syrup room; it is imperative that unloading times are optimized and that no delays are experienced.
A key to the Mouvex pump’s enhanced product-recovery capability is its unique conveying principle. This principle is based on two stainless-steel components – the static cylinder and the moving piston – driven by an eccentric shaft, which generates a circular movement. Through this movement the inner and outer chambers are formed, which displace the liquid from the suction side to the pressure side with an impressively consistent and accurate flow. Given that the pump can run dry, the rotation of the parts creates a compressor effect that facilitates the stripping of discharge lines.
Conclusion
Considering Coca-Cola’s strengths and market leadership, they have to work hard to satisfy evolving consumer preferences and guarantee sustainable value over the long term. With a reputation as revered as Coca-Cola’s you can’t afford to experience any degradation in product quality or sustainability aspects. When the operations at the Coca-Cola HBC plant in Hungary were beginning to be compromised by the ill-performing twin screw pump technology, Zoltán Marincsák knew it was time to search for an innovative solution, and he has found the perfect answer in the SLS Series Eccentric Disc Pump from Mouvex.
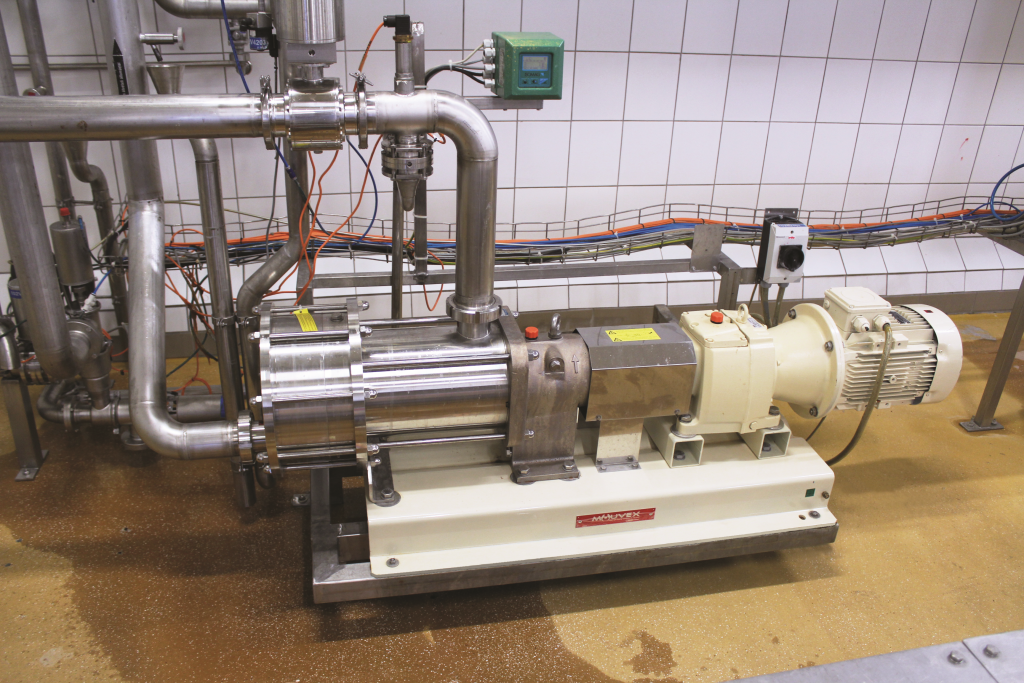
What sets the Mouvex ® SLS Series Eccentric Disc Pump apart is an innovative seal-less design that incorporates a hermetic pump head with a self-adjusting eccentric shaft protected by a double-wall stainless-steel bellows that ensure long life and product safety.
“The reliability of the equipment is very important because we provide high-quality products and to create them we need high-quality equipment,” he said. “With the Mouvex pump we eliminate waste, we reduce water and energy consumption, and our maintenance costs are reduced. We also get very, very good technical support from PROBC and PSG, which is very important to me.”
About the Author:
Johann Fourrat-Besson is the Industry Product Manager for Mouvex® and can be reached at johann.fourrat-besson@psgdover.com or +33 386 498 669. Auxerre, France-based Mouvex was incorporated in 1906 and is a leading manufacturer of positive displacement pumps, screw compressors and hydraulic coolers for use in the refined-fuels, oilfield, energy, food/sanitary, military, transport and chemical-process industries. Mouvex is a product brand of PSG®, a Dover company. Headquartered in Oakbrook Terrace, IL, USA, PSG is comprised of several leading pump brands, including Abaque™, All-Flo, Almatec®, Blackmer®, Ebsray®, EnviroGear®, Griswold®, Mouvex®, Neptune™, Quattroflow™, RedScrew™ and Wilden®. For more information on Mouvex or PSG, please go to mouvex.com or psgdover.com.
Mouvex® A Series Pumps Meet the Challenges in Oil & Gas Market