As technologies advance, and new demands are placed on systems for special functionality, it creates new challenges for the right pump to be selected and meet the specifications of the application.
Water Jet Cutting has gained increased acceptance in manufacturing processes due to the many advantages it offers. A narrowly focussed stream of water under high pressure and moving at a high velocity is a potent source of energy that can cut through metals and hard materials. There are some similarities with lasers, but without the complexity. Water jet cutting systems are simple, environmentally friendly, and relatively less costly.
A high pressure water stream is adequate to cut through softer metals such as aluminum. Harder materials may require an abrasive to be added to the water jet. Typically, sand or garnet is used as the additive. On the downstream side, the water will contain abrasives as well as the particles removed from the cutting surface. This abrasive slurry is collected in a cutting pool below the machine and has to be pumped to a separation pool and subsequently separated. The solid particles consisting of the abrasive and the residual cuttings from the material that has been cut, are bagged and disposed appropriately, and the cleaned water can be recycled.
The water jet cutting process is very suitable for cutting complex shapes and removes very little material so the dimension of the final part is more precise. Since there is no heat generated at the cutting surface, the properties and structure of the material being cut is unchanged.
NETZSCH Pumps & Systems, a leading global manufacturer of pumps, has developed the TORNADO® T2 Lobe Pump which is specially suited for situations that involve slurries with fine particles of aggressive abrasives, and is ideally suited for Water Jet Cutting Systems. It can pump the slurry from the cutting pool to the separation pool, and also from the separation pool back to the cutting pool.
The TORNADO® T2 pump is the most innovative Rotary Lobe Pump. It has been optimized for excellent performance and the design has been simplified for ease of minimal maintenance. It can be assembled and disassembled without requiring special tools, and requires very little space, as very often pumps are installed in tight spaces. Synchronizing the lobes is simple with a tool that forms an integral part of the housing cover. It is a Full-Service-In-Place Pump.
The NETZSCH Rotary Lobe Pump provides maximum operational performance, high reliability, and durability, ease of maintenance, and a low total life cycle cost. It is service friendly and has a smaller footprint. It handles shear-sensitive fluids, permits reversible operation, and can be serviced without disconnecting pipework.
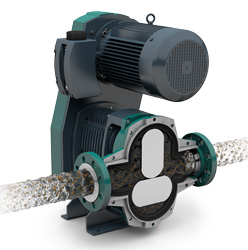
The NETZSCH TORNADO® T2 Rotary Lobe Pump can be used for almost any media on internittent, continuous or metering applications.
The pumping of abrasive fluids is generally difficult, and when the abrasives are in fine particles, the process is much more destructive to the pump components. The unique design and the precision of the rotating parts play a key role in the longevity of the TORNADO® T2 Lobe Pump.
In other types of pumps, the erosion of the rotating parts can be very severe. If the lobes have to be changed, this is not only expensive but the removal and replacement of lobes can result in significant downtime. Another common problem in handling fine abrasives is the wear that occurs due to the abrasives being squeezed through narrow clearances. The NETZSCH TORNADO® T2 is designed in such a way that the synchronized rotation of the lobes allows sufficient clearance to prevent the abrasive from causing erosion of the lobe surface. This is a huge advantage compared to competitive Rotary Lobe Pumps.
In the NETZSCH TORNADO® T2, the wearing part is the elastomeric liner and it can be easily and quickly replaced.
Since the rotating parts do not rub against the liner, the erosion is very slow and it is an inexpensive part to replace. Competitor pumps experience greater wear on the lobes which are expensive and time-consuming to replace.
The TORNADO® T2 Rotary Lobe Pump optimizes the total cost of ownership. The revolutionary design of the pump head extends the system lifetime and improves the performance of the major components. The modular design approach reduces the overall life cycle costs. The choice of materials of construction reduce weight and energy consumption. Most significant of all, is the elimination of oil in the drive unit which lowers operational costs and makes the system environmentally friendly.
The high performance and low overall ownership cost makes NETZSCH pumps a cost-effective option.
One installation of the NETZSCH Lobe Pump in a Water Jet Cutting Machine System transports the mixture of water and abrasives from the cutting pool to the separation pool. As needed, it can also be installed to pump the water back to the cutting pool. Some of Europe’s biggest Water Jet Cutting Machine producers are using NETZSCH pumps, as well as some of their customers. These pumps have been operating successfully for more than two years.
A company in Europe has been using a TORNADO® T2 pump on their machine. The flow rate – at this particular installation – ranges from 44 to 66 gallons per minute (10 to 15 cubic meters per hour) with a differential pressure of 57 to 87 pounds per square inch (3.9 to 5.9 bar).
The rotational speed is between 150 and 220 rpm and the operating temperature is 68 degrees Fahrenheit (20 degrees centigrade). The pump operates 8 hours per day and has been in use for more than18 months. The customer is very satisfied with the performance of the pump, and the quality and service provided by the NETZSCH team.