Mining equipment maintenance can take between 35% and 50% of a company’s total expenditure on the project. This shows that a significant portion of a mining project’s budget is spent to keep the equipment running.
The mining industry spends billions of dollars annually on maintenance, which is only expected to rise—mining equipment is expensive and must withstand a lot of wear and tear.
In addition to proper equipment maintenance, a good mining project must have a good maintenance technician to keep the project running smoothly. After all, technicians make sure that the equipment is adequately maintained and repaired when necessary. Therefore, the techs are invaluable to the company and the project.
In the next 600 words, we’ll show 5 ways maintenance technicians save costs on mining projects. Let’s get started!
1. Remote diagnostics and troubleshooting
The ability to use remote diagnostics and troubleshooting are core skills for any maintenance technician. Before this technological advancement, a technician had to be on-site to inspect and diagnose problems.
With the advent of new technologies, such as remote desktop sharing and cloud-based file storage, it is now possible to connect to equipment and systems from anywhere in the world —this led to a dramatic reduction in the need for on-site visits and the associated costs of travel and accommodation.
Also, it increased sustainability in mining projects as technicians can now work from home. When technicians detect an issue, they can use diagnostic tools to troubleshoot the problem and identify the root cause. By doing this, they can also help prevent future issues.
2. Enhanced risk-based maintenance management
The whole reason for mining is to unearth valuable materials that various industries can use. The costs associated with mining are significant, so mining companies need to find ways to reduce expenses and increase profits. One way to do this is by implementing an enhanced risk-based maintenance (RBM) program.
RBM is a data-driven approach to maintenance that uses information about a mining operation’s equipment and processes to prioritize maintenance activities. By identifying and addressing potential problems before they occur, RBM can help mining companies avoid costly downtime and repair bills.
In addition to reducing costs, RBM can improve safety by helping to prevent accidents and injuries. When properly implemented by technicians, this maintenance approach can be a powerful tool for improving the bottom line of any mining operation.
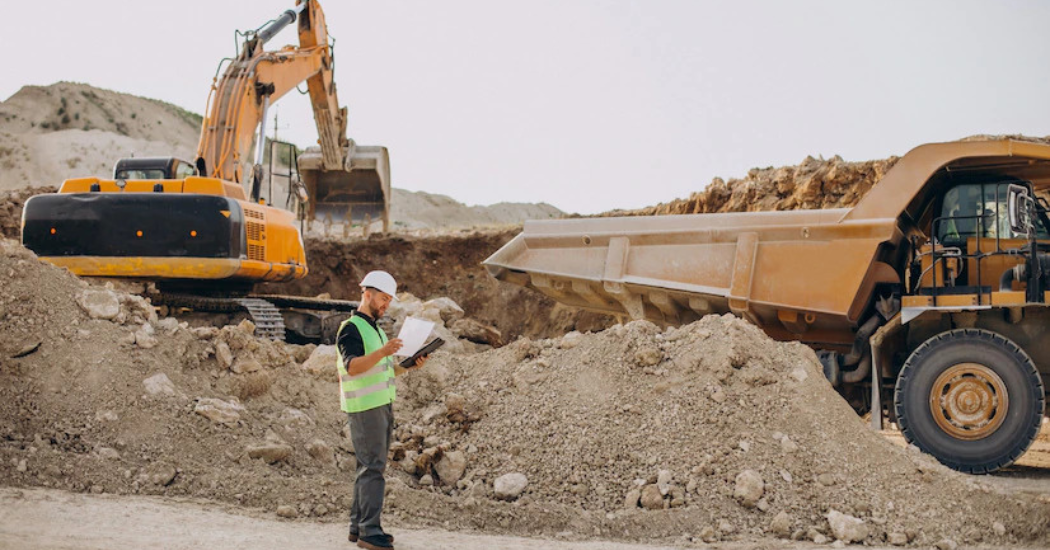
Source: Freepik
3. Improved maintenance scheduling
Since mining is a capital-intensive industry, projects require a lot of fixed assets. To keep the project up and running, you need to maintain your equipment properly —it prevents even higher expenses for the assets.
One way that maintenance tech can reduce costs on mining projects is through improved maintenance scheduling. By coordinating maintenance tasks —ensuring they are performed as efficiently as possible —less time and money are wasted on downtime and repairs.
This can be especially helpful in large-scale mining operations where the cost of even a short stoppage can be sky-high.
Some important items for your technician include:
- Regular check-ups and inspections
- Preventive maintenance
- Emergency repairs.
By following a regular maintenance schedule, technicians can avoid many costly issues from neglecting their equipment —it will help to keep the project on budget and running smoothly.
4. Use of automation technology
When it comes to the mining industry, industrial maintenance automation ensures that machines, control systems, and software complete tasks without human intervention—therefore minimizing human error.
Automation can also help eliminate or reduce workers’ need to be present in potentially hazardous areas, which prevents accidents and injuries.
In addition, automation technologies improve productivity and efficiency —maintenance activities are completed quicker and with reduced downtime. This can ultimately lead to cost savings for the mining company and improve its bottom line.
5. Improved training for maintenance personnel
Because you’ve fully embraced the idea of maintenance tech and the various ways it can help reduce costs on mining projects, the next logical step is to ensure that your maintenance personnel is appropriately trained in how to use these technologies.
Investing in training for your maintenance technicians can help to improve their skills and knowledge, which can, in turn, lead to more effective and efficient use of the best maintenance practices. This can help further reduce mining project costs by ensuring that maintenance activities are carried out more effectively.
Conclusion
Maintenance is a critical function in any mining project —by properly maintaining equipment, a company can avoid costly downtime and repair bills.
Additionally, the role of the maintenance technician is to ensure that the equipment is operating correctly and safely.
These professionals can save the company money by implementing best practices, such as improved maintenance scheduling, automation technologies, and personnel training, and lead to significant cost savings for mining projects.
Author’s bio: Bryan Christiansen is the founder and CEO of Limble CMMS. Limble is a modern, easy-to-use mobile CMMS software that takes the stress and chaos out of maintenance by helping managers organize, automate, and streamline their maintenance operations.