Simulation and Optimization for the HVAC Industry
Computational turbomachinery design and the use of commercial computational fluid dynamic (CFD) codes to solve industrial engineering problems has come a long way since it was first introduced in the early 1990s. That’s when Ralph Peter Mueller started working as an independent CFD consultant in Germany.
“It was, indeed, the beginning of a new era,” says Mueller, who is now the president of CFturbo, Inc., a sophisticated technology company that offers an intelligent 3D-CAD system specifically for rotating machinery equipment. “In the early years, CFD was mainly limited to aerospace and defense applications, funded by governments, and run by scientists on colossal mainframe computers.”
However, over the years, CFD and the optimization of rotating parts has become an affordable, straight-forward process, and it’s no longer technology used only for large corporations or academia. Small to medium-sized companies and start-ups have been enabled to create the new designs of pumps, blowers, fans, compressors, and turbines very effectively and in a short period of time.
“Instead of the usual ‘trial and error’ engineering, we consequently focus on virtual methods, which we call ‘Digital Turbomachinery Modeling,’” Mueller explains. “It requires a modern, user-friendly, powerful, robust software toolchain to produce accurate simulation results before building physical prototypes and testing.”
The quicker path toward better products, higher efficiency, more reliable operation, and longevity of HVAC rotating equipment is already available. Taking technology another step forward, an intuitive software like CFturbo plays the vital role in the digital development process. Its interoperability with open-source and commercial codes for CFD/FEA/CAD is essential for the engineering process.
Moving forward, parametric turbomachinery component design will be the key factor for any automated product development process that includes simulation, design exploration, and optimization.
Evolution of Computational Fluid Dynamics (CFD)
Through the years, Mueller has witnessed a clear evolution of CFD technology first hand.
“From my first days in college, I have been fascinated by numerical methods, heat transfer, and fluid flow simulation, aerodynamics, and propulsion,” Mueller says.
He studied mechanical engineering with a special focus on Fluid Dynamics, Thermodynamics, and Turbomachinery followed by a successful professional career in Computational Fluid Dynamics (CFD). As an early adopter of the technology, he worked more than 15 years as a CFD consultant for various industries before co-founding CFturbo in 2008 in Dresden, Germany. In 2017 he became the President of CFturbo, Inc. in Brooklyn, NY.
“From the early days of turbomachinery development it has been solely an expert business,” Mueller explains. “It is a complex task. Very often it was complicated, time-consuming and a lot of resources were required for simulation and testing. Today we want to empower any engineer or scientist for automated design exploration, simulation, and optimization to create better turbomachinery equipment.”
In the early 1990s the age of desktop RISC workstation had begun. CFD became affordable to a broader group of scientists and engineers. Manufacturers like DEC, Silicon Graphics, SUN, and others used Linux as their operating systems.
For example, Silicon Graphics Workstations (SGI) became very popular first and later legendary.
“I was proud and excited when I purchased my first SGI workstation in 1993,” Mueller remembers. “The machine had 64 MB RAM, and was more than $30,000. That sounds crazy today! My current notebook has 64 GB RAM and cost me about $3,000. And, besides the new hardware, there was the first generation of commercial CFD codes available on the market. Brand names like CFX (AEA, now Ansys), FINE/Turbo (NUMECA, now cadence), StarCD (CD adapco, now SIEMENS), and TASCflow (ASC, now Ansys) among others.”
Mueller remembers that the codes were expensive and not at all user-friendly—they required significant expertise to work with them.
“Even for grid generation and modeling, you had to be an expert,” he says. “And we were always lucky when a CFD run had converged after many hours or days of simulation. Depending on the resources, typical mesh sizes were around 100k to 1m nodes, which often limited the representation of full geometric complexity in all details.”
Especially with the automotive industry, CFD was pushed to the limits in the early years, driven by continuous product development, the need for innovation, and usually complex geometries. External Aerodynamics, Underhood Thermal Management, Cooling, HVAC modules, passenger compartment comfort, and engine development with turbochargers, gas exchange, and injection systems were critical CFD applications.
Alternatively, the oil and gas industry and the power-generation equipment manufacturers were the second industry catalyzing CFD in the ‘90s. Turbomachinery design and simulation were already a part of CFD from the beginning.
According to Mueller, some of the most significant improvements during the last 30 years in CFD technology include:
- Most CFD codes became available on Windows, which made it popular with a new group of users.
- CFD codes, meshing tools, and post-processing software became more and more user-friendly, as some of them were integrated into 3D-CAD systems.
- A dramatic increase in computational power for everyone went along with a significant drop in hardware cost.
- More geometrical details were incorporated into computational models.
- Substantial progress was made in grid generation, which has allowed highly complex geometries/meshes.
- Transient flow simulations and better turbulence models provided more reliable predictions, also in absolute values not only showing tendencies like in the past.
- In recent years, seamless workflows combing design, simulation, and optimization were established, which is the critical part of automated design exploration
- HPC Cloud computing seems to be a promising possibility to come to bring CFD to the next level.
Each Turbomachinery application is designed for a specific task in a certain operating range, but there is only one particular operating point of best efficiency.
“For pure hydraulic or aerodynamic tasks, modern Turbomachinery design and simulations systems can achieve single-point performance target at excellent overall efficiency pretty easily,” Mueller says. “However, if there are conflicting performance targets because of a wide operating range, or if there are constraints determined by structural integrity or manufacturing methods, multi-objective optimization would be the right choice. Only with seamless, robust, and accurate software tools can development goals be reached in a relatively short period of time. It is mainly a matter of development time and cost.”
To establish an automated workflow for Turbomachinery design exploration the following is needed:
- A versatile, parametric free-form modeler for 3D CAD
- Reasonable initial conceptual designs based on fundamental physics and empirical correlations
- Excellent data export functionality to all major CAD, CFD and FEA software tools
- Interoperability to set-up automated simulation workflows and digital twins
In future the key factors for CAE/CFD based “Digital Turbomachinery” will include:
- Fully automated, robust design and optimization workflows, combining different CAD/CFD/FEA codes, based on users preferences, even combining software from competitive vendors
- Digital Twins of Turbomachinery assemblies in development, production, and operation
- Data mining, data management, and AI algorithms to create, produce and operate Turbomachinery – more reliable, more efficient, more cost effective
How End Users Benefit from CFD Technology
In general, it is the primary motivation to use CFD for a wide range of applications to manufacture and to operate energy-efficient equipment and systems. The latest legislation in the US and EU drives development activities in that direction. No other technology like CFD helps to improve products and systems and helps shorten development time and operational costs, according to Mueller.
For all kinds of end-users, their utility bill will be lower thanks to the sophisticated simulation technology.
Additionally, there has been a massive impact from the aerospace industry to CFD applications in the last decade. Private companies, along with government agencies, have recently entered into the “New Race to Space.”
“This change is a significant technology driver for the whole CFD community,” Mueller explains. “It is about aerodynamics, propulsion, rocket turbopump design, and many more subjects which propel CFD applications, including automated design optimization and HPC in the cloud.”
Even though the HVAC industry was not one of the early adopters of CFD, much has been improved throughout the last 15 years. There are several functional areas that use CFD within the HVAC industry in a broader range. Besides simulation of ventilation systems and predictions of airflow room comfort, there are at least three significant examples from Turbomachinery for HVAC systems:
- Chiller (refrigerant) compressors
- Axial and centrifugal fans for ventilation
- Circulator pumps for efficient heating of buildings
“All three types of Turbomachinery equipment play a critical role in HVAC systems for commercial and residential buildings,” Mueller says. “Besides the energy efficiency of the Turbomachinery itself, there is a need to know what happens and various operating conditions. In many applications, the rotating machinery equipment is running off-design, which means the machines are not running in a defined duty point, which is supposed to be the best efficiency point.”
Turbomachinery simulation can now accurately predict whole performance maps of compressors, blowers, fans, and pumps if the user does it correctly. This means applying geometrical details, generating appropriate computational grids, and choosing the correct solver settings. There is still a need for some expertise in CFD, Mueller emphasizes.
The Future of CFD for the HVAC Industry
Companies like CFturbo are paving the road for fully automated Turbomachinery design, simulation, and optimization.
“It combines our software with various meshing tools and CFD simulation codes to streamline the whole process of Turbomachinery design exploration of pumps, blowers, fans, and compressors,” Mueller says. “Our mission is to provide the software tools enabling ordinary mechanical and aerospace engineers to create excellent Turbomachinery components. Such new developments or re-design of rotating machinery can be made on powerful notebooks, desktop workstations, clusters, or in the cloud.”
The combination of 3D-CFD simulations and 1D-systems simulation seems to be a promising approach. It is essential to consider both the Turbomachinery equipment as well as the system.
“I also see good possibilities in building Digital Twins for our customers, monitoring operations 24/7, predicting unusual conditions, and preventing failure,” Mueller explains. “HPC computing would be essential for such a task.”
In general, CFD will become more and more utilized in all relevant areas of HVAC, not only Turbomachinery design and optimization, but also for ventilation, thermal comfort and building simulation.
Case Study Example 1
Refrigerant R134a Centrifugal Compressor: Aerodynamic design, CFD simulation, and optimization
As a major trend in the HVAC industry, more and more turbocompressors are used in refrigerant cycles, replacing other types of compressors, like piston or scroll-type machines. There is a need for high-performance high-efficiency components and systems. By its working principle, turbocompressors can achieve better efficiency and performance over a wide operating range.
By combining CFturbo with Ansys Workbench, the design and development process have been streamlined. Now, it is possible to create a new, optimized high-efficiency refrigerant compressor design within a few days, instead of weeks or months, like in the past.
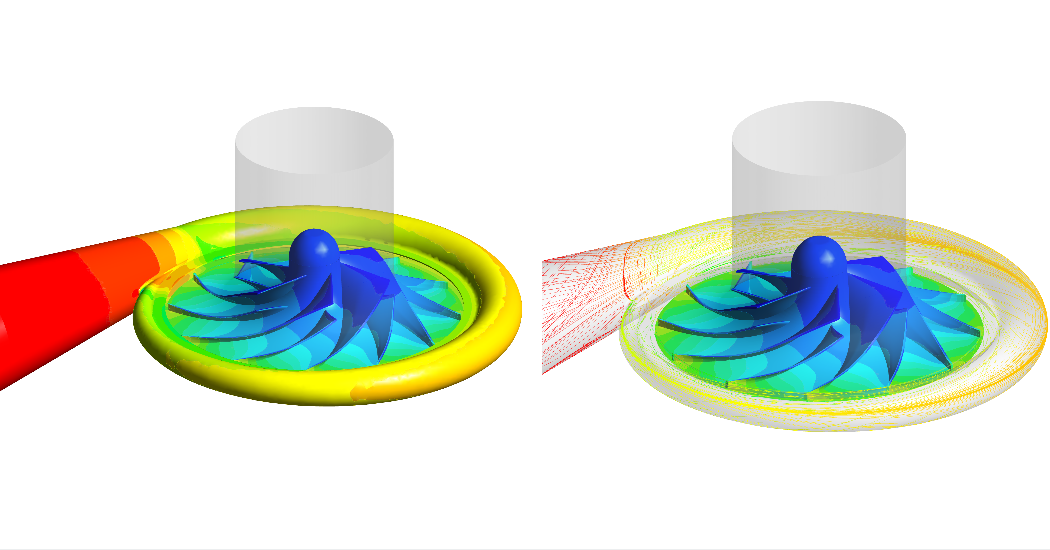
Images Case Study Example 1.
Case Study Example 2
Submersible, Vertical Multistage Pump: Hydraulic design, CFD-simulations, design exploration (DoE), and optimization.
Designing highly efficient pumps is crucial. However, for multistage vertical turbine pumps, which are key components in the freshwater supply infrastructure, the first pump stage’s suction capability is also an essential attribute.
To resolve a problem with conflicting targets, a multi-objective design exploration must be done. CFturbo, integrated in Ansys Workbench, can provide such a solution. It is a user-friendly, streamlined, robust design and simulation process with excellent accuracy to predict performance, efficiency, shaft power, and NPSHR.
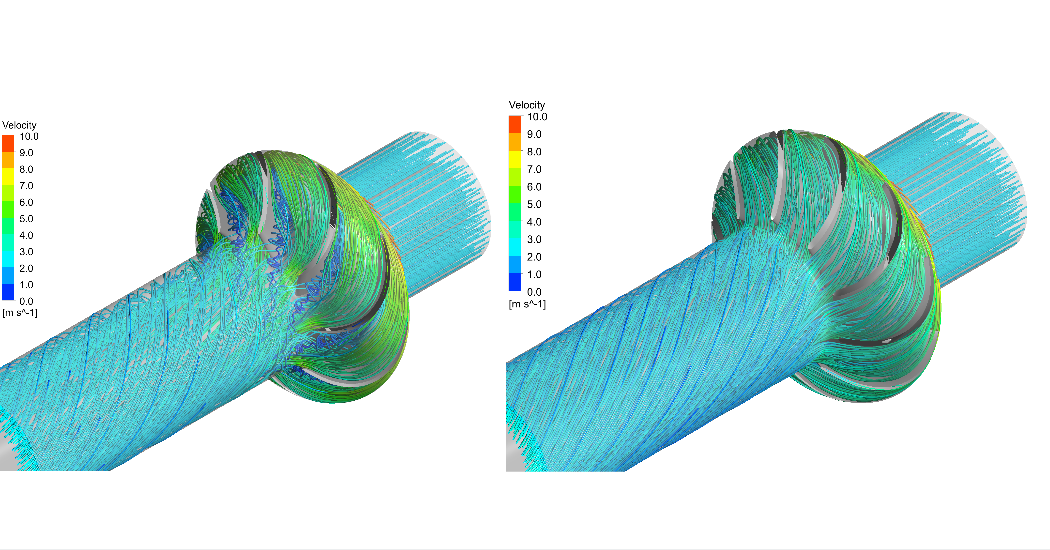
Images Case Study Example 2.
Case Study Example 3
Contra-rotating Axial Fan: Design, Simulation, Testing, Development – ILK, Semi-Therm papers 2018, FAN 2018
Contra-rotating fans are rarely used in HVAC or other industries because of their complex drivetrains. Usually, an expensive gearbox is needed, making it difficult from a commercial perspective. However, there is vast progress in electric powertrains, so that one could use two electrical motors rotating in opposite directions. The critical advantage of the contra-rotating fans can come into play: compact, variable speed, high pressure, high-efficient, low noise.
CFturbo provides the design and simulation platform for this innovative contra-rotating design concept. For specific applications, contra-rot fans can replace traditional centrifugal fans or multistage axial fans with vaned stators.
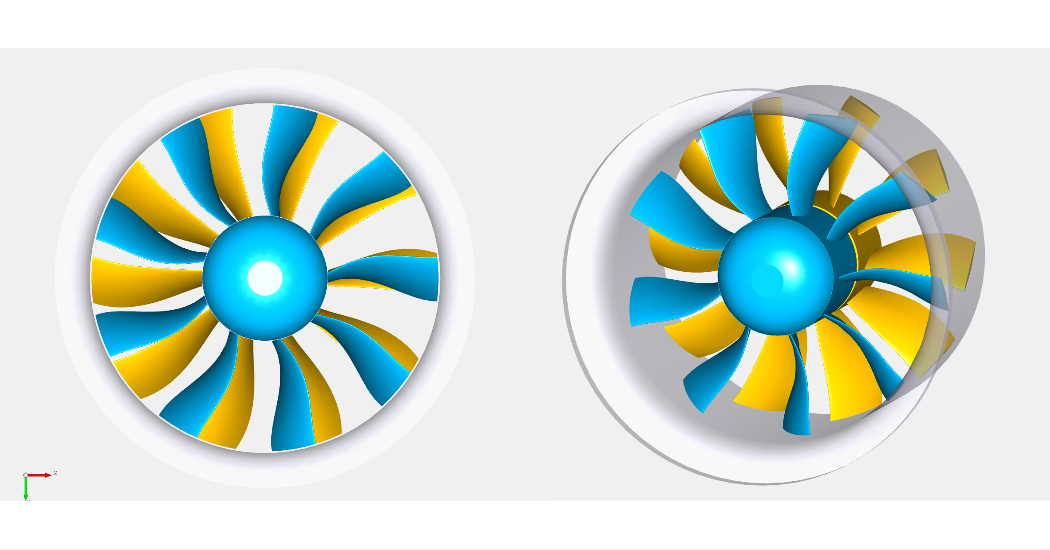
Images Case Study Example 3.
To learn more about the CFturbo software and service, visit them at AHR 2022 booth #9312 or register for a free trial at www.cfturbo.com
About the Authors:
Michelle Segrest is president of Navigate Content, Inc., a full-service content creation firm and has covered the industrial processing industries since 2008. Find her podcast, “Factory of the Future” wherever you listen to podcasts
About Ralph-Peter Müller born and raised in Germany.
– Technical University of Dresden; Studies of Fluid
Mechanics, Thermodynamics and Turbomachinery
– M.S. in Mechanical Engineering
– Development Engineer at General Motors, Russelsheim, Germany
– CFD Consultant, Founder and Director of CFDnetwork, Munich,
Germany
– Co-Founder and Managing Director of CFturbo GmbH, Dresden,
Germany
– Co-Founder and President of CFturbo, Inc. Brooklyn, NY
Comments