Discover the transformative potential of refurbishing and safeguarding worn pumps using specially the right high-performance coatings. These coatings have the remarkable ability to not only restore lost pump efficiency but also surpass the levels depicted on the manufacturer’s pump performance curve. Delve into the advantages of applying coatings to the internals of new pumps or opting for pre-coated pumps—a growing trend that ensures enhanced reliability right from the outset.
Performance & Protection
The performance of a standard centrifugal cold water pump naturally declines over time – often losing as much as 10-15% of its original efficiency, according to an EU SAVE Report. The same report revealed that many pumps lose 10% after only one year of service!
When you introduce solids and increased temperatures or speed into a pumping system, pump performance can deteriorate even more quickly. As the fluid moves through the pump’s wet end increased friction and wear can be the biggest factor in efficiency loss. In the field, Chesterton staff members have seen as much as 40-50% decline in expected efficiency performance.
Sizable Savings
When you recognize that operational costs (energy) and maintenance (service) account for >70% of the pump’s total life cycle cost, you can truly appreciate how protecting the pump asset from wet end corrosion, scale build-up, and tolerance losses can generate a sizable payback.
Beyond improved energy savings and performance, the restoration/coating of older equipment can give you the advantage of repairing worn equipment at a fraction of the cost of spare parts replacement or whole replacement. It also avoids lengthy delays due to lead times from pump manufacturers.
Monroe Country Study Results
In 2005, the Monroe County Water Authority (MCWA) in Rochester, NY, began a pilot study to test the impact of removing the corrosion and tuberculation from three horizontal split case pumps and then applying protective coating to the restored surfaces.** Prior to this, the pumps had been mechanically rebuilt (new wear rings, bearings, impeller re-balancing), but the head, flow, and efficiency had not returned to the manufacturer’s specifications. The results of the study surprised even the most skeptical staff members: Pump efficiency increased by 8+ percent. Overall performance returned to below the original manufacturer’s specifications.
Following this study, MCWA received a state grant to conduct research on the use of ceramic epoxy coatings’ impact on enhancing and retaining critical pump performance characteristics. The study, which was conducted in independent steps, showed:
- Mechanical restoration only restored about 50% of a pump’s performance improvement (compared to the manufacturer’s performance curve).
- The combination of sandblasting and the application of protective coatings were a major factor in bringing the pump back to expected performance levels.
- Sandblasting alone contributed on average a 4.6% boost efficiency. However, after several months this declined.
- Pumps that were both sandblasted and coated effectively matched the gains provided by mechanical restoration and retained performance for a longer period of time compared to pumps that were simply mechanically restored and sandblasted. Over time these refurbished pumps lost less than 1% efficiency, even after several years of service.
How Does Restoration/ Coating Improve Pump Performance?
Restoration and Sandblasting
Restoration is mechanical in nature. Replacing worn wear rings, bearings, and balancing impellers provides significant gains in performance and efficiency. However, no modifications have dealt with scale and corrosion in the wet end of the pump.
Sandblasting removes tuberculated rust and scale from the pumps hydraulic passages — opening up passages and reducing pipe friction losses. It is possible to gain significant improvements (as much as 8-10%) by taking these simple steps.
After wear ring re-circulation is addressed by wear ring replacement and bearing replacement reduces frictional drag on the shaft, the next largest opportunity (and one which can reap rewards for years afterwards) is reducing the friction on the wet end by applying a ceramic reinforced epoxy. Field experience has resulted in gains equal to and, in some cases, exceeding the gains brought about by only mechanical refurbishment.
Application of Protective Coatings
Coatings increase reliability by reducing the impact of corrosion and wear resistance:
- The polymer-based coating provides both corrosion protection and reduction of surface roughness of the otherwise uncoated, wet-end base metal.
- If choosing a ceramic reinforcement system, utilized in coatings, enhances the overall wear resistance of the wet-end components by maintaining tolerances longer and reducing the “wear eddies.”
These coatings typically come in paste rebuilding and liquid resurfacing grades, allowing worn pumps or new pumps with significant casting defects to be resurfaced and coated.By effectively blocking the corrosion/erosion cycle, coatings can preserve and protect wet end corrosion from taking hold (see Figure 1).
Coatings improve the use of energy by reducing frictional losses associated with scale and tuberculation:
- The applied polymer coating will significantly reduce surface roughness which directly impacts the amount of energy transferred to the fluid by the impeller.
- The “Surface Energy of Coating” is significantly less than that of the base metal, in essence making the surface hydrophobic (water repelling) and reducing wetting factors throughout the hydraulic passages of the pump and impeller.
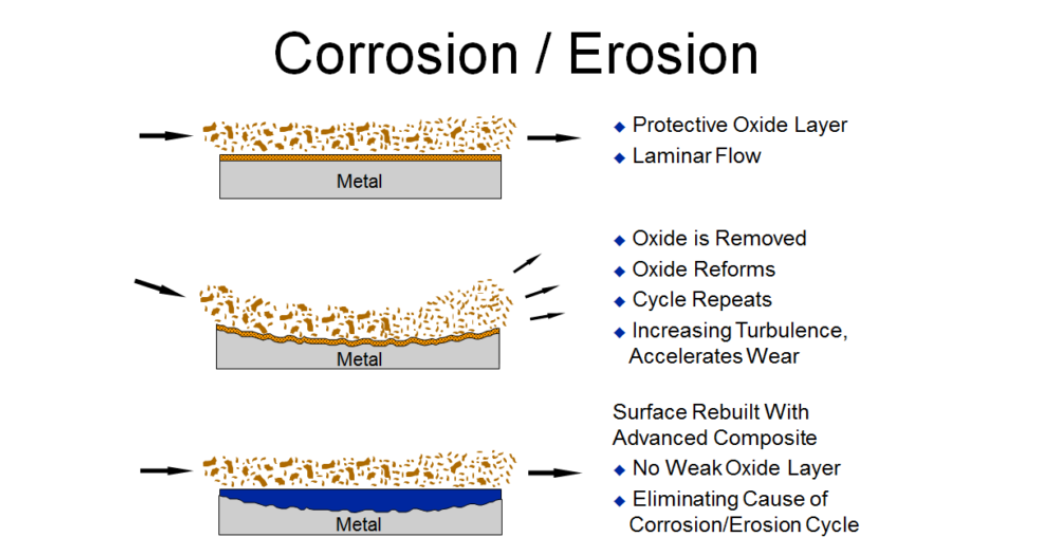
Figure 1: Impact of Corrosion/Erosion vs. Protective Coatings
Choosing the Optimal Coating
In selecting a coating, the following factors come into play:
- Does the coating have the right performance properties to resist the “wet end” pump conditions while it is operating? Several key factors to consider are:
- Fluid media and temperature
- Suspended solids concentration and particle size range
- Temperature and pressure/vacuum within pump system
- Do tolerances exist that allow application of coating to wet end parts without impacting critical tolerances?
- What is the potential for, and impact of, a coating that disintegrates and contaminates the process flow?
“While failure of seals or bearings may be immediately apparent, the deterioration in pump hydraulics is unlikely to be obvious. This can have many sources: chemical erosion, physical abrasion, deposition. The use of glass or resin coatings can help to increase and maintain a good hydraulic efficiency over a long period of time, and for larger pumps many users specify these coatings as standard.”
European Union SAVE Report (2001)
Pre-Coating of New Pumps
One of the more common methods of pump part manufacturing is sand casting. Sand casting results in a rough surface finish (350-750 RMS) which induce frictional losses and can accelerate erosion eddies. In addition, some pumps are designated for potable water service, and many of these will require a NSF-certified coating. In both of these cases, coatings can be used to enhance performance and provide extended reliability where rough sand cast finishes are present and provide potable water compliant contact surfaces for the life of the pump.
Are you considering refurbishing your pumps? AW Chesterton’s experienced team is on call to help. Contact them for a Plant Visit or email their Ask the Expert desk.
For more information:
Pump Efficiency Case Studies
Webinar: Identifying and Addressing Equipment Decay in Hydropower
Sources:
*** Monroe County Source: Opflow – October 2015 “Save Energy by Refurbishing and Coating Pumps”
About the Author
Steve Bowditch is the Global Market Development Manager for ARC Efficiency and Protective Coatings. He is a NACE Level III CIP Inspector and SSPC Corrosion Specialist with over 35 years’ experience in the areas of protective coatings development and applications. When he is not immersed in the exciting world of protective coatings, he is hopefully sailing on a Hinckley Bermuda 40’ somewhere near a tropical island chain.