In a slurry pump, seals, which are commonly either packing or mechanical seals, are frequently replaced components. Packing can be easily worn down or mechanical seal components can be clogged by abrasive particles. In both situations, the lifespan of the seal in a slurry environment can be significantly reduced to just a few days or weeks. In operations where downtime can cost tens of thousands of dollars an hour, you can reap significant rewards by choosing not only the best sealing solution but also one that is easy and quick to replace.
In this post, AW Chesterton will focus on some of the best practices to speed up packing and seal replacement as much as possible when it is necessary.
Packing: Avoiding Lantern Ring Woes
When replacing packing, one of the biggest hassles is removing the lantern ring. Lantern rings can get off-axis and bind up in the stuffing box. Sometimes they get clogged and filled with particulate—making removal difficult and time consuming. Due to these difficulties, it is unfortunately a common practice to leave the lantern ring in place and only repack the rings above.
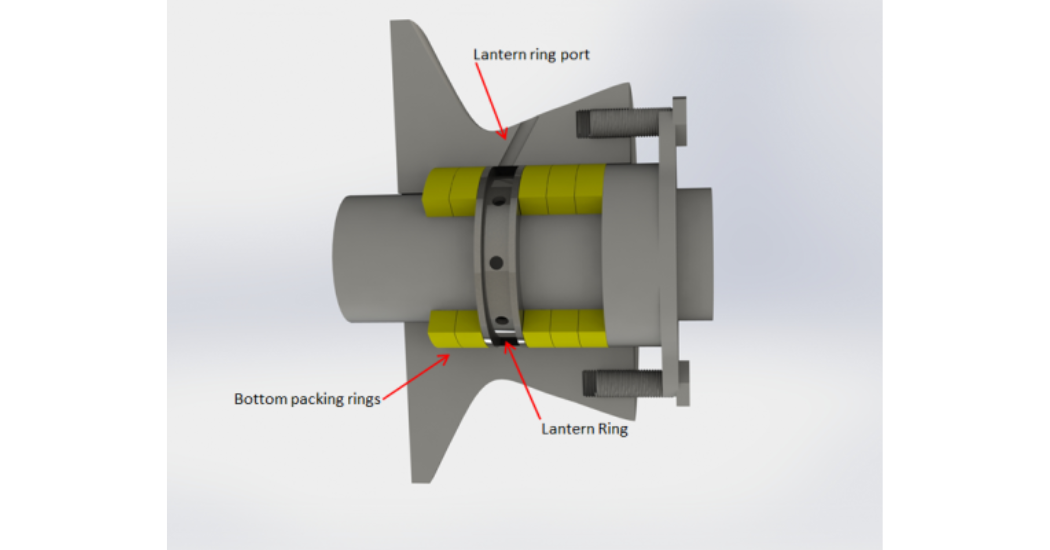
Figure 1
Here’s why Chesterton doesn’t recommend that approach:
- After a time, the bottom rings that aren’t being replaced will erode, extrude, and condense. As a result, the lantern ring will move towards the bottom of the stuffing box and no longer align with the lantern ring port.
- This alteration will keep flush from getting to the ID of the packing where it can flow down the shaft and into the pump casing, allowing solids to penetrate under the packing, and dramatically shortening life.
- A symptom of a misaligned lantern ring is heavy flush water leakage on the OD of the packing. If this occurs, it’s likely that either the lantern ring is misaligned, or it has become clogged with particulate. If it is clogged, the most likely cause is intermittent or inadequate flush pressure, or a dirty flush.
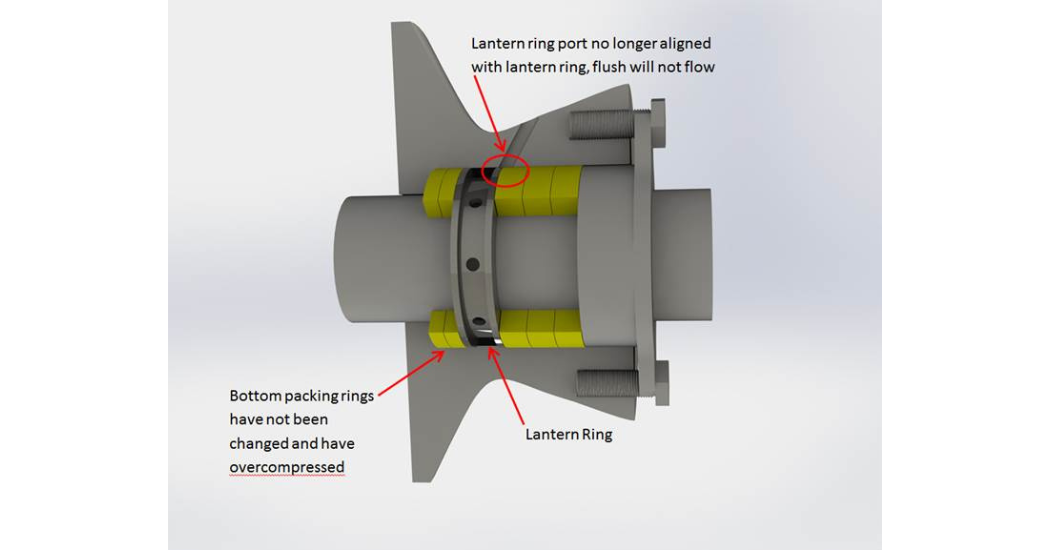
Figure 2
So what to do about difficult lantern ring removal? It’s simple – don’t use a lantern ring.
- Our tests have shown than the first three rings of packing do the majority of the sealing, and the bottom rings mostly serve to help keep solids out.
- Using a throat bushing with built-in flush ports, you can eliminate the need to remove the lantern ring when you repack, and you’ll use less packing.
- Because the top rings do most of the sealing, you won’t be sacrificing sealing capability.
- To make the system even more reliable, specifically engineered bushings are available that alter the flow of water within the stuffing box to actively remove and exclude solids (see SpiralTrac – Type P).
Pre-Cut Packing Rings
Another way to make re-packing of a slurry pump easier and less time consuming is to purchase pre-cut rings. Most packing manufacturers now offer rings pre-cut for a small fee, which is easily recouped through eliminating the time and scrap required when cutting them yourself. You’ll know that the rings are the correct size, and the cuts were made accurately and with a sharp blade.
Mechanical Seals in a Slurry Environment: Selection & Environment
The biggest hassle with modern cartridge mechanical seals is installation. The single-piece cartridge seal is significantly easier to install than component seals, but this design still has its drawbacks. Installing a cartridge seal requires decoupling the power end and often moving pump/motor components. And since slurry pumps are often very large, this can become extremely time-consuming. The answer is to use the next step up in mechanical seal technology: advanced split seal design, such as that used in the Chesterton 442C Split Seal.
Over the past decade split seals have evolved to have fewer components, making installation a matter of minutes rather than hours. This seal design can also now achieve seal life equivalent to a non-split seal. Newer features also include fully split O-Rings and easy field-repair capabilities.
Controlling the Seal Environment
The only disadvantage in a slurry pump environment is that split seals do not typically have the features of a heavy-duty cartridge slurry seal, so setting up the appropriate environmental controls is paramount:
- A clean flush must be available
- A bushing is often recommended to limit the amount of particulate than can get into the seal chamber. As with packing, there are engineered bushings designed to remove particulate from the seal chamber and help the seal operate in a clean fluid to improve seal life (Chesterton carries several varieties of these: the SpiralTrac Environmental Controller).
When flush isn’t an option, heavy-duty slurry seals have features such as non-clogging external springs, larger clearances to reduce clogging, and high-strength drives. These can often operate flushless under certain conditions, which can be improved with other environmental controls.
Other Methods of Improving Reliability and Reducing Maintenance
Although sealing considerations have been the main focus, there are various other methods to safeguard assets and simplify maintenance:
- Reinforced coatings can extend the life of pump internals and reduce equipment costs
- Proper and automated lubrication extends bearing life along with adequate bearing seals
- High quality bolt and nut lubrication makes disassembly much easier.
Ron Frisard is Field Product Manager of Packing & Gaskets for A.W. Chesterton Company. He has worked for Chesterton for 27 years in all facets of valve and pump packing. Ron has presented at many conferences including the Electric Power Research Institute (EPRI), the American Society of Mechanical Engineers (ASME), and Valve World in Europe and America. Ron is also currently the Vice Chair for both the Packing and Gasketing divisions of the Fluid Sealing Association (FSA).