Challenge
A large steel cold rolling mill experienced premature seal failure and intensive leakage of the back-up roll chocks of a reversible cold rolling stand. The leakage required unscheduled downtime to replace seals and raised environmental concerns due to leakage.
Root Cause
The original manufacturer’s rotary seals had a short lifetime because of high peripheral speed, leading to the hardening and cracking of the seal lips. This condition resulted in high maintenance costs, lost bearing lubrication oil, and reduced production.
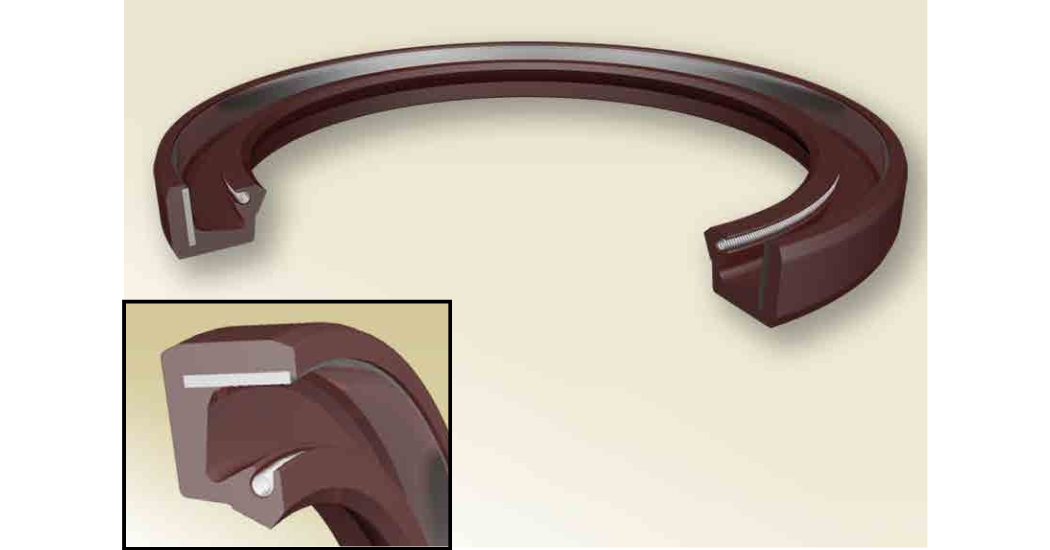
Chesterton 52K Mill Rotary Seal
Solution
Chesterton’s local specialist recommended an advanced, heavy-duty rotary seal solution.
Products
Design
The unique design includes a flexible stiffener ring that ensures improved fitting in the seal cavity and allows for installation in stuffing boxes without end covers. A helical garter spring maintains the seal lip contact and sealing force on the shaft. A direct retrofit, this seal solution eliminates equipment modification.
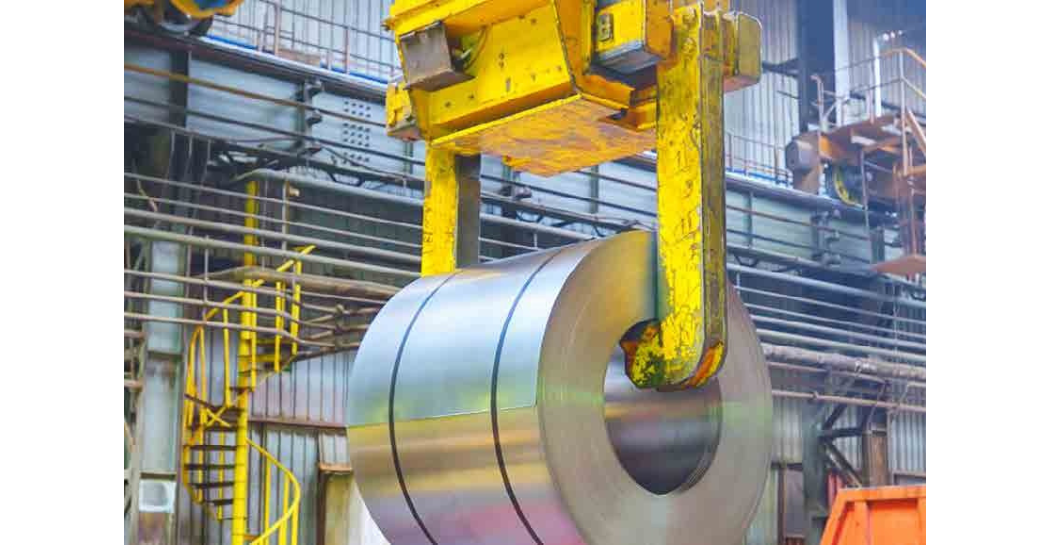
Sheet cold rolled steel coil
Results
Improved Performance and Reliability Chesterton seals far exceeded the customer’s expectation during the evaluation period. The sealing solution was specified as the standard offering for all future rebuilds of the rolling chocks.
Benefits
- MTBR increased by 2x
- Reduced lubrication oil leakage/loss
- Direct retrofit, which eliminates the need for equipment modification