Challenge
A sustainable packaging operation was looking for a more efficient and reliable system to control the temperature of coolant in a tank used to manufacture aluminium cans. During the manufacturing process, oil is passed out of the tank to be heated or cooled, and then is transferred back into the tank. The existing system had to be modified because the electric heaters being used could not provide sufficient heat (115° F) and a chilling component needed to be added to the system.
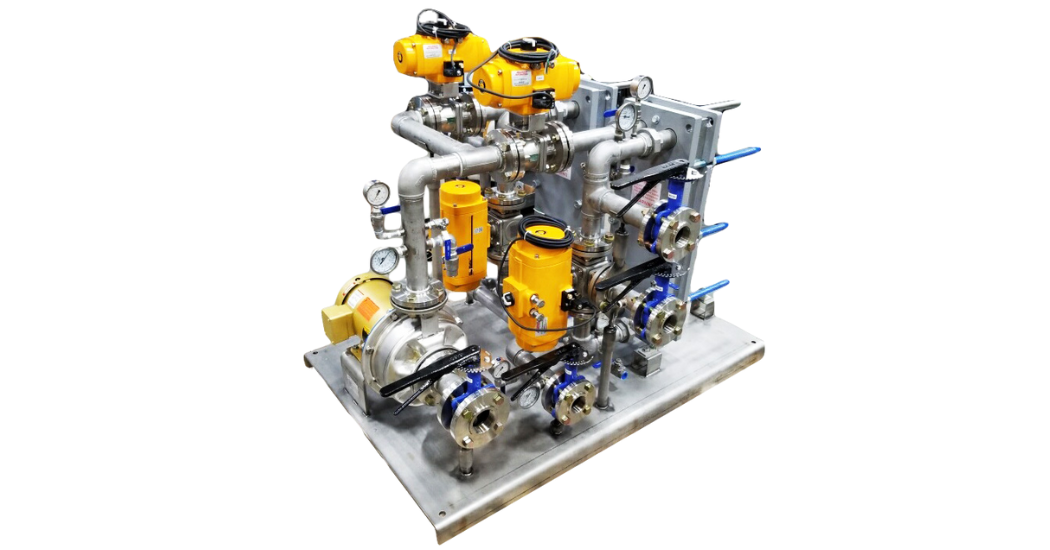
The system, designed by Anderson Process and featuring Xylem technology, efficiently heats up 6,000 gallons of oil within the required 30-60 minutes and holds the desired temperature.
Solution
Xylem’s channel partner Anderson Process was tasked with designing a custom system that could efficiently and reliably heat and cool the oil to the desired temperatures. Space was limited, so it was important that the skid be compact enough to fit neatly into the available area. The team custom engineered a skid incorporating an assortment of fluid handling components, including a Goulds Water Technology e-SH pump and two Standard Xchange heat exchangers – one for heating and the other for cooling.
“The most suitable heat exchanger is system that can fit within a compact space. expertly matched to the specific needs of a project, to maximize productivity and reliability.”
Standard Xchange’s broad portfolio of products includes gasketed plate, brazed plate, pre-engineered shell and tube, air-cooled, and custom shell and tube heat exchangers. They’re custom engineered according to project requirements. This means the most suitable heat exchanger – our P14 Gasketed Plate & Frame heat exchanger – is expertly matched to the specific needs of a project, to maximize productivity and reliability.
In the upgraded system, the pump successfully transfers the oil from the tank through the relevant gasketed plate & frame heat exchanger, and then pumps it back into the tank. Operating conditions required the pump to move coolant with 1.5% concentration of additional oils, along with aluminum particle fines approximately five microns in size.
“It’s also possible to enhance the system’s automation features, thanks to the built-in pressure and temperature transducer ports.”
Two-way and three-way air actuated ball valves direct the flow of the oil, cooling water and heating water though the system. Manual butterfly valves and a valve for the pressure and temperature gauges provide ease of maintenance. This means that the skid and specific components can be isolated and taken offline for any necessary servicing or repairs. The skid also includes ports for pressure and temperature transducers, to add automation and control, making the system convenient, user friendly and effectively plug-and-play.
Results
The result is an efficient, reliable system that can be easily maintained. The system efficiently heats up 6,000 gallons of oil within the required 30-60 minutes and holds the desired temperature. Minimizing temperature swings reduces wear and tear on system components. It’s also possible to enhance the system’s automation features, thanks to the built-in pressure and temperature transducer ports.
Learn more about the Xylem Standard Xchange Heat Exchangers