Author: Robert A. Leishear, PhD, P.E.
Ground breaking research hammers out new methods to stop hundreds of thousands of piping failures per year that have been misdiagnosed and misunderstood for more than a century.
This research centers on two original theories. The first theory was the “dynamic stress theory” that was published in a 15 year series of publications, which culminated in an ASME press book titled, “Fluid Mechanics, Water Hammer, Dynamic Stresses, and Piing Design”, by R. A. Leishear (American Society of Mechanical Engineers). This book proved that the pipe stresses that cause pipes to break had been improperly calculated by engineers for centuries. The basic equation that they were using needed to be multiplied by four to obtain the actual stress to cause failures in pipes. This multiplier is known as a dynamic load factor (DLF), where the resultant dynamic pipe stresses may be referred to as “Leishear Stresses”. Engineers may simply calculate the static pipe stress that would occur by pressurizing pipes, and multiply that static stress by four to obtain the maximum dynamic stress. This theory has been recently applied to show that water main failures are caused by water hammer.
Briefly consider an example of the dynamic stress theory that was investigated at the Savannah River Site, which operates a nuclear waste storage plant in South Carolina, along with other facilities. At that plant, a cooling system prevents the boiling of radioactive liquid waste that is stored in nearly 50 storage tanks with tank volumes near a million gallons each. Rows of vertical serpentine cooling coils were installed in most of these tanks, where the coils were two inches in diameter and several hundred feet long. More than 200 of those coils were removed from service when they leaked, where corrosion was assumed to be the cause of coil failures in those tanks since 1970. However, radiation resistant cameras were used for the first time in the 1990’s to observe the coils, where cracks and not corrosion were the causes of pipe leaks.
Also in the 1990’s, underground pipes in that cooling system began to crack and leak, where there was no corrosion at the pipe cracks. The cause of the cracks was unknown, where ASME Piping Standards used static stress calculations, which of course showed that the pipes could not crack since the equations were, and still are, incorrect. Extensive research was performed to invent the dynamic stress theory, where advanced calculus (fourth order differential equations) was used to derive new equations, and these equations were shown to be correct through experimental validation.
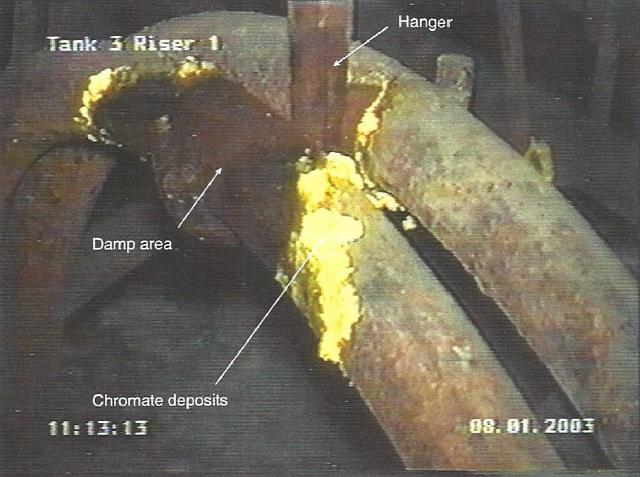
Typical Savannah River Site Cooling Coil Failure – Note that hundreds of piping failures in multiple tanks stopped when water hammer was stopped.
In short, water hammer occurs when valves and pumps are operated, where pressure waves are transmitted along the bores of pipes at near sonic velocities. These pressure waves pressurize the piping and DLF’s can be used to determine the dynamic pipe stresses that cause fatigue cracks. Fatigue cracks occur when pipes are subjected to water hammers again and again. Having identified the source of piping cracks, corrective actions were implemented, and pipe failures stopped fifteen years ago, where 40 years of failures were abruptly brought to a halt. The causes of pipe cracks were identified and stopped by using this one-man theory!
The second original theory from this research is the finding that nearly 250,000 pipe failures per year in the U.S. and Canada are caused by water hammer, where this opinion is proven by new research that is in publication (Water Main Breaks, Water Hammer, Corrosion, and Fatigue Failures, R. A. Leishear). That research approximated piping failure stresses due to fire hydrant operations, which were performed annually. Although there are many other sources of water hammer in water mains (e.g. any pump and valve operations), this investigation showed that water hammer cracks piping in many systems.
Additionally, a 2011 study was performed by the University of Utah to determine the cause of piping failures. Seventy percent of water main failures were from cracks, and 28 percent of water main failures were attributed to corrosion. According to the work presented here, water hammer causes cracks in the absence of corrosion, and cracks due water hammer also initiate most, if not all, corrosion failures, where water hammer cracks the pipes and provides a moisture source to accelerate underground corrosion, and corrosion increases the size of leaks. Leaks percolate to the ground from both cracks and corrosion accelerated cracks, where soil can then be carved out to cause large leaks to the ground. Additionally, all underground pipes are cracked by water hammer regardless of material, e.g., PVC, and HDPE plastics, steel, ductile iron, cast iron, and concrete. In other words, water hammer causes 98% of the water main failures in America, and thousands, perhaps hundreds of thousands, of other piping failures occur in other industries and countries around the world!
If you have any questions, please post in our Industry Forum!