Author: Heinz P. Bloch, P.E.
Pump bearing selection is always a compromise. Again, each improvement in one of the 5 performance characteristics depicted in Figure 1 will be at the expense of another. If it’s not shown as a physical characteristic, it must be another universal yardstick: money. Improvements in all five characteristics will cost money, possibly because exotic materials will be involved. The API-610 clause on using flush-ground angular contact bearings oriented back-to-back as your thrust bearing is one such compromise. The main reason for the clause is simplicity and low cost, certainly not superior performance (Ref. 1).
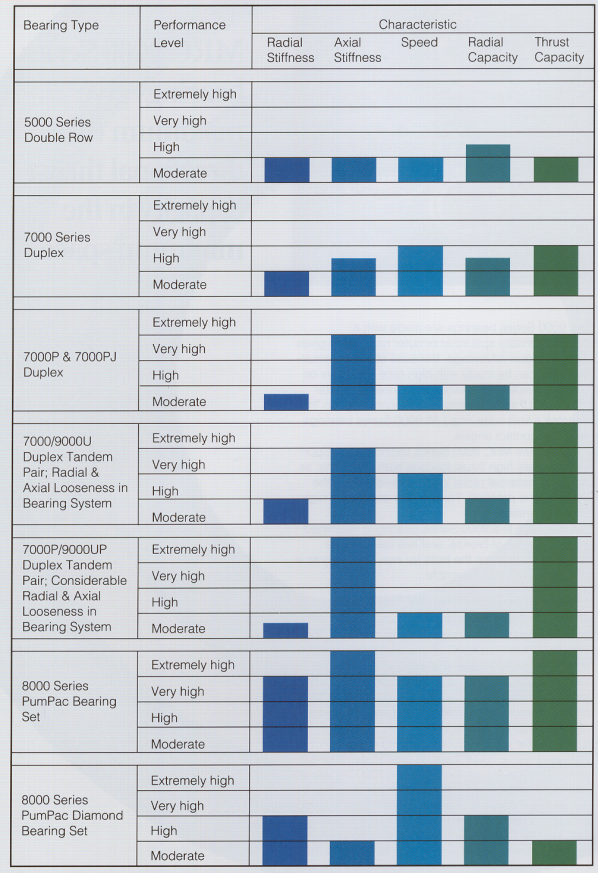
Fig. 1: Some of the many styles and sizes of rolling element bearings found in process pumps (Source: MRC Division of SKF USA, Jamestown, NY)
Preloads
For superior performance we may have to use preloaded bearings, or bearing pairs where each of the two bearings has contact angles that differ from each other. This is shown in Figure 2. Our advice is to work with only those bearing manufacturers that explain these facts to you. A superior manufacturer will work with you and recommend bearing sets that solve problems, not bearing sets that increase the manufacturer’s sales figures and profit margins.
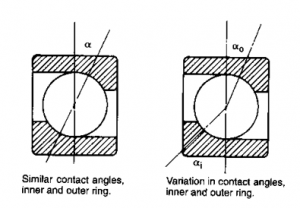
Figure 2: Competent bearing manufacturers can design contact angles so as to ascertain
favorable rolling motion and minimize skidding (Source: SKF USA, Kulpsville, PA).
Granted, bearing sets selected per API-610 work most of the time, but they do tend to skid (Figure 3) if the axial load causes one bearing to carry more than 50 or 55% of the total load. In that case, bearings designed per Figure 2 will serve you better because they avoid skidding (Ref. 2). Skidding generates heat. We see the result of skidding as streaks of rubber on an airport landing strip or on a drag strip for hot rod vehicles. Skidding means wear and wear means premature failure.
It stands to reason that misapplications and misunderstandings relating to bearing technology can lead to costly repeat failures. Paying attention to detail is needed for lowest cost of ownership over the long haul. Accordingly, being detail-oriented is perhaps the most important attribute of Best-of-Class performers.
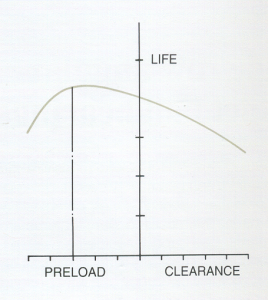
Figure 4: Rated life is greatest with a certain amount of preload. Neither excessive preload nor excessive clearance is good for the bearing (Ref. 3)
Rolling element bearings are precision components that must be treated with great care. Thoughtful selection and picking the right bearing for the application will allow rolling element bearings to run flawlessly for six or more years in centrifugal process pumps. Careless installation is certain to wreck bearings. Visualize from Figure 4 that rated life is greatest with a certain amount of preload. Neither excessive preload nor excessive clearance is good for the bearing. Thrust bearings configurations that comply with API-610 have no preload and thus usually have internal clearances near zero. Therefore, their life expectancies are probably close to what SKF is here (in Figure 4) representing by the vertical, i.e. away from the otherwise reachable maximum life.
Bearing selection overview and windage as a design problem
The location of a bearing’s cage relative to other bearing components is seen on the five bearing nomenclature drawings, Figures 5(a) through 5(e). Because of the inclined cage in the angular contact bearing of Figure 5(e), a certain pumping action exists from the “a” to the “b” direction. In most instances, lubricant finds it more difficult to flow from “b” to “a” because windage will have to be overcome. Windage is the fan effect that generates air flow from the smaller to the larger cage diameter. In essence, an inclined cage acts as a tiny impeller, blower, or small bladed fan (Ref. 3).
Side “a” is called the “back” of a bearing. Note that this is where the outer ring is wide and the inner ring is narrow. In an inadequately designed bearing housing this windage can cause fluctuating oil levels or leakage from bearing housing seals. Issues of windage and pressure balance are related to cage location and cage configuration; both are very important. Note also that with back-to-back mounted thrust bearing pairs, oil applied by traditional means will encounter point “b” before it can reach point “a”. Remember that fact whenever you deal with oil rings, perhaps in a future issue of “Knowledge is Uptime.” Lubricant application by oil ring is still Present Practice, but it is decidedly not Best Available Technology—in spite of the fact that oil rings have been around since the mid-19th Century. We will deal with it in a future issue of “Knowledge is Uptime.”
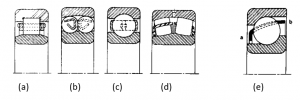
Figure 5: (a) Cylindrical roller bearing; (b) self-aligning ball bearing; (c) deep-groove ball bearing; (d) spherical roller bearing; (e) angular contact ball bearing
API-style pumps are of sturdy construction and are recommended by the American Petroleum Institute (in its Standard API-610) for flammable, toxic, or otherwise hazardous services (Ref. 2). It should be noted that, in API-style process pumps, two separate angular contact ball bearings styles per Figure 5(e) make up the set typically used to absorb the axial thrust load created by impeller hydraulics.
References
- Bloch, Heinz P. and Allan Budris; “Pump User’s Handbook: Life Extension,” 4th Edition, (2014), Fairmont Publishing, Lilburn, GA, ISBN 0-88173-720-8
- Bloch, Heinz P.; “Pump Wisdom: Problem Solving for Operators and Specialists”; (2011), Wiley & Sons, Hoboken, NJ; ISBN 9-781118-04123-9
- Bloch, Heinz P.; “Petrochemical Machinery Insights,” (2016) Elsevier Publishing, Oxford, UK, and Cambridge, MA, ISBN 978-0-12-809272-9