Case Description
A 365-acre community farm devoted to helping young people with special needs, suffered from high fuels costs which prevented much needed facility upgrades. This challenge inspired renewable energy and hydronic exploration.
Summary
Two hours north of New York City, in the beautiful Hudson River valley, is a 365-acre farm community with organic gardens, fields, two large greenhouses, 10 homes and a barn with pigs and cows. There’s also a dairy, bakery and pottery studio, all designed to serve young adults with developmental disabilities as residential or day students who are on the threshold of a transition into adulthood. Triform Community is staffed by men and women who have chosen to live in a community that is dedicated to helping young people with special needs. Today, there are 95 residents who enjoy life within the structured learning environment.
Last year, Triform managers tapped John Abularrage, owner of Stone Ridge, N.Y.-based Advanced Radiant Design, Inc. (ARD), to install a sophisticated wood-burning boiler and thermal storage system as the source for several interior spaces. Abularrage visited the community and soon devised a plan to install a small district heating plant that would move BTUs underground. The heart of the system is a 170 MBH Fröling wood gasification boiler coupled with a 1,500-gallon thermal storage system.
“Fuel costs were chewing through the community’s reserves and, at the same time, preventing some of the desired facility improvements,” Abularrage recalled.
Over the past few years, ARD crews have installed a dozen or more Fröling cordwood-burning and wood pellet-burning boiler systems. He was confident that, after studying the community’s needs, the wood boiler/thermal storage solution, which is manufactured in Austria, would work ideally for them.
According to Abularrage, with so many complaints about smoke caused by the outdoor wood boilers that dot the countryside, many towns and states are cracking down on wood-burning appliances. New emissions standards are pending at both the federal and state levels. That’s why state-of-the-art gasification “biomass” boilers – also to include U.S.-made wood boilers like those produced by another firm, Brocton, N.Y.-based Econoburn – are now regarded as among the best heating systems from an environmental standpoint.
“A two-stage combustion process burns standard firewood very cleanly and at very high efficiencies,” Abularrage explained.
The first stage is a traditional low-temperature wood fire and takes place in the upper firebox. This is also where wood is loaded into the boiler. The smoke and creosote vapor that would normally go up the chimney and into the atmosphere as visible smoke is, instead, burned as wood gas at 1,800°F to 2,000°F in a second, refractory-lined, combustion chamber. This high-temperature secondary combustion not only cleans up emissions dramatically, but also gives the boiler near condensing levels of efficiency. Unique to Fröling boilers is a “Lambda” control system that, based on oxygen levels in the exhaust, continuously adjusts both primary and secondary air settings to achieve optimal combustion throughout the burn cycle. The boiler control automatically modulates the induction fan speed based on boiler and thermal storage temperatures. This makes their gasification boilers some of the cleanest burning, low NOx systems available.
In Triform’s mechanical space, ARD crews installed the boiler and it’s large, site-assembled thermal storage tank with copper coil heat exchanger. Between them went a large control panel, with hydronic components that were pre-assembled with factory precision back at ARD’s home shop.
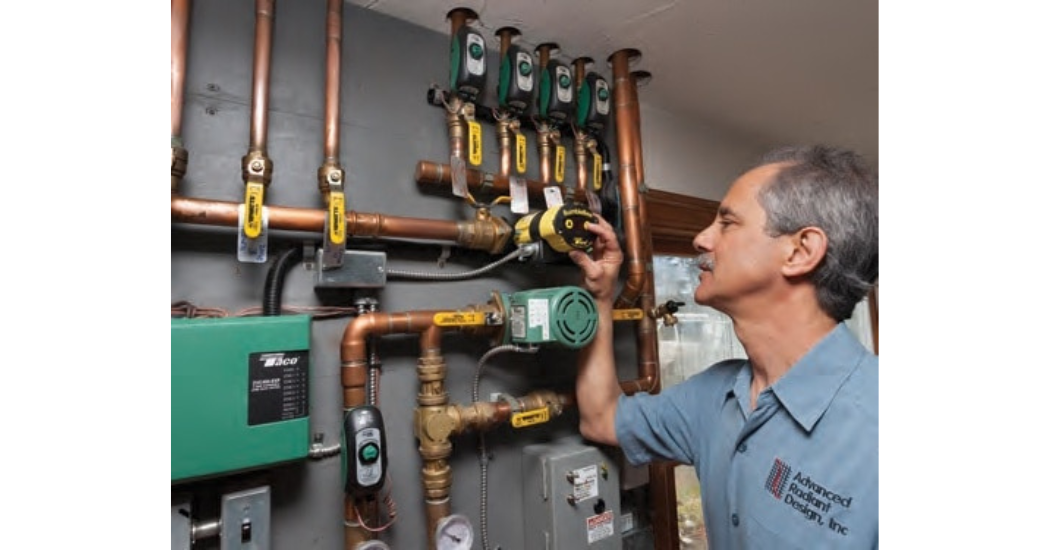
John Abularrage checks the function of a Taco Bumble Bee circulator (now discontinued) at another biofuel job just a few miles down the road from the Triform facility. Photo by Joan Barker.
At Triform
The Triform Community panel’s six-zone, primary-secondary piping arrangement includes many specific wood boiler components – such as a Termovar loading unit to protect a boiler from thermal shock and condensation, a diverter valve that sends excess heat to the storage tank, and an “automag” valve to activate a dump zone in the event of a power outage.
“We chose Taco’s ECM motor Bumble Bee Delta T circulator and Zone Sentry zone valves to help maximize the efficiency of the overall system,” said Abularrage. “While we’ve built standard single and dual-temp radiant control panels for decades, it’s taken some time and careful thought to develop what we consider an optimal wood boiler control panel. And, if a job comes along that requires something different, then we go back to custom fabrication.”
Abularrage added, “For this job, we were one of the first firms to install some of Taco’s prototype BumbleBee pumps to prove-out their functionality. One of them is planted on the Triform panel. We were glad to have the opportunity, and from the day we commissioned the system in January of 2012, Triform’s hydronic system – and the little Bumble Bee – have performed flawlessly.”
The Bumble Bee is a wet-rotor circulator that utilizes the latest in ECM (electronically commuted motor) permanent magnet motor technology. It uses up to 85 percent less electricity than a standard circulator and its out-of-the-box settings and 360 ̊ swivel flange makes it easy to install. The Delta-T circulator has the ability to determine the exact flow required to match ever-changing building heat loads, all the while reducing boiler short cycling, increasing total system efficiency, maximizing energy savings, and improving comfort.
“The Bee offers flow up to 15 gpm and head up to 15 feet,” explained Abularrage.
Factory preset to run in Delta-T mode, it can also be programmed for variable speed set point operation to maintain a fixed supply temperature or dialed in to one of four fixed speeds. Integral flow checks (IFC) and two plug-in remote temperature sensors are included in the carton. The high-temp hydronic system installed for Triform provides heat for a 288 square foot staff meeting room, a small greenhouse (720 square feet), the larger one (3,072 square feet) and the 2,500 square foot barn woodworking workshop areas. All, but the meeting room with 16 feet of baseboard, receive heat via fan coil units.
“The tank’s water temperature will vary according to where the boiler is in its cycle, and what the heating loads are,” explained Abularrage. The delivery system is designed to work at temperatures between 140°F and 180°F. “When there’s a heat demand, the boiler’s always sourced first, and if the boiler’s in a cycle where adequate output isn’t available, then heat is sourced from the tank,” Abularrage added.
According Abularrage, the boiler’s gasification process involves a carefully engineered firing process through two combustion chambers. The boiler is designed to run continuously, hot and clean, and at close to maximum output. When optimal output and operational efficiency are achieved, the heating load is served directly from the boiler. If the boiler is producing a higher-than-load output, excess heat is sent to the storage tank, allowing the boiler to continue operation at peak efficiency.
“But if a call for heat exceeds the boiler’s output, or if the boiler isn’t firing, the system pulls heat directly from the storage tank,” said Abularrage.
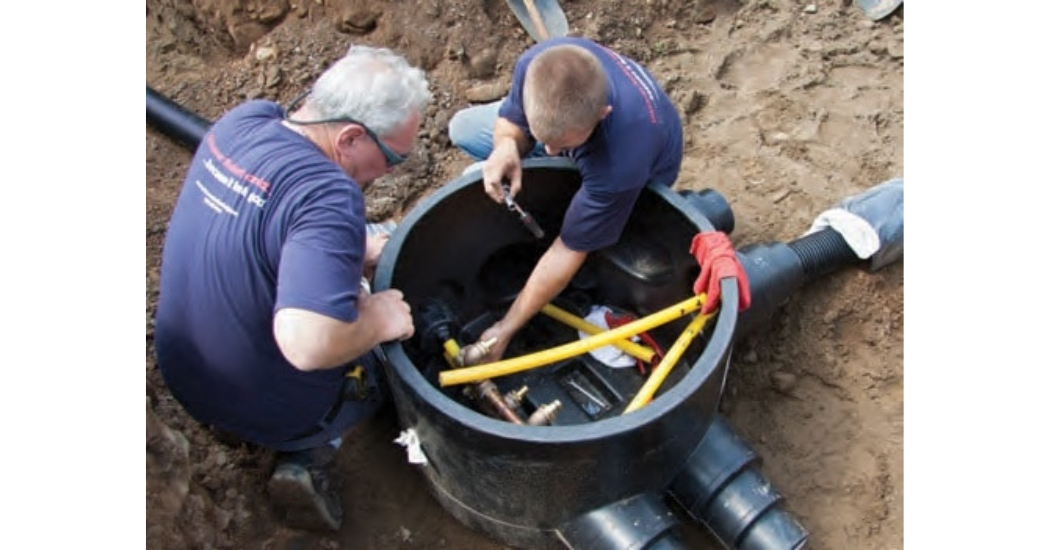
Mike Cahill, job foreman and shop manager, and Bob Witte, assistant mechanic, make Watts Radiant R-Flex supply and return connections inside an R-Flex distribution vault. Photo by Joan Barker.
Final Result: Subterranean heat
To provide heat for the community, ARD crews installed the heat plant in an improved area that was once used as a tool shed. They dug trenches and buried about 400 lineal feet of preinsulated, 1-1/2-inch R-Flex supply-and-return tubing manufactured by Watts Radiant to circulate heated water/glycol mix to the large greenhouses, new woodshop and the meeting room.
“Products like R-Flex have made small, district heating plant installations viable for homes, schools, farms and businesses,” said Abularrage. “The use of R-Flex at Triform was a huge advantage for us, making it possible to deliver heat in many directions with negligible loss of BTUs.”
R-flex piping consists of long-lasting PEX carrier pipes surrounded by thick micro-cellular, cross-linked polyethylene foam insulation layers with a closed cellular structure, all contained in a double-wall outer casing for maximum protection. The flexibility and light weight of R-Flex make it far easier to install than rigid piping systems.
An environmental win
“With firewood harvested from their own land, Triform is very pleased to be heating with a carbon-neutral, locally produced fuel, all while slashing their heating costs and allow- ing more money to be available to support their mission,” Abularrage said.
Triform’s newly-heated greenhouses not only produce food for community residents; they also offer a way for residents to acquire new skills.
“It’s an amazing place,” Abularrage continued. “It’s gratifying to solve a challenge for the community. We have grown very fond of the staff and residents.”
Keith Bogdanovich, co-director of Triform, said that if they were heating the greenhouses with gas or oil there would be no advantage in growing lettuce, spinach, tomatoes and cucumbers for the residents.
“But today we harvest our own fuel, saving substantially that way, and now we also save by growing food,” Bogdanovich said. “The greenhouses are producing year-round. Our only regret is not having done it sooner. Last winter was rather mild, but the winter before it was awful. If we’d have made the switch to wood heat a year earlier, our savings would have been that much greater.”
Article by John Vastyan