Contributor: Dorota Zoldosova, Head of Marketing and Communications, Sulzer
Careful planning is key to successful repair of coker drums
Delayed coker units (DCUs) operate under extremely harsh conditions, particularly during quench cycles. These can cause cracking, bulging or corrosion of coke drums, eventually leading to equipment failure. Weld overlay offers an interesting solution to repair DCUs and their coke drums, yet it should be carefully planned and controlled to ensure the delivery of a durable system.
Andrew Petticrew, Business Development Manager at Sulzer Tower Field Services, looks at the importance of desk-based assessments and real-time monitoring to perform top-quality weld overlay repairs
Weld overlay offers a highly cost- and time-efficient alternative to coker drum replacements when surface cracks, bulges and corrosion compromise the correct functioning of the DCU. Different weld overlay solutions are possible, each one using a large number of processing parameters. Therefore, skilled repair specialists must be able to evaluate the various alternatives, choose the most suitable and reliable, as well as set the processing parameters correctly.
Finite element analysis
Sulzer, a leading provider of specialized field services with over 40 years of experience in tower, drum and vessel maintenance, repair and revamps, conducts detailed finite element analysis (FEA) to ensure the ideal weld overlay practice is selected.
FEA, also known as finite element method (FEM), is a key tool to simulate weld overlay procedures and the resulting residual stresses and distortions. More precisely, FEA offers a computer-aided insight into the mechanical and thermal behaviors of weld overlaid structures, such as coker drums. As a result, the technology allows weld overlay operators to define an optimal strategy in a quick and cost-effective way, without the need for real-world experiments and pilot tests.
Within the FEA program, a model of the pieces of equipment with a possible weld overlay is computed and subdivided into a mesh with a finite number of small elements, each of which is assigned its specific mechanical and thermal properties. Mechanical models analyze the relationship between stress, strain and elastic moduli, while thermal models use features such as thermal conductivity and heat capacity to determine thermal expansion as well as which areas reach threshold temperatures during operation.
The comprehensive model is then virtually exposed to the conditions that it is expected to withstand during operation. Different project plans can be tested and based on the results from the FEA simulation, specialists can fine-tune the weld procedure by adjusting the parameters within the model. This enables the most efficient position and dimensions of the weld patches for the intended coker drum repair to be established. As a result, customers can be sure that their equipment will run optimally under non-steady state operating conditions.
Real-time monitoring
Once the optimal weld overlay procedure has been selected, it is important to stick to it. A method to ensure this consists of using a laser profilometry system that monitors the topography of the surface being welded. By creating a detailed and accurate surface map, the laser-levelled track system can detect small surface imperfections that require thicker or thinner weld overlay to ensure continuity and homogeneity.
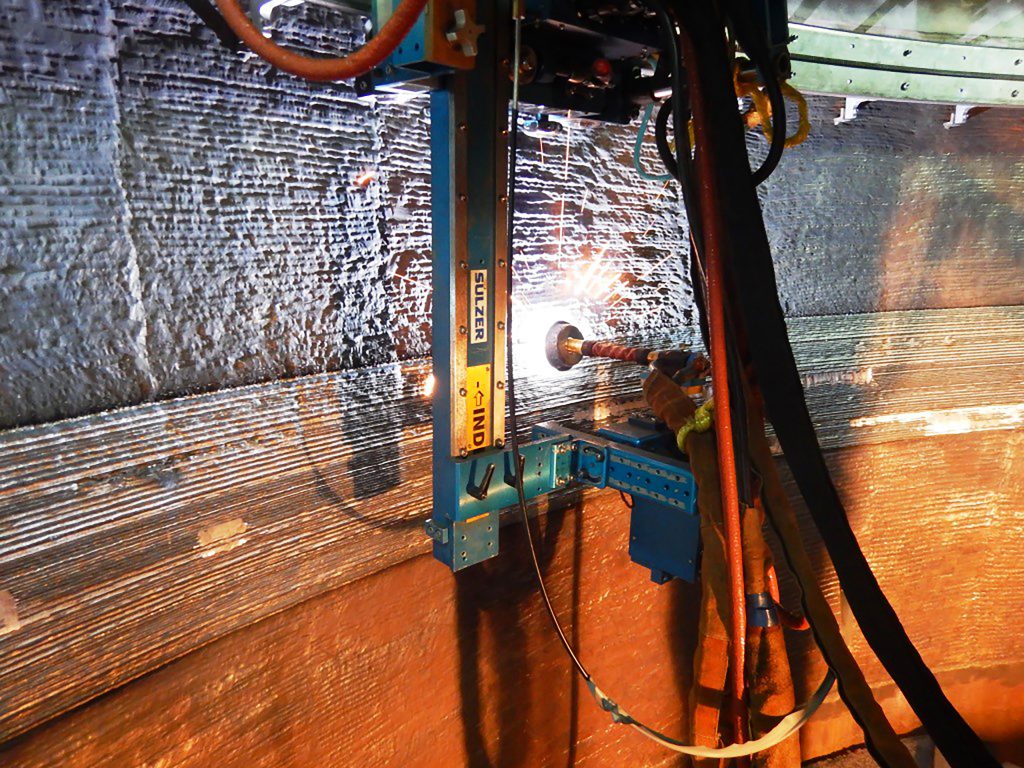
Sulzer improves the end quality of its weld overlays with the use of CladFuseTM technology, automating the entire process.
In addition, Sulzer further improves the end quality, reproducibility and consistency of its weld overlays by means of its CladFuseTM technology that automates the entire process. The system uses a programmable logic controller (PLC)-based robotic index arm that moves the welding torch and the oscillator in order to create weld beads. All the relevant process parameters, such as carriage speed or bead thickness, are controlled by the PLC, according to the weld sequence defined by FEA. As a result, the automated process can quickly perform welding with high accuracy.
Refineries always aim to improve the durability of their equipment and advanced weld overlay provides a highly suitable repair method. When this technique is backed by high-quality FEA and real-time control, plants can restore the initial DCU capabilities and run their operations at peak performance. By choosing leading experts like Sulzer, businesses can rely on carefully designed and controlled weld overlay projects that efficiently extend the service life of coker drums whilst minimizing downtime.
About Sulzer:
Sulzer’s core strengths are flow control and applicators. We specialize in pumping solutions and services for rotating equipment, as well as separation, mixing and application technology.
The Chemtech division is represented in all important industrial countries and sets standards in the field of mass transfer and static mixing with its advanced and innovative solutions. The product offering ranges from process components to complete separation process plants. The customer support covers engineering services for separation and reaction technology and tower field services to perform tray and packing installation, tower maintenance, welding, and plant turnaround projects. Our customers benefit from a network of over 180 production and service sites around the world. Sulzer has been headquartered in Winterthur, Switzerland, since 1834. In 2018, we achieved sales of CHF 3.4 billion with around 15’500 employees. Our shares are traded on the SIX Swiss Exchange (SIX: SUN).
Geothermal plants in Philippines benefit from Sulzer expertise