Sulzer’s turnkey pumping station reduces energy costs by 40%
Sulzer has completed the first in a series of wastewater pumping stations for a Danish municipality. Replacing a pre-existing facility, the new station offers twice the capacity of the old one, while its highly efficient, horizontally mounted XFP pumps have cut energy demand by 40 percent.
The project, in the Danish city of Aarhus, will be one of up to ten new pumping stations delivered under a six-year framework agreement with the municipality. Those stations will each use one of three standardized, modular designs developed by Sulzer to meet the needs of its customer. Sulzer wastewater engineers took advantage of advanced computer-aided design techniques during the development process, including the use of virtual reality technology to help the customer visualize the new concepts.

The XFP pumps working in a duty/standby arrangement, give the station a capacity of 25 liters per second.
Turnkey solutions
Under the terms of the agreement, Sulzer will be responsible for end-to-end execution of the pumping stations, including detailed design, supply of pumps, control systems and pipework, installation, and the demolition of pre-existing stations. To minimize disruption during construction, the new stations make extensive use of modular design elements and pre-cast concrete structures that can be manufactured off site.
The first station delivered under the new framework is based on the largest of the three design concepts. Its two XFP pumps, working in a duty/standby arrangement, give the station a capacity of 25 liters per second. That’s double the previous station’s capacity and enough to meet expected wastewater demand in the area for the next 25 to 30 years.
The station’s dramatic improvements in energy efficiency come from a combination of the advanced pump design, the use of high-efficiency electric motors and the introduction of new control systems with variable speed drives that allow the station’s output to vary smoothly in response to changes in demand.
Commissioning of the station went smoothly too. Once construction was complete, the changeover from the old station took around two hours, minimizing disruption to the local sewage network and eliminating the need to use tankers to remove wastewater while the system was offline.
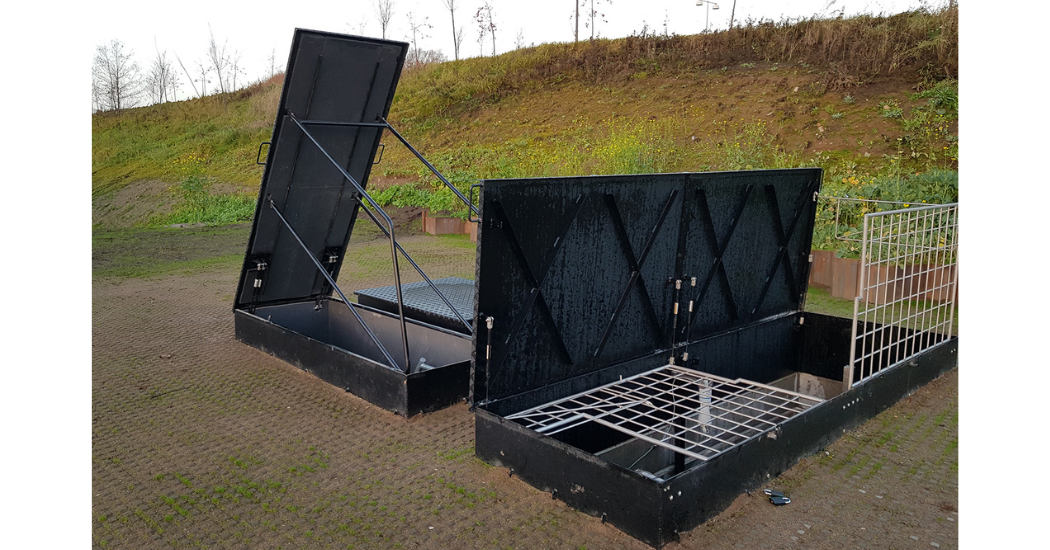
The pumping station design uses a dry-well concept.
Streamlined approach
For the municipality, using a library of standard designs will streamline the process of commissioning and constructing each pumping station under the contract, since per-project design time is minimized, and manufacturing can commence as soon as the customer is ready to initiate a project.
While fast project execution and the use of the latest and most efficient pump and control technologies were key aspects for the customer, it also wanted to improve working conditions for its operations and maintenance staff. All but the smallest pumping station designs use a dry-well concept, and the horizontally oriented pumps are mounted on special maintenance sleds that allow them to be decoupled and moved for maintenance without the need for heavy lifting equipment.
The sled allows most common maintenance operations to be completed by a single operator. The use of common equipment types and design concepts across all the new pumping stations, meanwhile, will simplify spare parts management, reduce training requirements, and make it easier for staff to familiarize themselves with operations and maintenance tasks.
“The customer is keen to streamline the whole operation relating to pumping stations, so using a modular design from one supplier means they benefit from cost savings throughout the lifecycle of the station,” explains Kenneth Larson, Technical Manager, Sulzer Pumps. “From concept to operation and spare parts, every aspect of our solution is designed to make the project as cost-effective and easy to run as possible.”
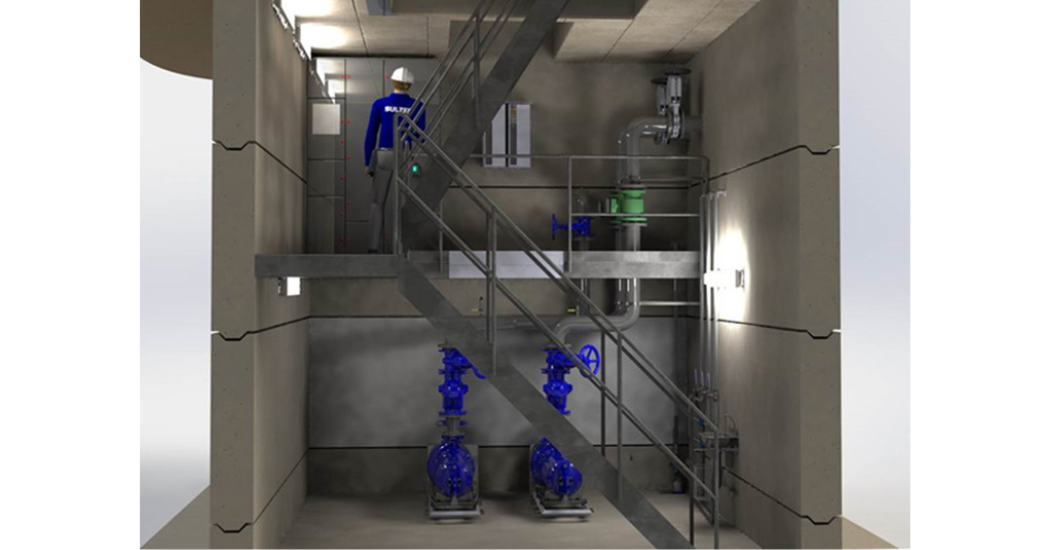
Sulzer wastewater engineers used virtual reality technology to help the customer visualize the new concepts.
About Sulzer
Sulzer is a global leader in fluid engineering and chemical processing applications. We specialize in energy-efficient pumping, agitation, mixing, separation, purification, crystallization and polymerization technologies for fluids of all types. Our solutions enable carbon emission reductions, development of polymers from biological sources, recycling of plastic waste and textiles, and efficient power storage. Our customers benefit from our commitment to innovation, performance and quality through our responsive network of 180 world-class manufacturing facilities and service centers across the globe. Sulzer has been headquartered in Winterthur, Switzerland, since 1834. In 2022, our 12’900 employees delivered revenues of CHF 3.2 billion. Our shares are traded on the SIX Swiss Exchange (SIX: SUN). www.sulzer.com
The Flow Equipment division specializes in pumping solutions specifically engineered for the processes of our customers. We provide pumps, agitators, compressors, grinders, screens and filters developed through intensive research and development in fluid dynamics and advanced materials. We are a market leader in pumping solutions for water, oil and gas, power, chemicals and most industrial segments. www.sulzer.com
Through a network of over 100 service sites around the world, Sulzer provides cutting-edge parts as well as maintenance and repair solutions for pumps, turbines, compressors, motors and generators. We service our own original equipment, but also all associated third-party rotating equipment run by our customers, maximizing its sustainability and life cycle cost-effectiveness. Our technology-based solutions, fast execution and expertise in complex maintenance projects are available at our customers’ doorsteps. www.sulzer.com
Comments