Contributor: Sulzer
Downtime in the steel industry can be a very costly experience, so minimizing the completion time for major overhauls and repair projects is a prime objective. For one steel manufacturing site in Brazil, a large, integrally-geared compressor needed two impellers replacing and the original equipment manufacturer (OEM) had quoted 18 months as the expected project duration. The steel company turned to Sulzer for an alternative solution which was delivered in just 6 months and with a 35% saving in overall costs compared to the OEM.
Steel production is a very competitive industry that requires a tight control on costs and a constant effort to improve productivity. In order to achieve cost effective manufacturing, any maintenance or repair project that will affect productivity needs to be carefully assessed for the impact on production. Meticulous planning and the use of planned shutdown periods can greatly reduce the financial impact.
The large scale steel manufacturing facility in Brazil has a capacity to produce over 7 million tons per year and the associated industrial gas plant forms an integral part of the production process. Throughout the site, large pieces of rotating equipment require monitoring as well as remedial maintenance in order to minimize downtime.
In many cases, the steel plant operator had retained the maintenance services of the OEMs to ensure that all the necessary work was completed by engineers with sufficient expertise and access to the spare parts. However, this arrangement came under review as part of a rationalization process aimed at reducing repair costs and improving the timescales involved.
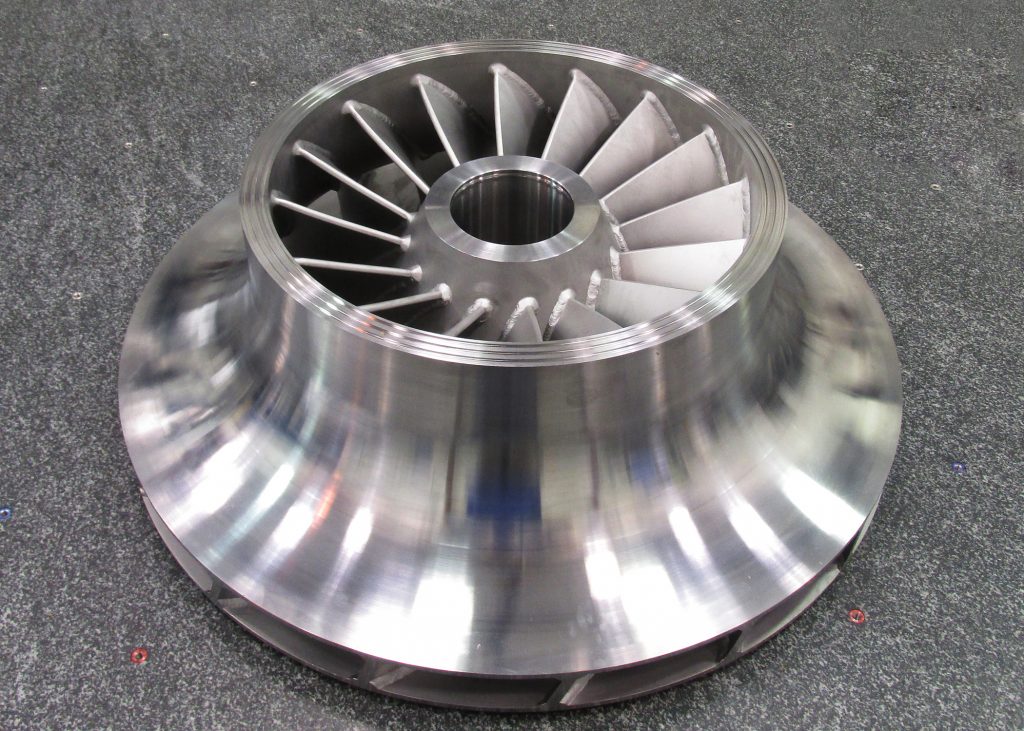
The new components allowed the project to be delivered with a huge time saving over the OEM proposal
As the leading independent service provider for all brands of rotating equipment such as turbines, pumps, compressors, generators and motors, Sulzer has the facilities, experience and expertise to deliver maintenance contracts across the world. This reputation, coupled with the ability to significantly reduce project delivery times compared to OEMs, led to Sulzer being selected as the maintenance partner for a number of projects.
The customer raised concerns about the performance and reliability of an integrally geared, 4-stage compressor. The first step was to establish the exact condition of the compressor and then establish a plan of action that would deliver the most cost-effective solution. Sulzer deployed an experienced field service team to carry out detailed inspections and diagnostics to identify the areas of concern.
The results of the inspection showed several issues, including a reduction in wall thickness of the third stage impeller and cracks in the fourth stage. Based on this, and the lack of operational reliability, the decision was made to take the compressor out of service until the impellers could be replaced.
In the past, the OEM would have been considered as the only option for such a repair, but in this case the lead time for two new impellers installed and commissioned was 18 months, a time frame that would be unsustainable for the customer. In contrast, the detailed repair program devised by Sulzer, which included precision laser measurement, manufacturing and installation, could be completed in just 6 months.
Rafael Ribeiro, Project Manager for Sulzer explains: “The key to a successful project such as this is close coordination of the various teams of design engineers, site engineers and manufacturing personnel as well as the ability to clearly communicate progress with the customer. In this way, decisions that are required throughout the repair process can be made with all the necessary information in place, making the project much more efficient.”
The process to reverse engineer two new impellers began with extensive measurements using portable coordinate measuring machines (CMM) and laser scanning to create a true 3D drawing. Positive material identification highlighted the potential to improve the corrosion resistance of the components by upgrading the base material.
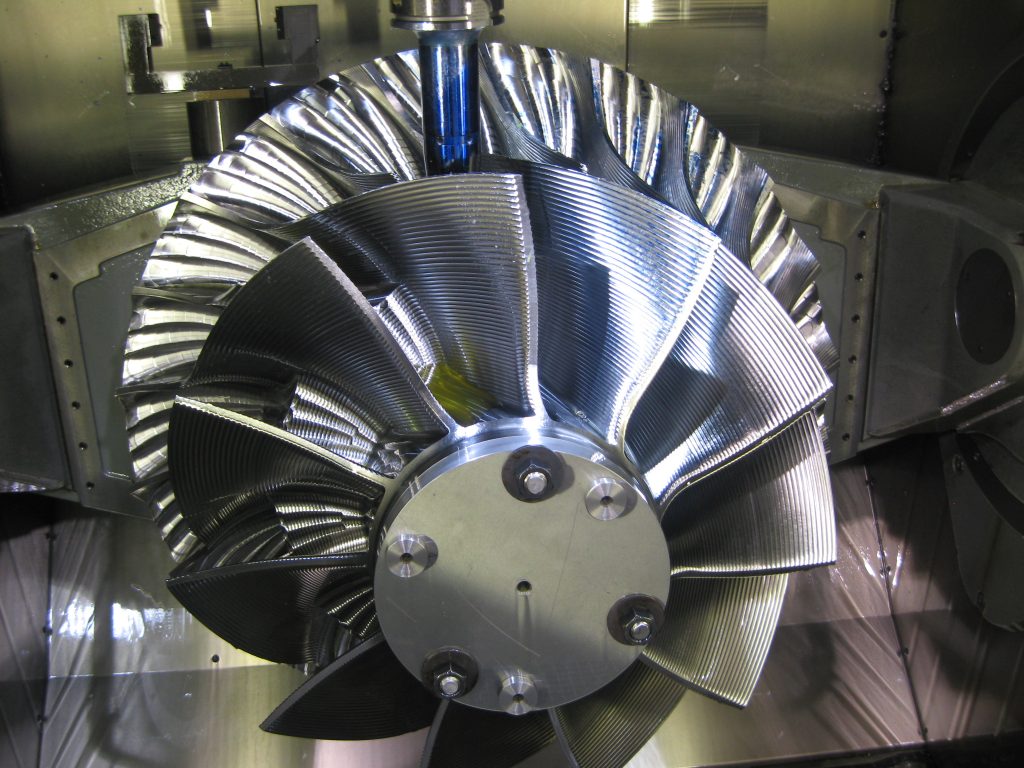
The new impeller vanes were manufactured from a solid piece of chrome molybdenum vanadium steel using 5-axis vertical milling machine
The new impellers were designed and manufactured at Sulzer’s Houston Service Center in Texas, where the new vane sections were manufactured from a solid piece of chrome molybdenum vanadium steel using a 5-axis vertical milling machine. These were then welded to the outer casing to create the finished impellers. In cases such as this, Sulzer can offer a range of anti-fouling coatings that can be applied to impellers to improve their durability and efficiency.
The completed impellers were shipped to the field service engineers where the installation and commissioning process was completed before the compressor was handed back to the customer.
Rafael Ribeiro concludes: “The decision to work with an independent maintenance provider has been completely justified by the significant savings in this project while meeting or exceeding OEM quality standards. In this case, Sulzer has delivered every aspect of the project to the satisfaction of the customer, especially the huge time saving versus the OEM delivery time.”