Advanced pump technology and rapid delivery capabilities expand geothermal generation in Turkey
Together with Sulzer, Italian geothermal power specialist Exergy, has been installing renewable power generation equipment at sites around the world. Their most recent project was the development of a new facility in Turkey. With decades of experience in pump design and engineering, Sulzer has become a preferred supplier of pump technology for geothermal applications. The company has significant experience in the complex design requirements of working fluid pumps, which must be adapted to match the characteristics of different fluid types and operating regimes.
Large-scale wind and solar farms are the most visible aspect of the global transition to sustainable energy, but there is another important source of clean, reliable power hidden beneath our feet. Geothermal energy is already the most important source of power in Iceland, now countries from Indonesia and the Philippines to Turkey are rapidly developing their own geothermal resources.
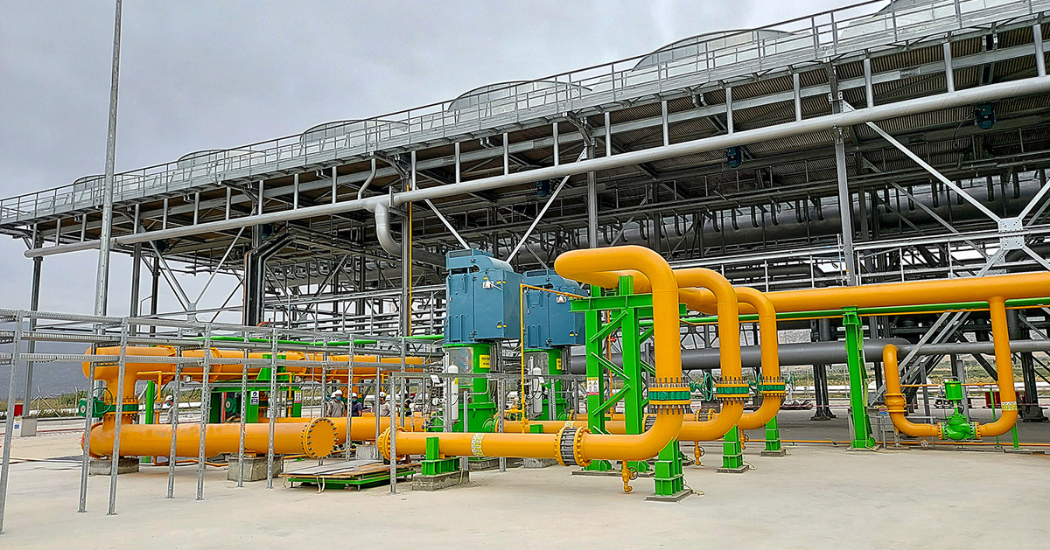
Sulzer’s main feed pumps installed in a Binary Cycle Geothermal Power plant. (Image Source: Exergy International srl)
Process enhancement
The energy for a geothermal power plant comes from hot water or brine extracted from deep underground aquifers. Traditional plants require water temperatures of at least 350 °F (180 °C) to create the steam used to run the station’s turbines. More recently, however, the geothermal industry has perfected an alternative approach that can operate at lower temperatures, greatly expanding the range of possible generating sites.
Binary cycle power stations pass hot brine from the geothermal borehole through a heat exchanger, where it heats a working fluid. This has a lower boiling point than water, allowing the plant’s turbines to operate efficiently at the lower geothermal temperatures. After the turbine, the working fluid is cooled and condensed, then returned to the heat exchanger to complete the loop. On the geothermal side, the cooler brine exiting the heat exchanger is re-injected into the ground.
Handling the working fluid in a binary cycle power station requires highly specialized pumping technology. The pump used to return the working fluid to the heat exchanger must be able to work with a very low net positive suction head (NPSH) and develop a high head to provide the right conditions at the inlet of the gas expander turbine.
Performance by design
The pump chosen for Exergy’s most recent project was one of the largest from Sulzer’s SJD CEP range of multistage canned vertical pumps. The selected pump has a unique double suction first stage, which ensures safe operation at low NPSH values, while, through its bowl diffuser configuration, it can also develop a high differential head per stage. Achieving the high head required for the application with fewer stages results in a smaller pump that is easier to integrate into the plant design. For the customer, fewer stages also means lower purchase, spare parts and maintenance costs.
Andres Mercader, Tendering Manager, Sulzer Pumps, explains: “Exergy was already confident that the Sulzer design would meet its performance expectations; an identical design has been in operation for several years at another of the company’s projects in Turkey. The key challenge for the latest build was ensuring every component of the project could be manufactured and delivered to exceptionally tight timescales.”
Rapid construction
In common with other renewable energy installations around the world, geothermal power plants often benefit from government financial support. Accessing that support requires facilities to be up and running before pre-agreed deadlines, leading to tight construction schedules.
To meet the delivery deadline, Sulzer drew on its global manufacturing and supply chain capabilities. All parts were then inspected, assembled and tested in one of Sulzer’s facilities focusing and specializing in vertical pumps. The standard, modular design of the CEP pumps proved especially beneficial here, as high-precision casts and components are shared by several Sulzer facilities across its global supply chain locations.
After assembly, the pump was tested with water at full speed using a calibrated lab test motor. Upon successful completion of the test, the motor was replaced with the smaller job-specific motor, since the isopentane working fluid used at the power plant is significantly lighter. Despite the challenging timeframe, the completed unit was delivered to the customer ahead of schedule, helping to ensure the plant could begin generating power before its deadline.
“Our mission is to shape technical innovations and deliver high quality services that enable our customers to transform a heat source into clean, sustainable and efficient power. To attain this target our projects depend on reliable, high-performance components from leading specialist suppliers,” says Marco Frassinetti, Sales Director at Exergy. “Sulzer has once again met our expectations and helped us to meet a very tight schedule.”
Comments