Innovative weld repair saves time and expense for main oil line pumps
Main oil line (MOL) pumps are responsible for transferring oil away from platforms and on to processing and storage facilities. As such, their reliability is very important with any downtime needing to be kept to a minimum. For one international oil company (IOC), one of a group of five MOL pumps was severely damaged but Sulzer was able to return it to service in just 12 weeks for a fraction of the replacement cost.
After more than 18 years in service, the MOL pumps had been exposed to considerable erosion damage and had effectively reached the end of their design lives. However, the IOC was planning to increase the flowrate through the platform as production from other facilities was to be directed to this unit. To achieve this, the MOL pumps needed to be inspected and repaired within the shortest possible timeframe.
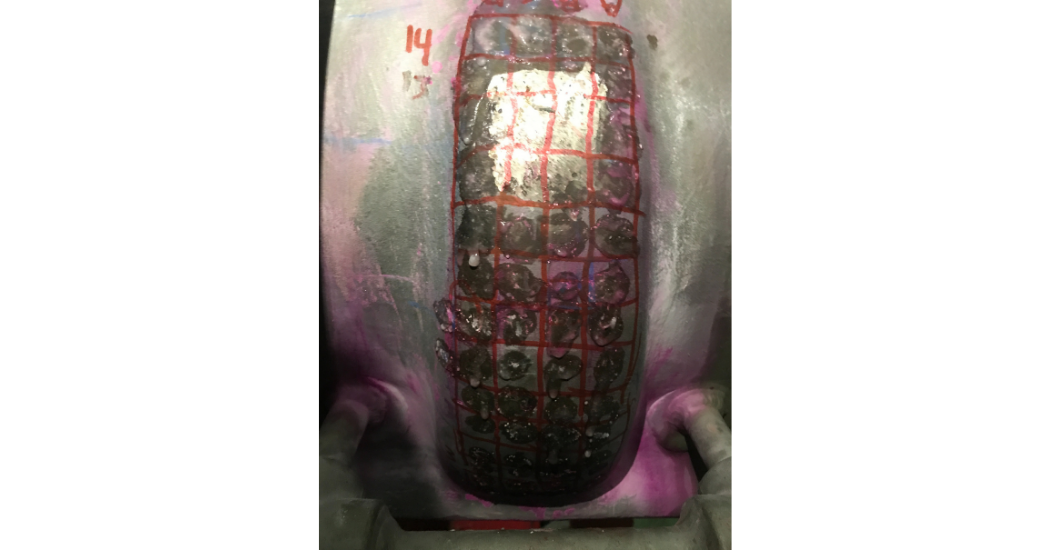
Repairs to the volute were carefully completed to ensure continued integrity of the surrounding material
Repair or replace
Sulzer’s initial inspection of one pump revealed significant erosion of the impeller tip, internal passages, shrouds, inlet vanes and the casing cutwater areas. There was also a leak from the suction volute, all of which meant that the operator faced two options: repair or replace the existing casing and impeller.
Sourcing a new casing would have had a lead time of around 48 weeks as well as being a large investment. Sulzer’s repair solution could be completed in just 12 weeks and for 25% of the replacement cost. This would extend the design life of the pump for at least another five years.
The impeller was beyond economic repair and was replaced. Sulzer applied a boron coating to the new component using a chemical vapor deposition process to improve its wear resistance. In addition to this, the repairs to the casing would require an innovative solution to ensure a reliable, long-term solution.
The first step was to measure the casing thickness along the areas of erosion, to ensure that the area highlighted for the repair was the only one and that the rest of the casing was in good condition. Having established this, it was possible to develop a repair schedule and advise the operator of the planned actions.
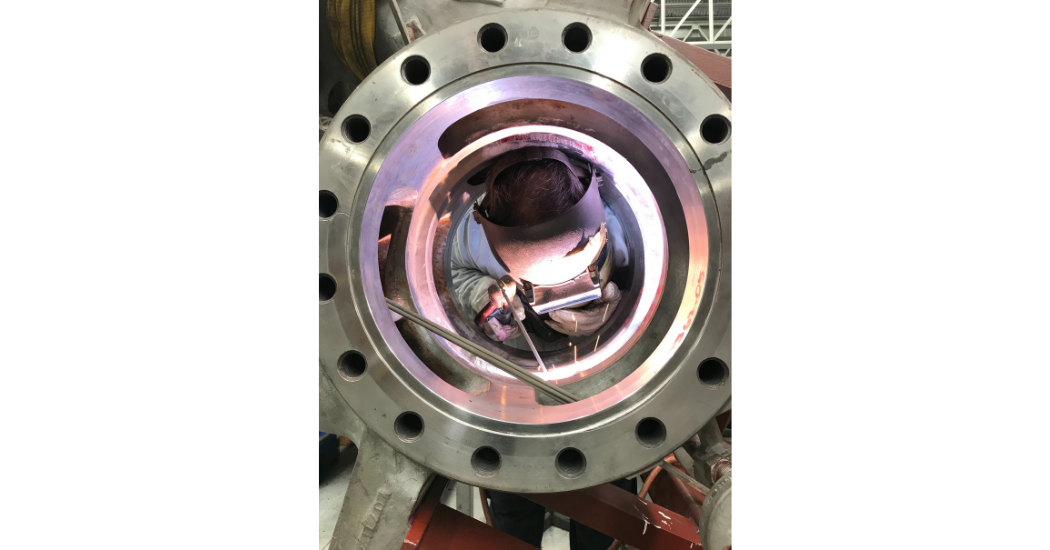
Applying overlay and hard-facing welds to the internal geometry
Long-term solution
The erosion had caused considerable damage to the volute, but its design meant that it was not possible to access the area that required attention, which ruled out using high velocity oxygen fuel (HVOF) coating technology which typically has its limitations to “Line of sight” coating capability only. It would also be very difficult to complete any weld overlay repairs unless a hole was cut in the volute to allow access to the damaged area.
Manish Talwar, Head of Retrofits APAC for Sulzer explains: “This was quite a complex and difficult task. The base material was CA6NM, which requires pre-heating before any welding can be completed, to avoid damaging the surrounding material. We were able to remove a section of the volute, complete the overlay and hard-facing welds before checking the integrity of the repair using dye penetrant testing.”
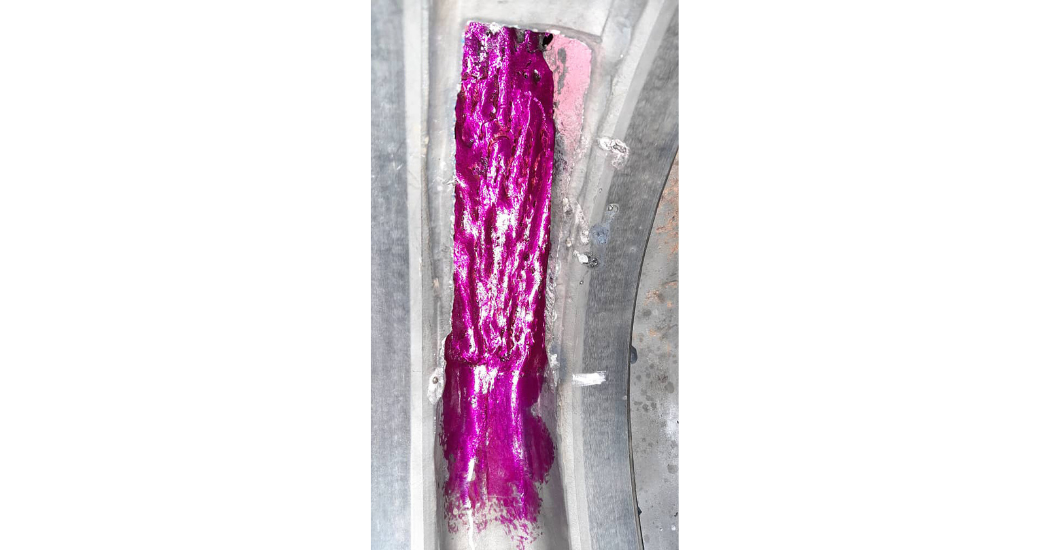
Weld quality was checked using dye penetrant testing
Sulzer also included some mechanical design improvements, such as the integral wear rings, which will reduce maintenance time in the future, and the shaped cutwater for improved durability. While the casing repair was being completed, the remainder of the pump was overhauled, and all bearings and seals were replaced before the pump was reassembled. Throughout the project, the operator was provided with regular updates, including photos of the work in progress.
Manish concludes: “These pumps are very important for the future productivity of the platform. The repairs we have completed will ensure at least another five years of reliable service and at a quarter of the cost of replacing the casing. More importantly, we quickly delivered a solution that required no external modifications while keeping downtime to an absolute minimum.”
Comments