Contributor: Alex Edwards, Marketing & Communications Manager, Rotating Equipment Services, Sulzer
Aging frequency converter given extended service life
When specialist equipment, such as a frequency converter, needs to be refurbished, it is best to work with expert suppliers that have the experience and facilities to complete the project efficiently. With a state-of-the-art high voltage (HV) coil development lab, Sulzer was ideally placed to support a partner during the rewind of a large 20 tonnes (approx. 22 US tons), common-shaft frequency converter.
Also known as motor-generator sets, rotary frequency converters are used in many industrial applications to provide an electrical supply with a precise frequency, usually different to the local grid supply. Their robust design makes them particularly well-suited to operating in outdoor locations and with proper enclosures can provide long and reliable service.
Frequency converters consist of a motor which is coupled to drive the generator. The main principle behind their operation is the difference in windings between the motor and the generator, which allows the frequency of the supply to the motor to differ from the output of the generator.
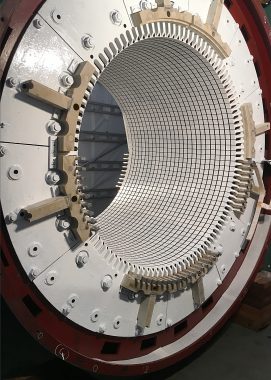
Sulzer also designed and manufactured a new blocking system using Class F materials.
These specialized pieces of equipment are used for applications with large starting motor loads or where particularly clean supply, i.e. free from harmonic distortion and noise, is required. They are often seen in marine, offshore and military applications as well as the rail sector.
Despite their rugged design, many years’ service takes its toll and there comes a time when the unit needs to be refurbished, as was the case for a recent project that was undertaken by Sulzer. In this instance, the project was in partnership with Karsten Moholt, which has worked with Sulzer on larger rewind projects for many years.
Routine maintenance of the frequency converter had revealed low insulation resistance readings on the windings of the generator and Karsten Moholt was contracted to complete the repair. In projects involving larger pieces of equipment there is a long-standing arrangement that Sulzer offers assistance with the repair through its HV coil center of excellence in Birmingham.
The process began with the stator being disassembled, unsoldering the coil joints and removing all of the original insulation using a controlled burn-off oven, before cleaning and polishing the copper bars. The coils were then reinsulated using resin-rich tapes and consolidated in a heated press to produce the precise coil slot dimensions.
Benny Hinchliffe, Head of International Sales explains: “In this case, Sulzer reinsulated the generator side of the frequency converter using the existing copper bars, which had a Kaiser transposition as part of the design. This is where two pieces are copper run side-by-side and cross over one another within the slot section. This is more commonly seen in traction motor coils, which are also manufactured at the Birmingham Service Center.”
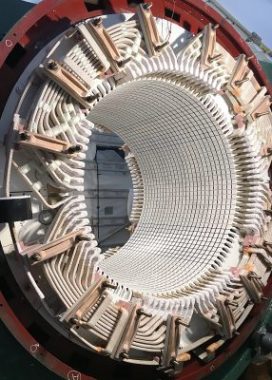
The finished stator, which weighs 2 tonnes, was returned to Karsten Moholt within six weeks.
As part of the project, the engineers in Birmingham also designed and manufactured a new blocking system to replace the original components which had begun to crack and deteriorate due to age. The new blocks were manufactured to meet the Class F insulation standards and will provide a much-needed extension in the service life of the components.
In many cases, customers often come to the Birmingham Service Center to review progress and as part of the customer acceptance tests. Recent investment by Sulzer has seen HV coil testing capacity significantly increased. It is now possible to prove insulation systems quicker as well as watch live tests from a remote location, making it easier for customers to witness tests and check the results.
Benny Hinchliffe concludes: “In all, the whole project was completed within six weeks and Karsten Moholt was able to return the completed frequency converter to the end customer on time. As a direct result of this project, Sulzer has also been considered for the refurbishment of the complete drive-train for a similar machine, which would include both stators from the motor and generator sides as well as the associated rotors.”