Like many arid regions around the world, southeastern Spain has long faced significant water shortages. In the early years of the new Millennium, with rising consumer demand and the changing climate exacerbating the challenge, Spain’s government and some regions’ water utilities launched a major desalination initiative. Most of it was developed by Acuamed, which is a public company that reports directly to the Ministry for Environment of the Spanish Government.
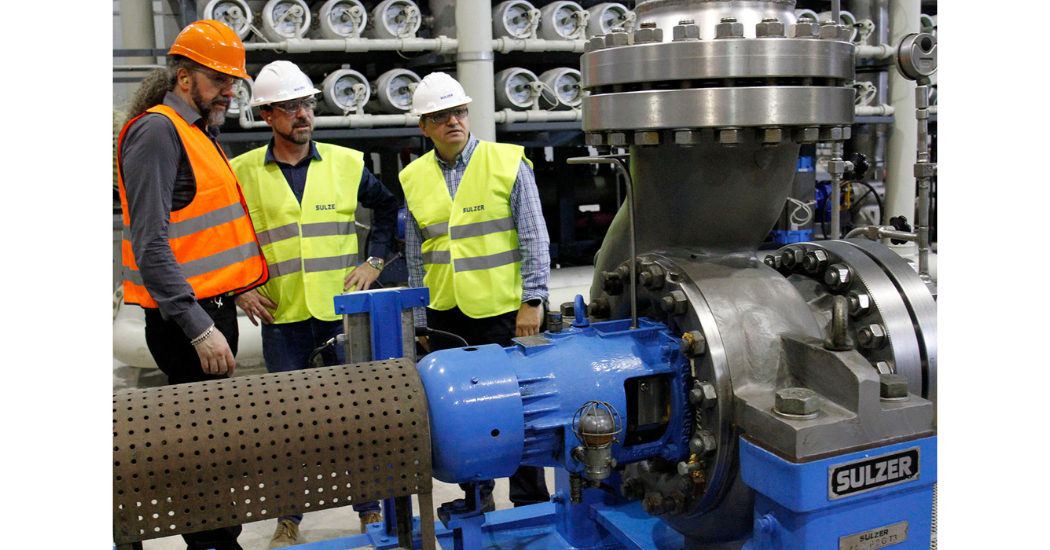
All the pumps use corrosion-resistant Super Duplex stainless steel.
The Torrevieja desalination plant, one of several new facilities constructed in the following years, is the largest reverse-osmosis (RO) site in Europe; it was built and is operated by the Spanish company ACCIONA. Since 2008, the plant has supplied up to 240’000 cubic meters of fresh water every day to the homes, farms, and businesses of 1.6 million people in and around Alicante.
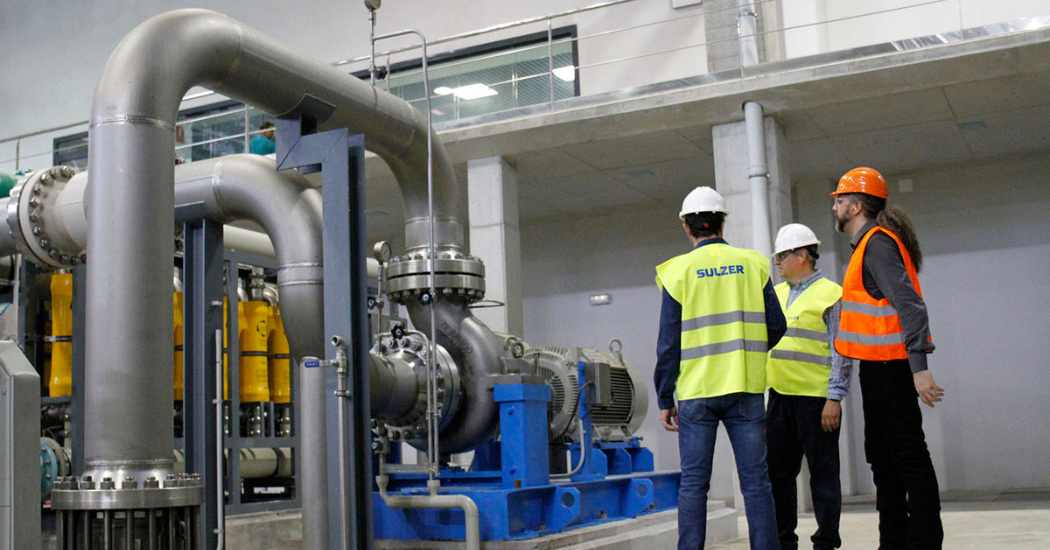
16 ERD Booster pumps driven with variable speed drive support the efficient operation.
RO technology has transformed the efficiency of desalination processes, but the production of fresh water from seawater on a large scale is still an energy-intensive activity. For the operators of these plants, and for their customers, efficient, reliable high-pressure pumps play a crucial role in minimizing their energy consumption and the final cost of the supplied water.
Mission critical pressure
For the specialist engineering company responsible for the Torrevieja plant, pump performance was an extremely important criteria, since it was contracted to design and build the plant, then operate it for a 15-year period. After an intensive and wide-ranging tender process, the contractor, with the owner’s agreement, selected Sulzer as its main pump technology partner for the project.
As a full-service provider for the different activities within the water industry, Sulzer’s Flow Equipment division is proud of its track record in helping utilities worldwide to optimize their operations as well as their sustainability. Offering state-of-the-art solutions and a truly global manufacturing and service infrastructure, Sulzer helps the water industry to create next-generation facilities that drive the sector forward into the future.
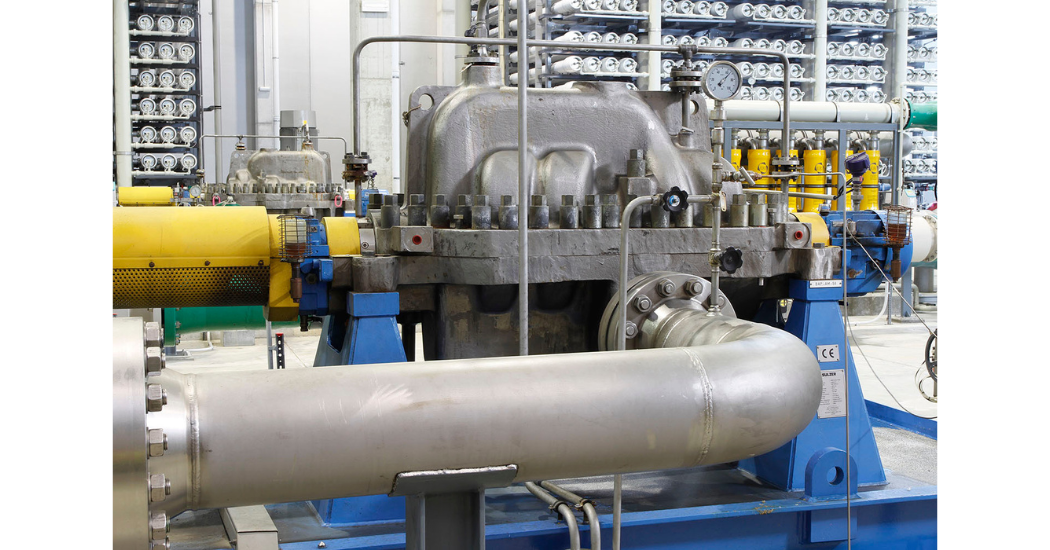
Sulzer delivered 16 MSD high-pressure pumps feeding the RO trains.
With a holistic understanding of the water sector, its applications and needs, coupled with comprehensive, industry-leading engineering skills, Sulzer equipment has been selected for many of the world’s most demanding water and wastewater projects. The company offers bespoke, fully integrated technologies that address the specific requirements of customers, along with the delivery capabilities to meet demanding design, engineering and construction timescales.
For the Torrevieja project, Sulzer supplied a total of 57 pumps, including 16 high-pressure pumps MSD type, and 16 ERD booster pumps, ZF type, the primary pressure generators for each of Torrevieja’s 16 RO trains. The project drew upon Sulzer’s worldwide engineering and production expertise: the MSD pumps were designed and manufactured in Leeds, UK and the ERD units were supplied by Sulzer’s plants in Spain and India.
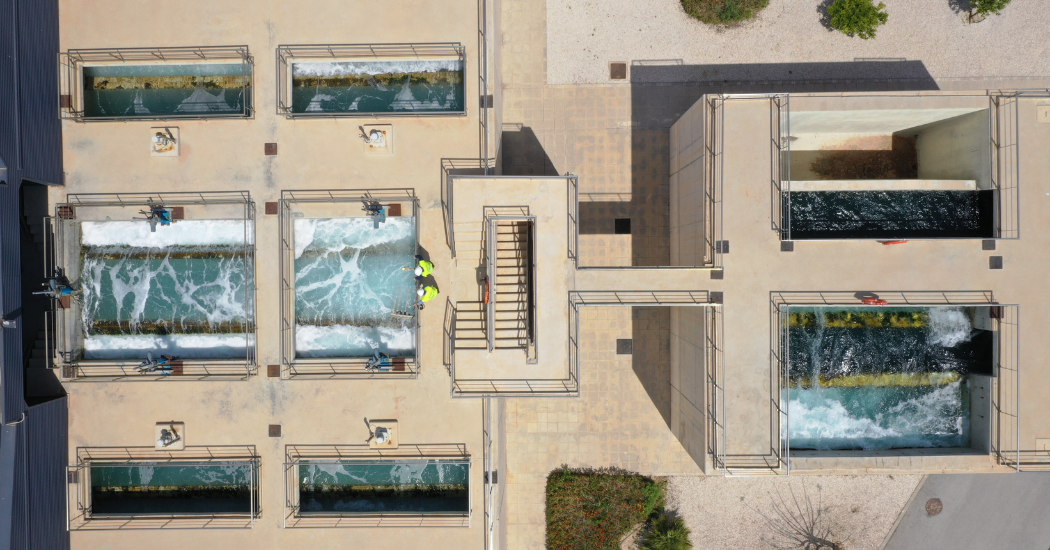
Sulzer supports globally the production of more than 14 million of cubic meters per day of fresh water.
Proven performance and reliability
Designed for a long operating life in a challenging seawater environment, the pumps all use corrosion and erosion-resistant Super Duplex stainless steel in their construction. The installation and commissioning took place during 2008 and 2009, with support from Sulzer field service teams.
Over the ensuing 13 years, the Sulzer pumps have met the plant’s demanding requirements. They have delivered exceptionally high levels of reliability and availability, continuing to operate with high efficiency, practically to the same level they achieved when brand new.
Torrevieja’s case is just an example of Sulzer’s success in the desalination sector. Today, more than 14 million of cubic meters per day of fresh water are produced with the support of highly reliable and efficient Sulzer pumps.
About Sulzer:
Sulzer is a global leader in fluid engineering. We specialize in pumping, agitation, mixing, separation and application technologies for fluids of all types. Our customers benefit from our commitment to innovation, performance and quality and from our responsive network of 180 world-class production facilities and service centers across the globe. Sulzer has been headquartered in Winterthur, Switzerland, since 1834. In 2021, our 13’800 employees delivered revenues of CHF 3.2 billion. Our shares are traded on the SIX Swiss Exchange (SIX: SUN).
Comments