Sulzer’s retrofit solution improves pump reliability and reduces parts inventory for refinery
Established refineries and petrochemical plants have hundreds of process pumps, usually from a multitude of manufacturers, that may have been in operation for decades. Over the years, API 610 specifications, which govern their design, have evolved to improve both safety and reliability. Today, modern materials and design concepts from Sulzer can be used to improve the performance of existing pumps and even commonize parts as exemplified by a case in Mexico, where 35 process pumps were upgraded.
For time-served assets in refineries and petrochemical plants, extending their service life can be a challenge and a replacement may appear to be the simplest option. However, in some cases, this may require extended lead times as well as changes in the existing pipework or pump foundations. A much quicker solution is to upgrade key components of the pump, bringing it in line with current specifications while simplifying the parts inventory at the same time.
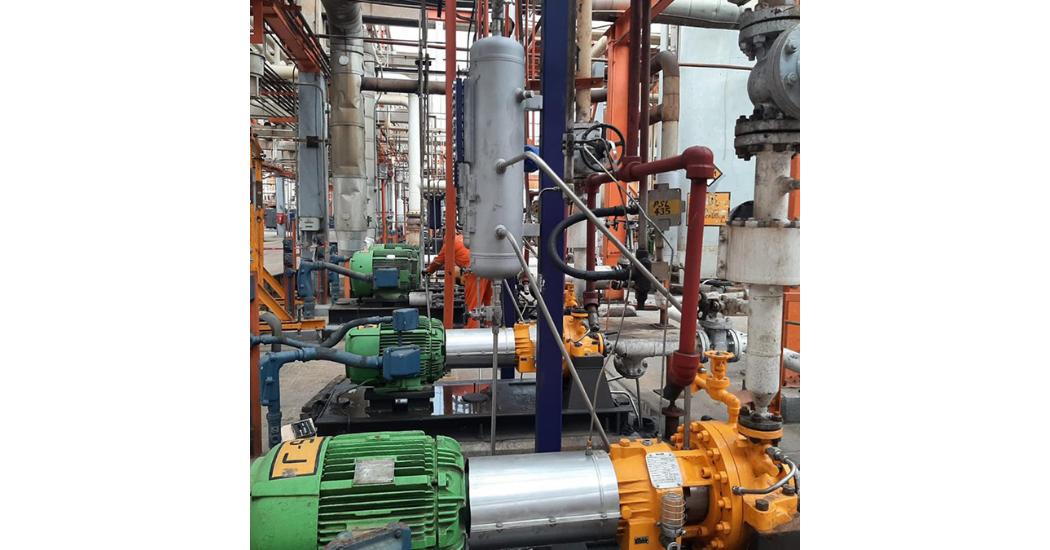
In total, 35 non-Sulzer OH2 process pumps were upgraded using the OHX retrofit kit
Improvements for aging assets
Take, for example a refinery in Mexico, which was commissioned in 1976, and processes several thousands of barrels per day. Since the refinery was built, API standards have moved on considerably, now on the 11th edition. Within the plant, process pumps are used for transporting propane, liquefied petroleum gas (LPG), sour water and gasoline.
Maintenance engineers had identified a number of pumps that were manufactured to 6th edition standards and would benefit from improved reliability. For example, one of the major factors affecting seal performance is pump vibration and since the 8th edition, the API 610 specification for stiffness of the impeller shaft has increased, reducing vibration and extending the mean time between failures (MTBF).
In addition, the design of the mechanical seals has also been enhanced and, in this case, a double seal as per API 682 was implemented to further increase reliability and reduce fugitive emissions, to comply with new environmental regulations. In total, 35 non-Sulzer OH2 process pumps had been identified for upgrade and Sulzer was selected to deliver the project based on the confidence that the operator had in the company and the proximity of the local service center.
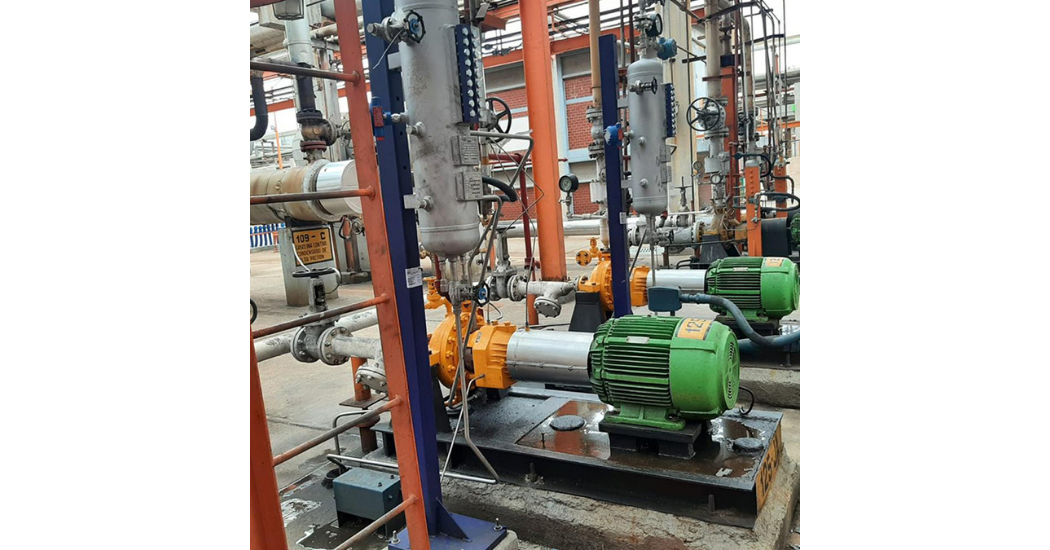
Redundancy in the processes enabled one pump to be repaired without affecting production
Cost-effective retrofit solution
Sulzer has developed the OHX pump retrofit kit to offer the latest API specifications to any brand of OH2 pump while delivering overall performance improvements without replacing the casing or making any changes to the connecting pipework. Just the affected parts can be upgraded, which is more cost-effective than replacing the whole pump.
A new case cover with API 682 seal chamber meets latest API 610 standards, which includes the double mechanical seal. In addition, the bearings are upgraded to a longer life component, extending the expected service life from 25’000 hours to 50’000 hours. This improvement also includes upgraded oil guards, which offer much better oil sealing compared to the components of the 1970s.
The retrofit kit also introduces a cooling fan and an improved coupling and guard. The former helps to reduce bearing temperatures, extending their service life, while the latter meets the latest occupational safety and health administration (OSHA) requirements.
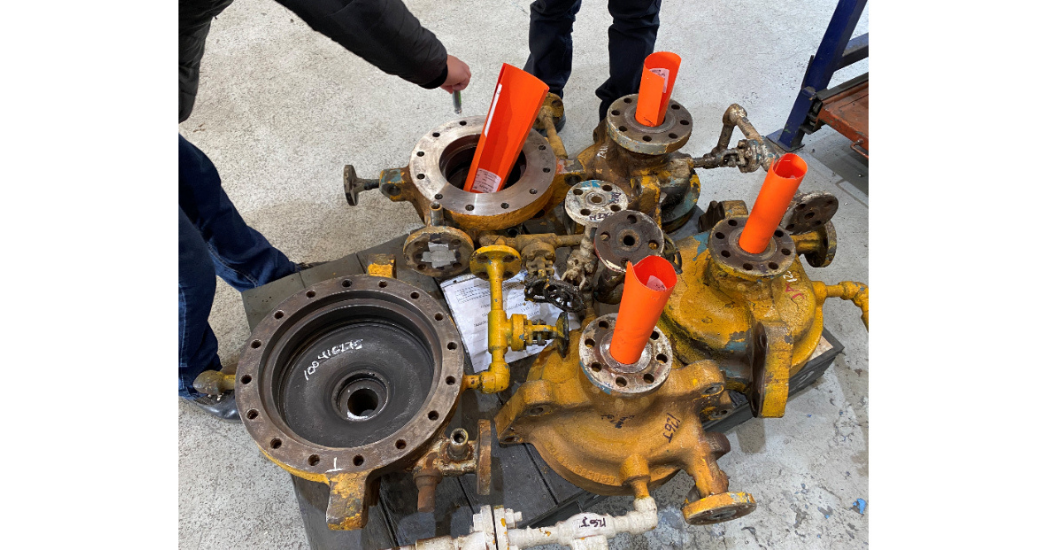
The process pumps were built in the 1970s and many components would benefit from the upgrade
Improved performance
Isabel Najera, Project Manager for Sulzer, explains: “The objective of this retrofit solution is to optimize long-term performance and reliability without impacting on the existing infrastructure. Pump upgrade projects such as the one for the refinery begin with essential information being gathered, including impeller diameter and volute measurements, which enable the case cover and other components to be manufactured without affecting the process pumps’ operation.”
Once all the parts are complete, they can be either installed on site or at the local Sulzer service center, keeping downtime to an absolute minimum. In most cases, these process pumps are paired with a standby unit, enabling the application to continue while one is upgraded.
Following on from the retrofit program, the updated equipment at the refinery now has common parts with Sulzer pumps on site that have been installed more recently, allowing the spare parts inventory to be optimized. Furthermore, Sulzer’s service center in Mexico manufactured the OHX retrofit kits, providing security of supply for spare parts in the future. The local facility also simplifies communication and could deliver on-site support for this project while also meeting any future requirements.

The refurbished pumps conform to the 11th edition of API 610
Fast turnaround
As a pump manufacturer, Sulzer has the necessary design expertise to enable the OHX kit to be installed on pumps from other OEMs, simplifying an operator’s spares inventory. By commonizing many components with other Sulzer pumps on site that have been installed more recently, operators can reduce operating and inventory costs.
Sulzer holds OHX retrofit kits in stock, so that lead times are minimized. Typically, for a single unit, the upgrade can be delivered within a week, once the initial information has been collected. This ensures that the service life of pumps can be extended quickly while delivering improved reliability and performance.
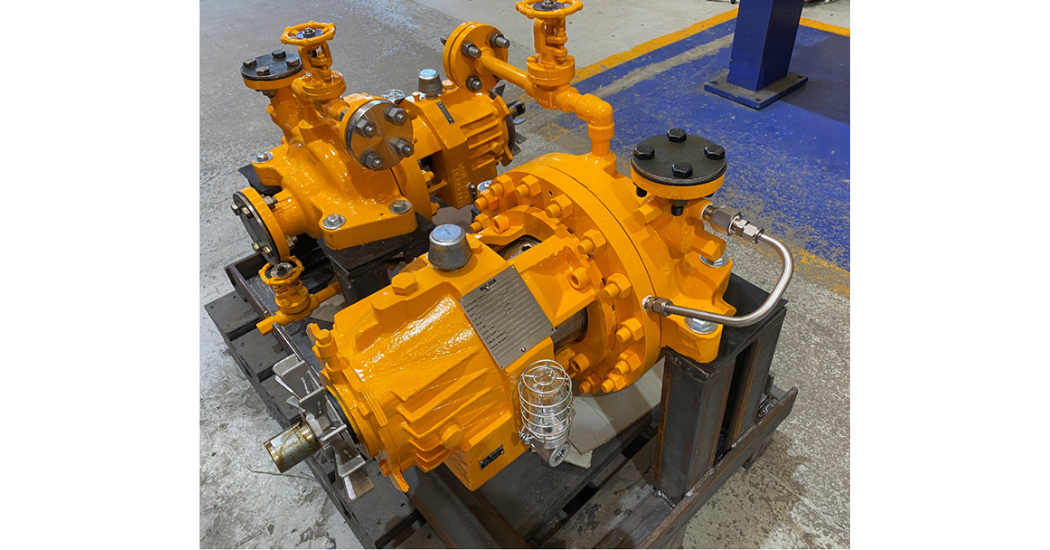
The retrofit kits have improved reliability and extended the service life of the pumps
About Sulzer
Sulzer is a global leader in fluid engineering. We specialize in pumping, agitation, mixing, separation and application technologies for fluids of all types. Our customers benefit from our commitment to innovation, performance and quality and from our responsive network of 180 world-class production facilities and service centers across the globe. Sulzer has been headquartered in Winterthur, Switzerland, since 1834. In 2020, our 15’000 employees delivered revenues of CHF 3.3 billion. Our shares are traded on the SIX Swiss Exchange (SIX: SUN). www.sulzer.com. The Pumps Equipment division specializes in pumping solutions specifically engineered for the processes of our customers. We provide pumps, agitators, compressors, grinders and screens developed through intensive research and development in fluid dynamics and advanced materials. We are a market leader in pumping solutions for water, oil and gas, power, chemicals and most industrial segments.
Throughout the Americas, Sulzer provides cutting-edge parts as well as maintenance and repair solutions for pumps, turbines, compressors, motors and generators. We service our own original equipment as well as third-party rotating equipment operated by our customers. Our technology-based solutions maximize reliability and lifecycle cost effectiveness.
For more information on Sulzer, visit www.sulzer.com