Contributor: Dorota Zoldosova, Head of Marketing and Communications, Sulzer Chemtech Ltd.
Innovative retrofit technology enhances existing upstream oil facilities
Upstream systems for oil separation effectively delivered regulatory-compliant dehydrated crude oil during the ’easy oil’ era. Now that oil and gas companies need to look beyond ’peak oil’, existing separators can still serve midstream and downstream facilities. This is made possible by state-of-the-art retrofits that boost separation efficiency and performance in this equipment.
Erik Bjørklund, Manager at Sulzer Chemtech in Asker, Norway, looks at how the latest innovation in demulsification technology can support existing upstream facilities.
During extraction operations, crude oil is found in the form of oil-water emulsions. These need to be processed using separators to remove most of the water in the earliest upstream processing stages. In this way, it is possible to meet quality standards and transport specifications, which generally require concentrations of water below 0.5% by volume. This activity is also key to avoid catalyst poisoning, corrosion of oil processing equipment in midstream and downstream activities as well as complications due to increased emulsion viscosity, caused by the presence of finely dispersed water droplets in crude oil.
The design of oil-water inlet separators for upstream demulsification has practically remained unchanged since its introduction in the 1930s. Only in the last decades, a different, advanced technology has emerged to improve the setup.
These pieces of equipment traditionally consist of large vessels that are able to remove free water from an oil feed via sedimentation processes. According to this method, the oil and liquid phases separate due to their different densities. More precisely, the water droplets, which are denser than oil, settle at the bottom of the continuous oil phase.
This is why conventional oil-water separators are also called gravity separators. The sedimentation process causes larger water droplets to separate first, due to their larger diameter, while the smaller droplets require longer settling times.
When gravity separation is not enough
If the composition of a crude oil feed makes the emulsion particularly stable or challenging to separate, it is difficult to sediment water. Thus, to successfully separate the liquids it is necessary for the feed to remain in the separator for a long residence time. This slowdown also results in low flow rates, causing a substantial performance bottleneck. This is the case, for example, when oil feeds contain asphaltene or acidic compounds, as these improve the oil-water emulsion stability. Similarly, oilfields reaching maturity deliver emulsions with higher volumes of water, which need to be fully removed.
Common solutions to address these issues include adding a number of separators in line, increasing the process temperature to promote separation or using chemical additives as demulsifying agents. All these solutions, however, result in higher operating costs (OPEX), environmental impacts and often substantial capital expenditures (CAPEX). In addition, they may have floorspace requirements that cannot be accommodated in existing upstream facilities.
A technology that is often used during the last steps of the upstream oil three-stage process train can actually be applied at an earlier stage to optimize gravity separator performance. As a result, facilities can benefit a cost-effective and efficient setup with no increase in the manufacturing footprint. This solution utilizes electrodes to leverage the physical phenomenon of electrostatic coalescence, or electrocoalescence, and destabilize the emulsion. The process causes the water droplets to merge, or coalesce, in the presence of an electric field. As larger droplets form, their settling time is reduced, even in presence of asphaltenes and other emulsifiers.
A winning design
An example of a unique electrostatic coalesce apparatus for upstream separators is Sulzer’s electrostatic coalescer internal for vessels (VIECTM). This consists of a number of coalescer modules, each one comprising electrodes and transformers that form a cross-sectional wall within the inlet separator. Once the oil-water emulsion passes through the structure, it is exposed to a destabilizing electrical field that forces the water droplets to merge.
When applied to the first stages of the separation process train, it is important for electrostatic coalescer internals to withstand any concentration of water or gas in the emulsion to ensure optimal process operations. In fact, as the separator may be fed with content that are 100% water or 100% gas, the electrode must not short out in these situations. Sulzer addressed this issue by using fully insulated electrodes that can continue to operate independently in the presence of gas or the volume of water.
The resulting modular setup of the VIEC is ideal for existing vessels, as it can be easily adapted to fit the separator’s diameter. A suitable cross-sectional coalescing wall can then be inserted through existing manways, ensuring a successful retrofit. In this way, facilities can enhance their separation efficiency and productivity without affecting the manufacturing footprint or running costs.
Sulzer’s in-house modelling and testing capabilities ensure that operators receive the optimal design for each specific application. Specialized engineering teams conduct concept and Front-End Engineering Design (FEED), laboratory-based batch and continuous flow-loop assessments. Once the ideal VIEC system has been delivered, Sulzer offers installation supervision, commissioning, start-up assistance and continuous life-cycle support.
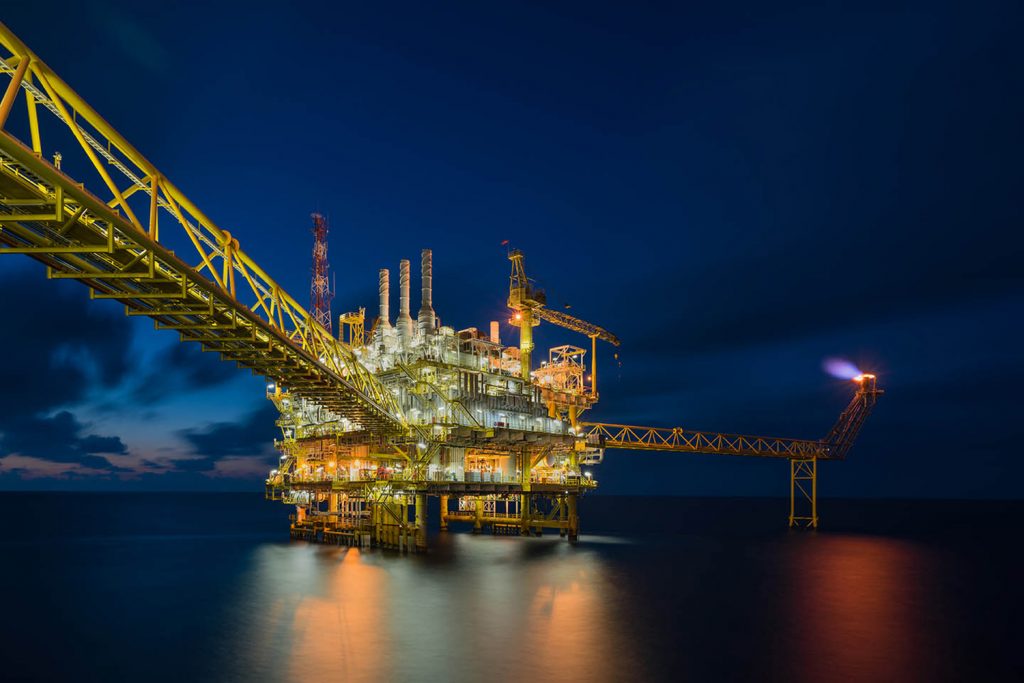
Sulzer’s electrostatic coalescer internal for vessels (VIEC™) can help upstream facilities improve productivity and separation efficiency of existing gravity separators without increasing their manufacturing footprint.
(Image Source: Shutterstock – Oil and Gas Photographer)
Case study: exploit challenging oilfields
The Shell Oil Company wanted to extract crude oil from Cardamom, a deep-water reservoir in the Gulf of Mexico. The company’s existing Auger offshore platform featured a legacy gravity separator that could not effectively process the oil-water emulsion from the newly developed tieback. In addition, Shell could not install new separators due to the lack of space on the platform. The company decided to retrofit Sulzer’s VIEC system within the separator to make its system suitable for operations in Cardamom. Thanks to this technology, Shell de-bottlenecked its processing capabilities, enhancing the separation efficiency and increasing the overall capacity.
Case study: optimize the separation process and reduce CAPEX
A global energy company wanted to optimize its oil-water separation process on one offshore platform. To achieve this, the business wanted to reduce the number of inlet separators while maintaining high crude oil quality. The installation of Sulzer’s VIEC system enabled a reduction in the overall footprint and saved over USD 5 million in CAPEX.
Case study: improve energy efficiency in heavy oil processing
In an offshore U.S-operated plant in Canada, the oil from one of the pools was found to be particularly heavy. Therefore, it would require a long settling time in the separators in order to remove water from the crude oil. Increasing the operating temperature to promote the demulsification process would result in higher costs and affect the system’s efficiency. Plant managers decided to install Sulzer’s VIEC system to address this issue. As a result, the offshore facility managed to enhance oil-water separation, increasing the produced oil quality, as well as reducing the process temperature from 90°C to 60°C, which led to substantial savings.
Conclusions
While competition in the oil and gas market is increasingly fierce and challenging, upstream facilities should not feel limited by their existing gravity separators. In fact, advanced coalescing technologies, such as the VIEC system, offer a unique opportunity to tackle challenging or mature oilfields. In addition, they can help businesses to increase their separation performance and efficiency while retaining their existing equipment.
By relying on skilled mass transfer and phase separation specialists, such as Sulzer, upstream facilities can benefit from expert support in designing electrostatic coalescer internals for inlet separators that seamlessly integrate with existing vessels. Even more, they can count on a unique system to boost operations as well as address their specific needs, quality and transportation requirements.
About Sulzer
Sulzer is a global leader in fluid engineering. We specialize in pumping, agitation, mixing, separation and application technologies for fluids of all types. Our customers benefit from our commitment to innovation, performance and quality and from our responsive network of 180 world-class manufacturing facilities and service centers across the globe. Sulzer has been headquartered in Winterthur, Switzerland, since 1834. In 2019, our 16’500 employees delivered revenues of CHF 3.7 billion. Our shares are traded on the SIX Swiss Exchange (SIX: SUN).
The Chemtech division is the global market leader in innovative mass transfer, static mixing and polymer solutions for petrochemicals, refining, LNG, biopolymers and biofuels. Our product offering ranges from process components to complete separation process plants, including licensing. Customer support covers engineering services and field services to tray and packing installation, tower maintenance, welding and plant turnaround projects.
Comments