Many factors can affect a mechanical seal’s reliability. Some of them are within a plant team’s control. They are:
- Correct application
- Design selection
- Precision installation
- Proper operation and environmental controls
Design Selection for Mechanical Seal Reliability
Three variables that most affect the design selection of mechanical seals are: equipment characteristics, application and operating conditions, and the leak rate objective.
Single or Multiple Mechanical Seal Arrangement
The first decision, however, rests in determining if one or multiple seals are required. This often has the potential for a devastating impact on overall performance and reliability.
One of the primary requirements when applying end-face seals on high-speed rotating equipment is ensuring sufficient and effective lubrication between the seal faces. Excessive rubbing friction between the rotating seal face and the stationary face must not occur. Friction can quickly wear and deteriorate the seal components, causing rapid and premature failure.
Mechanical seal reliability may depend on barrier fluid and the proper set up of environmental controls.
Relatively clean process fluids with adequate lubricating properties can be contained with a single-seal arrangement. These seals are typically less expensive to install and simpler for teams to operate and maintain. If a separate lubrication system is required, a double seal arrangement will be needed. This will help ensure mechanical seal reliability.
Application: Speed, Pressure, and Shaft Movement
The design must operate at fluctuating peripheral speeds and pressure. Complex equipment conditions, such as axial and radial shaft movement exceeding allowable tolerances, must also be included in the evaluation.
Leakage Rate
The amount of leakage to atmosphere, which is dictated by the plant’s leak rate objectives and/or regulatory requirements, must be controlled by the seal design chosen. All end-face mechanical seals operating effectively on high-speed applications allow a small amount of vapor to pass through the primary seal interface. Average leakage will be in the 1-cc-per-day range, which is within acceptable tolerances of most process fluids.
However, allowable leakage rates to atmosphere of hazardous or toxic process fluids are regulated and mandated by government agencies, such as the Occupational Safety and Health Administration and the Environmental Protection Agency.
Ultimately, safe sealing can only be met by specific configurations and designs that minimize or eliminate leakage rates to the required tolerances.
What Applications Are Best Suited for Mechanical Seals?
Rotating equipment is the primary application in which end-face mechanical seals can be cost effectively considered and applied. This equipment is used in processing gases, liquids, and slurries.
Component Seals
Some types of rotating equipment are not equipped with a seal chamber or stuffing box for installing a gland. These will require a component seal.
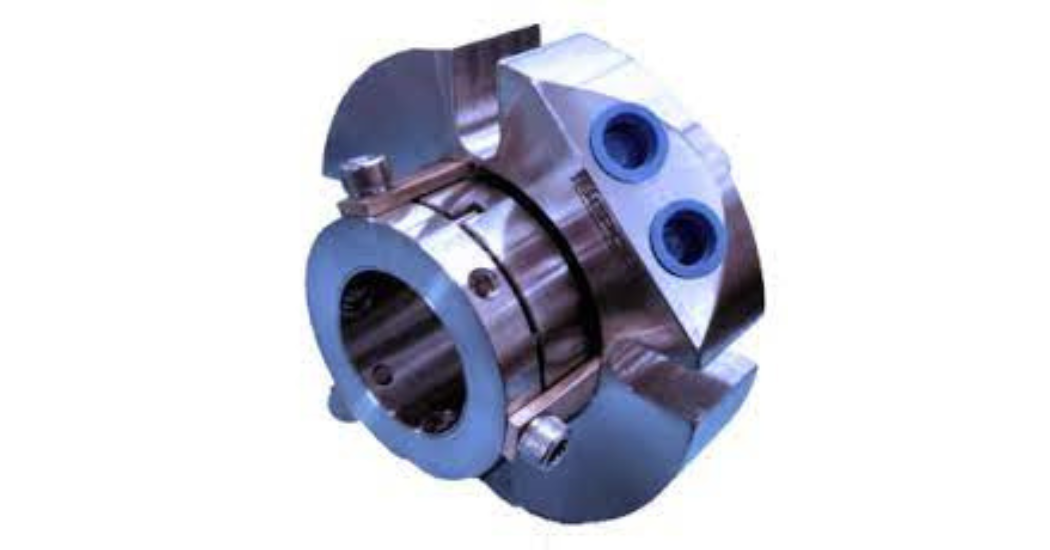
Example of a cartridge seal
Cartridge Seals
Cartridge-mounted, end-face seals were primarily introduced for installation on American National Standards Institute centrifugal pumps for making axial shaft adjustments. Their simplicity and ease of installation and maintenance makes cartridge-mounted single and dual units a strong choice for rotating equipment with a stuffing box or seal chamber in which a gland can be installed.
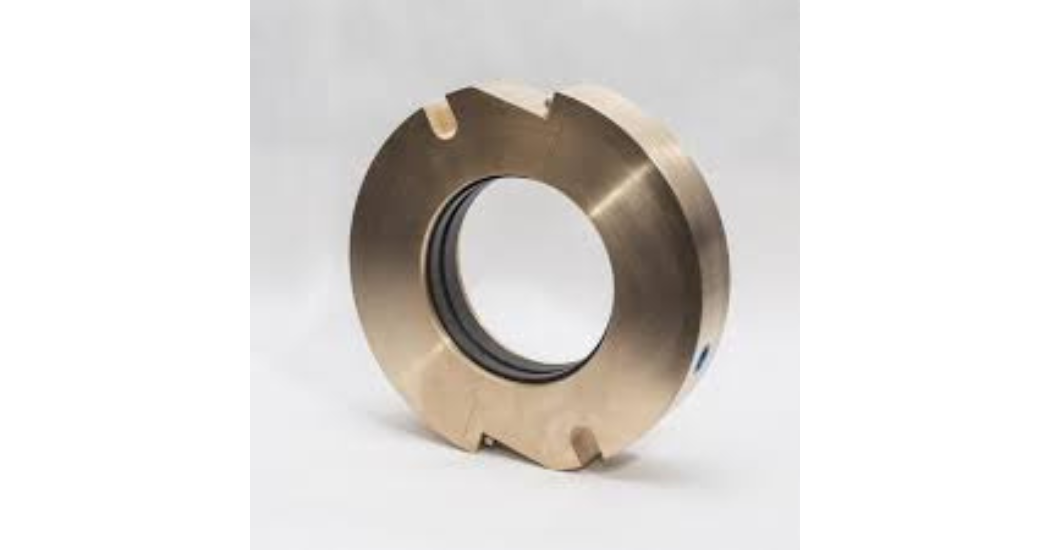
Air seals are well-suited for powder and slurry applications.
Air Seals
Air seals are well-suited for powder and slurry applications. Air seals use a knife of air to seal the process instead of seal faces. They are primarily installed on rotating equipment used to move or mix powders, bulk solids, or heavy slurries.
Application, Installation, and Operation: Critical for Mechanical Seal Reliability
The reliability of an end-face mechanical seal depends on three factors — application, installation, and operation.
Design Selection for the Application
One factor stands out as the primary cause of premature seal failure — application. This involves defining the conditions inside the seal chamber, which dictate how long and how well the seal performs. Once these conditions are known, the best seal design for the conditions should be selected.
Extending the life of end-face mechanical seals primarily depends on clean and cool operation, which is directly affected by the application.
Every application, process fluid, and change in the environment adds a new and often unconsidered mix of consequences, which is why the application has such a tremendous impact on seal reliability.
Precision Installation
Once the seal design best for the application is selected, precision installation follows. Many seal failures occur because the personnel incorrectly installed the seal. If installing a component seal, an experienced technician should be the installer. Cartridge seals are simpler to install, but errors still occur. Follow the manufacturer’s instructions carefully. If external barrier fluid will be used, ensure that the environmental controls are set up correctly. Correct setup allows for the proper pressure of the barrier fluid into the stuffing box and adequate cooling of the fluid.
Many steps are required to carry out precision installation. The major steps for most cartridge mechanical seals are:
- Preinstallation check list (including equipment inspection and cleaning)
- Shaft and sleeve inspections to ensure that no deep scratches, sharp edges, or burrs are on the equipment
- Inspect and empty the stuffing box, correcting any holes, burrs, or sharp edges and ensuring that adequate space is available to adequately fit the seal assembly
- Ensure proper alignment of the shaft
- Install the seal assembly by positioning the seal over the shaft and sliding the unit back to the bearing housing or nearest obstruction; a slight twisting motion will help compress the O-ring over the end of the shaft/sleeve

A team works in a wastewater treatment facility
Ideal Operation and Operating Environment Are Key to Optimal Mechanical Seal Performance
Defining how a mechanical seal will be used and its environment is critical for optimal operation and life. Often, seal environmental controls are over looked, resulting in shorter seal life. Even with the ideal design and precision installation, problems may arise. Any hostile operating conditions or changes in the process parameters can override the capabilities of the design and materials, thereby reducing reliability. To obtain optimal seal life, the seal should be operated and maintained as designed.
One example can be found in wastewater treatment plants where raw sewage must be moved with high-speed centrifugal pumps. These water-based solutions are entrained with solids that can hang up the seal and quickly erode the selected materials if the slurry migrates between the faces.
Flush water from an external source is a common solution for preventing premature failure. It floods the seal cavity with a clean, cool water. This flush must be maintained at a higher pressure than the wastewater because it provides a clean, cool environment that is essential for safeguarding the life of the mechanical seal. These single-seal systems operating properly will increase water consumption and will also dilute the pumped product.
In some facilities, water consumption may be a primary concern or process dilution cannot be tolerated. For these situations, a dual-seal system operating with an independent, clean-liquid flush will be required.
Other environmental factors, such as temperature and pressure, must also be carefully controlled to prevent leakage. Careful attention should be given to the environmental control systems specified for sealing hazardous or toxic fluids. They must meet the allowable leakage tolerances for the fluid being sealed and prevent excessive leakage in case a seal fails.
How Mechanical Seals Can Improve Equipment Optimization
Poor equipment conditions caused by factors such as failing bearings, cavitation, excessive impeller loads, and misaligned shafts typically result in many problems including:
- Excessive motion
- Vibration
- Heat
- Mechanical shock to the mechanical seal
Additionally, these conditions cause greater stresses, more heat, and more opportunity for abrasives to enter the sealing system.
While mechanical seals are designed to handle a range of motions and conditions, they are just one machinery component in a larger system. Understanding the basics of mechanical seals and how they may be adapted for different application requirements is critical when choosing the best seal for the application and ensuring optimal overall system reliability.
Mechanical Seal Failure
Mechanical seals prevent pumps from leaking by containing the pressure of the pumping process. They withstand the friction caused by the pump shaft rotating. This results in less wasted product, more cost savings, and less clean up.
In many pump systems, a mechanical seal is the first component to fail, but why? Learn more in the article “Why Do Mechanical Seals Fail?“
About the Author
Thomas (Tommy) Seales is the Mechanical Seal Division Product Manager for Sealing Equipment Products Company (SEPCO). He is primarily responsible for managing the engineering department and overseeing new product development. His responsibilities also include providing any and all domestic and international technical support for the distributor and outside salesforce for SEPCO. Seales has worked at SEPCO for more than 42 years and has been the product manager of the mechanical seal division for 35 years. He is an honorary lifetime member of the United Who’s Who Registry of Executives and Professionals. Seales may be reached at tommys@sepco.com.
Comments