A drywall facility experienced equipment failures, bearing problems, and major housekeeping issues before a new installation.
Gypsum is a soft mineral used in fertilizer, drywall, plaster, and blackboard or sidewalk chalk. It causes a mess in the facilities that process it. A drywall facility had a problem with gypsum leaking out of a screw conveyor. The team sought a new solution to eliminate the mess.
The Problem
The drywall facility’s screw conveyor used compression packing rings to seal the conveyor’s shaft. Compression packing can be effective in many applications. However, when dry powders are being sealed, the packing is easily contaminated. This causes packing wear, excess product leakage, and shaft wear.
The leaking powdered gypsum created a major housekeeping issue for the plant (see Image 1). It also cost money because of:
• Wasted product
• Compression packing replacements, which were needed every couple months, but the facility did not always have the personnel to perform the replacements
• Repeat bearing failures because gypsum contaminated the lubricant
In addition to leakage on the floor and onto other equipment in the facility, gypsum can become a safety issue. It is very light and can blow/float along the air. While it is nontoxic, gypsum irritates the skin and mucous membranes of personnel and its leakage should be minimized.
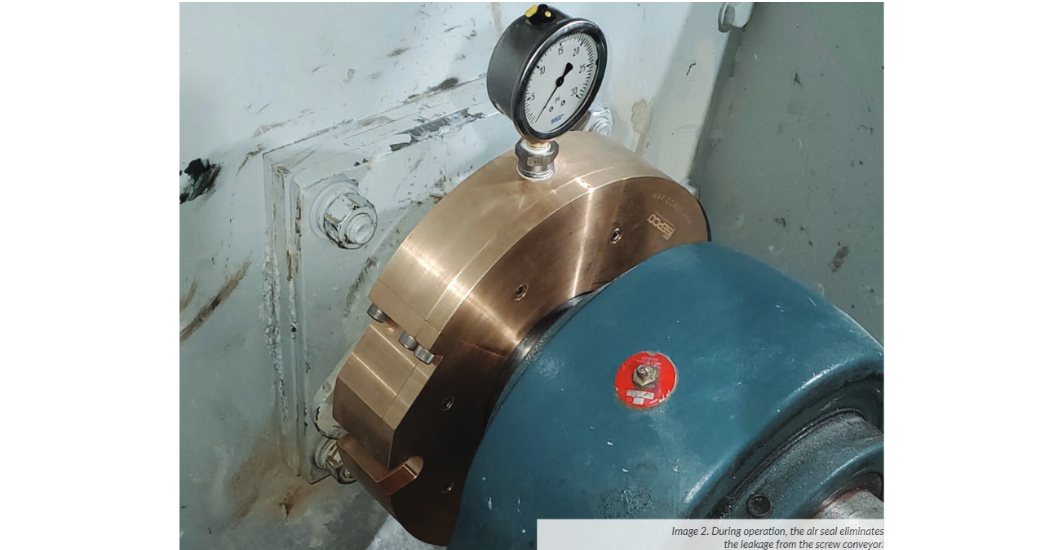
Image 2. During operation, the air seal eliminates the leakage from the screw conveyor.
The Solution
The team decided to take a chance on a newer technology, an SAS Air Seal. The noncontact air seal was the ideal solution. Air seals use engineered clearances and directional flow paths to create uniform pressure and velocity profiles, generating a pneumatic seal.
To accommodate the inherent misalignment that may be present in many applications, a floating throttle inside the seal handles ±0.125 inch of parallel movement.
By controlling the internal pressure or flow profile, a circumferential boundary layer of air is formed between the throttle and the shaft/sleeve. This boundary mitigates any damage that would occur because of mechanical runout because the throttle floats on the boundary layer. It never touches the shaft.
In March 2020, the drywall producer installed the air seal on the screw conveyor. Nearly two years since the installation, the seal has experienced zero leakage. This is an improvement of meantime between replacement from every two months to more than 22 months.
The air seal eliminated the screw conveyor’s problems. The plant saved money; decreased personnel time on maintenance, housekeeping, and packing replacements; reduced bearing failures; and eliminated product waste.
Terry Roberts is the Midwest regional manager for Sealing Equipment Products Company (SEPCO). He has worked in the fluid sealing industry for more than 23 years. In his role with SEPCO, he provides training, sales support and solutions to channel partners and their customers. Roberts is also on the technical committee of the International Sealing Distribution Association (ISD). He may be reached at terryr@sepco.com
Comments