What do Pump Pros Know and why do they know it? This series of articles highlights the brilliance of those who work with pumps. Read more Pump Pros Know.
Pumps stand as the mechanical workhorses driving fluid movement in a multitude of applications, from industrial processes to commercial water systems. At the core of these machines lies a crucial aspect often overlooked but vital for their optimal operation: radial thrust. This force, stemming from the unbalanced forces within the pump’s components, significantly impacts the pump’s performance and longevity. Understanding the intricate dynamics of radial thrust is essential for engineers, maintenance personnel, and anyone involved in the design, operation, or maintenance of pumping systems.
Radial thrust, characterized by its perpendicular action to the axis of rotation within the pump’s casing, collector, or diffuser, is influenced by a confluence of factors (Figure 1). The impeller’s design, outside diameter (D2), width (b2), configuration, and the type of discharge collector all contribute to the behavior of radial thrust (Figures 2). The magnitude and direction of this force undergo fluctuations across the pump’s operational range, making it a pivotal consideration in the engineering and maintenance of these systems.
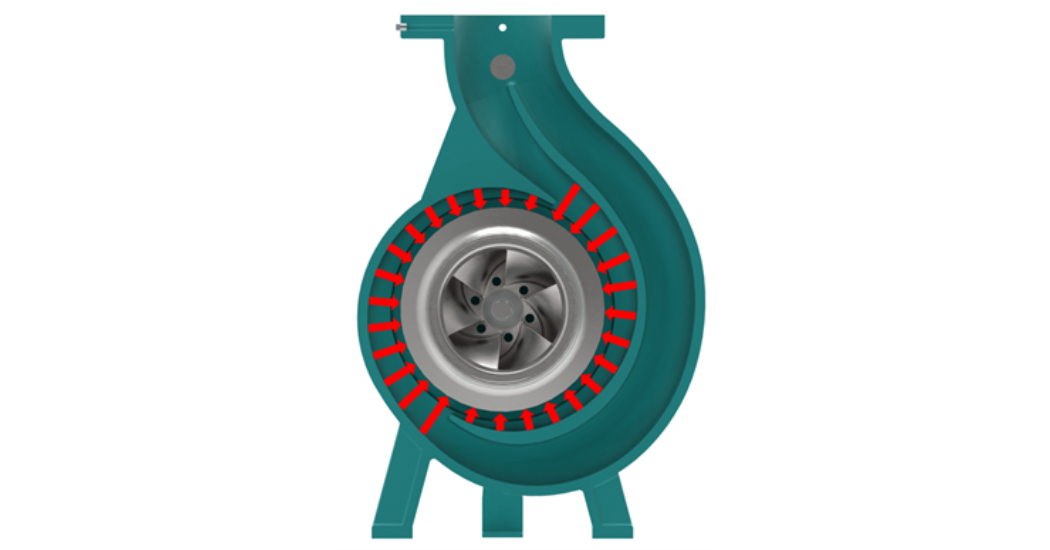
Figure 1: Hydraulic Radial Forces in a Double Volute Casing
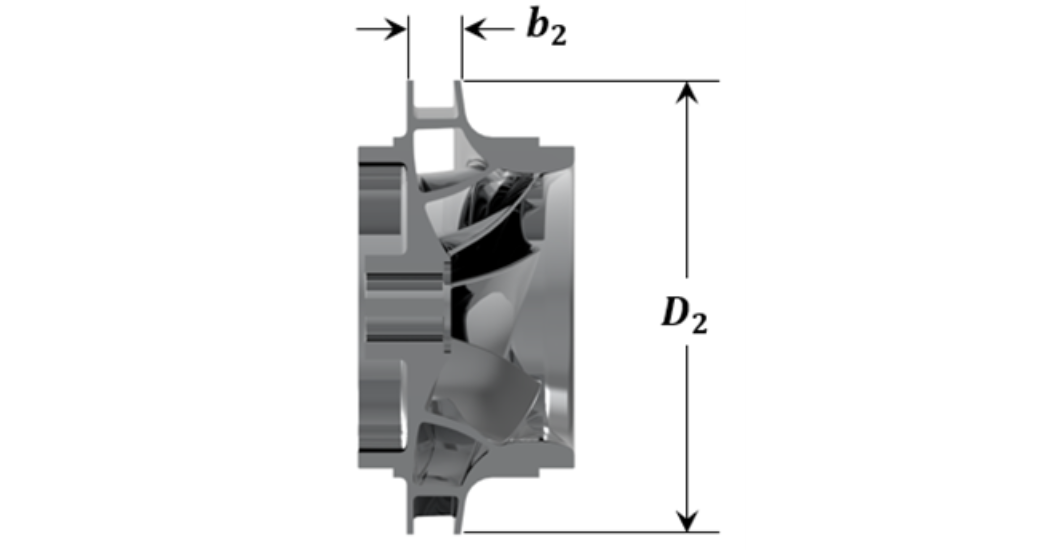
Figure 2: Radial Impeller Outside Diameter (D2) and Impeller Width (b2)
One of the key determinants of radial thrust is the flow rate. The Best Efficiency Point (BEP), the flowrate where the pump operates at optimal efficiency, typically experiences the lowest radial thrust. Figure 3 shows the radial thrust factor for a single volute casing, and you can see that as flow rates deviate from BEP, radial thrust increases, exerting varying pressures on the impeller and surrounding components. Operation at reduced capacities significantly below BEP amplifies these forces, leading to increased shaft stresses, potential bearing problems, and heightened vibrations.
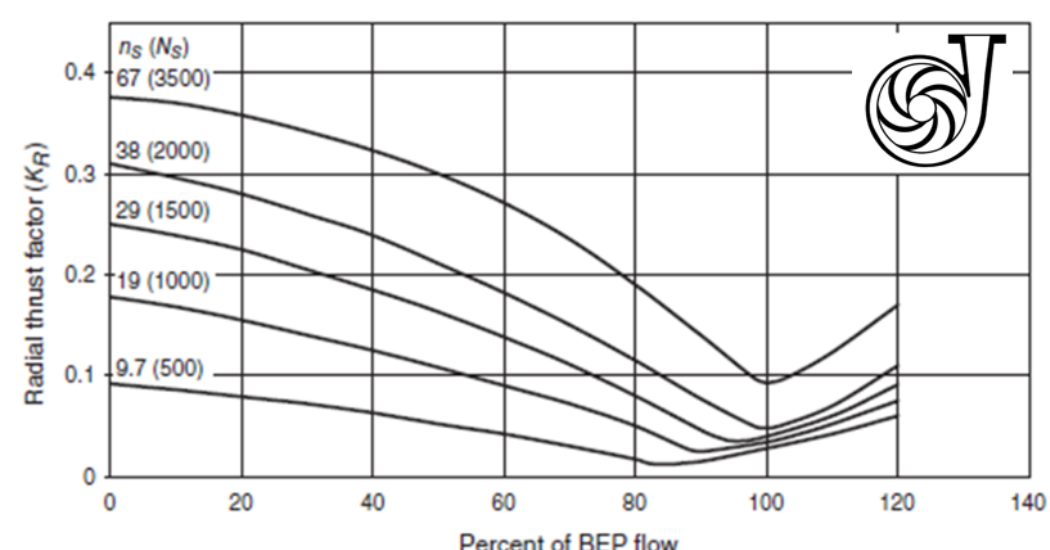
Figure 3: Radial thrust factor for single volute with various specific speeds
Operating pumps at extremes, such as shut-off conditions or beyond the allowable operating region (AOR), poses additional challenges. Operation outside the AOR not only elevates radial thrust but could also induce overheating of the fluid within the pump. Mitigating strategies, such as employing recirculation piping or variable-speed controllers, can help alleviate these effects, extending the pump’s life as recommended by pump manufacturers.
The design intricacies of pumps play a significant role in managing radial thrust. For instance, the configuration of discharge collectors—whether single volute, double volute, or concentric casing—significantly influences the distribution of pressure and subsequently the radial force on the impeller (Figure 4). Single volutes typically exhibit the highest radial thrust at zero flow, while double volute or concentric casings tend to reduce this load across the operating range. Additionally, different casing designs, such as annular casings or modified concentric casings, each present unique characteristics influencing radial thrust.
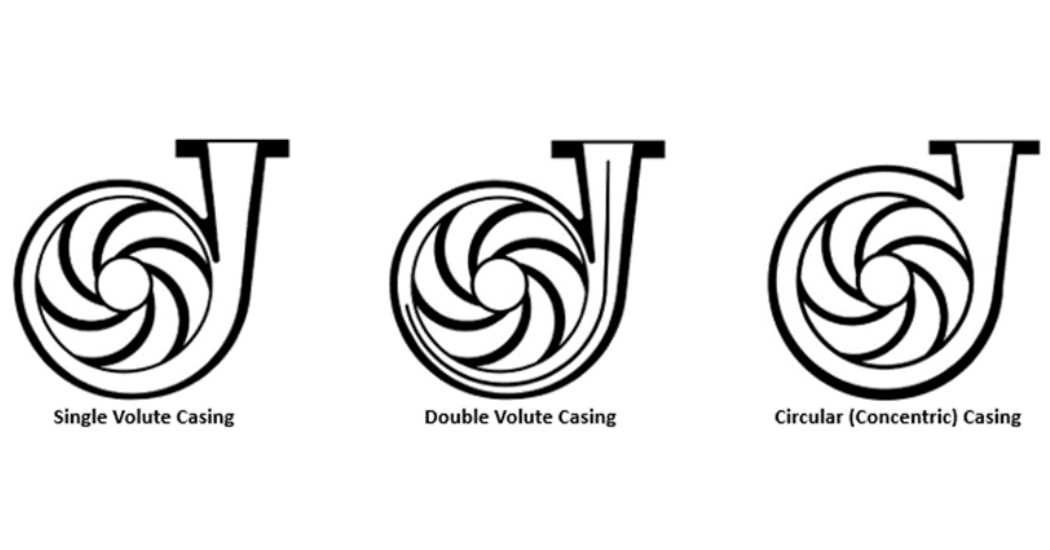
Figure 4: Discharge Collectors (Single Volute, Double Volute, and Concentric Casing)
Furthermore, the relationship between impeller diameter, speed, and the resultant thrust unveils more complexities. Changes in impeller outside diameter or pump speed directly impact radial thrust, albeit in different proportions—impeller diameter changes affecting thrust to the third power, while speed alterations affect it to the second power.
The intricacies of vertical pumps, especially vertically suspended vertical turbine pumps, present distinct considerations. Their multivane bowl diffusers tend to equalize pressure forces, keeping radial thrust notably low. However, factors like erosion, corrosion, or mechanical imbalances can lead to the development of radial rotor thrust forces over time.
Vertical pump installations introduce a different dimension to radial thrust concerns. The ideal plumb suspension minimizes lateral forces on the rotor, but any deviation from this vertical alignment, due to mounting or operational factors, can lead to increased radial thrust, potentially impacting the pump’s components and longevity.
In essence, the understanding and management of radial thrust in pumps involve a delicate interplay between design, operating conditions, and inherent system dynamics. Mitigating excessive radial thrust demands a comprehensive approach, considering the design specifics, operational nuances, and recommended practices by pump manufacturers.
The effect of high radial thrust might also play a role in additional factors such as increased shaft deflection, premature wear and failure of the radial bearings, higher shaft stresses, potential mechanical seal problems, increased radial vibration, and potential pump failure if continuous operation occurs.
Typical mitigation strategies to high radial thrust include changing the discharge collector style (i.e., from a single volute to a double (dual) volute), trimming impellers to meet design conditions, limiting the AOR to a percentage of the BEP that provides adequate bearing life and limited shaft deflection, designing pumps with a limited impeller width, and changing the pump type.
The comprehensive understanding of radial thrust provides a foundational basis for efficient and prolonged pump operation, emphasizing the significance of design considerations and operational best practices. Balancing these aspects ensures the longevity and optimal performance of pumps across diverse applications, securing their crucial role in various industries.
To learn about radial thrust, please refer to ANSI/HI 14.3-2019 Rotodynamic Pumps for Design and Application.
Comments