What do Pump Pros Know and why do they know it? This series of articles highlights the brilliance of those who work with pumps. Read more Pump Pros Know.
Water hammer, a potentially destructive force within pumping systems, poses a significant threat to system equipment and piping. Understanding the intricacies, impact on pump systems, and effective mitigation strategies is crucial for ensuring optimal operation, longevity, and reliability.
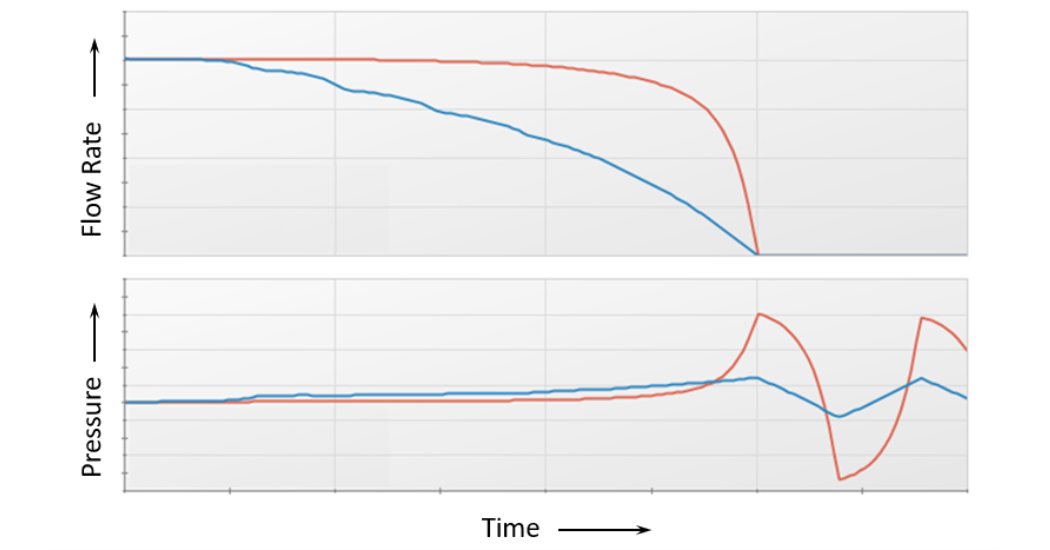
Figure 1: Pressure spikes arising from differential valve closure rates: gradual versus rapid
Hydraulic transients, also known as surge or water hammer, occur when a column of liquid undergoes a sudden change in velocity, which results in transient pressure spikes that go above and below the average system pressure (Figure 1). This transient pressure can result in damage to the pump, the system, and associated components (Figure 2). The magnitude of water hammer depends on factors such as the rate of change of velocity, pipe size, length, and the velocity of the pressure wave along the pipe. It is important to note that observing a point of failure may not indicate the actual cause, as different materials in the system can react differently based on their properties.
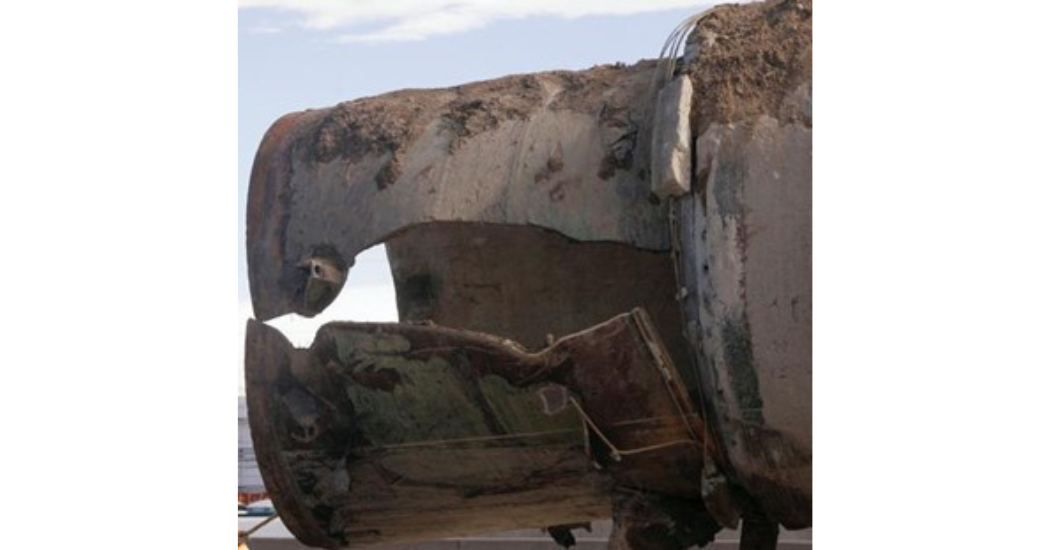
Figure 2: Burst pipe due to water hammer
The pressure transients can surpass the pressure rating of pump casings, valves, and associated components, posing a risk of long-term failure. Different materials within the system may react differently to water hammer – brittle materials like cast iron may be more prone to cracking due to the pressure overload, while ductile materials may suffer permanent deformation without cracking. Strengthening the pump casing, system piping and other pressure contain components is generally not a cost-effective method of preventing failures due to water hammer.
One of the simplest yet effective strategies for water hammer mitigation is to properly manage the startup and shutdown of a pumping system. For example, gradual opening or closing of the discharge valve, or extending the acceleration and deceleration of the pump motor during pump startup or shutdown, can effectively manage the velocity change and transient pressure waves. This approach minimizes sudden changes in velocity, reducing the risk of water hammer pressure spikes, especially crucial in installations with long discharge piping.
In complex installations, mathematical system analysis may be necessary to accurately assess the severity of water hammer. Specialized engineering services are recommended for precise calculations, involving a comprehensive evaluation of influencing factors, including hydraulic pump characteristics, pipe layout, and fluid properties. Engineers can tailor mitigation strategies to specific installations by understanding the system dynamics.
Controlling the closure time of valves, especially fast-closing valves like check valves (Figure 3), is a critical aspect of water hammer mitigation. Modeling may be required to determine the effects of valve closure characteristics on the pump and system. Factors such as valve type, liquid velocity, pipe material properties, and system configuration must be considered to optimize valve closure and minimize water hammer effects.
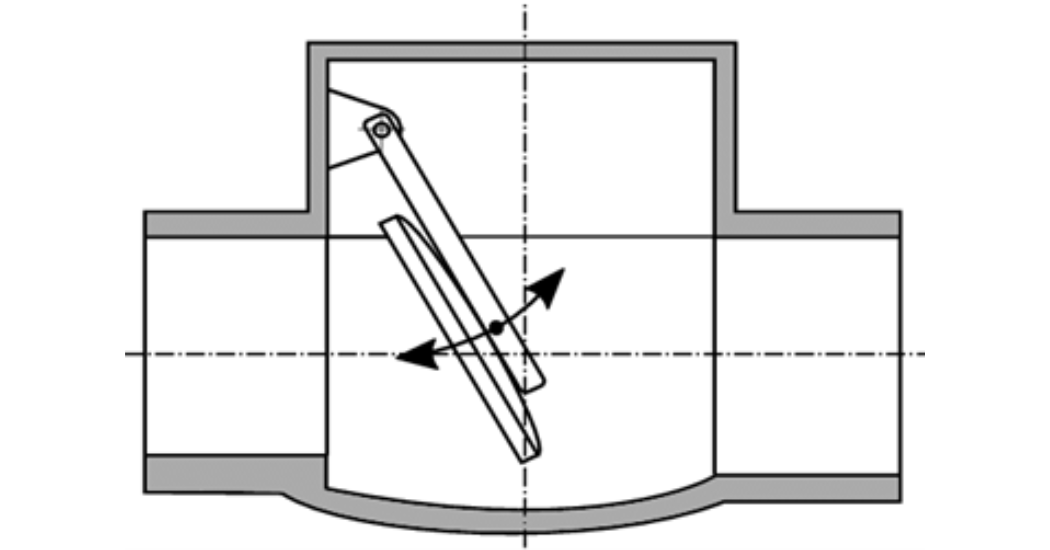
Figure 3: Swing Check Valve
In certain applications, providing additional rotating inertia to a pump can slow its rate of deceleration when power is cut off (Figure 4). This allows more time for flow-control devices to mitigate water hammer effects, reducing the risk of damaging backflow through the pump and water hammer effects on the system.
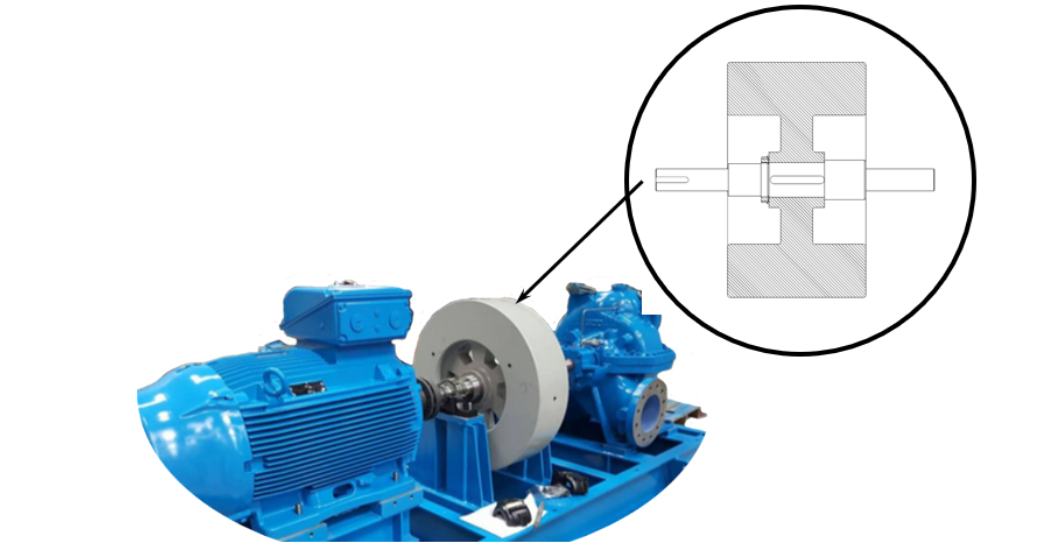
Figure 4: Flywheel between the pump and motor
In certain situations, it is essential to install an air-vacuum release valve to expel air from the piping and will affect the transient pressure dynamics (Figure 5). Additionally, strategically placing check valves in the drop pipe can minimize the formation of a vacuum, further reducing the risk of water hammer.
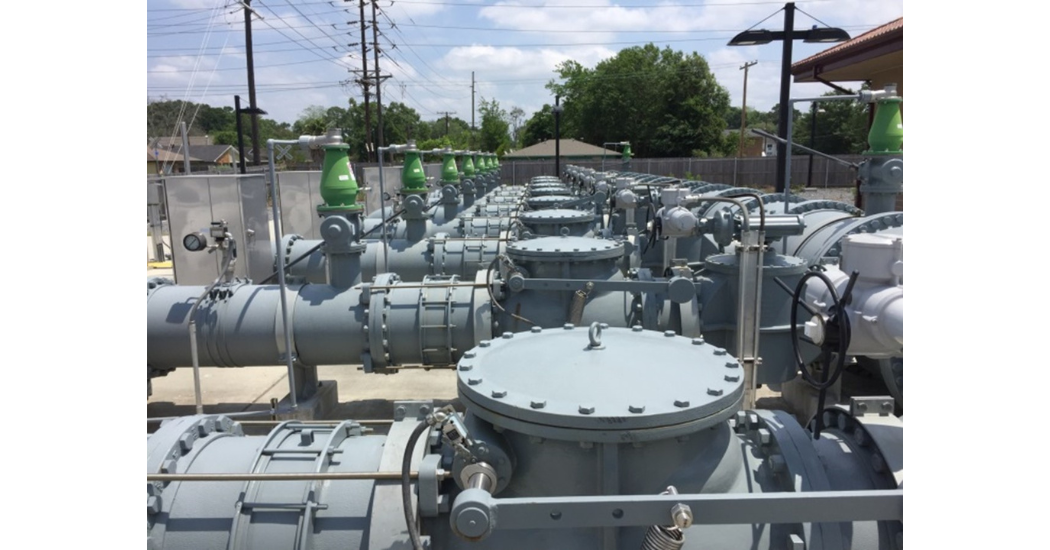
Figure 5: Air-vacuum release valve (in green, to the left) located on the pump discharge piping
Accurately calculating water hammer magnitude involves considering various factors such as pipe configuration, size, material, fluid properties, and pump or fluid acceleration/deceleration. While equations like the Instantaneous Water Hammer or Joukowsky equation provide quick estimations, they have limitations. For precise evaluations, especially in complex systems, it is advisable to use more robust methods.
Effectively controlling water hammer involves implementing proper valve closure rates, using slow-closing valves, incorporating diaphragm tanks to absorb pressure surges, and adding relief valves to release excess pressure. Careful modeling and analysis are essential to verify the effectiveness of proposed solutions in reducing water hammer pressures. In essence, limiting water hammer in pump systems requires a delicate interplay between design, operating conditions, inherent system dynamics, and following recommended practices by pump manufacturers. For a deeper dive into water hammer and its mitigation strategies, referring to industry standards such as ANSI/HI 9.6.6 Rotodynamic Pumps for Pump Piping and consulting with experienced engineers is highly recommended. By recognizing water hammer, professionals can contribute to the reliability and efficiency of fluid movement in various industries.
Comments