Contributor: Sebastien Brosse, PSG®
It’s said that looks can be deceiving, but when it comes to considering the appearance of peristaltic (hose) pumps, that is definitely not the case. The pump’s heavy-duty construction coupled with the indestructible look of its hoses and the shoes that are affixed to the pump rotors give the pump the look of a machine that is capable of handling anything that is thrown at it or, more precisely, passes through it.
And the operators in some of the world’s most demanding industries – from oil-and-gas production to mining and water/wastewater management to chemical processing – have come to rely on peristaltic (hose) pump technology when handling thin to viscous, particle-laden, aggressive, abrasive and corrosive liquids in potentially explosive atmospheres is required. In other words, peristaltic (hose) pumps can successfully pump just about anything.
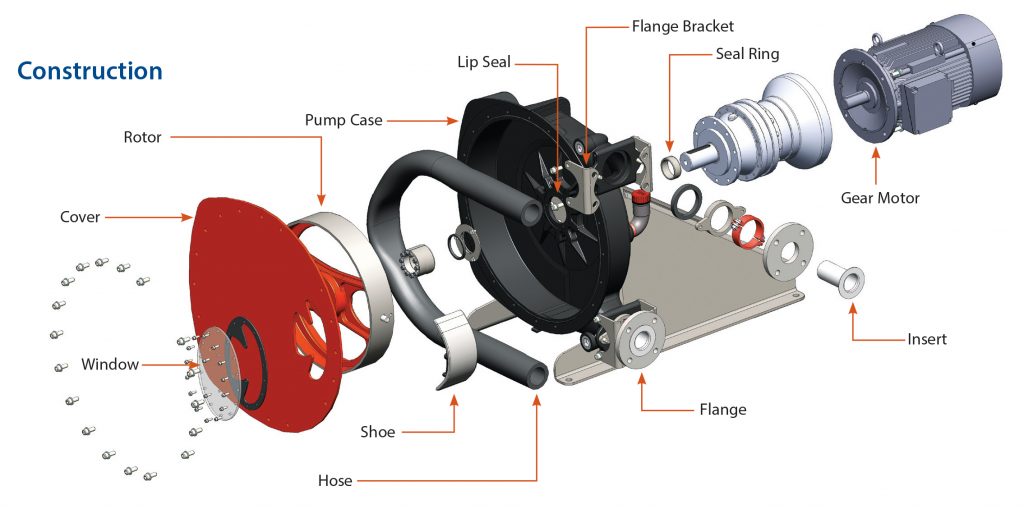
Abaque Construction: The simple, seal-free design and construction of peristaltic (hose) pumps makes them dry-run, self-priming and low-slip capable while eliminating the chance that any leak paths will form of cross-contamination points created. These are critical considerations in oil-and-gas liquid-transfer applications.
The Peristaltic Principle
The design and operation of peristaltic (hose) pump technology, which was patented in 1925 in France, satisfy the requirements of such a wide range of industrial liquid-handling applications because the pump’s operation relies on the alternating contraction and relaxation of the hose, which force the contents to move through the pump and into the discharge piping.
A smooth-wall, flexible hose is fitted in the pump casing and is squeezed between shoes on the rotor that is positioned inside the pump casing. This rotating action moves the product through the hose at a constant rate of displacement. The hose restitution after the squeeze also produces a strong vacuum effect that draws product into the hose from the intake piping. The vacuum that is created by the hose’s restitution can build discharge pressures of as much as 16 bar (232 psi) without damaging or deforming the hose, or causing it to rupture.
The pump casing is also lubricated to cool the pump and lengthen the service life of the shoes and hose. Since the product only contacts the hose and inserts, and not the internal pump components, this pumping technology is very suitable for abrasive and corrosive applications. The pump’s reversible operation also allows for pumping in both directions.
This pump style also maintains excellent volumetric consistency, making it ideal for the strict dosing and 24/7 operating cycles that can be required in many industrial applications while typically providing suction-lift capabilities of as much as 9 meters (29.5 feet). Peristaltic (hose) pumps are also easy to operate and easy to maintain with no seats, valves, glands or mechanical seals needed, which leaves the hose as the pump’s only replacement part.
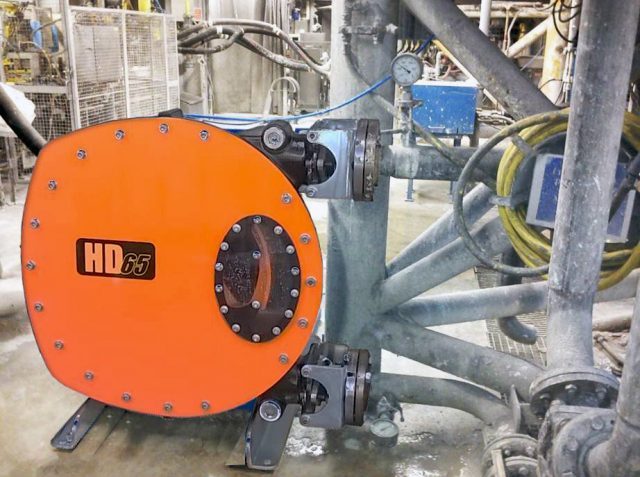
Abaque HD65 0001:
The peristaltic (hose) pump’s ability to maintain excellent volumetric consistency and provide suction lift up to 9 meters (29.5 feet) makes it ideal for the 24/7 operating cycles that are common in oil-and-gas production.
A critical advantage to peristaltic (hose) pump operation is its seal-free design that makes it dry-run, self-priming and low-slip capable. This design also eliminates the chance that any leak paths will form or cross-contamination points will be created.
The peristaltic pump’s hose and inserts – which, because of the pump’s seal-less design, are the only components to actually come into contact with the pumped medium – need to achieve the highest level of material compatibility, while also being able to reliably deliver the millions of pumping cycles that are required during its lifetime. That’s why peristaltic (hose) pump manufacturers have taken great pains to work with hose suppliers who can offer products that are compatible with a wide array of chemical compositions, knowing that leaking acid, or some other potentially harmful or dangerous liquid, will be a disaster for the operator.
Another consideration when selecting a hose material is its “fatigue resistance.” This trait defines how resistant to failure the hose material is as it runs through its millions of pumping cycles. A hose material that is susceptible to developing cracks and holes early in its operational life is not as desirable as a material that can reliably handle the demands of the repeated contraction and relaxation of the hose, especially when particulate-laden liquids are being pumped.
The reinforced construction of the peristaltic hose and its use of rubber compositions that have been specially designed for the stresses within the peristaltic hose allow for the optimum life cycle and performance. The following materials have gained wide acceptance for use in the construction of peristaltic pump hoses:
- Natural rubber (NR): highly resistant to abrasion
- Natural rubber ATEX: for applications in explosive-atmosphere areas
- Buna-N (NBR): provides wear resistance when used with oily liquids
- Buna-N FDA: for hygienic applications
- NR FDA 1935/2004: for food-grade applications
- EPDM (ethylene propylene diene monomer) rubber: optimized chemical resistance when handling concentrated acids, alcohols and ketones
- EPDM ATEX: for EPDM applications in explosive atmospheres
- Hypalon®: high resistance to oxidants, concentrated bases and acids
Oil’s Well That Ends Well
The peristaltic (hose) pump’s construction, method of operation, liquid-handling range and low maintenance requirements make it ideal for use in harsh operating atmospheres. One of the harshest – and most complex – is oil-and-gas production. The operations are usually located in some of the world’s most rugged, unforgiving and trying climates and landscapes. Within each operation, numerous liquid-handling functions need to be completed reliably and flawlessly in order for the production operation to be fully optimized.
The bottom line is that everywhere oil-and-gas products are being recovered from the Earth’s core is the result of a massive, complicated undertaking that requires extremely large amounts of fuel and other liquids to keep them running effectively and efficiently.
An example that is common to today’s oil-and-gas production universe is the hydraulic-fracturing process that is being used to produce much of the shale oil and natural gas that is found in the United States and Canada. The “fracking” process requires thousands and thousands of gallons of water to be sent down the wellbore. This water delivers the chemicals and frac sand that open up the reservoir and allow the trapped oil and natural gas to flow to the wellhead on the surface.
Once the fracked oil and gas is collected, the water that was sent down the well – which can contain a large amount of particulates and contaminants – must also be delivered to the well’s surface and either disposed of or recycled for further use. Also, when the actual oil and natural gas rushes to the wellhead, it can feature varying liquid viscosities and particulate levels, depending on the geologic makeup of the well.
So, the oilfield operator requires a pump that can do three things: handle the pressures that are required to complete the pumping operation; handle large volumes of liquids with varying viscosities and particulate levels; and maintain volumetric consistency while producing flow rates that can be as high as thousands of liters per minute.
For many years, internal gear and lobe-style pumps have been a common technology choice in various oilfield fluid-handling applications because they had proven to be capable of handling basic liquid-transfer operations. However, both styles feature mechanical shortcomings that can ultimately compromise a liquid-transfer operation’s efficiency, reliability, safety and cost-effectiveness over time.
Specifically, the constant wear of gear pumps adversely affects the pump’s flow capacity and volumetric consistency, resulting in energy-robbing product “slip.” Any abrasives that may be contained in the liquid will also harm a gear pump’s internals and compromise performance. Similarly, lobe pumps also wear constantly, resulting in an overall decrease in the pump’s efficiency and a corresponding increase in its cost of operation due to the higher speeds needed to deliver desired flow rates.
As highlighted previously, these are not concerns that affect the operation of peristaltic (hose) pumps.
Conclusion
When looking for a pump technology that checks all of the operational and compatibility boxes that contribute to an effective oilfield production system, peristaltic (hose) pumps can prove to be a first-choice technology. The pump’s design, construction and operation make it ideal for many of the unique – and harsh – liquid-handling applications that help define success in the world’s oilfields.
About the Author:
Sebastien Brosse is the Abaque® Team Leader for PSG®, a Dover company and can be reached at sebastien.brosse@psgdover.com or +33 386 498 699. Abaque is a leading brand of peristaltic (hose) pumps and a product brand of PSG. Abaque pumps are manufactured in the PSG facility in Auxerre, France, and supported in the Americas by its facility in Grand Terrace, CA, USA. Headquartered in Oakbrook Terrace, IL, USA, PSG, a Dover company, is comprised of several leading pump brands, including Abaque®, All-Flo, Almatec®, Blackmer®, Ebsray®, EnviroGear®, Griswold®, Mouvex®, Neptune™, Quattroflow™, RedScrew™ and Wilden®. For more information on Abaque or PSG, please go to abaque.com or psgdover.com.