Breakdown maintenance is an approach to maintenance strategy in which repairs are performed on equipment only after it has completely failed or broken down. The ultimate goal of breakdown maintenance is to restore the equipment to its normal operating condition as quickly as possible. That ensures production can resume, while minimizing resources for proactive maintenance on low-risk/criticality assets.
That being said, an entirely reactive approach to maintenance can be costly and often leads to further downstream problems. Effective planning is critical for executing breakdown maintenance, as it enables organizations to proactively identify potential issues, allocate necessary resources in advance, and minimize the likelihood of extended unplanned downtime.
This article will explore the importance of planning for breakdown maintenance and provide a few actionable strategies to help you prepare to handle breakdown maintenance and minimize its impact on production.
Step 1: Identify critical equipment
The first step in maintenance planning is to identify the criticality of systems and equipment in your facility. Operationally and safety-significant equipment should be prioritized for planning when it comes to maintenance and repairs. If the equipment fails and repairs end up taking longer than required, it could have a significant impact on the bottom line of your business.
To identify critical equipment, consider the following:
- What equipment is essential to your operations? Here, you can consider aspects such as production (impact on bottom-line revenue), regulatory compliance, and worker safety.
- What equipment is most frequently used (high-duty cycles) and which has the harshest operating environment (extreme temperatures, extreme humidity)?
- What equipment is most expensive to repair or replace?
- What equipment has the highest likelihood of failure based on past internal experience or external industry benchmarks?
Let’s go over the example: if there is built-in redundancy in the HVAC and temperature control system in a manufacturing facility, they may not be as operationally critical as the instrument air compressors if they are considered a single point of vulnerability. Assigning the appropriate criticality codes and rating to individual assets in the plant makes downstream maintenance planning and prioritization activities much more streamlined and effective.
Once you’ve identified your critical equipment, you can start developing a maintenance plan for each piece of equipment in your facility. By prioritizing maintenance tasks based on the level of risk, organizations can focus on value-based maintenance of critical equipment.
Step 2: Develop a maintenance plan
A maintenance plan should include a schedule for regular maintenance and inspections, as well as a plan for responding to equipment breakdowns. While the ideal scenario is to be able to prevent breakdowns from occurring in the first place, if they do happen you want the organization to be prepared to respond quickly and efficiently to emergent issues.
This plan should include:
- What maintenance crew is responsible for responding to breakdowns? Does it require specialized training, experience, or qualifications
- What are the steps to take when a breakdown occurs? Are the procedures and manuals reflective of the most up-to-date information and best practices?
- What spare parts are needed for repairs?
- How long will repairs take?
- What is the estimated cost of the repair?
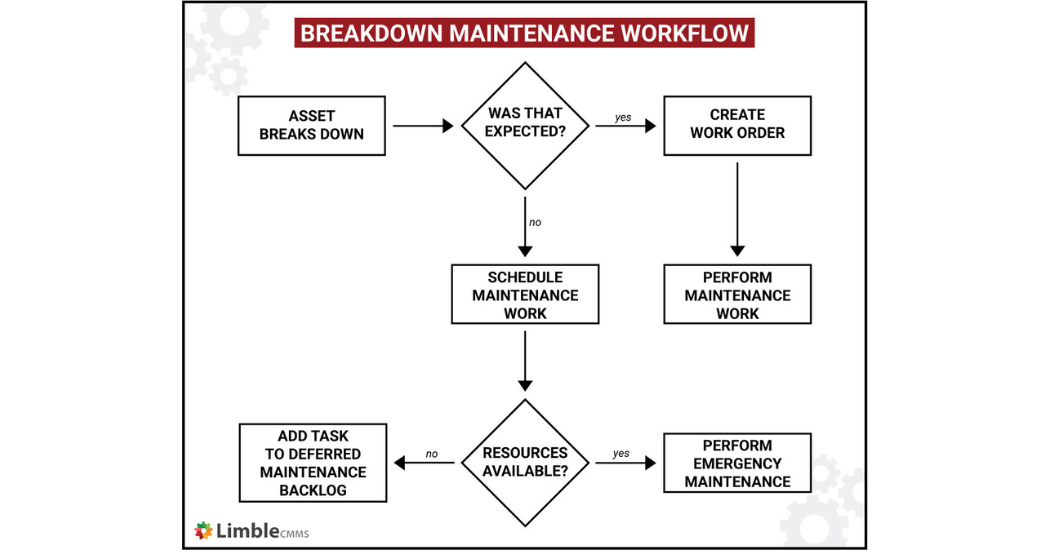
Source: LimbleCMMS
For example, a wastewater treatment plant that relies on pumps and motors to operate would likely identify those components as high-risk and high-criticality equipment for its operation based on the aforementioned Step 1. Then, by developing a maintenance plan that prioritizes preventive maintenance for these assets, such as gearbox lubrication and oil changeout, the plant can minimize reactive maintenance by reducing unanticipated equipment failures requiring costly repairs and downtime.
Additionally, the plant can proactively plan and assess work order tasks and procedures for performing the maintenance to ensure that any intrusive work that is performed happens in the most streamlined manner possible.
However, in this case, not all failure modes can be addressed or prevented through preventive or condition-based maintenance when operating online. For example, impeller wear and bearing degradation requires the equipment to be offline for maintenance.
For such breakdown maintenance activities, the plant could take steps to have necessary spare parts ready and pre-fabrication work done in case unexpected breakdown maintenance occurs, as well as ensure that overhaul procedures are up-to-date and readily available.
By having a plan in place for responding to breakdowns, you can minimize downtime and get your equipment back up and running as quickly as possible.
Step 3: Use data to make informed decisions
Data is an essential tool when it comes to planning for breakdown maintenance. By analyzing data on equipment performance and maintenance history, you can identify patterns and trends that can help you make informed decisions and plan better for breakdown maintenance.
Below are two ways you can leverage data to plan for breakdown maintenance:
- Condition monitoring: This involves using sensors to collect data on equipment performance, such as vibration, temperature, pressure, and chemical compound concentration. This data can be used to identify and trend adverse conditions before they become major problems. For example, by measuring and trending system chemistry parameters, you can predict the likelihood of deposit formation in boiler systems and plan for detailed maintenance months in advance.
- Computerized Maintenance Management Software (CMMS): A CMMS is a software system that can be used to track equipment maintenance activities, including breakdowns. Through a CMMS, you can collect data on equipment downtime, repair costs, and other factors that can help you identify opportunities for improvement. With time, the more data you collect, the more basis you will have to optimize your breakdown maintenance plans. With a centralized data repository feature that a CMMS enables, it can help identify clear trends (such as parts usage rates, resource allocation, and discovery issues) from maintenance activities that can further help streamline your breakdown maintenance plan.
However, keep in mind that even components that have a robust predictive maintenance program in place may not be immune to breakdown! For example, a random grid electrical disturbance may be all it takes to damage high-power devices or electronics.
Conclusion
Breakdown maintenance may seem like a reactive maintenance approach, but with proper planning, you can minimize the impact of breakdowns on your operations. By identifying critical equipment, developing a maintenance plan, and using data to continually improve, you can minimize downtime when they do occur.
Remember, planning is everything when it comes to breakdown maintenance. By taking the time to develop a solid maintenance plan, you can ensure that your equipment stays up and running, your operations remain efficient, and costs stay under control.
Bryan Christiansen is the founder and CEO of Limble CMMS. Limble is a modern, easy-to-use mobile CMMS software that takes the stress and chaos out of maintenance by helping managers organize, automate, and streamline their maintenance operations.