FSIP® pump design with the xLC® stator adjustment unit permits situation-specific adaptation
An existing pump, which conveyed thick sludge to an intermediate tank, showed a high level of wear due to the abrasive medium. The wastewater treatment plant decided to replace it with a unit that is more robust and easier to maintain. A NEMO® progressing cavity pump with “Full Service in Place” (FSIP®) from NETZSCH Pumpen & Systeme GmbH in Waldkraiburg was chosen and has been used since 2016. Maintenance on the pump is easily made without dismantling it from the pipes. Overall, the new design saves time during inspection, repair and cleaning work while also reducing the required installation space.
The xLC® unit is now an additional component available for NEMO® pumps. When wear occurs in the rotor-stator system, this new technology allows the performance of the pump to be re-established several times before the stator finally needs to be changed. This new unit allows re–adjusting the preload in the rotor-stator system.
Until the change of the pump, the thick sludge generated after the centrifuge was conveyed to the sludge disintegration in an intermediate storage tank by a conventional progressing cavity pump with a pressure of up to 100 psi / 7 bar. “Because the solids ratio is over 8 percent, this unit was subject to a particularly high level of wear,” the water treatment manager at the plant explains. “The texture of the medium was probably also a factor in this: It contains iron and aluminium salts from the tertiary sludge and also iron from the local industrial plant.” The original pump had to be serviced approx. every 8,000 operating hours.
Pump interior freely accessible with just a few moves
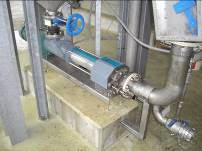
For the new acquisition, it was particularly important that the pump has a significantly higher reliability and longer service life and is be very easy to service. The customer selected the service-friendly FSIP® version of the NEMO® progressing cavity pump from NETZSCH.
For the new acquisition, it was particularly important to the customer that the pump would have a significantly higher reliability and longer service life and would be especially easy to service. The customer finally selected the service-friendly FSIP® version of the NEMO® progressing cavity pump from NETZSCH. Its design features a special inspection cover, among other service friendly components. This maintenance opening is positioned at the transition from the pump housing to the stator, allowing ideal access to the clamping coupling by removing the cover: “The cover is secured with just five screws that can be removed without any special tools in a really short time,” Mikael Tekneyan, development engineer at Netzsch, explains. “At the same time, we ensured that the pump will seal reliably at high pressures and with vertical installation of the pump.”
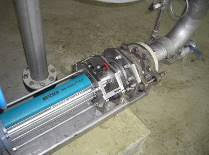
In case of wear, the setting screws of the xLC® unit are adjusted, compressing the elastomer part of the stator to re-establish the reduced sealing line.
“Once the cover is open, only one screw has to be released in order to separate the rotor-stator element from the coupling rod,” Mikael Tekneyan notes. “Then the rotating unit can simply be lifted out with the rotor-stator element. This provides free access to the pump interior from flange to flange.” All wearing parts of the progressing cavity pump can be replaced without having to remove the pump from the pipes. Because all parts are removed sideways or upwards, no additional space is needed for removal. The dismantling length at the end of the pump, which had previously been essential, is no longer required, considerably reducing the required installation space.
Elastomer stator easily replaceable
The new pump is also equipped with a newly developed mechanism which allows adjustment of the iFD stator® 2.0, significantly extending its service life: the xLC® adjustment unit. This allows the pump to run for an additional 16,000 operating hours in addition to the previous service life of around 8,000 operating hours before the stator has to be replaced. “When the performance of the pump drops, the preload between rotor and stator can be re-established with only a few moves,” Mikael Tekneyan remarks. This improves the service life of the rotor-stator element without dismantling the pump. “Our xLC® stator adjustment unit tripled the service life of the pump,” states the development engineer.
The xLC® unit is based on the proven iFD 2.0 stator technology. The iFD stator® is a dual system where the aluminium housing and the elastomer remain separated. The housing is split into two parts lengthwise and the elastomer insert can be removed easily. As the preload of the elastomer to the rotor is only established when the tension rods are tightened, the elastomer part can be pushed onto the rotor easily. It only achieves the optimum dimensions for operation through the axial compression during assembly of the pump. The axial compression of the stator elastomer with the xLC® unit compensates for wear in the rotor-stator system and re-establishes its performance. This significantly increases the service life of the conveying system components.
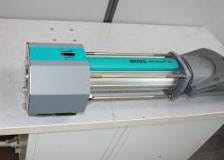
A scale with seven defined stop points facilitates gradual adjustment of the stator with only two setting screws.
How it works: If a readjustment of the stator becomes necessary due to a performance loss of the pump, you adjust the system via only 2 adjusting nuts which compresses the elastomer insert in the metal housing, reestablishing a reliable sealing line with the rotor. A scale with seven defined stopping points facilitates a step-by-step adjustment of the stator and at the same time shows the remaining potential until the stator has to be changed.
The iFD stator® 2.0 is also saves resources. The stator housing can be used throughout the service life of the pump. Only the elastomer component is replaced, which just takes a few minutes.
The stator housing can be used throughout the service life of the pump with a new elastomer insert. After opening the stator housing, the elastomer insert can simply be pulled off the rotor. This makes maintenance even easier and allows separate, environmentally friendly disposal of the elastomer, which is not possible with conventional stators.
Clearly more operating hours
Thanks to the xLC® unit, it has not yet been necessary to replace the stator: The pump runs 24 hours per day and reaches over 8,000 operating hours with an output of 4 – 13 gpm /1 – 3 m³/h. Wear has been compensated for successfully with the xLC® unit, i.e. the performance parameters of the pump were re-established every time. An end of the service life or a necessary stator change are not yet expected. “The components are ideally adapted so that the performance has been at the optimum level since installation,” the treatment manager explains.
Related Content: The xLC® stator adjustment unit triples service life of the pump
For over 60 years, NETZSCH Pumps and Systems has served markets worldwide with NEMO® progressing cavity pumps, TORNADO® rotary lobe pumps, NOTOS® multi screw pumps, grinding machines, barrel emptying systems, dosing technology and accessories, providing customized, sophisticated solutions for applications in every type of industry. With a workforce of over 2,000 and a turnover of more than 285 Million US Dollars (2016 financial year), NETZSCH Pumps & Systems is the largest business unit with the highest turnover in the NETZSCH Group, alongside NETZSCH Analyzing & Testing and NETZSCH Grinding & Dispersing.
An outstanding share! I have just forwarded this onto a colleague who has been conducting a little homework on this.
And he actually ordered me lunch because I stumbled upon it for him…
lol. So let me reword this…. Thank YOU for the meal!! But yeah, thanx for spending time to
discuss this topic here on your web page.