As the world moves to develop more earth-friendly manufacturing processes, NETZSCH NEMO® Pumps are helping a new, local plant turn food-waste into renewable energy and helping to reduce our carbon footprint. Working with local food and beverage manufacturers, from places like breweries, grocery stores, restaurants, food processing plants, schools, caterers, Wasatch Resource Recovery takes pre-consumer food and beverage waste and converts this waste into renewable energy in the form of natural gas and fertilizer.
As stated on their website, wasatchresourcerecovery.com, Wasatch Resource
Recovery, located in Salt Lake City, Utah is “Utah’s first and only anaerobic digester dedicated to food waste diversion. This process will turn the organic matter into sustainable resources – bio-gas and bio-based fertilizer.” (Wasatch,2015-2020)
Post-consumer waste holds very little remaining energy as the energy has been used by the consumer. However, food waste that would normally be disposed of in a landfill still contains a certain amount of unused and usable energy that normally would be wasted. Instead of throwing away this pre-consumer packaged and/or unpackaged food and beverage waste, the Wasatch Resource Recovery plant in Salt Lake City, Utah, collects this waste and turns it into useable natural gas and fertilizer.
“This food waste includes food scraps, liquid waste, and manufacturing food waste including prepared food, fruit, vegetables, meat, and dairy, as well as fats, oils & grease (F.O.G.) and other liquids. The Wasatch Resource Recovery plant diverts these food waste from landfills with the plan to make significant, long-term environmental benefits and create sustainable resource cost savings.” (Wasatch, 2015-2020)
For NETZSCH this application story began when the NETZSCH distributor, Tech-Flow was contacted by the contractor of the project to help select the pumps for multiple applications within the process. After working closely with the local NETZSCH Regional Sales Manager, Brett Hazen from Tech-Flow provided Wasatch Resource Recovery with NETZSCH NEMO® Progressing Cavity pump selections.
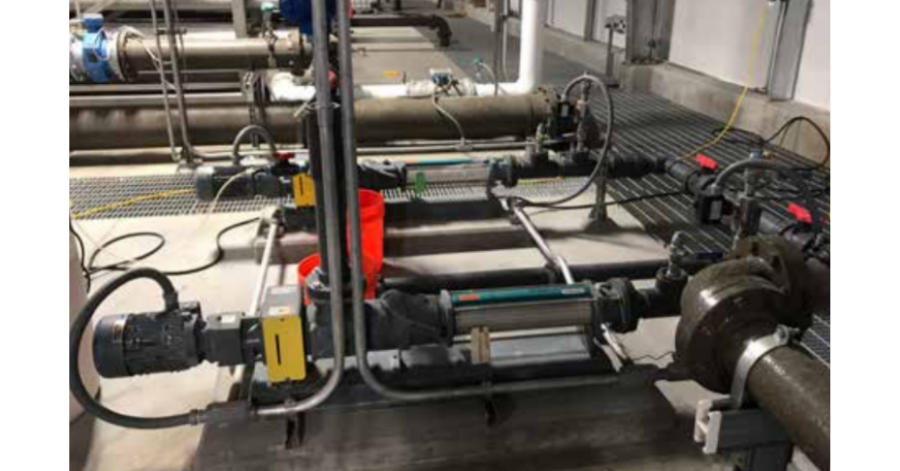
NEMO® FSIP® pumps in the boiler building to pump grease trap waste from restaurants and bacon grease from local bacon manufacturer to convey product to the digesters.
Brett Hazen said that when he was presented with the project specifications, he knew exactly where to turn stating, “NETZSCH Progressing Cavity Pumps are the ideal solution for the highly varying viscosities, products, and solids content found throughout this biogas process.”
The Wasatch Resource Recovery facility has a very high variability of incoming products (from liquids to solids). This high variability ensures a wide variation of product viscosity to be pumped. The NETZSCH NEMO® Progressing Cavity Pump which is a Positive Displacement Pump handles inconsistent viscosity easily along with any solids that make it to the pumps.
The NETZSCH NEMO® Progressing Cavity Pumps were selected in five (5) very different applications within the facility. Right after the food waste, called source-separated organic waste (SSOW), arrives at the facility, it is pre-processed and/or de-packaged. Through a series of machines, any packaging like plastic wrappers, cans, bottles, boxes, and other packaging are removed―basically all non-food material. The food waste makes its way through a grinder where it is chopped into small pieces and then onto the waste receiving tank were two (2) NETZSCH NEMO® BT Series Vertical Progressing Cavity Pumps convey the mixture of solids and liquids to the digester.
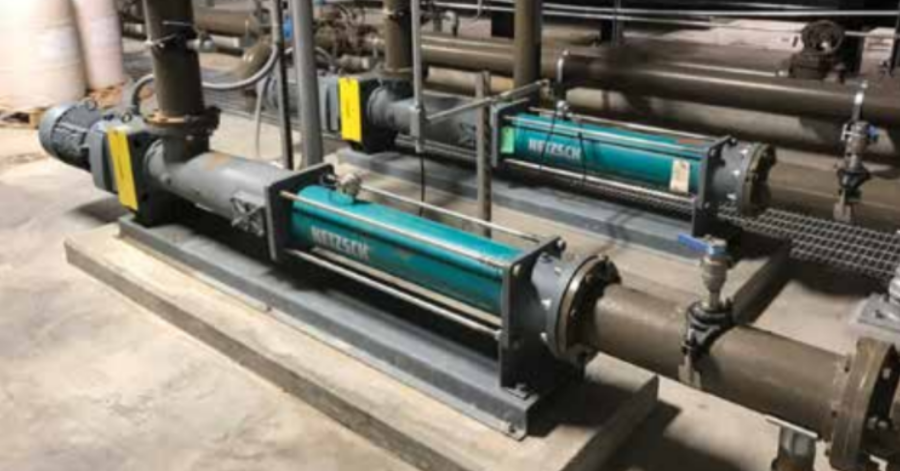
NETZSCH NEMO® 090 BY pumps in the Boiler Building transfer hydrolized food waste with extremely low pH product with 5% solids.
The digester works like a stomach and breaks down the organic matter with microbes and heat which creates biogas. This biogas is purified which generates renewable natural gas. Based on the Wasatch Resource Recovery website (Wasatch, 2015-2020), “WRR will supply enough natural gas for approximately 40,000 people or 15,000 homes…” This gas is approximately 60% methane and 40% CO2. The remaining product is converted into a fertilizer.
As mentioned previously, one of the products that is received by the Wasatch Resource Recovery facility is fats, oils, and grease or F.O.G. The F.O.G. requires a slightly different path as it does not need to be de-packaged and is pre-processed in a separate tank system prior to being pumped into the digester. An additional two (2) NETZSCH NEMO® Progressing Cavity Pumps transfer the processed F.O.G. These pumps are conveying grease trap waste from local restaurants and also bacon grease from a local bacon processing plant.
Next, two (2) more NETZSCH NEMO® Progressing Cavity Pumps are employed as the digester feed pumps. These pumps transfer hydrolyzed food waste to the digester. Hydrolized food waste is an extremely low pH media with up to 5% solids content.
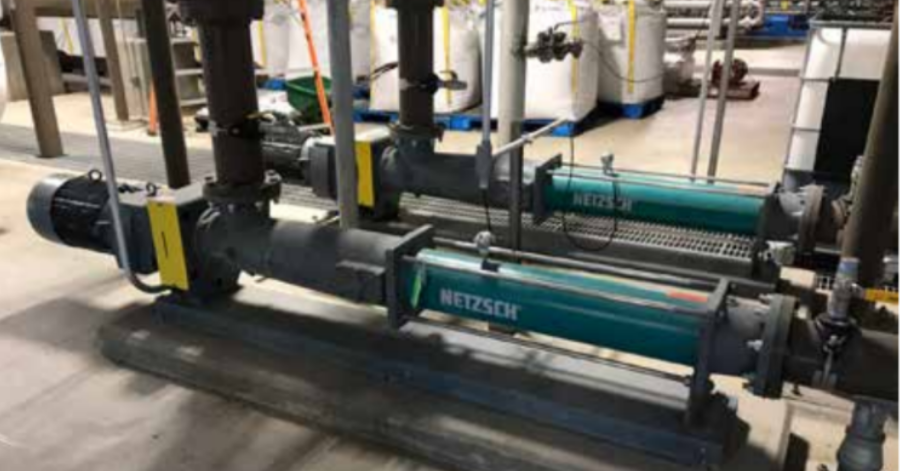
NETZSCH NEMO® 090 BY pumps in the Boiler Building provide a feed to the Struvite production.
“Organic waste in the digester is heated to aid the growth of microbes. These microbes break down in the organic matter, without the use of oxygen, resulting in biogas production.” (Wasatch, 2015-2020)
“Biogas is captured and purified before it is converted into biomethane (renewable natural gas) and fed into the nearby gas pipeline and sold into the market as renewable “green” power. Wasatch REsource Recovery will supply enough natural gas for approximately 40,000 people of 15,000 homes. (Wasatch, 2015-2020)
Two (2) NETZSCH pumps transfer the fluid (digestate) from the digester to the phosphorus recovery tank. Solids can be between 1.2% to 1.5%.
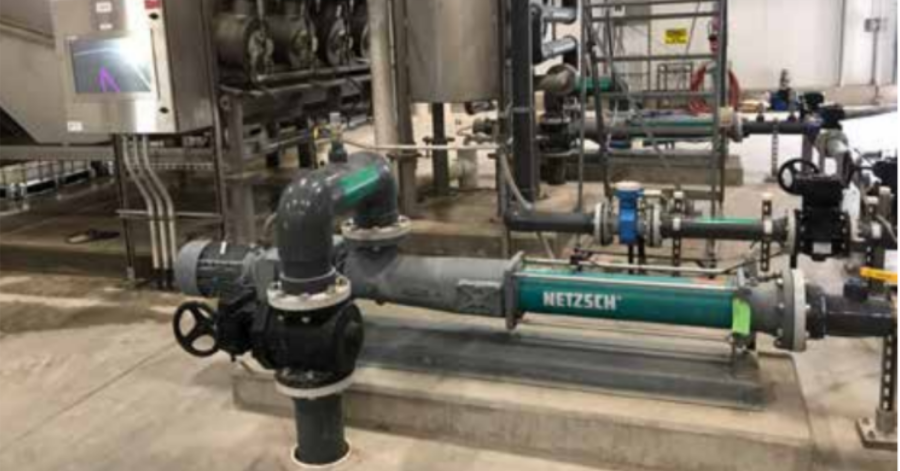
NETZSCH NEMO® FSIP® pumps in the chemical recovery building pumping post struvite production to water removal
Dewatering feed pumps: These pumps convey digestate with precipitant from the phosphorus recovery tank to the dewatering process where the material is dewatered. The solids leave the building on a conveyor where this byproduct becomes beneficial fertilizer.
February of 2021 marks the second anniversary of the WRR facility operation. As stated by Jacob Scott, the WRR Facility Engineer, “In 1.5 years of 24 hour-a-day operation, we have had zero callouts due to a NETZSCH pump issue.” That’s something when NETZSCH currently has a total of 10 pumps running in the facility. Jacob mentioned that he is currently very happy with all the NETZSCH pumps as they provide high-efficiency solids handling and very low maintenance. He said, “turn-on the NETZSCH pumps and they run.”
Learn more about NETZSCH pumps used in food and beverage applications!
Comments