The Carbon Graphite Production Process
In From Powders to Parts (Part 1), Metcar discussed the initial steps of mechanical carbon graphite production, starting with the mixing of raw powders. Part 1 outlines the processing steps that are required to produce plain carbon graphite. Part 2 addresses the various post-processing steps that can be applied to plain carbon graphite after baking.
The many different combinations of base carbons and post-processing techniques result in the hundreds of carbon grades available today. These grades are tailored to specific applications, depending on the operating conditions the material will see during operation. This versatility is one of the reasons engineers often turn to carbon graphite for some of their most difficult applications.
In this post, Metcar will split post-processing up into two categories, Graphitization and Impregnation, although these two processes are certainly not mutually exclusive.
Graphitization
Graphitization is a post-process that transforms carbon graphite into graphite. It is often used to improve the material’s oxidation resistance and self-lubricating ability. During this process, carbon graphite is heated to approximately 5,000°F in a controlled atmosphere for over a week. Throughout this time, the amorphous carbon matrix that surrounds the graphite grains within the material begins to change form and become graphite, shown in the figure below.
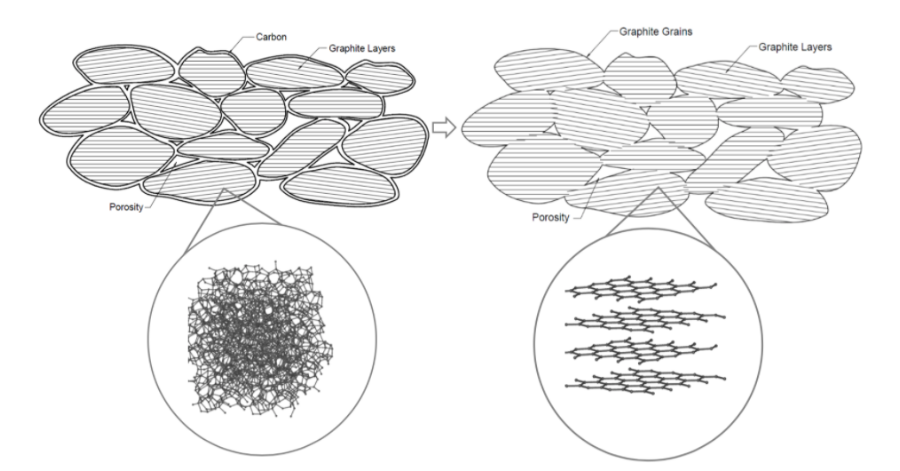
Plain carbon graphite (left side) consists of graphite grains embedded within a matrix of hard, amorphous carbon. Plain graphite (right side) does not have the same amorphous carbon matrix, but rather a softer, more lubricious graphite matrix.
Plain carbon graphite (left side) consists of graphite grains embedded within a matrix of hard, amorphous carbon. Plain graphite (right side) does not have the same amorphous carbon matrix, but rather a softer, more lubricious graphite matrix.
Graphite is often used in very dry running applications since the layered structure of graphite serves to reduce the material’s coefficient of friction. This layered structure is what gives all forms of carbon/graphite its self-lubricating ability. During operation, graphite grains deposit a burnished film onto a countersurface, against which carbon/graphite can easily “slide.” Increasing the amount of graphite in the material enhances this effect.
Yet another benefit of graphitization is improved thermal properties. Just by graphitizing plain carbon graphite, the material’s temperature rating can increase by over 200 degrees Fahrenheit. This is due to the fact that plain graphite (whose amorphous carbon matrix has been graphitized) has fewer active sites that are prone to oxidation. Essentially, this means that there are fewer exposed carbon atoms to react with oxygen during an oxidation reaction.
In addition to improved temperature resistance, graphite has higher thermal conductivity. This is due to graphite’s layered structure which allows for the easy transfer of heat. Higher thermal conductivity serves to minimize localized heat build-up, allowing the material to operate in even more demanding conditions. As carbon graphite users are constantly pushing for higher and higher temperatures, this increase in temperature resistance and thermal conductivity is key.
Turning the material’s hard amorphous carbon matrix into graphite does have a negative impact on certain mechanical properties. In addition to being softer than carbon graphite, graphite has slightly lower strength properties. This trade-off means that it is not always in one’s best interest to go with a graphitized grade over carbon graphite.
Impregnation
Carbon graphite and graphite are inherently porous materials. As discussed in Part I, the material undergoes outgassing of non-carbon elements during baking. These gasses push their way through the material, leaving behind a network of interconnected porosity. Carbon graphite manufacturers are able to take advantage of this porosity by filling it with resins, metals, salts, and others. Doing so enhances the material’s physical properties in a number of ways.
There are many different impregnation types and there are unique benefits to each. The type of impregnation used is dependent on the ultimate application of the material. For instance, the material grade used for conveyor oven bearings will likely be very different than what is used for a mechanical seal in a jet engine.
As shown in the chart below, there are a few considerations to keep in mind when selecting the proper carbon grade. However, there are also many application-specific nuances that must be considered. As such, the best way to determine the proper material grade for your application is to speak directly with your carbon graphite manufacturer.
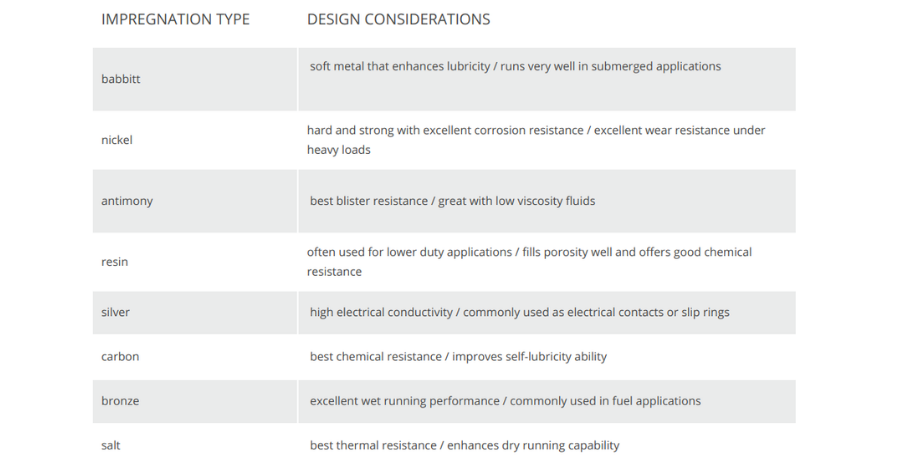
Carbon graphite design considerations for impregnation types including: babbitt, nickel, antimony, resin, silver, carbon, bronze, and salt.
Final Notes
The material processing of carbon graphite is extensive, but it is important that each step is done properly. Carbon graphite is used in a wide range of critical components across many industries. The success of these components in operation is directly linked to material processing, which is why diligence during material production is so important. For more information on how this incredible material is made, contact a carbon graphite manufacturer today.
Comments