Challenge
A wind turbine generator was suffering from grease leakage as the existing lip seals continually suffered failures. Frictional heat caused the seal to harden, lose flexibility, and leak. Heat transfer to grease caused carbonization, contributing to shortened seal life. Additionally, the heat generated from the lip seals was creating power loss, lowering the output potential of the turbine.
Once the seals failed, grease from the auto lubricated bearings would continually purge through the seal, creating housekeeping issues in the surrounding area.
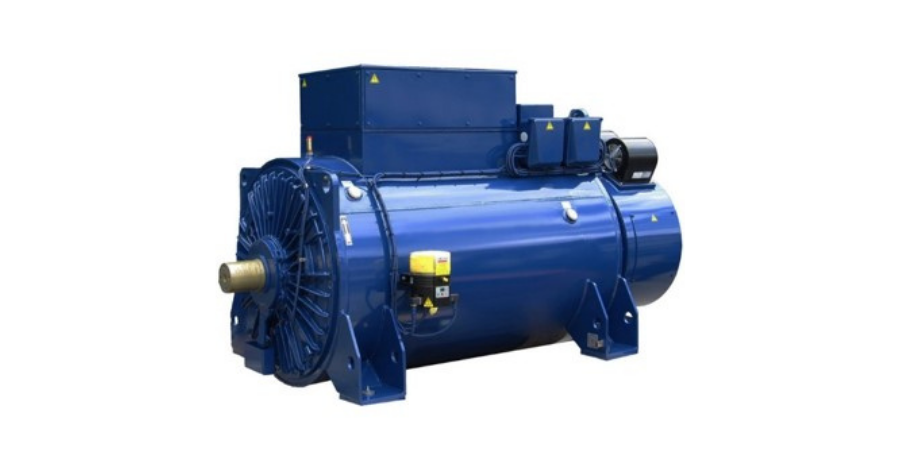
Wind Turbine Generator
Solution
Customized Inpro/Seal® Bearing Isolators were installed on the generator bearing housings. Inpro/Seal Bearing Isolators are non-contacting compound labyrinth seals that permanently protect against contamination ingress and lubrication loss. The unique design used on this application incorporated an internal rotor to contain grease lubricant within the bearing assembly.
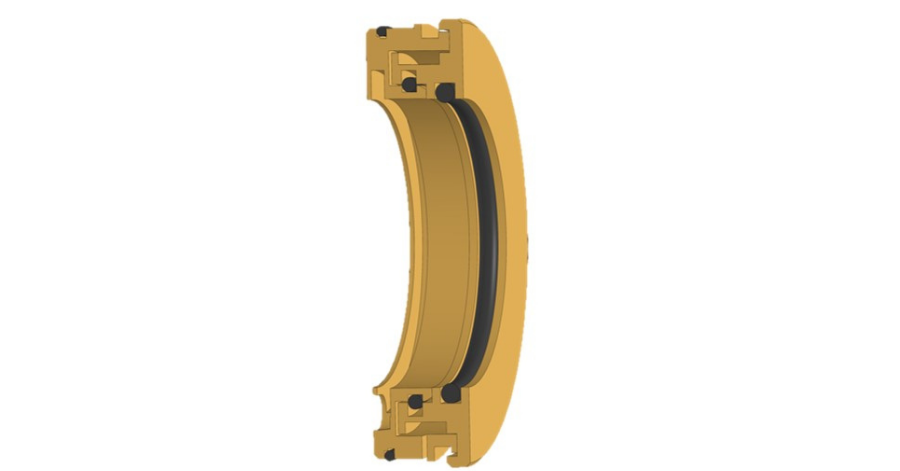
Inpro/Seal Bearings Isolator replace OEM lips seal and can be customized to fit exact equipment dimension
Result
These seals have operated successfully in the field since 2012. After initial installation, both the end-user and OEM have deployed this solution on numerous turbines across multiple wind farms with no issues.