Fig 1. Power plant and a Re-Engineered Pump installed with existing pipe runs and pipe spools.
Author: Sven Olson,
The costs of operating older pumps in vintage power plants, oil fields and process facilities have dramatically increased over the years. This in itself is often an obstacle to life extension or upgrading of plants that may have still many years of economic life. In reality to shut down and close may be the only alternative as regulatory restrictions and economic returns make new construction hard to justify. Another factor are changes in process conditions, which require pumps to perform outside the data they were originally selected for.
The replacement pump component purchase cost however is normally not the driving factor. Competitions among manufacturers and moderate labor and material cost increases have kept the pump price very stable over recent years.
The cost of replacing pumps with newer and more efficient ones are more related to the installation and commissioning than purchase cost, especially as more and more 3-rd party installation and service contractors are involved performing the work.
Lack of skilled manpower and new regulatory demands are often the reason. It can very challenging when upgrading or renewing a pump installation in an existing facility where the original pump no longer is available in the market or the replacement parts are excessively expensive. New piping, driver and mounting modifications may be required for a new pump. The original manufacturer may have stopped production of a particular model or replaced it with a new that does not fit the old installation footprint. Or the manufacturer has been acquired and reorganized and no one knows anymore where to trace the original pump.
This article is looking at a more economical way to replace a pump in an existing installation with what we refer to as Re-Engineered Pump.
Please note that the Re-Engineered pump should not to be confused with a Re-Manufactured Pump. The fundamental difference is that the first one is a brand new pump whereas the second one is an upgraded, modified or repaired older pump.
The value proposition of the Re-Engineered pump is that it avoids modifying the original installation but instead maintains the already installed piping connections, insulation and instrumentation including the driver and mounting configuration. The Re-Engineered pump is designed to fit into the original envelope where the mounting pads, nozzles and drive shaft are designed to suit the location of the original pump installation. Obviously this option will drive the costs of a replacement pump significantly lower.
The 3-screw pump, which is mostly used as Re-Engineered Pump belongs to the positive displacement pump family. It is known for its good suction lift also with viscous liquids and low fluid pulsations. The pump flow rate is directly proportional to the speed and with speed control using a VSD, the flow can be controlled which helps to save on power consumption. Direct drive eliminates the speed reducers and with internal hydraulic rotor balancing the thrust load is compensated without using thrust bearings.
Fig 2. Three screw cartridge pump
The standard pumping element designed as a cartridge, which makes it easy to install, operate and maintain. The Re-Engineered pump includes the cartridge installed in a customized fabricated external pump casing as seen in Figure 3 below.
Fig 3. Standard pump cartridge with fabricated direct fit pump casing.
The cartridge is sized for the desired flow and pressure data of the installation and tested separately in the factory. The casing, which made of fabricated steel allows for almost infinite variations of nozzle locations and mounting feet. The casing designer who is assisted by an up-to-date CAD system can import dimensions and locations from an existing pump installation and apply it to a new casing design for a direct fit. It can include an integrated relief valve as well as steam or hot oil jackets. A relief valve integral to the pump makes the installation simpler and saves from additional expensive piping modifications.
The potential candidates for Re-Engineered screw pumps applications are typically in mineral oil service with refineries, pipelines, terminals and power plants. The original pump can be another positive displacement pump as example, gear, vane, piston or screw pump. Also centrifugal pumps not well suited for actual process data are good candidates. The liquids which the Re-Engineered pumps handle includes everything from distillate to No 6 oil, pitch, asphalt, crude oil, diesel and regular lubrication and hydraulic oils. The list of applications can include charge and transfer applications, pipeline and loading service as well as general lubrication of turbines and reduction gears.
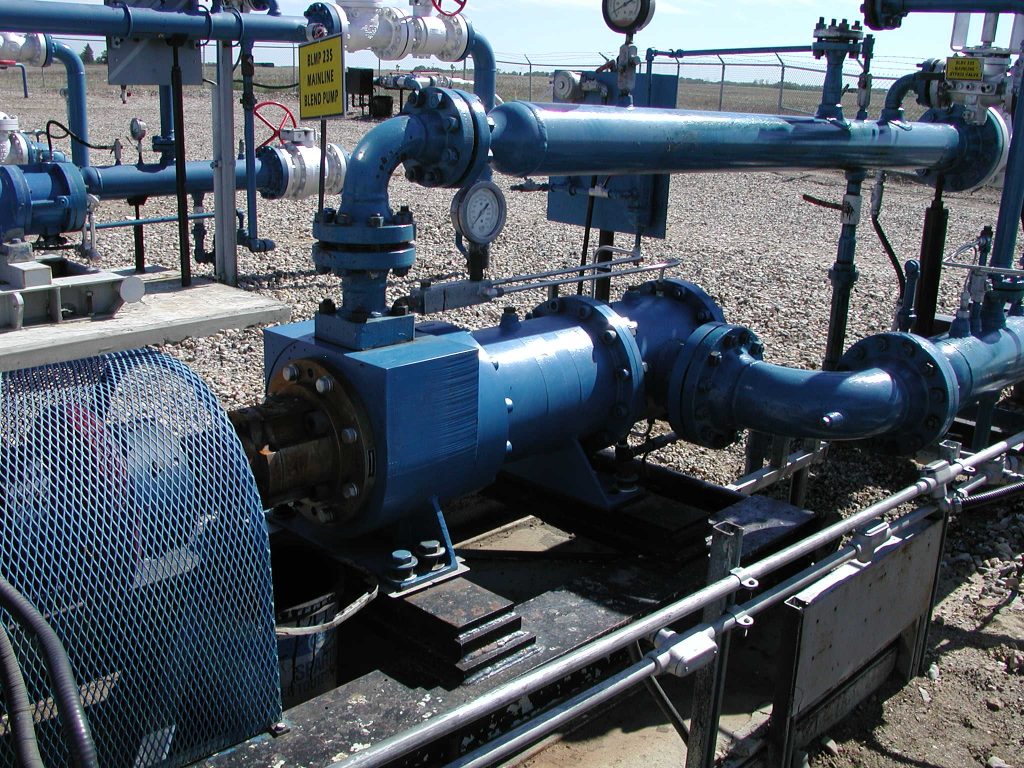
EPSON DSC picture
Fig 4. Crude oil pump designed as direct drop in
The Leistritz Re-Engineered pump offers a quick turn around as one of the key features of this pump program. Most pump cartridges are stocked in the US facilities in Allendale, NJ covering flow rates between 50 and 400 GPM and pressure up to 600 PSI. As standard the cartridges include hardened and finish ground carbon steel rotors with cast or ductile iron liners. As standard they are equipped with mechanical seals.The performance test of the cartridge takes place at the factory test stand in Germany before shipment to the US. Thus a cartridge direct from the local inventory is ready to be installed in the customized casing, which is based on customer input data including manufacturer and model/serial number of the original pump. The operating data from the past as well as motor and installation information with existing instrumentation are important information.
The casing will be produced according to this information. If an integral relief valve is needed the set pressure and location on the pump body must be decided.
The fabrication is done in a certified weld shop. ASTM standard pipe material, flanges and structural steel are used. The pump service determines the pressure rating of the casing, which is hydro tested per API 676 III Ed. Machining of the rotor bore and mounting flanges and final assembly takes place at the Leistritz facility in New Jersey including surface preparation and finish painting. If necessary additional pipe spools with flanges and instrument tabs can be provided. Shims or a pump bedplate can be offered if the motor or driver needs to be modified.
In a time where plant economy and MRO costs are under pressure the Leistritz Re-Engineered pump offers a competitive alternative to simplify the change or upgrade older, obsolete and inefficient pumps. The cartridge style screw pump is ideal for mating with the customized casing for quick turnaround and easy direct fit with a minimum of on-site disruption and installation work.