The Situation
Creating certain chemicals requires precise temperatures to ensure the chemical reaction yields the highest concentration of product. The addition of larger heat exchangers at a Midwest U.S. chemical processing and distribution company resulted in increased capacity for its chemical production. It also caused significant strain to its aging water system. An inability to keep up with the increased load resulted in inefficient product temperatures, as well as frequent and costly service to the pumps. Each time the pumps went down, production was halted for maintenance.
“The primary challenge with the old system was reliability,” said plant project manager Craig Snyder. The pumps became inefficient and costly to maintain.
In order to accommodate a growth in the company’s production needs, the producer needed to upgrade to a reliable raw water intake system.
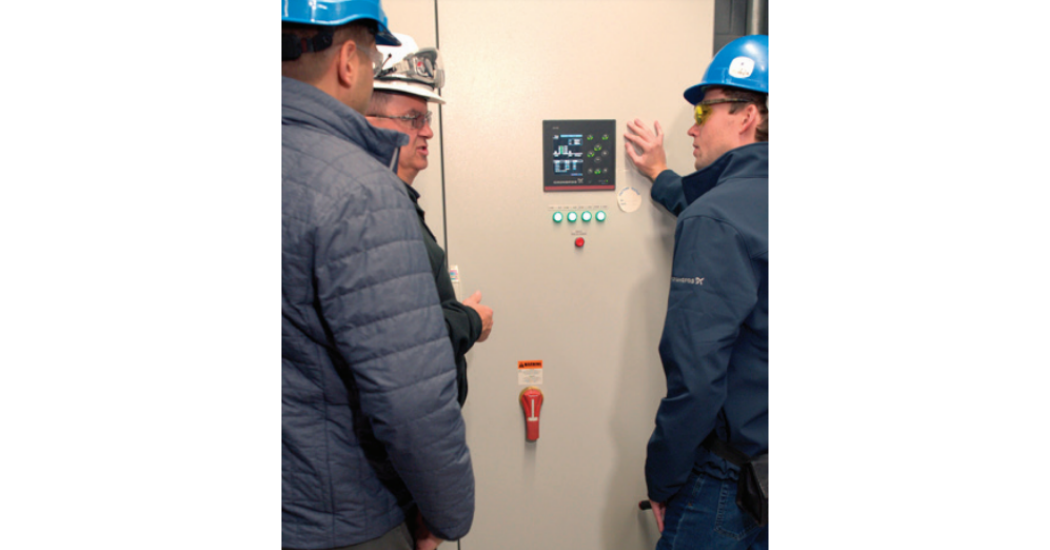
The CU352 controller allows the system to adapt to changes in demand, ramping up or down as needed.
The Solution
The company wanted the reliability and efficiency they experienced with two previous Grundfos booster systems, and were willing to invest in a system change from suction lift to a booster system because they were familiar with the operating advantages of their Grundfos booster system. Working with Illinois Process Equipment (IPE) they chose four CR 95 vertical multistage pumps in a Hydro MPC BoosterpaQ system with panel mounted VFDs and a controller. This allowed for a quick, plug-and-pump installation of a complete solution.
“Without the capability of the new Grundfos CR 95, the customer’s flow and pressure demands wouldn’t have been possible in the past,” said David Rossi, IPE territory manager. The CR 95 is part of the expanded range of CRs, which increased the overall performance of the vertical multistage range to offer more than 1,000 gpm and 1,000 feet of head.
The producer’s raw water source was a quarry, which experienced temperature variation and intake demand variation based on production capacity. The BoosterpaQ system was optimized to automatically operate at varying demand levels and eliminated the waste of energy caused by the need to open a bypass valve when system demand fluctuated.
In this system, sensors detect system demand, and pressure and flow automatically adjust to changing environments, including water temperature changes. The automated system ensures system optimization and the highest efficiency.
When one Grundfos pump requires servicing, it may be taken out of service while the other three automatically adjust to manage the load, eliminating production downtime.
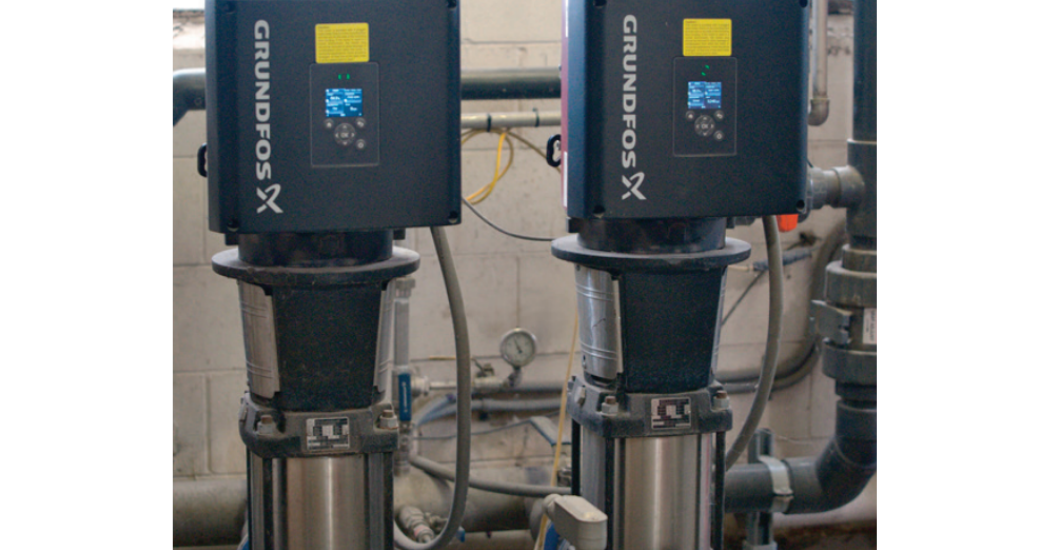
Grundfos CREs are also used in boiler feed applications in the chemical plant.
The Outcome
The new installation reduced downtime on site. The BoosterpaQ system has allowed for flexibility, depending on the demand and temperature of the quarry water, so the producer is confident their booster system is optimized at all times.
In addition to saving energy by reducing the need for a bypass valve, the automated system also delivered an immediate, real savings in maintenance time and cost. It also yields higher quality product on a consistent basis.
“We’re experiencing savings of $30,000 each year,” said Jose Ramirez, chemical plant maintenance supervisor. Now the company has eliminated a safety hazard in the plant, which was caused by loud noise from the old pumps. Because the Grundfos pumps were quiet, there was no longer a need for hearing protection in the pump house.
“The Grundfos pumps have proven to be almost maintenance free and are very efficient,” said Ramirez. “Today, we use Grundfos pumps for 100 percent of our water needs, including boiler feed water, raw water and potable water.”
Comments