What is IoT?
Terms like IoT (internet of things) and predictive analytics have been buzzwords for some time. But many people seem to have different ideas of what these technologies are, how they relate to one another, and what they can achieve. To strip away the confusion, let’s take a closer look at IoT and predictive analytics as well as the potential they hold for oil and gas companies, refineries and petrochemical facilities.
First, let’s dive into IoT. In simple terms, IoT refers to devices that are embedded with technology which enables them to connect to infrastructure. Common examples include smart hubs that can automatically adjust lighting, air conditioners, heaters and other devices, depending on when people are likely to need them. Sounds similar to a thermostat, right?
But unlike a thermostat, which is set to perform a command once the environment reaches a specific temperature, or an infrared sensor that turns on the lights when someone enters a room, IoT technology can track behaviors and learn over time.
Manual to monitoring devices
It’s these abilities for IoT devices to collect data, store it, and then use it to automate otherwise manual tasks which hold so much promise for industrial applications. One of the ways this technology has changed the rotating equipment industry is by significantly improving operational efficiency and streamlining equipment maintenance.
Before the advent of IoT technology, if an asset went down, reliability engineers and maintenance staff scrambled to identify and resolve the issue. However, with equipment monitoring devices (which use IoT technology), connected sensors inside the equipment can immediately alert maintenance teams the moment an asset experiences a failure. Knowing the moment an asset fails enables maintenance teams to begin assessing and repairing the problem immediately. Getting the asset back online as quickly as possible limits downtime and productivity losses.
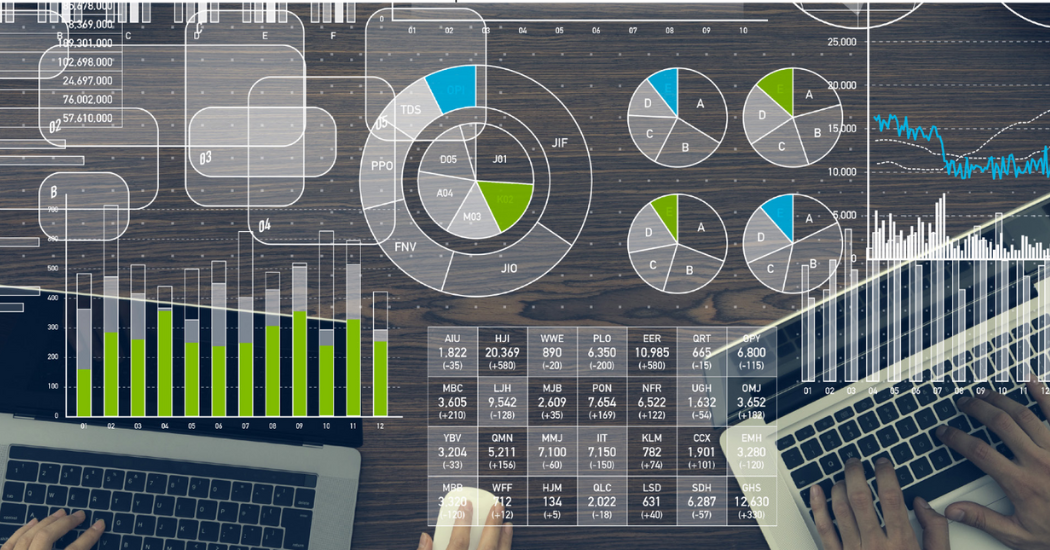
IoT refers to devices that are embedded with technology which enables them to connect to infrastructure.
Identify performance deviations, saving time and money
Predictive analytics refers to the analysis and diagnostics provided by algorithms that are continuously analyzing data in real time. These algorithms analyze equipment performance data, look for specific indicators, and make predictions on what will likely happen in the future.
It’s important to understand that algorithms are based on proprietary models, methodologies and industry experience, so the company providing the algorithms has a significant impact on what an operation can achieve by using them.
There’s currently a lot of excitement among those in the fluid motion industry because predictive analytics can apply algorithms and models to equipment data and identify performance patterns and trends over time. With this information, oil and gas companies, refineries and petrochemical facilities can see when their rotating equipment performance deviates from pre-defined thresholds. For example, changes in temperature, vibration, pressure or other conditions could indicate a problem is looming in the future. By observing these trends, reliability engineers can assess and repair failures before they happen.
IoT refers to using devices to collect, store and transmit equipment performance data; predictive analytics is the ability to interpret this data and determine some action.
What the future holds
Rotating equipment manufacturers are developing sophisticated predictive analytics offerings that go far beyond trend analysis to identify specific equipment failures before they occur.
Interconnected sensors installed on equipment monitor for changes in temperature, pressure, vibration, flow rates, torque, thrust and other conditions. Proprietary analytic models compare the data captured by these sensors to give companies a complete view of their equipment’s remaining life, most likely failure modes and recommended actions. With this information, operators can take preventive action to respond to adverse equipment conditions before they impact their respective organization.
The next generation of predictive analytics combines two critical aspects of equipment monitoring: innovative equipment sensors and algorithms
These technologies also give reliability engineers the ability to monitor equipment and predict behavior on a large scale. By connecting equipment monitoring across a network — not just across a plant, but across all operations globally — companies can apply advanced algorithms to compare interconnected
datasets from multiple systems to discover operational improvements, predict equipment failures, evaluate equipment life and plan equipment change-outs.
From reactionary to predictive
IoT and predictive analytics have enabled reliability engineers to shift from a reactionary to a predictive mindset. It’s this predictive capability that has industrial organizations excited because it allows them to see what matters. Bringing predictability to an otherwise unpredictable process allows organizations to avoid equipment failures, downtime and costly repairs while maintaining high productivity.
About the author
Aric Zurek Vice President – Marketing & Technology, Parts & Services Aric is a global executive with more than 20 years of experience in the energy field in power generation, oil & gas, and the general industry. As the director of aftermarket products & services at Flowserve Corporation, he is responsible for leading and shaping the company’s strategy for a global product portfolio of flow-related parts, repairs, services and seals for the oil and gas, power, petrochemical, water, mining and general industry applications.
Comments