Water is one of the most basic and essential resources for life, as well as for the maintenance of ecosystems, and it is also a strategic component of the world economy. Water has high rates of exploitation with a fragile balance between available water resources and demand.
Unfortunately, water is increasingly considered a scarce commodity (Fig. 1) for the following reasons:
- Climate change: Many countries periodically experience droughts with notable drops in rainfall. A recent report from the World Drought Observatory concluded that Europe is suffering its worst drought in 500 years and in 2022, more than 270,000 hectares burned, according to the System European Information System on Incendios Forestales [1].
- Water pollution: There are more than 70,000 substances known as pollutants whose discharge into seas and oceans are one of the main causes of water pollution (There are liquids that, in low concentrations, can contaminate vast water areas. For example, only four liters of naphtha can contaminate up to 2.8 million liters of water [2]).
- Overpopulation: According to the U.N. [3], it is estimated that the freshwater resources available per person have decreased by more than 20% in the past two decades due to population growth.
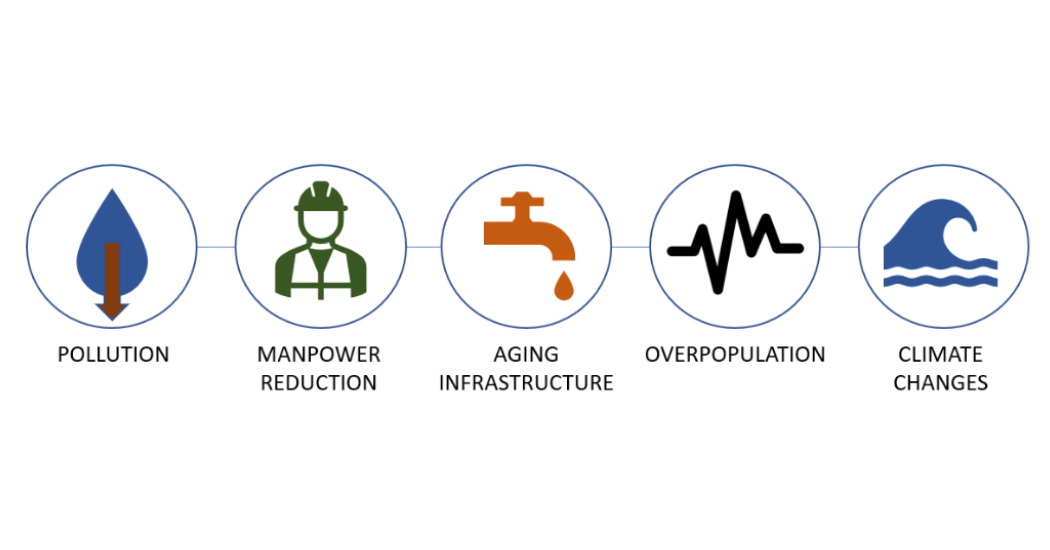
Fig. 1 – Interrelated challenges in water systems are creating critical vulnerabilities.
On the other hand, water management infrastructures are increasingly obsolete and, in many cases, there is incomplete information on their consumption, as well as on the losses that occur in the distribution networks due to leaks or breaks.
It is estimated that water companies worldwide lose 40 billion euros per year in revenue due to non-revenue water (NRW). For example, in Italy, according to an Istat report [4], more than 40% of the water is lost during its distribution.
If we do not act quickly and responsibly, almost one of four children worldwide will be living in areas with extremely high water stress by 2040, according to a UNICEF report [5].
The main solution to these evidenced problems consists in applying digital technologies: It is necessary to undertake a complete modernization of the water cycle through the Internet of Things (IoT) to move toward a more efficient management of the fluid while simultaneously minimizing the impact of climate change by achieving a better balance between demand and available water resources.
IoT is essentially the grouping and interconnection of devices and objects through a network (either private or the Internet, the network of networks), where they could be visible and interact. The types of objects or devices could be anything, from sensors and mechanical devices to everyday objects such as a television, radio or washing machine. With more than 10 billion IoT devices connected today, experts predict that this number will rise to 22 billion by 2025.
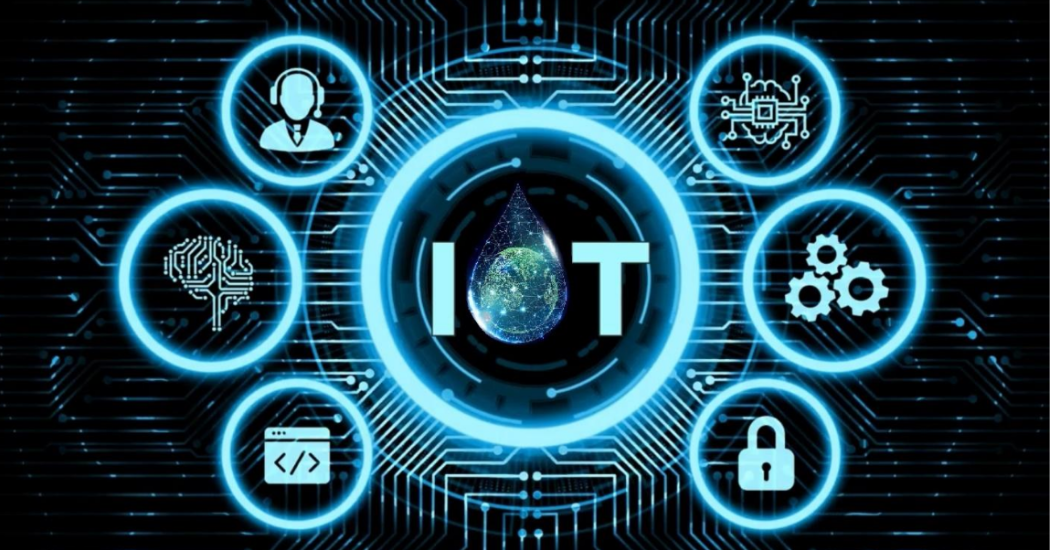
Fig. 2 – Internet of Things (IoT) chart for Digital Water (courtesy of Flowserve).
Digital technologies could save the water sector 60 billion euros a year worldwide.
In this article, we will analyze which are the digital solutions available in the market with particular attention to asset monitoring (for example, pumps and valves), one of the main protagonists for the correct distribution and management of the water.
Many industries have already gone through a digital transformation with overwhelmingly positive results. For example, Formula 1 cars now have more than 300 smart sensors installed in them that allow critical engine parameters and driver biometric data to be analyzed in real time (it is estimated that more than 400 GB of data is exchanged between the car and the control center at each GP) — significantly improving performance compared to 10 years ago.
Digital transformation, therefore, can be seen as a natural evolution in the water industry.
The barriers to digital transformation and their solutions
There are several reasons why digitization adoption is taking longer in the water industry than in other industries:
- Water distribution and control systems are often old, making integration and interoperability of new systems a major hurdle. Fortunately, IoT is facilitating this transition with cloud-native platforms that are data-agnostic — a key factor for everyone to participate and seamlessly integrate new capabilities (for example, API systems).
- Cybersecurity is another growing concern that is giving rise to a new set of fears. However, newer security software tools have been developed that are practically impossible to corrupt (example: 256-bit AES encryption).
- There is also the issue of culture in the industry. There is a resistance to new technology, especially in a water industry with a large aging workforce accustomed to a defined role where their experience is their greatest asset. Giving those defined responsibilities to a connected device can be perceived as a threat to the workforce. Fortunately, many cloud-based technologies are designed to be intuitive and easy to use, with customizable visual dashboards, alerts and automated processes. Cloud hosting also offers a maintenance-free solution for business IT departments.
- Cost/investment problems are another hurdle. It is true that many of the tools may entail a large initial cost, but this investment is gradually offset by the environmental benefits and future savings. We normally expect a return on investment of less than one year for solutions such as condition monitoring.
However, these obstacles have led to a nonlinear transformation in water companies, so every company should research the available options to gain the best customized solution according to their digital level of adoption.
In the following section, we will define various steps of digital adoption and their primary solutions.
Digital adoption phases and their solutions
To become a digital water company, it is important to clearly establish the level of digital implementation in order to effectively improve the efficiency of water resource management.
For example, we can define five phases of digital adoption (Fig. 3):
- Not Started
- Basic
- Opportunistic
- Systematic
- Transformational
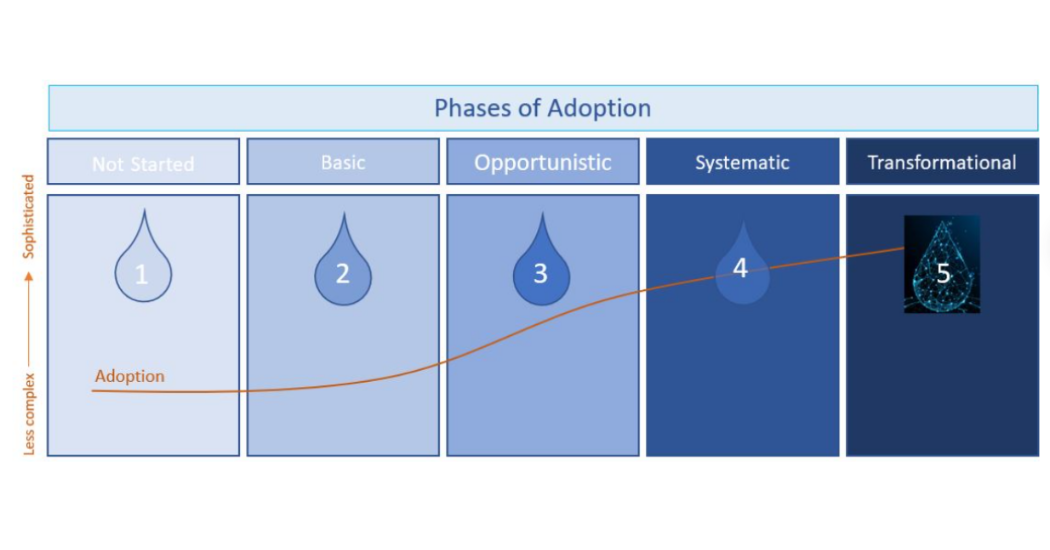
Fig. 3 – The five phases of digital adoption (Courtesy of Flowserve).
In phase 1, we are considering an analog and obsolete infrastructure, where the first step is to recognize digitization as a priority. It is essential to develop a pilot project, selecting the most critical parameters to be digitized/monitored. A pilot project, for example, could be the implementation of vibration, temperature and pressure sensors in the pumps that notify the control room immediately in case of abnormal values.
Phase 2 is a direct evolution of phase 1. The data sent to the control room can also be stored in the cloud and sent (there are several wireless communication protocols such as LoraWan, WirelessHart, GSM, Isa-100, etc.) to a tablet, mobile phone or laptop to have remote monitoring (condition monitoring). In this phase, the basic concept of IoT begins to be adopted since the instruments, sensors and mobile devices are connected to each other (implementing SCADA systems, for example). Being able to collect data in the cloud allows a water company to move almost immediately to phase 3 of this digital transformation.
Level 3 consists of implementing a broader range of sensors compared to phase 2, either using an advanced measurement infrastructure and/or solutions such as geographic information systems (GIS) or models of hydraulic networks directly connected to each other that inform and improve decision making.
For example, at this phase, the use of water leak detection sensors, together with historical leak data stored in the cloud and implemented with a hydraulic network model, can significantly improve correctly selecting the most critical pipes that have to be replaced during a scheduled maintenance and while also managing more efficiently the flow through the distribution pumps.
Levels 4 and 5 are achieved by collecting near real-time data from different sources. The information generated from sensors and historical network data, combined with the most innovative techniques (artificial intelligence, machine learning, digital twins, algorithms, and virtual/augmented reality), help companies improve the efficiency of their system and its environmental impact. In addition, they improve planning (based on predictive results) to meet their long-term business, environmental and regulatory goals.
For example, a predictive analysis of a pump not only makes it possible to anticipate problems such as cavitation or internal flow recirculation, but also allows continuous work at maximum efficiency while optimizing energy consumption and reducing carbon dioxide emissions.
Another example of this level of digital transformation is the use of virtual or mixed reality to safely learn the correct maintenance steps on the digital twin of the asset or be remotely connected to the service center for immediate assistance.
As we have seen in the previous paragraphs, in each of the five steps, assets like pumps and valves are among the greatest challenges of digital transformation in the water market. For example, in reverse osmosis desalination plants, high-pressure pumps represent 80% of the plant’s total electrical consumption.
Therefore, in the next section, we will examine the best digital solutions for asset management.
The importance of asset management in the digital transformation of water
Asset management and the analysis of assets’ status in the field it is something that all industries have been working on for many years.
A routine field measurement has long been implemented as a form of maintenance. Unfortunately, this approach is not anywhere close to preventive maintenance and instead remains as part of the corrective maintenance mindset.
A routine analysis in the field only details the state of the equipment at a given time and service conditions. Given that that this equipment may not work continuously under the same processes, it is not logical to assume that a piece of equipment is in optimal condition when the only reference is an isolated data at a given moment.
With a measurement taken in the field once a month, 12 measurements will be obtained in a year. On the contrary, with a measurement taken every 30 minutes by sensors, for example, there are more than 18,000 opportunities to find variations. In terms of real-time measurements, the number grows to more than a million opportunities in a year.
It is obvious how proper instrumentation can exponentially increase the data we obtain from the equipment.
This data can be stored in asset management systems (AMS) and eventually carry out a search or a detailed analysis, although unfortunately it is an activity that requires many hours of work or is practically impossible since the human teams that manage this data are usually small or do not have the necessary knowledge to perform a deep analysis.
In general, it is apparent that the technology facilitates the data collection, although not its management. So where is the IoT revolution?
The revolution in this field is directly the management of this data.
There is a simple approach for non-critical equipment: A trend analysis of the data obtained through management implemented on a web platform where the data is detailed in graphs allows a visual and intuitive way to see if any of the monitored parameters has a tendency toward risk values. Oppositely, the data are kept in a safe zone according to the parameters of the machine where the measurements are made.
In the case of data moving to a risky area, the system will automatically notify the end user, which would allow the operators to focus on and dedicate the necessary resources in the field to verify this situation.
If we compare this with a data storage model (AMS), the differences are obvious. With an AMS we immerse ourselves in a large volume of data without any format. Giving the data meaning is complicated and when a conclusion is reached, it is a situation that has already happened and has most likely gotten worse.
However, with an automatic alert service, those responsible for a plant’s reliability can notify operations at the same time an asset shows symptoms that could lead to a major failure. Therefore, it is important to start taking preventive measures and at the next plant shutdown, think about the equipment that will need a more in-depth review or whether any spare parts or auxiliary equipment are necessary to complete the work.
Another advantage could be to carry out a detailed study of the process conditions and determine if any of these have been the trigger for the asset operation deviation — instead of thinking of the equipment itself as the problem. We could improve the operation and extend the meantime between failures (MTBF) of the equipment. Equipment availability is increased, and maintenance is reduced.
If this information is not available in advance, any action to alleviate the problem once it has occurred is reactive, which entails a very high level of risk for the operation. The optimization and management of human teams and equipment is reinforced, which has a positive economic impact in the plant management.
Systems such as Flowserve’s RedRaven™ and LoRaWAN technology and its Node ER sensors, take data from a multitude of devices in a very secure manner with minimal infrastructure. A single gateway could receive information from hundreds of sensors distributed within a radius of up to 1.6 km. From there, the information can be sent to the cloud for automatic management and analysis in the web portal.
An application for this technology could be pumps in a water distribution network where a multitude of equipment is distributed in different plants and in most cases with minimal maintenance. With RedRaven™, all these assets could be perfectly monitored and, in the event of any variation in their operation, those responsible could be notified and they could then decide which preventive action is best to avoid a major problem.
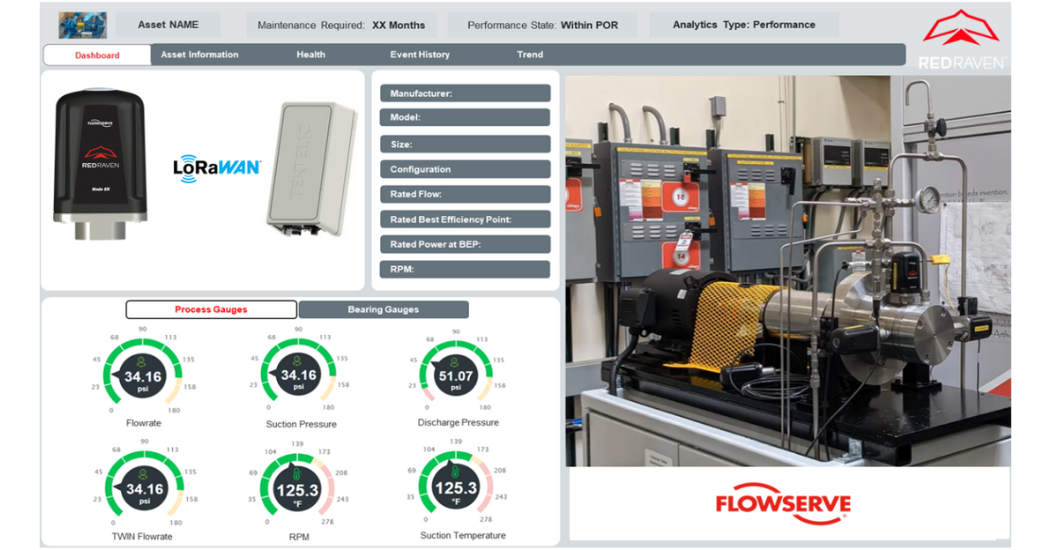
Fig. 5 – Example of RedRaven wireless condition monitoring.
Another approach for the use of this technology is the management of critical equipment for the operation where it is not enough to know the trend of its condition, but a deeper insight is required, such as knowing in detail how each component is or if the equipment’s performance has changed regarding its design.
This requires a much larger data collection than in the first case mentioned. For these scenarios, we are talking about real-time measuring. This allows users to implement a detailed analysis on an algorithmic basis and even discuss forecasting future conditions before they occur.
However, it is paramount and should be noted what kind of algorithms are suitable for each situation, since handling this subject incorrectly can make a CBM implementation fail catastrophically.
There are a lot of models based on artificial intelligence, however, in many situations it is not the best ally, particularly when managing these critical assets. It is important to understand this concept since in many cases it is presumed that “artificial intelligence” can solve all problems and do everything automatically. This is not the case.
Artificial intelligence algorithms work from the existing asset condition where the data is taken. This creates, difficult problems to solve. For example, if the initial data taken from the machine is not ideal, that baseline from which to start analyzing will be wrong, and future management and monitoring of the equipment will already be conditioned. It will be linked to pre-existing conditions, which is not what is desired.
Fine tuning this technology is particularly difficult, whether it is the amount of data required and the time to implement it or the continuous algorithm feeding, which makes the algorithm handling inviable.
This can be a big problem when using artificial intelligence technology correctly. In addition to the fact that specialists will be required to the continuous manipulation of the algorithm to adapt to changes in the machine will require specialists for its maintenance and this will have a considerable cost.
These types of algorithms are usually available through companies that are unfamiliar with the equipment where the algorithms are being implemented.
The client who uses this technology will most likely be in an awkward position, because although it may receive data, it will not be reliable, and the number of false positives reported will be overwhelming for the operation and management teams, which will jeopardize the implementation of predictive maintenance.
With this information, some monitoring service providers took a different approach. They developed algorithms based on the machine’s physical parameters from its optimal factory condition. This brings a great advantage with respect to the implementation of artificial intelligence algorithms.
The baseline against to do the analysis is ideal, and implementation is immediate. It does not require adaptation time or continuous tuning of the algorithm to the process conditions of the machine.
So, if the physical approach makes more sense than artificial intelligence, why are more companies offering artificial intelligence models for equipment monitoring?
To develop physical algorithms, one must have extensive previous experience and knowledge of the equipment that is to be monitored. The data needed to develop physical algorithms is the result of many years of experience in the research and development of machine design and testing.
Very few companies can offer these models and a reliable solution with the ability to anticipate and foresee a previous condition in the operation and performance of the equipment.
Solutions such as Flowserve’s RedRaven™ “Predictive Analytics” offers a solution under this principle and shows through its portal, all the information of the monitored equipment. Working in over 15 different failure models, from mechanical failures, tribology, and hydraulics failures such as cavitation, internal recirculation or vacuum circulation. It also makes a prognosis analysis where it calculates the asset’s remaining life.
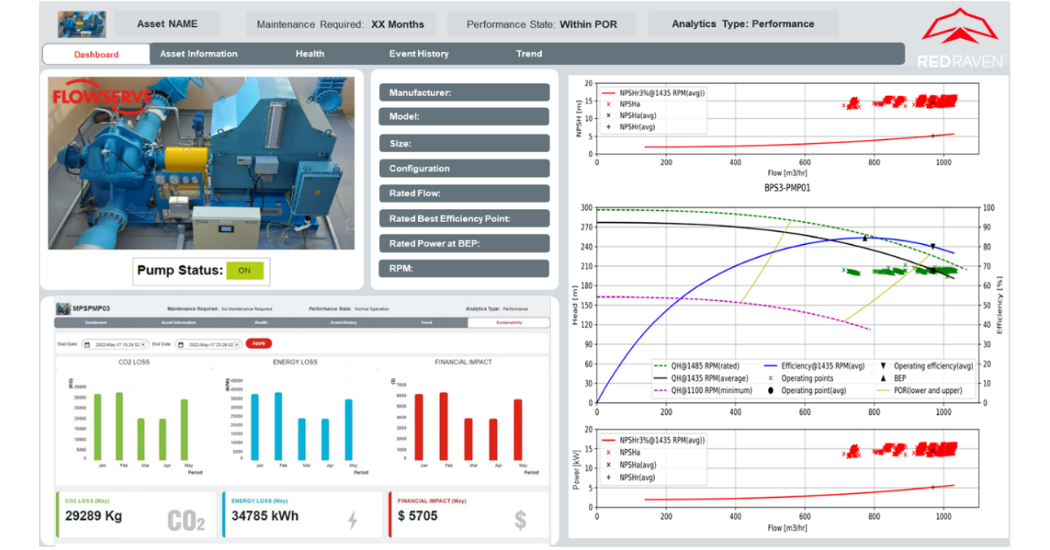
Fig. 6 – Example of RedRaven predictive analytics.
With the right sensors, the curve of a pump could be obtained in real time and create the digital twin of the equipment, being able to manage the performance, improving its availability and operability for a longer period. Recommendations could be obtained to improve its use or even manage the service conditions to improve factors such as production process and energy expenditure.
A clear example is a desalination plant where high-pressure pumps are a very energetic equipment and optimal operation is essential to keep the cost per liter within the parameters in which the plant was designed. Any deviation in this regard can create a big drawback for the plant’s profitability.
RedRaven™ offers solutions for predictive analytics on pumps and mechanical seals, as well as instrumentation, control valves and electric actuators.
Conclusions
We have seen how the optimization of water resources through digital technologies is essential. Becoming a digital water company is a necessity to address aging infrastructure and increasing water scarcity, stress on water systems, urbanization and extreme weather events.
Digital solutions represent the best measures we can take to improve the use of water because they allow:
- Reduction of CO2 emissions.
- Elimination or reduction of the use of pesticides and other types of chemical products that pose a threat to nature.
- Improvement of wastewater treatment.
- Reduction of NRW.
Avoiding the waste of the most precious resource in the earth is in our hands. We still have time to improve water management through digital technology, backed by solid institutions that guarantee everyone’s right to this precious liquid. If we start digitizing now, we make the world a better place for everyone to have reliable access to clean water.
Authors:
Francesco Giuseppe Ladisa
Global Product Leader – Digital Water Flowserve
Carlos Ortiz
Business Development Manager – RedRaven™ IoT Flowserve
Resources
- https://www.bbc.com/mundo/noticias-internacional-62718599
- https://www.fundacionaquae.org/agua-y-contaminacion/
- https://news.un.org/es/story/2020/11/1484732
- https://www.istat.it/it/files/2021/03/Report-Giornata-mondiale-acqua.pdf
- https://www.unicef.org/turkiye/en/press-releases/one-five-children-globally-does-not-have-enough-water-meet-their-everyday-needs