Flow loop optimization study identifies real energy savings
A typical processing plant such as an oil refinery can incorporate hundreds or thousands of pumps. They consume as much as 60%i of the facility’s energy usage.
The amount of energy used largely depends on the design of the pumps, the process conditions and the way in which the system is operated. Inefficient or inappropriately sized or selected pumps, valves and drive trains can add millions in unnecessary energy costs and increase Scope 2 emissions for plant operators. They also can contribute to poor equipment reliability, which increases the risks of unplanned downtime and higher maintenance costs.
That’s why a major oil and gas company partnered with Flowserve to evaluate their situation and develop a plan to address potential energy cost savings within various refining processes at one of its production facilities in Western Europe. The total electrical power consumption of the pumping systems in the study was approximately 40,000 MWh per year.
Together, we conducted a pilot project that analyzed actual operating data for 15 critical service, high-energy pump flow loops. The pumps and control valves in these systems had been supplied by Flowserve and other flow control equipment manufacturers. The study found that by modifying the flow control equipment, overall flow loop efficiency (or specific energy) could be improved and thereby significantly reduce the customer’s operating costs and improve their carbon footprint.
When the plant operator completes implementation of the recommendations, energy consumption of this equipment will be reduced by approximately 35% from the prior year. Payback on the investment in equipment upgrades is comfortably within the plant’s threshold for return on investment (ROI).
Understanding performance for a broad range of equipment
The refining processes form a complex hydraulic network that operates using flow control equipment supplied by multiple original equipment manufacturers (OEMs), including Flowserve. The range of installed equipment is broad, with many different pump types along with their respective downstream control valves. Flowserve’s expertise with pump and control valve design, along with operational characteristics and computational fluid dynamics (CFD) modeling of flow loops, was critical in being able to evaluate any type of flow loop within the process.
Systematic approach to efficiency improvement
In a consultative approach, Flowserve specialists partnered with the refinery operators to undertake an operational
assessment of the installed flow control equipment. A systematic data-driven evaluation process along with Flowserve’s engineering expertise allowed us to identify and achieve significant improvements in overall flow loop efficiency.
Calculating hidden costs and quick ROI
Flowserve analyzed two years of performance data from the refinery’s pumps and control valves and studied the pump flow loops to identify opportunities for improvement that met the refinery operator’s minimum ROI targets.
In instances where process data was not available, our experts utilized proprietary analysis tools to estimate the process performance data.
Energy savings of 35% annually
Within eight weeks, Flowserve proposed solutions that would result in an overall annual energy savings of 35%. We provided a proposal for the modification costs as well as calculated the corresponding CO2 emissions reduction and associated savings from lower carbon taxes and regulatory costs.
The study included a review to determine whether any of the pumps were “bad actors”, which meant they were operating with frequent repair events, negatively impacting maintenance costs, disrupting plant operations, and potentially risking production. Our experts recommended corrective actions that would address the bad actors we had identified and enable them to operate more reliably.
Comprehensive turnkey solution
The proposal presented a complete, turnkey solution from Flowserve, which included:
- Data gathering and solution analysis and definition
- Program management to align execution timing with the site
- Delivery of all necessary equipment modifications
- Testing to verify efficiency gains
- Monitoring program (reference ISO 50001 energy management program requirement on monitoring to maintain
gains) to measure and track efficiency loss over time
The monitoring program was RedRaven from Flowserve, which enables companies to realize the full benefits of the internet of things (IoT) and predictive analytics to continuously monitor efficiency performance.
The program management approach categorized equipment upgrades in terms of when the modifications could be
implemented (i.e., during normal operations, during routine maintenance cycles or wait for turnaround) to enable seamless execution within normal refinery operations.
Accelerate your energy transition plan
Optimizing pump efficiency is an increasingly important consideration toward the achievement of sustainability goals. The Energy Advantage Program from Flowserve offers a suite of solutions focused on enabling significant efficiency, reliability and carbon reduction improvements from the optimization of flow control loops.
The Energy Advantage Program can quickly enable your company to start achieving operational cost objectives and accelerate progress toward realizing your decarbonization goals. Partner with Flowserve to implement the program and then monitor the savings on an ongoing basis to ensure that your company continues to meet energy efficiency targets.
Flowserve specialists share their unparalleled experience in implementing solutions to optimize pump efficiency around your process needs. Contact Flowserve today to see how they can support you at EnergyAdvantage@Flowserve.com
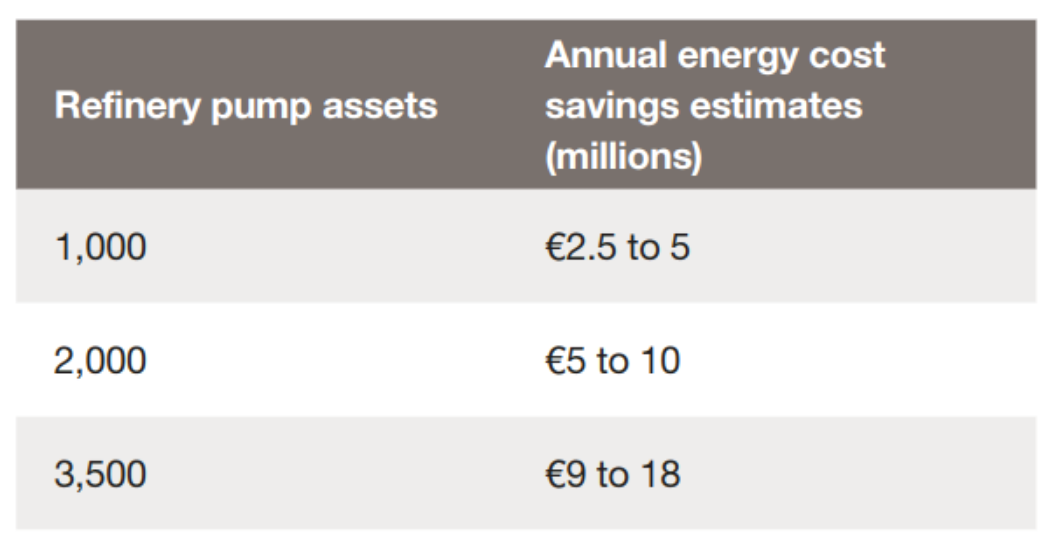
Source: Flowserve internal research (2022) based on 60% of pumps being operational, an average rated power of 50 kW for refinery pumps, 8,500 operating hours, 20 to 40% savings potential, 80% successful assessments at €0.06/kWh
Methodology used
Flowserve uses a systematic process and data-driven approach to identify and prioritize opportunities for efficiency and operational gains. Flowserve combines the system-level understanding of flow control component interaction with OEM product expertise for each of the main components to identify and act on energy optimization opportunities in flow loops.
A customized contracting and execution model can then be developed to implement solutions, delivering fast results while aligning schedules to achieve minimal impact to normal site operations. Adjusting and monitoring resultant savings is important to maintain achieved results. These are a few of the best practices identified in the pilot study conducted by Flowserve in partnership with this large refinery operator.
Significant reduction in operational expenses can be achieved; Flowserve typically estimates 20 to 40% energy savings for similar projects. Using the results of this pilot project, the annual energy cost saving range potential for your company’s project can add up to millions:
Our commitment to energy transition
At Flowserve, our approach to energy transition begins and ends with our purpose: to make the world better for everyone. We understand that when we enable our customers to tackle climate change and address increasing energy demands through our innovative flow control solutions, we can make the world better — now and for generations to come.
Our approach is threefold. We are diversifying, decarbonizing and digitizing to support the global energy sector’s transformation toward low-carbon sources.
i U.S. Environmental Protection Agency, “Energy Efficiency Improvement and Cost Saving Opportunities for Petroleum Refineries,” An ENERGY STAR® Guide for Energy and Plant Managers, Document Number 430-R-15-002,
February 2015, https://www.energystar.gov/sites/default/files/tools/ENERGY_STAR_Guide_Petroleum_Refineries_20150330.pdf (accessed January 21, 2022).