Challenge
A leading process licensor partner consulted Flowserve for flow control equipment expertise to improve the process design and capacity scale-up of an upcoming plant, with the objectives of improving efficiency, safety and reliability while reducing emissions.
Solution
By working together during the early design stages of the project, the Flowserve and process licensor partnership produced critical feedback concerning the interaction between the conditions and the control valves. This enabled adjustments to be made during the early design stages of the project which would ultimately help streamline the plant’s start-up time, thus minimizing waste and improving efficiency.
In 2021, a leading process technology licensor collaborated with Flowserve on the design of a large-scale, world-class plant. As part of this process, Flowserve sized up and modeled a solution using the latest control valve technology — the Valtek® Mark 100™ valve — designed to overcome limitations experienced in previous projects.
Flowserve has a long history of this kind of collaboration with technology licensors, plant operators, and engineering, procurement and construction (EPC) firms. The company’s expertise and product knowledge are proven assets when developing solutions to scale-up, reliability, efficiency and safety challenges. More recently, partners have increasingly turned to Flowserve to help meet the challenges of converting to cleaner energy sources and digitizing operations.
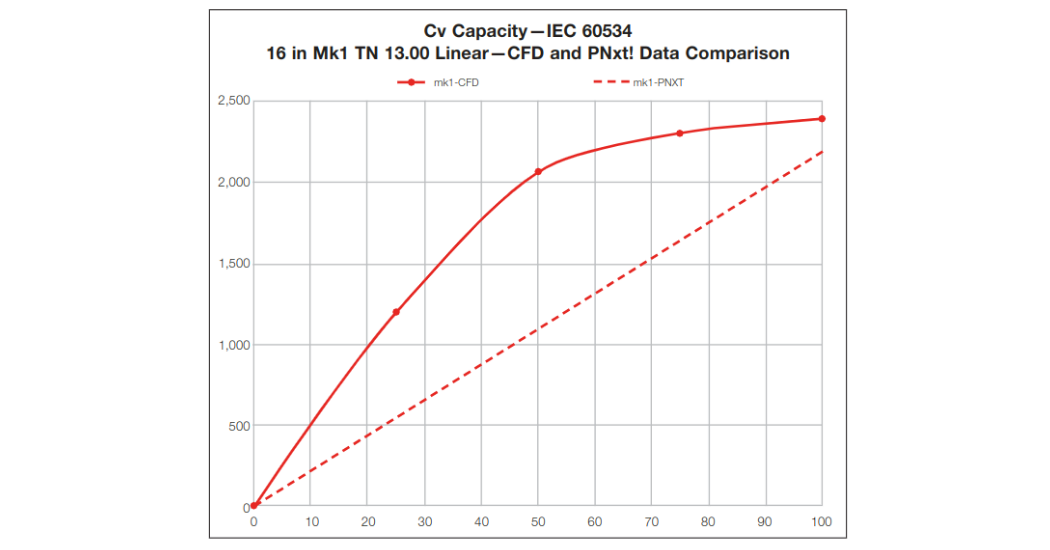
Original Mark One valve, published and modeled flow curves
Solving old problems — and preventing new ones
Technological advances have made it possible for Flowserve to improve the quality and performance of a critical control valve application that impacts product quality and the safety and availability of the unit’s process. The first step was to verify the accuracy of Flowserve’s sizing and computational fluid dynamics (CFD) analysis, using a computer-aided design (CAD) model of the original valve and replicating its past performance in an older plant.
Since no 3D model of the original control valve was available, 2D drawings and contours from a recreated parts list using the original data sheets were used to model one. When applied in the simulation, this model duplicated the old valve’s performance very closely to the licensor’s experience, validating the CFD modeling technique developed by Flowserve.
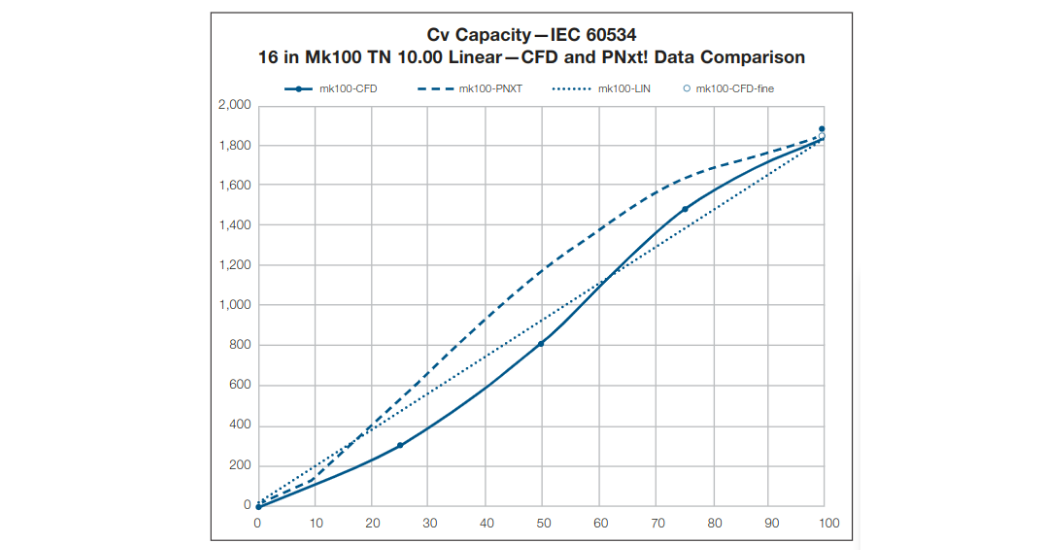
Proposed Mark 100 valve, linear, published and modeled flow curves
Flowserve then moved on to validating the performance of the latest Mark 100 valve via modeling under the same process conditions. The results showed that Flowserve could closely match the expected performance and provide flow curves meeting the licensor’s specifications for process control.
The next step was to scale up the valves for a new high-capacity plant design. During this process, the collaboration team discovered process requirements and control solution inconsistencies, which were promptly corrected.
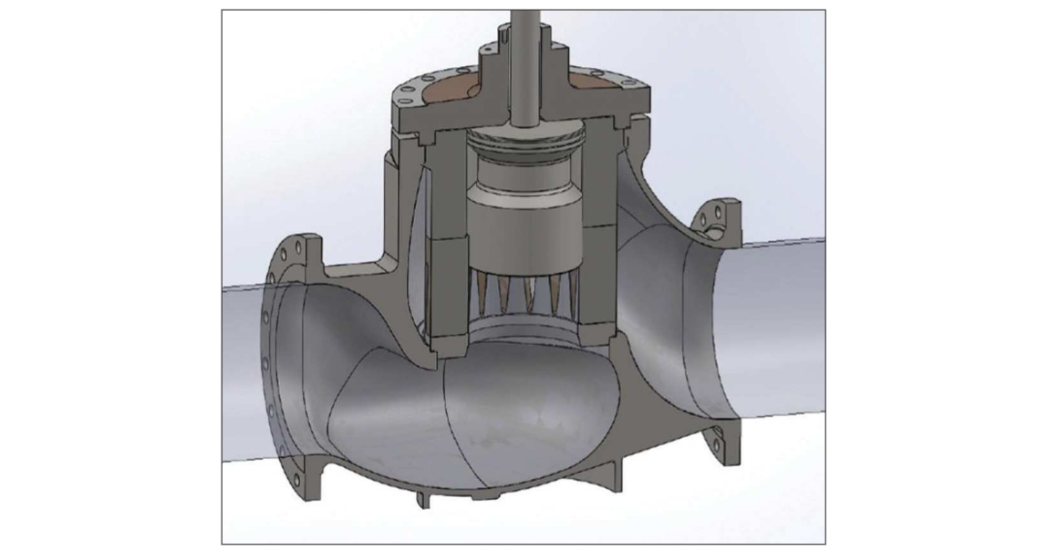
Mark 100 valve, fully open
Resolution
Fortunately, the design specifications had not been finalized. With the inconsistencies addressed, the collaboration team avoided issues with startup and control that would have followed in the future.
This example demonstrates how Flowserve’s role as a system solutions provider can go far beyond the valves, pumps and seals themselves. Collaborating as early as possible enables designers and operators to reap the full benefits of Flowserve’s expertise, thereby avoiding unplanned start-up delays, reducing production of off-spec quality product, optimizing energy consumption through precise controllability, and promoting faster speed-to-market.
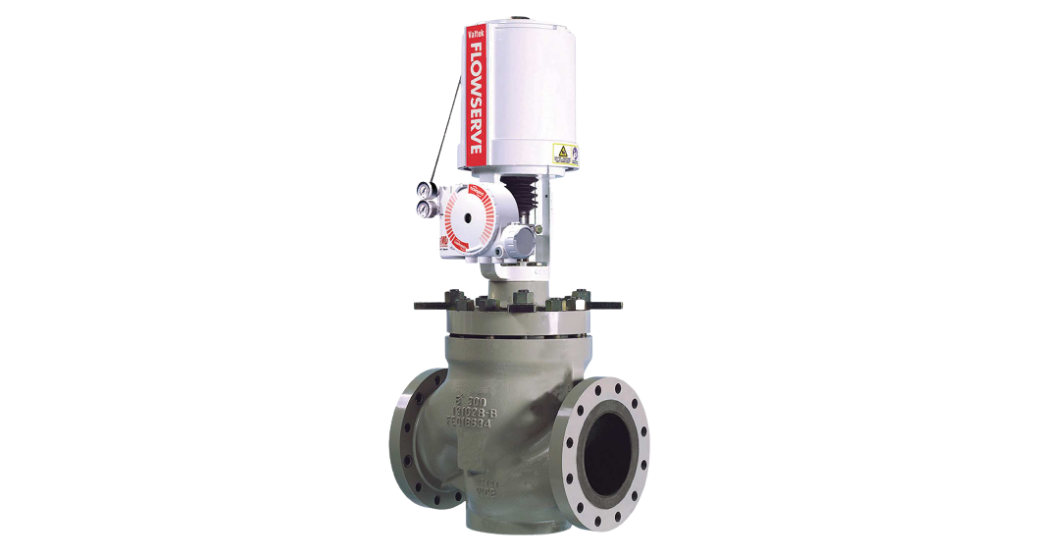
Typical Flowserve Mark 100 control valve
The Mark 100 valve solution exemplifies the benefits of this collaborative approach. In this case, it reduced the potential for off-spec production while improving plant availability and overall specific energy consumption (energy per unit of product produced). As the drive for energy transition grows, collaboration with Flowserve can help you streamline similar start-ups, maximize energy efficiency, minimize waste, solve critical problems, and reduce costs.
In addition to assisting with the process design, Flowserve’s RedRaven advanced internet of things (IoT) valve conditioning monitoring program can help ensure valve equipment continues to run as intended throughout its entire lifecycle. This real-time equipment visibility makes it easy to prevent failures, increase uptime, lower maintenance costs, and improve safety across all your sites.
Whether you’re a licensor, operator or EPC, it’s to your advantage not just to choose an equipment supplier, but a dependable partner with the experience, resources and know-how to help you achieve your objectives — without having to experience costly negative lessons.
Flowserve is that partner. Just as this engagement added value to a long-term relationship with a process technology licensor, Flowserve continues to help many other global operators mitigate their most critical challenges in a wide variety of industries
Comments