Are you using the best industrial coating to protect equipment from specific types of corrosion and erosion?
Protective coatings are primarily used in the Mining and Ore Processing industry for the wear protection of metal equipment. The most common wear issues in this industry are abrasion and corrosion.
When you are selecting a protective coating option, there are many technologies available. Defining the needs of the application will simplify the selection greatly. In this post, you can learn how to use the environmental conditions associated with an application to determine the best solution.
Types of Metal Wear in the Mining Environment
The predominant form of metal wear in mining and ore processing is abrasion which can be classified as either:
- Gouging abrasion
- High-stress grinding abrasion
- Low-stress scratching abrasion with erosion-corrosion
Within each process area, you must consider various criteria first when attempting to select a wear-resistant technology.
Goughing Abrasion
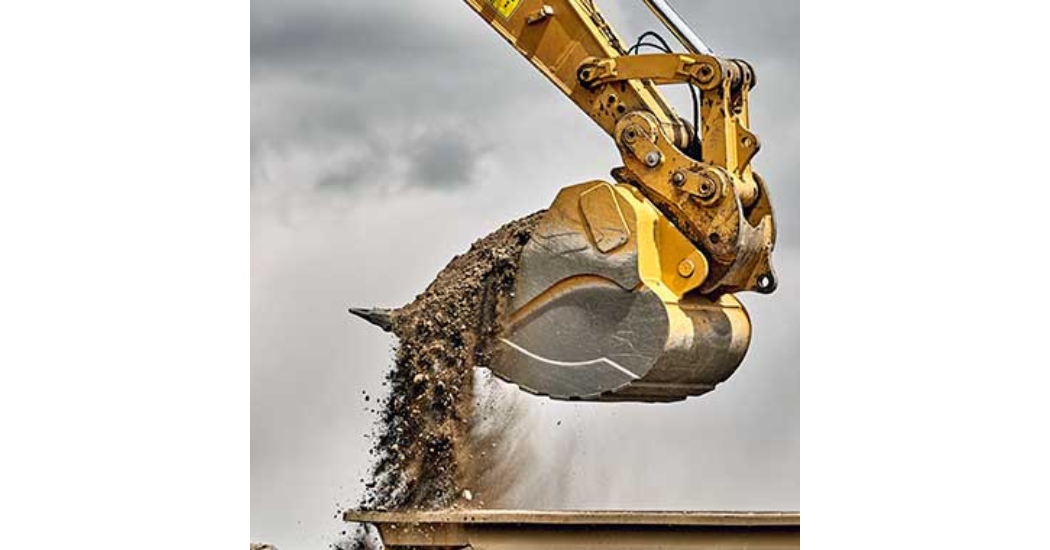
Gouging abrasion is indicated by gross surface indentation and possible removal of sizable metal fragments.
Equipment Example: Drag Line Buckets, Excavators and Crushers
Wear Issues: The shearing or plowing nature of the attack that drives coarse, >6” particle size, abrasive ore into the equipment under high load.
- In many ways this is similar to a cutting tool used in a machining application that cuts a furrow or groove, on a macro scale, into the softer metal.
- In this form of wear, the metal surface is first plastically deformed and then work-hardened so that it becomes more resistant. The high hardness surface then deflects further intrusion or cutting.
Best Coating Choice: Coatings with high hardness and work hardening properties such as martensitic as well as hi chrome, and manganese alloys and chrome carbide-weld overlayments.
High-Stress Grinding Abrasion
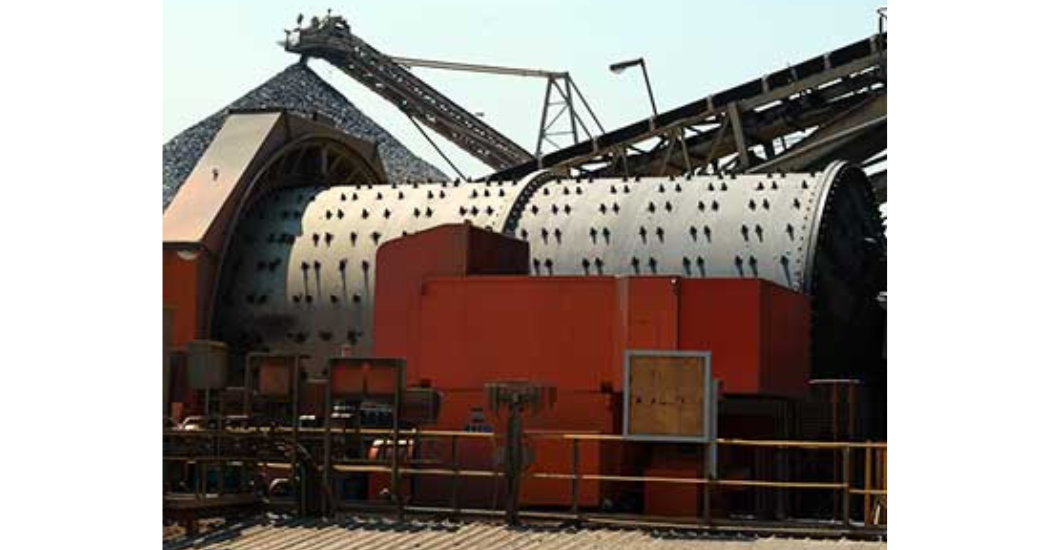
Occurs when the abrasive is crushed between two opposing surfaces.
Equipment Example: Crushers and Grinding Mills
Wear Issues: Abrasive particles are compressed between two opposing faces during the process of size reduction to liberate the valued ore from the gangue.
In this step <6” ore bodies are ground to allow further liberation of the valued ore phase.
The stress is primarily transferred to the grinding media which should have a high hardness to resist micro fracture.
Best Choice: An alloy with high levels of marteniste to resist fracture
Low-Stress Scratching Abrasion With Erosion Corrosion
Equipment Type: Slurry Pumps, Chutes, Agitators, and Cyclones
Wear Issues: Free flowing smaller particles impinge upon and move across a surface, cutting and plowing grooves similar to that seen in gouging wear, but on a micro scale.
- Stress forces are considerably lower than in gouging or high stress grinding so wear rates are lower.
Accelerated loss may be influenced by chemical attack due to slurry solutions (high chlorides, sulfates, acidic leaching solutions, etc.) that may be associated with the processes used to extract, concentrate and refine the various ore bodies. - The weakly bound oxides that form on the surface through electro-chemical corrosion reactions are easily worn away and new oxides form reducing the integrity of the base metal.
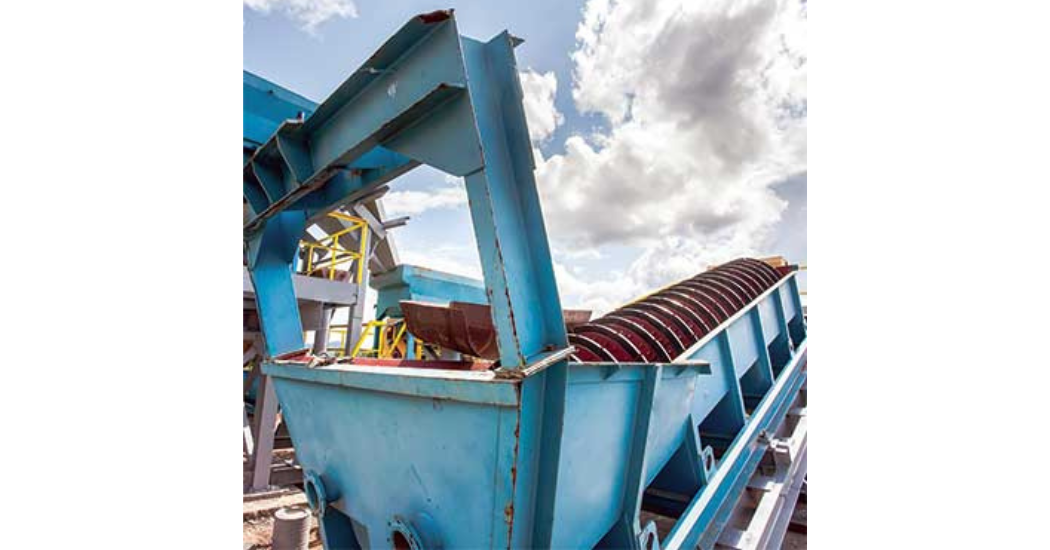
Grooves similar to that seen in gouging wear, but on a micro scale.
Best Choice: Alumina ceramics can be used to impart high hardness surfaces in low angle of impingement conditions. If high angle of impingement is expected then the brittle nature of the ceramic could be replaced with a softer elastomeric (rubber or urethane) or reinforced polymeric (epoxy) coating. These materials have a more ductile nature that prevents fracture but have a wear rate is sufficient to resist the sliding/scratching effect as the particles move over and across the surface.
Table 1: Coating Selections by Abrasion Type
The following table provides clarification as to which characteristics will need to be considered when selecting a wear resistant coating:
Comments