What are reciprocating pumps?
Positive displacement (PD) pumps are equipment that traps a fixed volume of fluid and physically moves it through a system. Reciprocating pumps are a more specific type of PD pump that uses the repeated back-and-forth motion of a piston, plunger, or diaphragm. This cyclic motion is referred to as reciprocation and is the mechanism by which fluid is driven through the pump.
The nomenclature of a reciprocating pump is derived from the component which drives pressure. In a piston pump, the primary component is a cylinder, or piston, with a seal about its outer diameter. A smooth rod known as a plunger moves through a stationary seal in a plunger pump. For a diaphragm pump, a flexible element called a diaphragm expands or contracts.
How does it work?
A piston, plunger, or diaphragm is a primary component of a reciprocating pump. This works inside a chamber which defines the ultimate pump volume. A connecting rod is attached to a motor crank on one end and the piston, plunger, or diaphragm on the other. A suction pipe allows fluid to be drawn into the chamber, while a delivery pipe allows fluid to be discharged. Inlet and outlet valves check the flow of fluid into and out of the chamber.
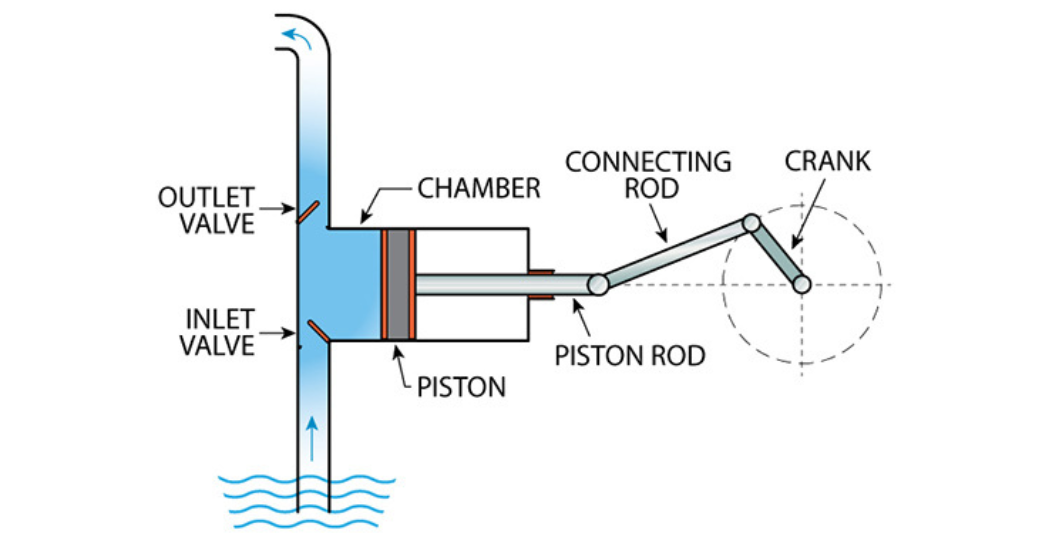
Figure. Piston Pump Diagram
At a high level, the actions of a reciprocating pump can be divided into two phases:
- Suction phase: The piston, plunger, or diaphragm is pulled back which increases chamber volume and thereby creates a vacuum. This process opens the inlet valve and closes the outlet valve. Vacuum acting on the chamber pulls fluid through the inlet.
- Compression phase: After the piston, plunger, or diaphragm has reached its maximum displacement it is then pushed back into the chamber. The inlet valve is closed and the outlet valve is opened. Fluid is then discharged under pressure through the outlet.
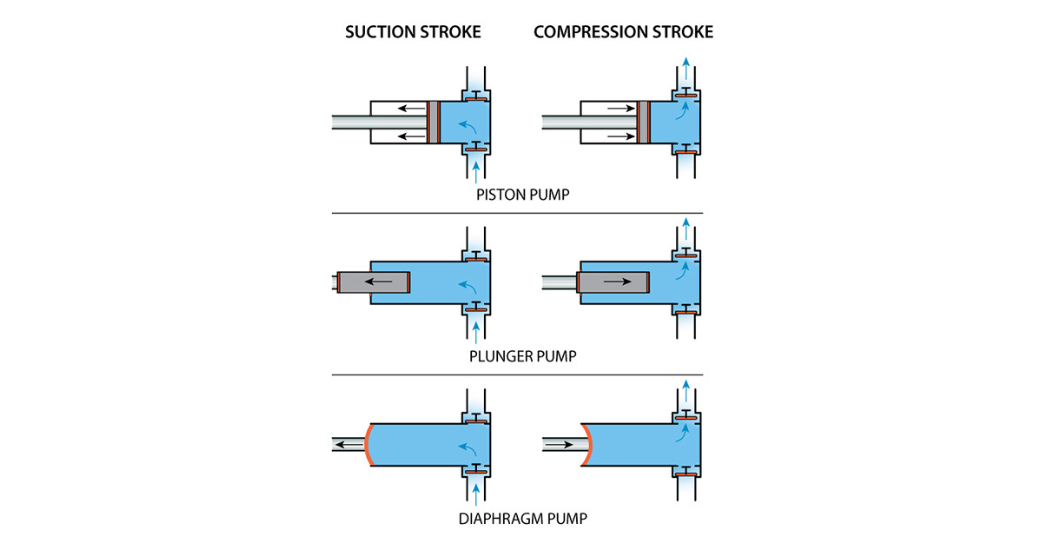
Figure. Suction and Compression Phases
What are its advantages?
Reciprocating pumps are capable of producing tremendous pressure, with some designs generating more than 69Mpa (10,000psi). They also have a fixed volume of fluid displacement at a given speed which allows them to perform well in low flow applications such as dispensing and metering. Reciprocating pumps are effective in handling high viscosity fluids such as paints, oils, and resins. They can also handle fluids containing solids that might otherwise erode components of a high-speed rotary pump. Diaphragm pumps in particular can be used for handling of especially aggressive chemicals.
While there are several advantages to reciprocating pumps, a disadvantage is the production of pressure pulsations created by this reciprocating motion. Pulsation dampeners can be installed to minimize damage to the pump itself and surrounding systems. Another disadvantage versus rotary pumps, is the relative maintenance required. While mean time between maintenance (MTBM) may be less, the cost and time of repair is still relatively low.
Where are they used?
Reciprocating pumps are used across numerous industries including Oil & Gas, Chemical Processing, Automotive, Medical, and others. These may be overlooked as they are in some cases used in equipment with which we are familiar.
A piston or plunger type pump is used when drilling in the oilfield to deliver a fluid called mud. This mud may consist of many suspended particles. It acts to cool the drill bit, prevent the drilled hole from collapse, and return drilled shavings to the surface.
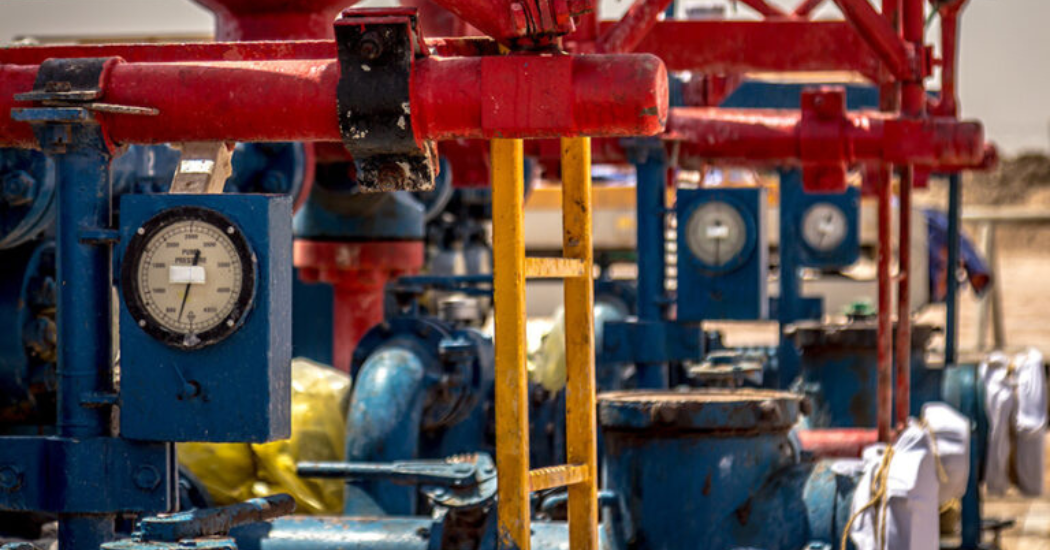
Figure. Oilfield Mud Pumping
High performance liquid chromatography (HPLC) is an analytical technique used to identify and quantify the components in a mixture. It is an important tool in pharmaceutical applications for evaluating formulations. The plunger pump may exceed 138Mpa (20,000psi) through a fluid column.
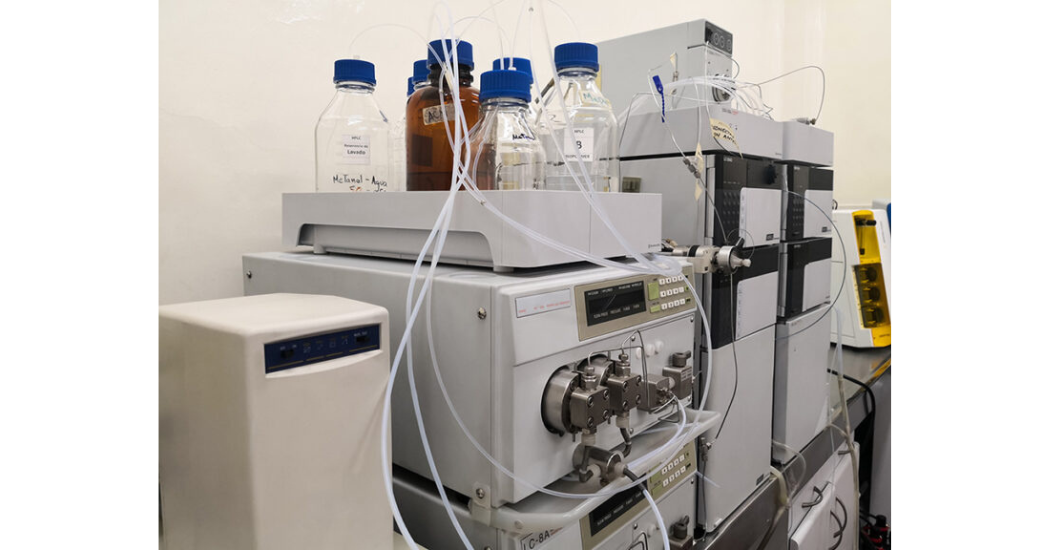
Figure. HPLC Testing
Chemical injection is used to inhibit deposits, limit corrosion, and keep systems flowing. This is becoming more commonly used in upstream to midstream operations in Oil & Gas. Chemicals are delivered in doses and include solvents, corrosion inhibitors, biocides, and many others.
Paint is used across industries to color and protect structures and equipment. Spraying affords even and efficient application of paint, with the pump an important part of that system.
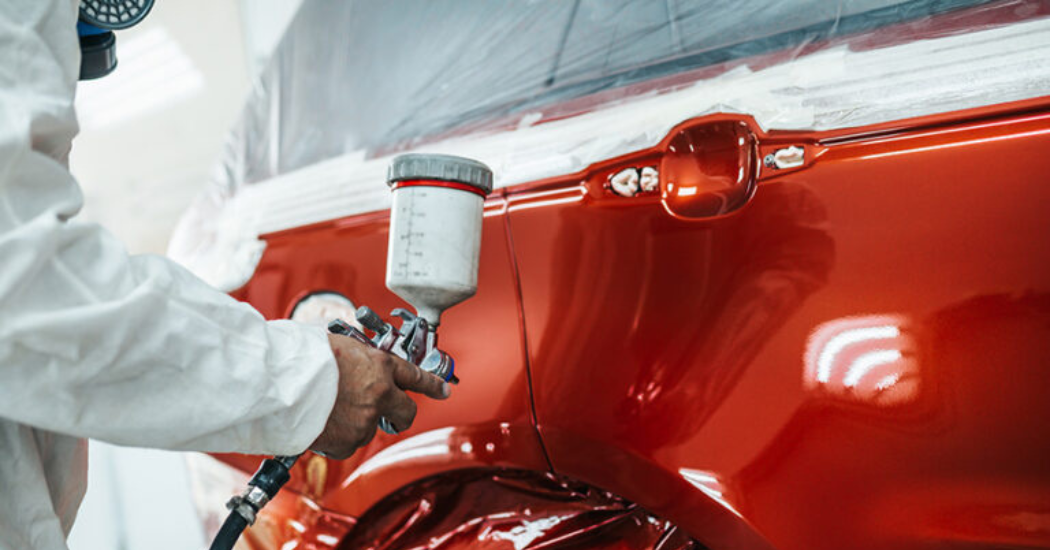
Figure. Paint Spraying
Water blasting is a technique used for cleaning internal and external surfaces. Results are comparable to other techniques which use cleaning agents and abrasives potentially harmful to the environment. Pressure driving the water stream can reach 172Mpa (25,000psi).
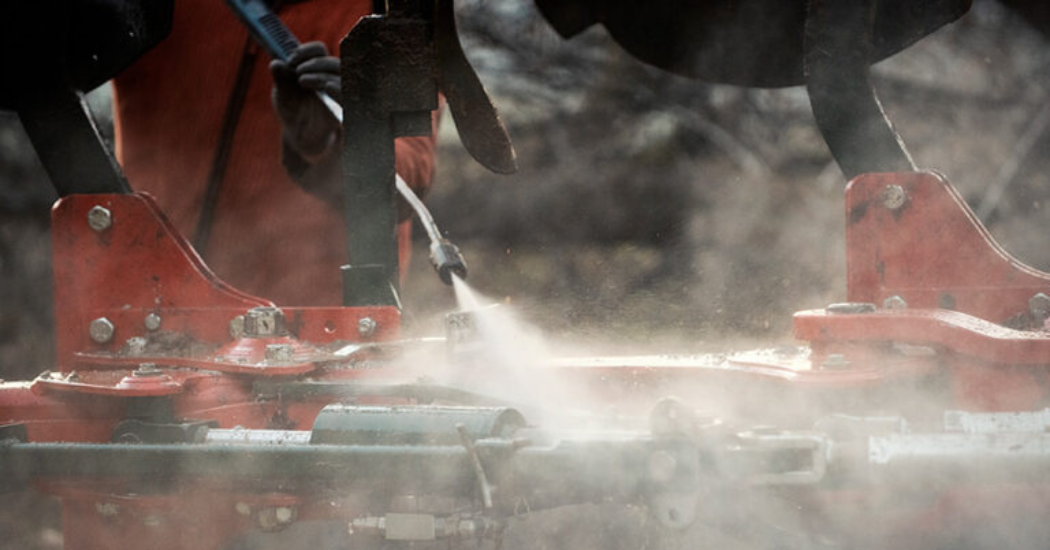
Figure. Water Blasting
Piston and plunger pump sealing challenges?
The seal around the piston, stationary seal through which the plunger moves, or diaphragm must be maintained to avoid leakage. Sealing challenges for diaphragm pumps can be somewhat different, and in order to focus on piston and pump sealing challenges see below for some of the conditions that may limit seal life and cause frequent MTBM intervals:
- Incorrect sealing solution: Appropriate material selection is necessary to ensure compatibility with the fluid medium and across the application temperature range. Design geometry must ensure effective sealing against pressure.
- Inappropriate seal installation: Guidelines are helpful to ensure appropriate and consistent installation. In some case, tools may be needed to help facilitate the process.
- Lubrication is insufficient: Insufficient lubrication can lead to excessive friction, high heat, and subsequent seal failure. Material selection is essential and lubricant injection may be needed.
- Misalignment of piston to seal bore, or plunger to packing space: Eccentric loading can result in poor sealing. Centralization devices located close to the seal can help minimize this.
- Excessive wear in seal bore or on plunger: Seal material or fluid media can be particularly abrasive. Hardening or coating of seal bore or plunger may be needed.
- Presence of solids in medium: While reciprocating pumps are relatively capable of handling media with particulates, excluder devices may be warranted to protect seals and sealing surfaces.
Seal stacks provide redundant sealing elements and are good solutions for reciprocating pump applications. Spring energized seals (SES) or spring loaded packing can provide further benefit. One reason is they require no adjustment to the gland which can remove operator error. Another is that they allow for expansion which may occur due to thermal growth or application of system pressure.
If you have any questions about seals for reciprocating pumps, contact your local Chesterton office or “Ask the Expert” service. They can help with material selection, geometry, and overall system design to ensure optimal performance of your equipment.
Comments