Are you unsure about the ideal sealing technology for your pump or agitator application? In this comparison, let’s explore the benefits and effectiveness of mechanical seals versus pump packing to help you make an informed decision.
Long ago, companies didn’t want to switch to mechanical seals because of the complicated installation and need to completely disassemble the equipment. The invention of cartridge and split mechanical seals effectively eliminated those dilemmas, but many operations have stayed with pump packing out of sheer habit in situations in which seals would provide a better return.
Likewise, some customers will try to make a mechanical seal fit into an application where packing makes more sense. This article provides information on making the best sealing choice based on operational priorities, applications, and budget.
When Mechanical Seals Are the Clear-Cut Choice
For many types of equipment, applications, or conditions, using a mechanical seal is really the only effective sealing option. This decision focuses on the safety or environmental issues associated with leakage.
A mechanical seal, and more specifically a double mechanical seal, should always be used when the pumped fluid presents a safety, health, or environmental hazard. Packing cannot be 100% leak free. Even when leakage isn’t visible, harmful vapors could be escaping. This is also true for single mechanical seals.
Establishing Priorities
However, often the decision to use packing vs. mechanical seals in pumps, agitators, and mixers is more blurred and requires a careful assessment of what is most important to your operation.
These are some factors to weigh when looking to replace packing with a mechanical seal:
Reliability & the Cost of Downtime
If reliability is a primary factor, the clear choice is mechanical seals. And although the initial investment is considerably higher than pump packing, it will pay off long term. The decision to go with a mechanical seal comes with a level of commitment to achieve a true return-on-investment. A good seal vendor will help you select the correct seal design, make sure you have the most effective installation/support setup for the conditions, ensure that the equipment is in the proper condition to support the mechanical seal, and outline the regular maintenance schedule. These commitments will ensure that the seal investment will pay off for many years.
Leakage/Loss of Valued Product
While compression packing doesn’t necessarily need to leak, typically there will be some leakage. Depending on the application and the fluid being sealed, this may be considerable. And due to the typically lower lifespan of packing, the leakage associated with failure will occur more frequently. In some instances, this is not an issue. However, it is often a safety issue due to the type of product or the volume of leakage (and/or lack of maintenance staff to routinely clean up the mess).In some cases, our customers find that the savings in lost product actually pays for the cost of the new mechanical seal very quickly. We recommend measuring the loss of product for a single pump for a week (including the clean-up maintenance labor)…then calculating for the year, multiplied by similar pumps across your operation. The results are often eye-opening and often make for an easy return-on-investment conclusion for moving to mechanical seals.
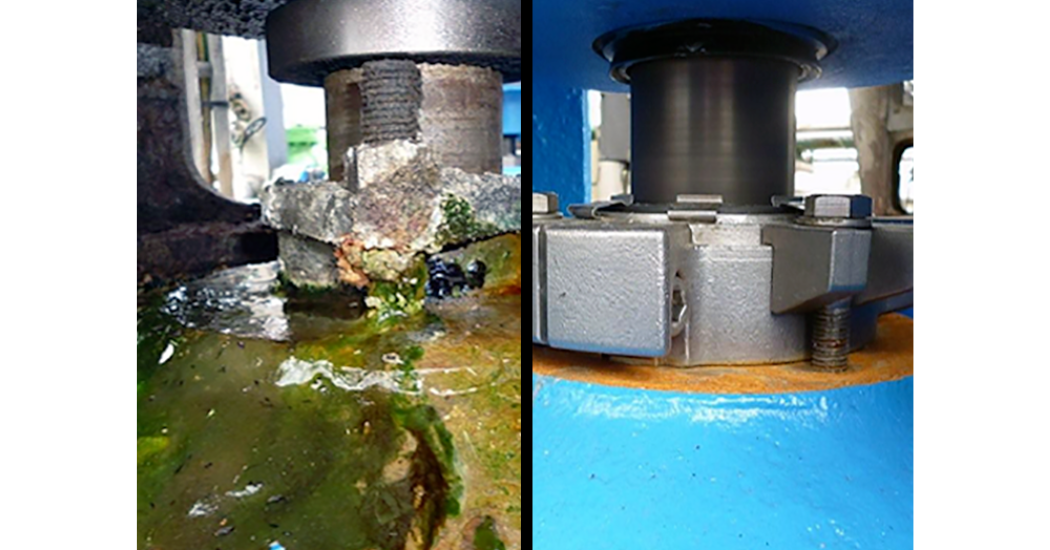
The decision to move to mechanical seals is often driven by the impact of constant leakage from packing on the shaft; bearings; safety; and maintenance.
Maintenance Support
Packing requires more labor to routinely adjust and repack as well as the frequent leakage cleanup noted above. Is your organization adequately staffed? This, too, may be a deciding factor.
Stuffing Box Accessibility
Because packing will wear over time and require gland adjustments, the stuffing box must be accessible to maintain the packing.
Product Contamination/Dilution
Since many sealing applications require the packing to include a flush to cool, the cost to remove the flush water or the possible contamination may be an issue in some applications.
Premature Bearing Failure
Maintenance staffs often use a water hose to rinse leaking product away from base plates, and the excess moisture from failed packing can wreak havoc with bearings.
Sleeve damage is a frequent occurrence and costly— not only because of the sleeve cost, but also the expense involved in the sleeve removal. Packing removal almost always means changing the bearings and wear rings. Many parts also get broken or lost when pumps are disassembled.
When Packing is the Choice
In many cases, compression packing IS still the right answer for rotating equipment applications. When the factors above are not an issue and adequate staff is available for adjustments and repacking, packing offers a low up-front cost and fairly simple maintenance. And although some say that packing requires more energy than mechanical seals, our testing has found that they are essentially the same.
- Cost: Packing provides a lower up-front cost than mechanical seals. The benefit of the mechanical seal has to outweigh this cost. This can be more difficult when the equipment is large, or requires more costly metals and elastomers.
- Ease of installation/Turnaround time: Installation of packing rings does not require decoupling of drive shaft unlike in case of installing the non-split mechanical seals. This leads to a relatively easier installation and shorter turnaround time.
- Equipment condition: Mechanical seals typically require equipment to be in good condition to operate reliably. This includes shaft finish, pump/driver alignment, cavitation, and vibration.
- Radial/axial motion and misalignment: Most mechanical seals tolerate very little radial movement or misalignment, and little to no axial movement. If the shaft is often moved axially, such as with many paper refiners, packing is often the only option available. While these issues can sometimes be addressed with the right choice of mechanical seal and support system, packing is typically the optimal choice.
- Plant-wide solution: Packing offers less complexity in terms of inventory/maintenance practices.
One area where these factors align is in large slurry pumps, such as those found in the mining and ore processing industry. Though mechanical seals will provide an excellent seal for some of this equipment, the confluence of the expense due to large equipment size, large shaft movements due to large particles impacting the impeller, and abrasive media leads to most customers choosing to pack their equipment.
Today’s packing advances also mean that packing will last longer in many situations and require fewer adjustments than the basic options available in the past. New materials such as carbon fiber, advanced lubricants, and new braiding technology translate to longer packing life and fewer maintenance and equipment wear issues. Learn about these different technology advances in an upcoming post.
Meet Raman Hanjra
Raman Hanjra is Global Product Line Manager of Packing & Gaskets for A.W. Chesterton Company. He holds a BS in Mechanical Engineering and an MBA in Product & Market Development and Supply Chain Management. He started his career as a sales engineer for mechanical seals and has held various sales, marketing and product leadership positions globally. In his free time, Raman enjoys photography, golf, and reading about international trade and macroeconomics. Raman.Hanjra@chesterton.com