Many teams are surprised about the savings delivered by comprehensive monitoring. Comprehensive monitoring of rotating equipment can pay off for maintenance teams in many ways, one of which is “watching” equipment for potential issues 24/7.
When all factors involved in monitoring equipment – surface temperature, vibration acceleration or velocity, process pressure, and process temperature – are tracked by the sensor, users can easily pinpoint potential problems early and fix them before sometimes catastrophic and expensive failures of the seal, the pump/mixer, or agitator, and other components.
Tracking these conditions can also help teams identify the source of failures not solved by in-person inspection. On a monthly basis alone, these new abilities can save tens of thousands of dollars at a single plant.
For this reason, many maintenance teams are adopting innovative technology such as monitoring of rotating equipment to transform their ‘preventative teams” into “reliability teams.”
Typical Maintenance Practices
Maintenance practices for industrial equipment in the process and service industry essentially fall under three different types:
- Reactive: When maintenance is reactive, the equipment is operated until failure. In a reactive approach, there are hidden costs such as increased plant downtime, interruptions in delivery to customers, wasted time waiting for material tools and labor, high overtime costs, high inventories, or often out-of-stock inventories.
- “Text Box” Preventive: When maintenance is preventive, the equipment is serviced/repaired at pre-determined times. To set preventive maintenance schedules, a conservative estimate of the expected life of the equipment is needed. Unfortunately, these estimates can be costly because the replaced components may have worked for a longer period. Issues may go unnoticed, resulting in failures and sometimes unplanned shut downs.
- Predictive: When maintenance is predictive, identifying when and why a component will fail becomes possible. In a predictive approach: spare parts are ordered just in time; shutdowns are planned and only when necessary; and the rates of failure and damage to equipment are lower, resulting in more safety and reliability in the equipment.
The Old Method
For rotating equipment, reactive and preventive maintenance has historically been the norm. The most common method used is monitoring vibration and surface temperature. These measurements are often performed by a vibration-trained technician taking point-in-time measurements and following a fixed schedule.
The technician walks around the plant collecting measurements to identify the specific signature of the vibration and to provide maintenance recommendations. However, the worst vibration events do not always correspond with the technician’s schedule. Therefore, with this vibration monitoring method, the technician could fail to observe harmful vibration events happening on the equipment during off hours.
The New Method
With smart monitoring sensors, the ease of data collection, visualization, and interpretation is important to quickly identify changes in the equipment.
Using smart monitoring sensors helps maintenance become predictive where proper equipment adjustments can be made as needed and when needed. Investing in the right tools can greatly simplify and improve pump maintenance.
New Maintenance Insights with the Chesterton Connect™ Sensor
With over 135 years of experience in pumps and seals, A.W. Chesterton Company recently developed a smart monitoring sensor for rotating equipment to detect factors affecting the seals as well as bearings and to facilitate equipment predictive maintenance. This product is now being use worldwide to help maintenance teams achieve a new level of reliability and cost savings.
Chesterton Connect is a 24/7 wireless smart monitoring sensor that detects variations in:
- Process pressure and temperature: caused by restrictions in the suction, discharge, seal chamber, double seal piping plan, shaft speed, etc. to determine what is happening inside the seal/pump and to avoid (or find) the root cause of seal failure.
- Vibration and surface temperature: caused by cavitation, equipment misalignment, impeller imbalance, and other issues, to determine when is the best time for the technician to assess the equipment vibration signature.
The Chesterton Connect sensor is a solution that provides easy-to-use all-inclusive monitoring of all rotating equipment to increase equipment reliability, safety, and performance. Installation takes less than two minutes; 24/7 data collection is easy, and the user-friendly mobile app allows for easy and safe data visualization and interpretation.
The following are cases where the Chesterton Connect sensor was used and immediate equipment savings were achieved:
Case Study #1: Identifying Seal Flush Conditions
A waste management plant was running a heavy-duty centrifugal pump to process its slurry. Despite installing a robust mechanical seal, the pump’s reliability was not satisfactory, and the seal continued to fail. Something was clearly not correct with the operation, but nobody could provide an answer.
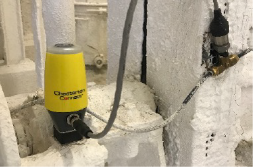
Chesterton Connect installed in flush line
The local Chesterton representative recommended a Chesterton 155 Mechanical Seal further protected by a SpiralTrac™ active throat bushing.
A Chesterton Connect™ sensor was installed to monitor the process parameters in the seal chamber to understand the causes of repeated seal failures.
The Chesterton Connect was set to monitor the seal 24/7 and revealed that during the night shift, when switching off between pumps, the operator often forgot to switch on the flush water/barrier water. Based on these findings, the staff was able to make corrections to the work schedule, increasing overall reliability. The pump is now running successfully without failures.
Case Study #2: Pump Vibration Issues Solved
At a paper plant, a critical hydrate slurry pump with a high concentration of solids had infrequent high vibration which posed a threat to equipment reliability. The vibration expert could take only point-in-time measurements and was unable to detect when the vibration reached its maximum.
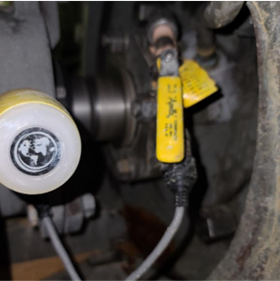
Hydrate slurry pump application
The Chesterton Connect sensor was installed on a Chesterton 180 Mechanical Seal to monitor stuffing box pressure and temperature, as well as on the outboard radial bearing to monitor vibration and surface temperature.
Using the Chesterton Connect sensor, the user was able to monitor vibration 24/7, access historical data, and understand precisely when the high vibration was happening.
Thanks to the Chesterton Connect sensor’s real time alerts, the vibration expert was called when the vibration was at its peak, and the customer was able to spot the issue causing the high vibration.
The customer was able to apply the proper maintenance assessments successfully to prevent the high infrequent vibrations from damaging the critical equipment.
Product Manager at A.W. Chesterton Company
Juan Cid is a Global Product Manager at A.W. Chesterton Company for the Mechanical Seals and IIoT product lines. He has over 5 years of experience designing and managing products for rotating equipment. Juan holds a bachelor of science in mechanical engineering and a master of business administration degree from the University of Massachusetts.
Comments