Coal processing involves transporting coal in various stages as bulk coal is refined into fine particular coal suitable for burning. The impact on equipment can be significant. Ever-persistent abrasion and wear takes a major toll on pulverizers, conveyors, chutes, screws, and other equipment. It can ultimately cause unexpected, costly downtime and/or greatly reduced equipment life.
In this post, you will learn how using industrial coatings on equipment and equipment areas used for coal processing can dramatically improve efficiency and asset life, often saving tens of thousands of dollars annually.
Coal Processing Equipment Affected by Abrasion
Coal is a major source of energy that generates electricity around the world. It comprises up to 40.8% of the electricity generation globally and 30.4% of the electrical generating capacity in the United States. To maximize profits and avoid significant fines in coal production, many power plant management teams focus improvement efforts on boiler efficiencies and reducing hazardous flue gas emissions. However, coal handling and coal preparation associated with combustion also have a significant impact on plant efficiency and operational costs.
From the moment coal arrives at the power plant, it is transported around the facility undergoing several processes to change bulk coal into fine particulate coal suitable for burning. Bulk coal coming into a power plant can be large and coarse in size (>3”). Milled coal to be sent to the boiler must be uniformly about the size of a grain of salt to ensure optimum combustion.
The numerous stages that the coal passes through on its way from the coal yard to the boiler entail:
- Conveyance by belt, screw, chute, etc.
- Bunkering/silo storage
- Metering to pulverizers
- Grinding/milling in pulverizer
- Classification in pulverizer
- Pneumatic conveying to the boiler
Each of these processes involves equipment that can often be dramatically compromised by the abrasive nature of the coal and the effort to process it.
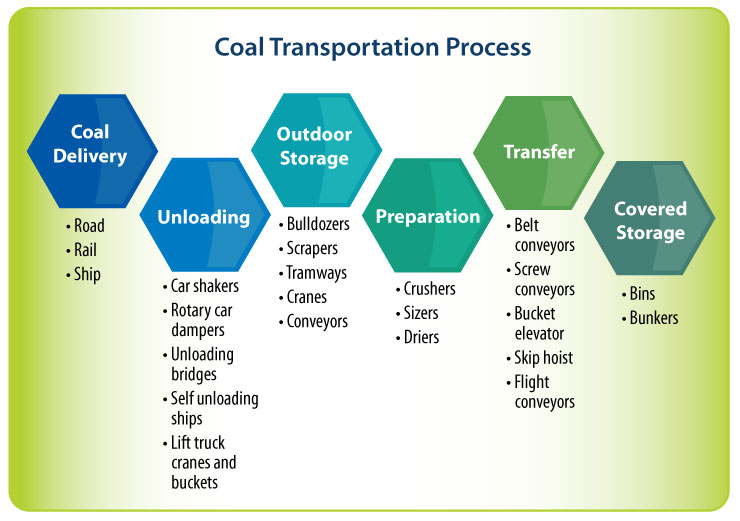
Table 1: Areas in the coal transportation process that can be impacted by abrasive/corrosive forces
Causes of Wear
Coal is primarily composed of carbon, hydrogen, oxygen and nitrogen along with sulfur with traces of iron in the form of Fe pyrites. In addition, coal contains high levels of chlorides. These elements in coal make it an abrasive as well as a corrosive material to unprotected steel. If left unprotected, equipment will experience significant wear, ultimately causing failure of the structure or the process equipment in contact with it.
Wear and corrosion rates are dependent on several factors:
- Sulfur and chloride contents affect corrosivity
- Hardness varies between lignite, sub-bituminous, bituminous, and anthracite coals which impact wear rates
- The variables associated with transport such as velocity, drop distances, impact angles, etc.
As electricity production increases, coal consumption grows. At the same time, wear and corrosion rates increase as well. It is imperative to adequately protect the equipment and structures in contact with the coal as it passes through the plant to extend equipment life and maintain tolerances set by the manufacturer.
Protection Options
There are several acceptable solutions that are typically used in the coal industry to protect equipment from these forces:
- Abrasion-resistant (AR) metal plates
- Ceramic tiles /cast basalt
- Corrosion-resistant industrial coatings
Welding Plates: Time Consuming & High Risk
Welding abrasion-resistant (AR) plates is a time-consuming process that requires the equipment to be shut down for long periods of time. The lack of redundancies in coal handling systems means that plant personnel have very limited time to get the repairs completed.
In addition to being a time consuming process, welding AR metal requires specially trained personnel, as well as having a fire watch in the welding area for several hours after the job has been completed. The Powder River Basic Coal Producers’ PRBCUG Fire Control Guide provides guidance on reducing risk of fires in bunkers and mills, but welding should be discouraged whenever possible to avoid fires in the system. In addition, welding in the vicinity of coal powders introduces major concerns from an employee and plant safety perspective.
Ceramic Tiles/Cast Basalt: Good for Limited Applications
Ceramic tiles come in varying thicknesses and work great for sliding abrasion; however ceramic tiles are very brittle and cannot be used in applications where impact exists. Additionally, ceramic tiles cannot be used in all applications, as their size and shape does not allow them to be used in irregularly shaped pieces of equipment such as screw conveyors. Basalt is typically slipcast directly to the pipe. Repair is difficult and unreliable so should be avoided in areas where high maintenance is required.
Coatings: With Proper Application Can Significantly Extend the Life of Steel Surfaces
Polymeric ceramic-reinforced coatings provide a versatile solution when abrasion and corrosion protection of metal surfaces is needed. Their benefits include:
- May be applied with no heat/hot work permit required
- Cure in a short period of time allowing for minimum downtime and minimum disturbance to the process.
- Extend the operational life many times over unprotected steel surfaces
The range of coatings available is quite large and versatile so selecting the appropriate coating based on the temperature, velocity, flow rate, and corrosive/abrasive nature of the particulates involved is critical
Coatings come with their set of challenges as well. Prior to application, appropriate surface preparation based on the manufacturer’s recommendation must be performed to ensure that the coatings perform as they are designed. Poor surface preparation can lead to premature failure of the coating.
Below are two case studies from the field that demonstrate the impact that the proper resurfacing and coating can have on profitability and reliability:
Case Study: Abrasion Mitigation on Eight Coal Mills
Case Study: Refurbishing/Coating Coal Pulverizer Liner
Get Assistance
A.W. Chesterton Company offers a variety of high-performance abrasion-resistant coating solutions through ARC Industrial Coatings that are used in the most demanding applications. Their experienced team is on call to help. Contact them for an on-site plant visit or email Ask the Expert desk for assistance with a specific application.
Learn More – Download This Free E-Book: Flue Gas Desulfurization Systems: Using Protective Coatings to Reduce Energy Demands
About the Author:
Hicham Saade is the Global Product Manager at Chesterton ARC Efficiency & Protective Coatings Business Group. Hicham has been with Chesterton for just over 2 years. Hicham is a NACE CIP Level I inspector and has over 10 years of product management, engineering, chemical industry, EH&S, sales and quality experience. In his free time Hicham enjoys traveling and spending time with friends and family.
Comments