What is a Food-Grade Grease?
Greases used to lubricate machinery in Food/Beverage/Pharmaceutical production are governed by special rules to protect product purity, health, and safety. Unlike standard industrial lubricants, the design of food-grade grease and oil must follow strict guidelines for chemical composition established by the FDA under title 21CFR Part 178.3570 “Lubricants with Incidental Food Contact.”
The National Sanitation Foundation (NSF), under DIN Standard V 0010517, 2000-08, has established three classifications of food-grade lubricants:
- H1: Food-grade lubricants used in food-processing involving possible incidental food contact in trace amounts. H1 lubricants are usually what is meant when people refer to food-grade lubricants.
- H2: Food-grade lubricants used on equipment/machinery where there is no possibility of food contact. These are used in utilities or in processing areas “BELOW” the processing line.
- H3: Food-grade lubricants used to prevent rust on hooks, trolleys and similar equipment. These are typically edible oils and are used where there may be direct food contact as part of the operation of the equipment.
Many of the base oils, friction/wear additives, corrosion inhibitors, water displacers, and polymer modifiers that are so effective in industrial grade H2 lubricants cannot be used in H1 designed oils and greases.
Unique Lubrication Challenges in Food, Beverage, and Pharmaceutical Industries
Those who maintain equipment in the food, beverage, and pharmaceutical industries also face some unique lubrication challenges. Not only is this equipment exposed to the same level of vibration, impact, and stress as seen many industrial environments, it is also subjected to constant sanitation involving water exposure, steam, sanitizing agents, and cleaning chemicals. These conditions can wreak havoc on bearings and potentially degrade many standard lubricating H1 greases, leading to unexpected failures and shutdowns.
Below, you’ll learn the best way to select the optimal H1 grease for best performance and reliability.
Considerations with Food-Grade Lubricants
Bearing Lubrication
According to the Bearing Manufacturer’s Association, over 60% of bearing failures are due to lubrication issues. This may be even more of an issue in the Food/Beverage/Pharmaceutical industries.Bearing failure is common
Stainless steel is the ideal material for machinery in the Food/Beverage/Pharma industries because it has the corrosion resistance to tolerate frequent water washowns, sanitizing agents, acid/alkali exposures. It also offers the rust-resistance to avoid contamination of the product. However, most bearings in stainless steel machinery are made of carbon steel due to mechanical ductility. These carbon steel bearings corrode much more easily than the equipment itself, especially under the constant cleaning/water exposure. This frequently leads to premature bearing failure.
To reduce corrosion of the bearings in these industries, stainless steel bearing components are sometimes used. However, this approach has been less than successful. CrNi alloy bearing surfaces tend to gall and work harden. In addition, CrNi alloy bearings may be up to 50% lower in load rating than their carbon steel counterparts.
Choosing the Optimal Food-Grade Grease for Bearings
To effectively lubricate processing and production machinery bearings, it’s crucial to look at the limitations of lubrication technology chosen vis-a-vis service conditions.
- Look at every factor facing the application. What are the specific environmental and mechanical service conditions? Consider:
- Speed and Bearing Size
- Temperature
- Corrosion Factors
- Shock/Vibration
- Metal Wear
- Water Exposure
- What is the current Mean Time Between Failure (MTBF) and what is your goal to improve operational life? If you have a highly problematic application that involves frequent bearing failure, you may have very definitive goals for improvement.
- Next, review the specific technical data for the grease brands you are considering. The performance attributes of a machinery oil or grease can be difficult to assess when reading the plethora of marketing copy and sales information on a product data sheet. As you read the marketing hype, all greases are “SUPERIOR,” “unique,” “water and load resistant,” or “designed for severe conditions.” In reality, when it comes to bearing performance and equipment reliability, it is the grease’s performance data that should be reviewed, interpreted, and guide your decision.
Assessing the Lubricant’s Technical Data
A lubricant should be reviewed on the merits of its mechanical and chemical attributes.
Mechanical
For bearings to work reliably, the bearing components (rollers, balls, raceways, cages, etc.) must be separated by a dynamic film of lubricating oil. While most people look for a grease of a specific consistency such as NLGI #0, #1 or #2, it is actually the base oil viscosity that provides the dynamic lubricating film that separates the bearing components. Full film separation (or hydro-dynamic separation) can occur only if the base oil viscosity and bearing speed are correct for the temperature of the application.
Selecting the correct grease by base oil viscosity is more important than asking for an EP #2 grease. Appropriate charts are available that indicate the correct base oil viscosity and bearing speed at specific operating temperatures. See one example in Figure 1 below.
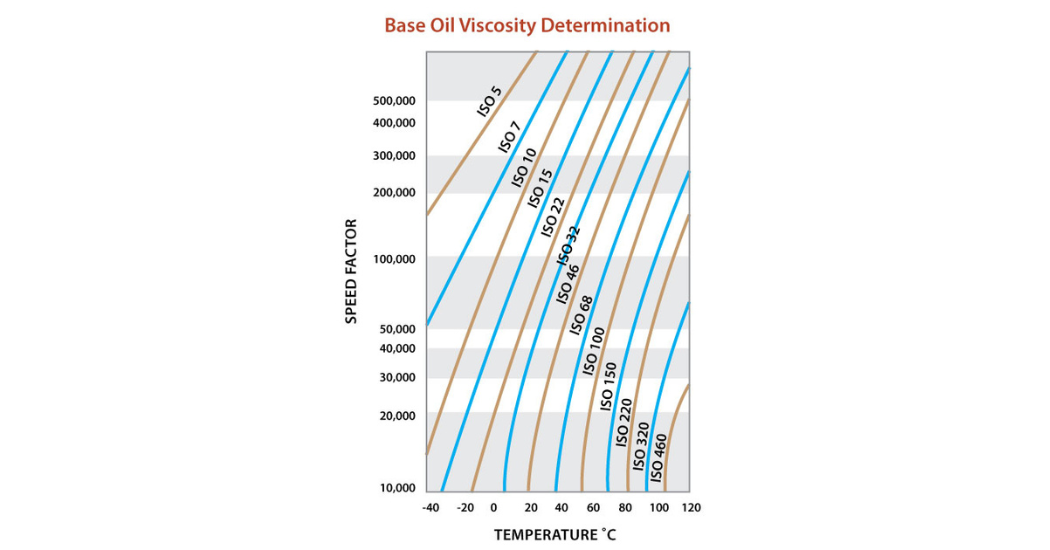
Figure 1: Base Oil Viscosity
Chesterton makes several food-grade greases. These greases have several different base oil viscosities, allowing the lubrication engineer to select the correct viscosity for the application. For example, Chesterton 630 SXCF is a ISO VG 46 base oil which can be used for bearings operating up to 3600 rpm. Higher base oil viscosity greases such as Chesterton 630 SXCF 220 #1 are available for larger diameter, slow rpm bearings.
Chemical
In harsh conditions, the ideal fluid film separation may be compromised. However, a lubricant that is expertly designed with the right combination of performance additives will be able to remain stable during harsh operating conditions and provide supplemental protection to the bearing. Tribology, or the science of reducing friction and wear, is a chemical event in which additives react to the surface of the bearings. This event generates a “passivating” film that protects the bearing from excess load and wear caused by vibration, start and stop, side load, misalignment, and the like.
Additionally, chemical additives can provide corrosion resistance by passivating the carbon steel, and reducing the affect of moisture and corrosive chemical vapors on the bearing metallurgy. A robustly designed grease might also be used for the lubrication of stainless steel bearings to help reduce galling, and permit higher service speeds and mechanical loads.
Ideally, you should review the published technical data that has been derived from a full body of ASTM and or DIN ISO performance testing as exhibited in Figure 2 below. For example, if a piece of equipment is exposed to frequent water washout due to cleaning requirements, one might want to select the grease that has the lowest percentage of water washout. If the same bearings are exposed to corrosive fruit juices, processing acids, and harsh cleaning compounds, we would additionally look for a lubricant that has excellent corrosion resistance as exhibited by ASTM B 117, Corrosion Resistant Testing.
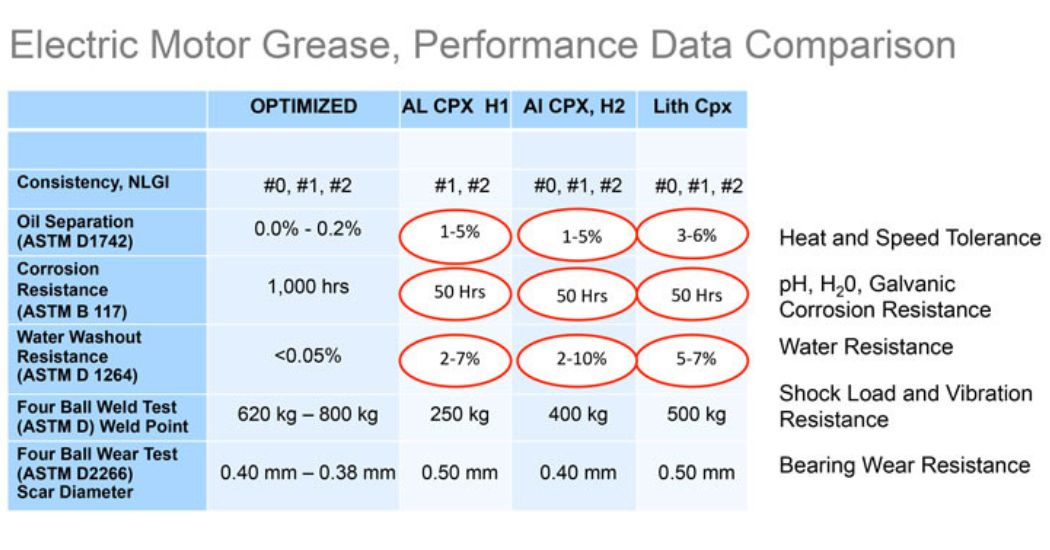
Figure 2: This chart shows the Optimal Target in the second column. This is the ideal goal. The other columns show typical lubricants encountered in the field, but you’ll want to insert the data from competing brands to determine the ideal offering for your application and budget.
Electric Motor Lubrication Challenges
In particular, electric motor bearings play an enormous role in the food, beverage, and pharmaceutical processing industries.
An electric motor bearing is typically lubricated with the OEM-specified Polyurea grease. This can be sometimes be an issue as these greases are formulated with minimal additives over concerns that excess extreme pressure and anti-wear additives may adversely reactive with copper components such as motor windings. As such, performance data of these greases (4 Ball Load/Weld test, Corrosion Resistance test, and Water Washout test) is often LOW as shown in Figure 3 below.
When faced with harsh operating conditions, you may want to consider replacing Polyurea grease with a food-grade, Calcium Sulfonate thickened grease. The optimal Calcium Sulfonate grease would meet the proper base oil viscosity, NLGI consistency, and thermal stability specification while also providing superior resistance to water washout, oxidation, and corrosion. This grease will provide superior lubrication to the motor bearings exposed to corrosive vapors, high humidity and oxidizing agents from frequent equipment sanitation procedures.
For example, the chart below shows how Chesterton’s 630 SXCF Grease, which is a synthetic calcium sulfonate-based grease, compares with the technical characteristics of typical Polyurea greases in the areas of load, water washout, and corrosion.
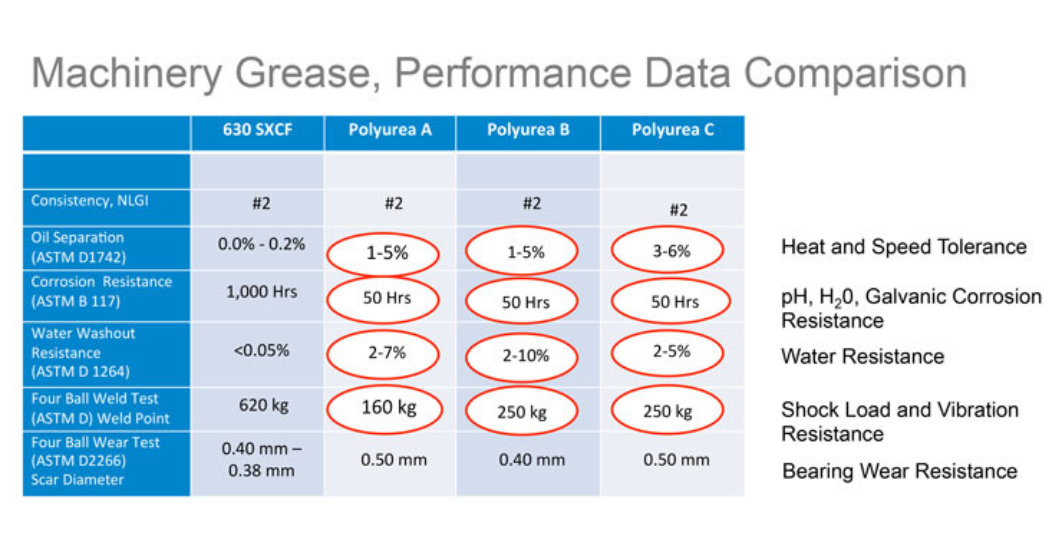
Figure 3: Comparing Machinery Grease
Summary
In summary, choosing food-grade greases for equipment in Food & Beverage and Pharmaceutical plants requires special attention. Always identify and prioritize environmental challenges, the size of the bearings, application conditions, and current performance levels. Carefully compare H1 food grade grease attributes of various brands against those priorities. With careful selection, you’ll reduce bearing failures and experience performance gains.
Mark Guenther
Mark has worked with A.W. Chesterton Company for 40 years, extensively focusing on the practical understanding of equipment failure and corrective action plans. While at Chesterton, he has fulfilled many functions: Chemist, Technical Service/Application Engineering, Research and Development Manager and Educator. Mark’s philosophy is that providing value to our customer is the single most important contribution we can make.
Comments